Automatisch von KI übersetzt, Original lesen
Mammoet transportiert riesigen Brecher für Codelco
11 März 2025
Über einen Zeitraum von 18 Monaten entwickelte das Team von Mammoet die Route, die Methodik und den Plan für die Durchführung des Transports der Brecherteile von einer Mine zur anderen.
Bergbauausrüstung ist riesig und schwer und wird ständig von einem Ort zum anderen transportiert. Nach dem Abbau der Ressourcen muss die Ausrüstung abgebaut und an einen anderen Ort gebracht werden, um ihre Arbeit wieder aufzunehmen.
Doch der Transport von Bergbauausrüstung ist ein komplizierter Prozess, wie es im Fall von Codelco der Fall war, dem staatlichen chilenischen Kupferbergbauunternehmen, das Minen in der Nähe der Stadt Calama betreibt.
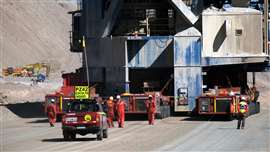
Codelco holte sich Unterstützung von Mammoet, um wichtige Brecherteile von einem etwa 4,5 Kilometer entfernten Standort zu einem anderen zu transportieren. 16 Komponenten mussten transportiert werden, und die sechs größten Teile bilden den Hauptteil des Brechersystems, das Materialien aus Minen fördert und in kleinere Stücke zerlegt.
Codelco hatte noch nie zuvor ein Projekt dieser Größenordnung durchgeführt. Das Unternehmen wandte sich an Mammoet, um sich über die optimale Schwerlast- und Transportausrüstung sowie technische Lösungen zur Erreichung seines Ziels beraten zu lassen. Die Ingenieure von Mammoet schlugen verschiedene Bergungsmethoden vor, um die Schlüsselkomponenten als ganze Einheiten zu verlagern. Dies senkte die Kosten und ermöglichte laut Mammoet eine frühere Fertigstellung des Projekts als erwartet.
Bei diesem Projekt arbeitete Mammoet erstmals direkt mit Codelco zusammen und musste erstmals an diesem Standort ein Brecher versetzen. Der erste Schritt bestand in der Planung der Route, der Methodik und der Schwerlast- und Transportausrüstung. Die Ingenieure von Mammoet unterstützten in jeder Phase.
„Wir haben anderthalb Jahre lang mit Codelco an der Planung gearbeitet“, so Mammoet-Vertriebsleiterin Vanessa Labana. „Wir erstellten sämtliche Trassenpläne und Zeichnungen und unterstützten Codelco bei allen Fragen und Überlegungen vor Ort. Beispielsweise bei der Wahl der richtigen Neigung, der richtigen Kurvenverhältnisse und der richtigen Straßenbreite, um die schnellste Transportroute zu ermöglichen.“
Eine der größten Herausforderungen bestand darin, die Ausrüstung und das Personal für ein Projekt dieser Größenordnung zu beschaffen und zu mobilisieren. Das Team von Mammoet bündelte seine globalen Ressourcen und nutzte einen selbstangetriebenen modularen Transporter (SPMT) aus Malaysia, Verschubsysteme aus den USA und zusätzliche Ausrüstung aus Kolumbien.
Verschiedene Ansätze
Sechs Schlüsselkomponenten mussten verlagert werden, wobei die Abtransport- und Transportmethoden für jede Komponente unterschiedlich waren. Die meisten Komponenten wurden mit Kletterwinden angehoben und anschließend mit SPMTs mit Stützbalken verlagert. Für das Antriebssystem wurde derselbe Ansatz verwendet, jedoch zusätzlich um ein Gleitsystem ergänzt. Damit wurde die Komponente 12 Meter weit verschoben, bevor sie in ihre endgültige Position abgesenkt werden konnte. Die beiden schwersten Transport- und Hebevorgänge waren der Silo (1.100 Tonnen) und der Brecher selbst (1.300 Tonnen). Letzterer war die komplexeste der sechs Frachtbewegungen.
