Automatisch von KI übersetzt, Original lesen
Mammoet erreicht Meilenstein von 3.000 Tonnen Verladung
26 Februar 2025
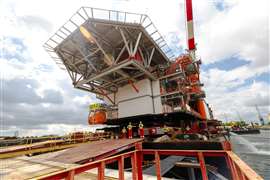
Der Auftragnehmer HSM Offshore beauftragte den internationalen Schwerlast- und Transportspezialisten Mammoet mit der Verladung eines wegweisenden Projekts.
Es handelte sich um die erste windbetriebene Offshore-Gasplattform in der niederländischen Nordsee. Die Plattform N05-A nutzt Strom, der über ein Unterseekabel vom nahegelegenen Offshore-Windpark Riffgat mit einer Leistung von 113,4 MW geliefert wird.
Durch die Nutzung der Windenergie dürften die Kohlendioxid-Emissionen über die Lebensdauer der Plattform um mehr als 85 Prozent sinken.
Mammoet erklärte, dass sein technischer Ansatz eine effizientere Montage der Jacke und eine Verkürzung der Bauzeit ermöglicht habe.
Die Arbeiten wurden auf der Kaianlage von HSM Offshore in Schiedam, Rotterdam, Niederlande, in der Nähe der eigenen Werft durchgeführt. Das 3.150 Tonnen schwere Jacket und das 3.050 Tonnen schwere Topside wurden verladen. Beide wurden auf ein Binnenschiff verladen und anschließend verschifft. ONE-Dyas, Eigentümer der Plattform, kümmerte sich anschließend um die Verschiffung und Installation auf See.
Zurück auf dem Fertigungsgelände wurden das Jacket und die Plattform mithilfe von Mobilkränen, Anhängern und einem modularen Transporter (SPMT) mit Selbstantrieb montiert und gewogen. Das Jacket wurde in Abschnitten gefertigt und anschließend mit Schwertransportern zusammengebaut. Anschließend wurde es mit vier mobilen Teleskopkranen von Liebherr aufgerichtet: zwei LTM 1650-8.1 mit 700 Tonnen Tragkraft und zwei LTM 1450-8.1 mit 450 Tonnen Tragkraft. Die Installation der Pfahlrohre des Jackets erfolgte mit einem mobilen Mobilkran mit 750 Tonnen Tragkraft.

Zusammenfügen
Für die Endmontage am Kai wurde der obere Abschnitt mit zwei Schwerlast-Scherbeinschiffen angehoben. Dadurch entstand genügend Platz, um den unteren Abschnitt auf Anhängern darunter zu fahren und die beiden Abschnitte zu verbinden.
Für den im Innenbereich errichteten Überbau wurde SPMT unter diesen gefahren, um ihn nach draußen zu bringen und zum Kai zu fahren. Dort montierte Mammoet mithilfe von Anhängern und Mobilkränen einen Sockelkran auf dem Überbau.
Das fertige Topside und Jacket wurden separat auf SPMT geladen und anschließend mit Mammoet-Wägezellen gewogen, um das Endgewicht zu ermitteln. Es kamen vier Reihen mit je 32 SPMT-Achslinien zum Einsatz.
Um den Zeitplan einzuhalten, wurden beide Module auf dasselbe Schiff verladen. Normalerweise werden sie getrennt verschifft. In diesem Fall stellte dies eine technische Herausforderung dar, und es gab Platzprobleme. Auf dem Schiff musste Platz für Pumpen und Winden geschaffen werden, und es musste eine andere Verankerungsmöglichkeit geschaffen werden.
Am Liegeplatz
„Das Verankern war äußerst kritisch und erforderte viel Ingenieursarbeit“, erklärte Sven Segeren, Projektmanager bei Mammoet. „Normalerweise würden wir mehrere Winden verwenden, um das Schiff zu verankern und zu stabilisieren, aber das war aufgrund der enormen Lasten nicht möglich.“
„Die Belastung der Winden war zu hoch und die Poller nicht stark genug. Daher wurde ein kleines Spud-Leg-Barge verwendet, um das Schiff zu sichern und es vor, während und nach dem Beladen in Position zu halten.“
Die Vorbereitung des Hauptschiffs dauerte fünf Tage. Dazu gehörten die Installation der Ballastpumpen, das Vorballastieren und anschließende Überprüfen der Segelbedingungen für die Reise.
Beide Module wurden in einer zweitägigen Operation verladen.
„Wir arbeiten viel mit HSM Offshore zusammen. Sie beziehen uns immer von Anfang an in Projekte ein, sodass wir ihnen mit intelligenten Lösungen für die Montage helfen können“, sagte Segeren.
BLEIBEN SIE VERBUNDEN
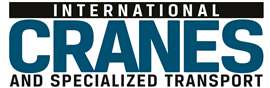
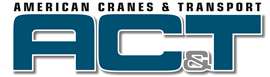
Erhalten Sie die Informationen, die Sie benötigen, genau dann, wenn Sie sie brauchen – über unsere weltweit führenden Magazine, Newsletter und täglichen Briefings.
