Sustainable site technology: cutting emissions in crane operations
09 April 2025
Construction sites are evolving, using new and smart technology to go greener than ever before. Niamh Marriott reports.
As the wider construction industry focuses more on being sustainable, new technology is playing a key role in reducing its environmental impact. From cranes that use electric power to smarter ways of handling materials and monitoring efficiency, these innovations are making a big difference.
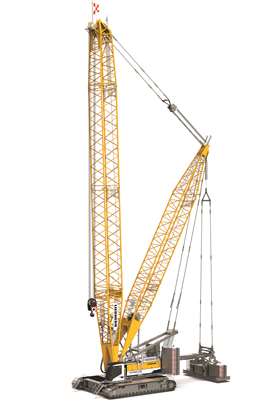
Not only do they help lower carbon footprints and reduce waste, they also boost efficiency and safety on job sites. The latest sustainable technologies in crane operations are helping the wider industry meet the necessary environmental goals.
Example electric
There have been fully electric construction sites, particularly in Scandinavia, where sustainability regulations and innovation have helped encourage low-emission construction. One of the first fully electric sites was in Oslo, Norway, in 2020. It was commissioned by Oslo’s municipality and used only electric machinery for the duration. It aimed to reduce noise pollution and cut carbon dioxide emissions by around 99 per cent compared to a traditional site. Contractors used battery-powered and grid-connected machinery.
In 2022 Sweden launched an electric construction pilot at the Slussen redevelopment in Stockholm, using battery-powered and hybrid construction equipment to cut emissions. It wasn’t 100 % electric but made significant progress in reducing fossil fuel use.
In Copenhagen, Denmark, there has also been a real push for emission-free construction projects, with requirements for electric machinery in certain public works.
These sites show what can be possible but there are still some obstacles to overcome before the industry can full embrace sustainability.
Challenges
First, it can be very expensive, especially with high upfront costs of green equipment. High prices of new electric and hybrid machinery are proving a barrier to more widespread adoption. Battery-powered equipment also often has limited operating hours and needs reliable charging infrastructure that might not always be available in remote locations or temporary sites – which are very common in construction. Not only might access to grid power be limited in really isolated locations but transporting green equipment there in the first place can be more complex and costly.
There’s also a question of looking at the full supply chain of a green site. How was the equipment in use manufactured initially? Was it a carbon-heavy process or did it require a lot of energy to produce? How is the equipment transported to and from sites and from the factory? What materials are used on-site and are they sourced sustainably? What energy sources power the site – are they renewable and is energy consumption optimised? Is the energy used to run the equipment being used efficiently, including idle time and wastage? What happens to the equipment at the end of its life – is it recycled, remanufactured, or disposed of sustainably? To answer these questions is an additional challenge.
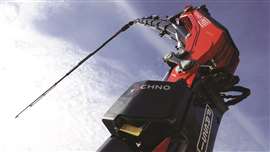
The industry is considering making equipment sustainable by using green manufacturing from the start or by carefully selecting the materials used in the manufacturing process. Green credentials can be factored in from the beginning, influencing the entire life cycle of cranes, for example.
Material change
SSAB and Italian crane manufacturer Fassi have partnered to produce and use “fossil free” steel. This new deal includes steel produced from both iron ore and recycled scrap and will be used in Fassi’s hydraulic and truck-mounted cranes. One of the useful benefits of this steel is that it’s lighter, in addition to being manufactured in a sustainable way.
Traditional steel production accounts for around 7 % of global CO2 emissions, SSAB notes, with both primary steel and recycled steel production contributing to emissions. To reduce the climate impact, SSAB is investing in new production technologies that will enable steel production with close to zero fossil carbon emissions, regardless of whether the raw material is recycled scrap or primary iron ore.
“Innovation is a projection towards the future. And there is no future without sustainability” says Giovanni Fassi, CEO at Fassi. “For this reason, we have chosen to participate with enthusiasm and determination in this partnership with SSAB to develop our cranes of tomorrow”.
Digital planning
We’ve heard a lot about building information modelling (BIM) in recent years – the concept of creating digital representations of physical and functional characteristics of places. While BIM is used widely in architecture, its significance in the crane industry is still being understood. By integrating BIM, crane operations can achieve enhanced precision in planning and execution. This digital approach allows for meticulous simulation of lifts, identification of potential problems and clashes, and it can optimise crane placements. All this can lead to improved safety and efficiency on construction sites.
Beyond just planning, BIM also enhances collaboration across a project. With all stakeholders working from the same digital model, there can be better co-ordination between crane operators, site managers, and engineers. This reduces misunderstandings, improves communication, and ultimately leads to smoother project execution. If it’s more efficient, the likelihood is that there will be less wastage on site.
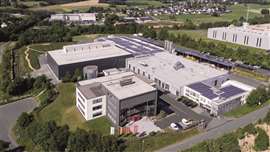
“The call for the electrification of construction sites will gain even more importance in the coming years, to meet local and global climate targets for the reduction of emissions,” says manufacturer Liebherr. “Therefore, construction site operators have a dynamically growing energy demand in response to the existing and upcoming emissions regulations.”