„Wir haben einen speziell für diese Ladung angepassten Stützbalken entwickelt“, sagte Labana. „Wir mussten unsere Originalbalken etwas verändern, indem wir an den vier Hebepunkten Bleiverstärkungen anbrachten, um Verformungen zu verhindern.“
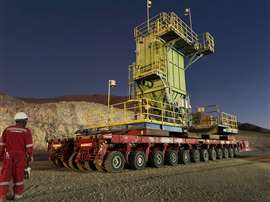
Der Brecher wurde mithilfe von Gleitschienen und Gleitschuhen aus seinem Gehäuse gehoben und anschließend hoch genug angehoben, damit SPMT darunterfahren konnte. Zurrgurte sorgten für zusätzliche Stabilität und hielten alles während der 4,5 km langen Fahrt in Position. In der Nähe des Demobilisierungsortes wurde ein Bereich geschaffen, um den Brecher um 180 Grad zu drehen und ihn so in die richtige Position für die Installation zu bringen.
Am Installationsort angekommen, wurde der vorherige Vorgang in umgekehrter Reihenfolge wiederholt. SPMT-Anhänger senkten die Ladung auf Gleitschienen ab, um sie zurück an ihre neue Position zu schieben. Auch die Galerieeinheit stellte eine Herausforderung dar, da der Boden mit einem Gefälle von 1 Prozent nicht vollständig eben war. Daher wurden zwei Hydraulikheber eingesetzt, um das hintere Ende in drei verschiedenen Abständen schwer anzuheben und so beim Vorwärtsschieben alles waagerecht zu halten.
Der Vorgang wurde in etwas mehr als einem Monat abgeschlossen und dauerte damit weniger Zeit als erwartet, hauptsächlich weil die Brecherteile als komplette Einheiten ausgebaut wurden. Dadurch konnte die Mine schnell wieder in Betrieb genommen werden. Labana sagte, Mammoet habe das Team, die Ausrüstung und die technischen Schritte so gemanagt, dass das Projekt sicher und effizient durchgeführt werden konnte. Alles wurde pünktlich zur Baustelle transportiert und kostspielige Verzögerungen und Strafzahlungen vermieden. Ein 70-köpfiges Team und insgesamt 160 SPMT-Achslinien, acht Gleitschuhe (500 Tonnen), acht Hebesysteme (400 Tonnen) sowie Stützbalken, Schienen und Zurrgurte kamen im gesamten Projekt zum Einsatz.
„Wäre dieses Projekt auf konventionelle Weise durchgeführt worden, hätte Codelco die Anlage zerlegen und zerlegen müssen, was sehr zeitaufwändig gewesen wäre“, erklärte Labana. „Dies ist das erste Mal, dass Codelco so etwas durchgeführt hat. Mit uns haben sie einen Partner für zukünftige Projekte, der auf unsere Erfahrung, unsere Ausrüstung und unseren Hintergrund vertraut.“
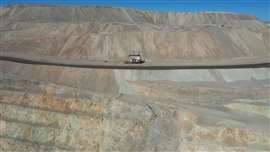
BLEIBEN SIE VERBUNDEN
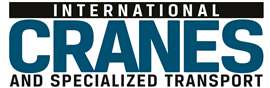
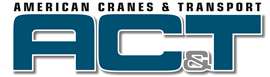
Erhalten Sie die Informationen, die Sie benötigen, genau dann, wenn Sie sie brauchen – über unsere weltweit führenden Magazine, Newsletter und täglichen Briefings.