KONTAKTIEREN SIE DAS TEAM
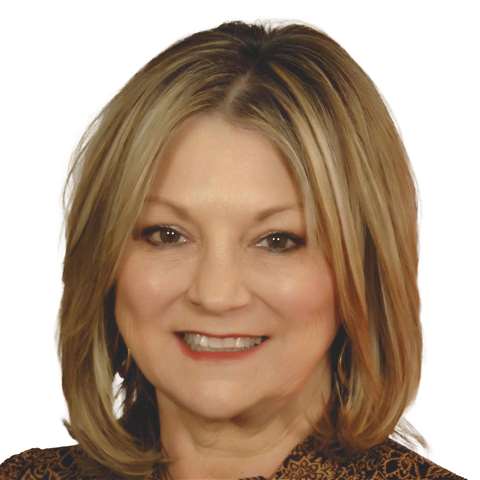
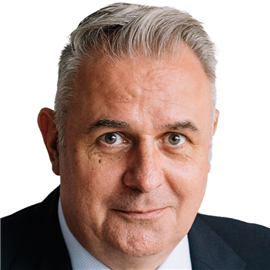
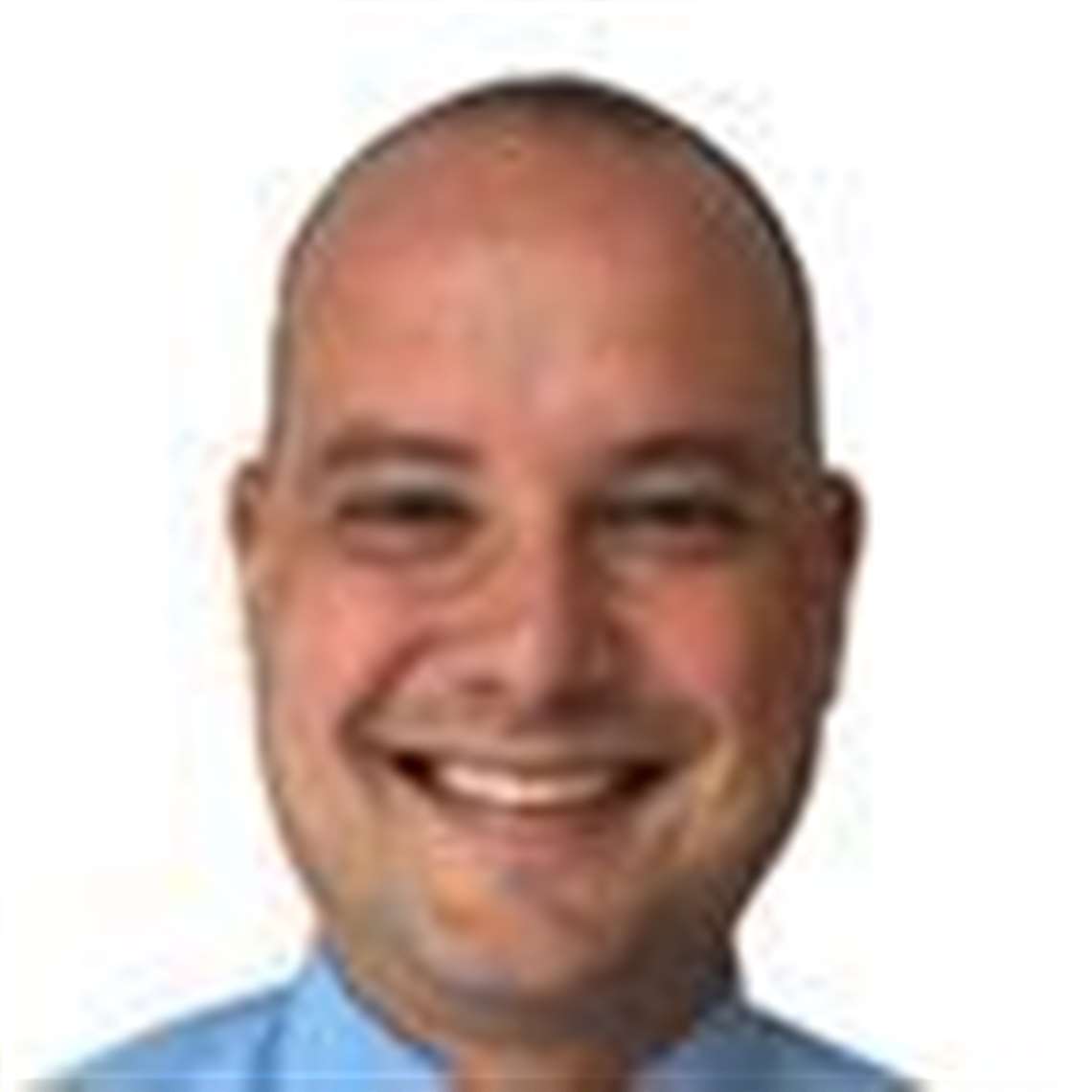
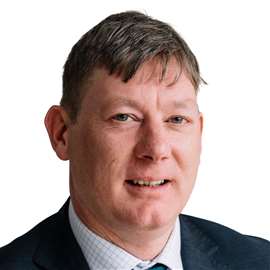