“Sometimes, access to power supply on construction sites is either limited or missing at all. Consequently, electrified construction sites face such challenges as machine operation at a maximum power, charging of numerous machines during breaks and smoothing load peaks.”
Liebherr has been investing heavily in hybrid and electric crane technology, including its unplugged battery-electric crawler cranes. At bauma 2025, the company will show its battery drive technology on its 300 tonne capacity LR 1300.2 SX lattice boom crawler crane. It will be shown for the first time as a battery-electric version with zero emissions. There is a 438 kW electric motor and it is powered by a 392 kWh battery. Up to 13 hours of operation on a single charge can be achieved, Liebherr says, depending on the application.
Energy on site
Talking of power there will be a new version of Liebherr’s Liduro Power Port (LPO) mobile energy storage system. Another stationary energy storage system, LPO 600, will be shown as a prototype. As a mobile charging station LPO 600 has a capacity of 564 kWh, enough for large machines or fleets, Liebherr said. Hydrogen technology will also feature, primarily to power larger machines that are difficult to power electrically.
Several manufacturers have been looking at the development and production of electric cranes. For example, Italy-based Marchetti launched its CW 25. 35 HY fully electric telescopic crawler crane at the Intermat trade show in France, in April 2024. It has a 17 tonne pick and carry lifting capacity and boasts a compact size, with a total weight of 25.5 tonnes. Power comes from an electric motor and lithium batteries and the crane carries 3.3 tonnes of counterweight.
A big announcement was Japanese manufacturer Tadano’s EVOLT eGR-1000XLL-1 rough terrain crane, the first electric rough terrain crane designed to work in North America. The company sees its electric cranes as a major step in its goal to reduce emissions generated by its products by 35 % by 2030.
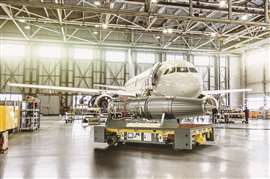
“Tadano is assessing other models for potential electrification as part of its Green Solutions initiative,” says Lance Rydbom, director for product management and engineering at the company’s Pan-American operations. “We are committed to advancing our electric crane lineup, focusing on sustainability and efficiency. We aim to respond to customer demand for sustainable solutions.”
“The machine’s zero emissions and lower noise make it ideal for urban areas or indoor projects where quiet operation is beneficial,” Rydbom adds.
As with much electric construction machinery, however, the main sticking points for electric rough terrain cranes are likely to be with both the higher initial purchase cost when compared with a diesel alternative, as well as concerns about running time.
International heavy lift and transport specialist Mammoet’s land-based 6,000 tonne capacity SK6000 can be powered electrically.
In addition to its work with self propelled modular transporter (SPMT) for specialized transport, including electric SPMT, Mammoet is looking at zero emission lifting and transport on site in a wider context.
Mammoet’s head of sustainability Mathias Hoogstra, says, “I want us to redefine the construction site – at least at small scale initially – where we have electric or hydrogen cars, electric cranes, electric trucks, and have all this equipment cross-link and charge each other.”
Mammoet says it sees sustainability as an important factor in the future of the heavy lifting and transport industry and it is working on fully electrifying its crane fleet. The company believes recent developments allow an entire project to be completed without engine exhaust emissions. This is achieved using equipment already introduced to the market.
Sustainability in heavy industry offers big rewards for sufficiently adaptable companies.
ESG
Belgium-headquartered lifting giant Sarens has been implementing its ESG initiatives for several years and continues to focus heavily on sustainable practices throughout its global work.
The company has launched its Sarens Sustainability Accelerator to drive smarter engineering solutions and cleaner energy opportunities, particularly in the wind and clean energy sectors. Sarens has developed a giant electric crane, the SGC-90, which can connect to the electricity grid and also produce its own energy regeneratively, with zero emissions.
Sarens is also investing in hybrid cranes and low-emissions technology, ensuring new fleet additions meet stringent emissions standards. In addition, it is researching electric SPMT power packs, promoting recycling, and reducing energy consumption across its offices.
New sector
The green energy industry presents significant opportunities for the development of sustainable construction sites, particularly as the demand for renewable energy solutions continues to rise. While the crane rental market remains heavily influenced by the oil and gas sector, the growth of renewable energy, especially wind energy, is creating new projects – particularly offshore – that are gaining momentum. This shift towards green energy is not only opening up new avenues for work but also encouraging the construction industry to adopt more sustainable practices.
Luxembourg-headquartered Faymonville Group, has been focusing on the wind energy sector for some time, with a product range tailored to transporting essential components for this industry. The company’s equipment is also environmentally conscious, offering options for diesel, hybrid and electric power across its Cometto range. At the Bauma trade show this year, the company will show its Eco500 modular transporter, demonstrating how the construction industry is really embracing sustainable technology.
STAY CONNECTED
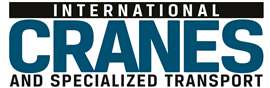
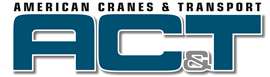
Receive the information you need when you need it through our world-leading magazines, newsletters and daily briefings.