KONTAKTIEREN SIE DAS TEAM
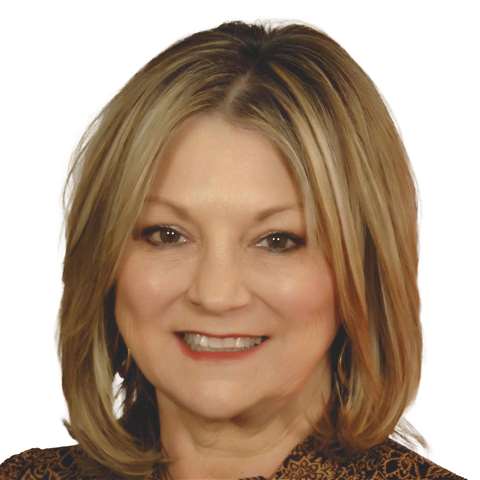
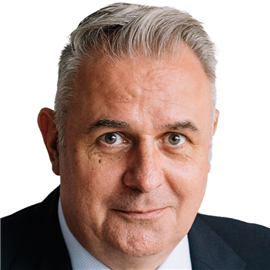
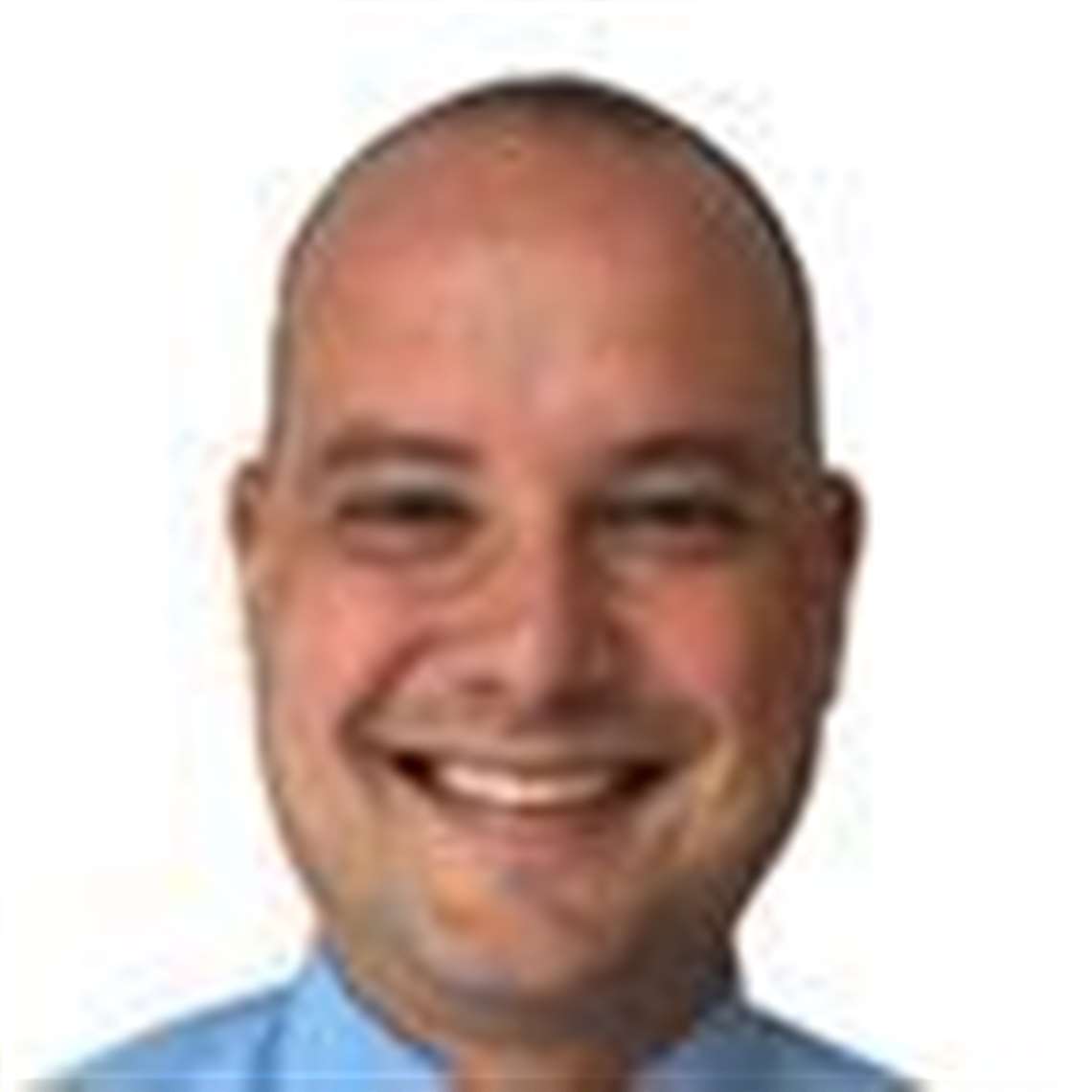
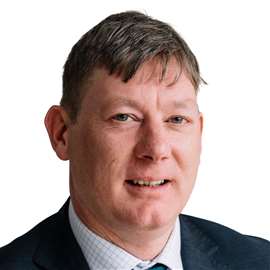