CONNECT WITH THE TEAM
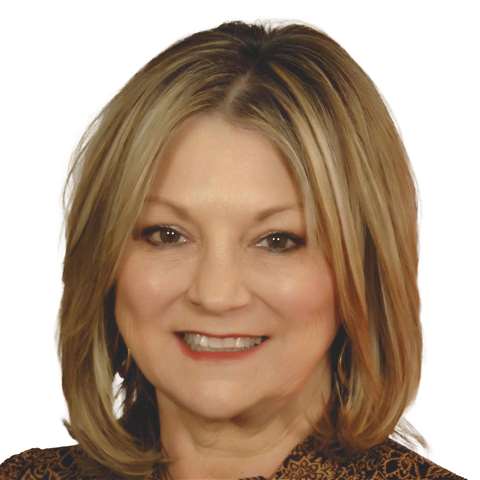
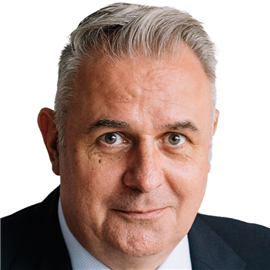
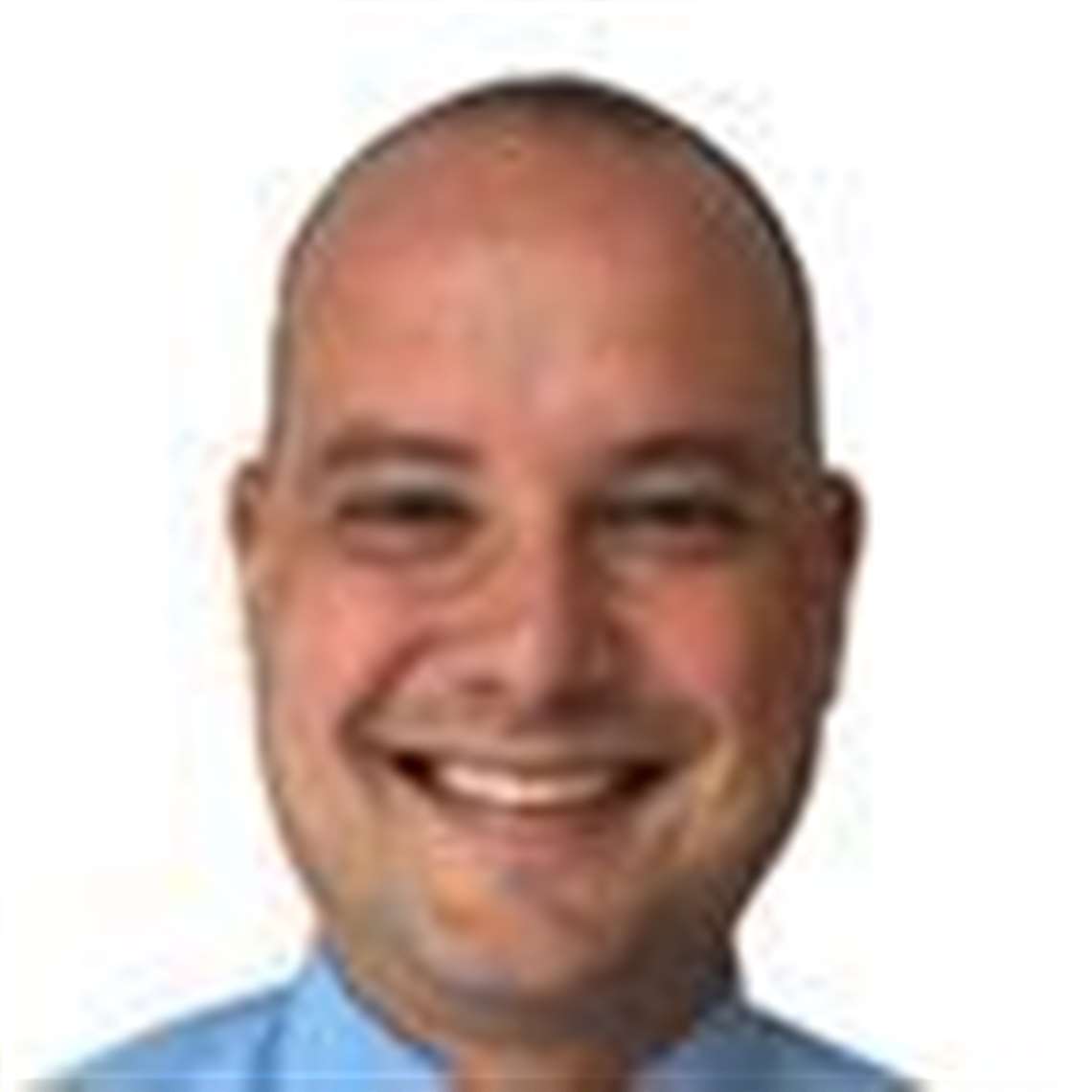
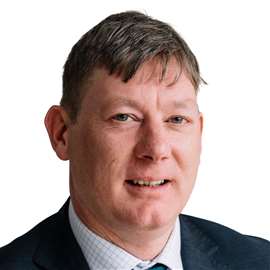