Automatisch von KI übersetzt, Original lesen
PSC Crane & Rigging montiert den neuen Windkanal der NASA
04 März 2025

Die Flight Dynamics Research Facility in Hampton (Virginia, USA) wurde zur Unterstützung menschlicher Erkundungen und wissenschaftlicher Rückkehrmissionen vom Mond und Mars konzipiert und verfügt in ihrem Kern über einen 37 Meter langen vertikalen Windkanal.
Die Einrichtung soll die Forschung und Technologieentwicklung für eine Reihe von NASA-Missionen vorantreiben, darunter Luftfahrt, Weltraumforschung und wissenschaftliche Unternehmungen. Zu ihren Aufgaben gehört auch die Erforschung der Venus und des Saturnmondes Titan.
Der Windkanal befindet sich im Langley Research Center der NASA und wurde von Teams von PSC Crane & Rigging an seinen Platz gehoben. Dabei kamen zwei MOD 50-Spreizbalken von Modulift zum Einsatz, um einen 4-Punkt-Hub zu erzeugen.
„Unsere Aufgabe bestand darin, Personal, Ausrüstung und technisches Know-how für die Montage der gesamten Windkanalausrüstung bereitzustellen“, sagte Adam DeBrosse, Senior Estimating Manager bei PSC. „Dazu gehörten große Lüfterbaugruppen, Leitschaufeln (zur Lenkung des Luftstroms), Strömungsgitter, eine Prüfzelle im Inneren sowie unterstützende Ausrüstung im Testbereich.“
Für den Kontraktionskegel luden die PSC-Teams die Baugruppe vor Ort ab, überprüften, ob die innere Strömungsoberfläche glatt und innerhalb der Toleranzen war, sicherten die Baugruppe, hievten sie hoch, setzten sie an ihren Platz, richteten sie aus und verankerten sie.
Mehrere Aufzüge
Das Projekt umfasste rund 100 Hebevorgänge, darunter auch Test-Hubvorgänge, um die Sicherheit der Besatzung und die Unversehrtheit der teuren und empfindlichen Ausrüstung zu gewährleisten. Das Herzstück der Hebearbeiten war der Kontraktionskegel, für den ein Testhub erforderlich war, der jedoch aufgrund von Bautoleranzen abgesagt werden musste. Das Teil wurde noch am selben Tag zugeschnitten und neu ausgerichtet.
Das PSC-Team verwendete einen Liebherr LR1300SX Raupenkran mit 29 m Hauptausleger und 38 m Wippspitze. Das Gewicht des Kontraktionskegels betrug 32.000 kg. Dieser Abschnitt wurde mit zwei 6 m langen Modulift 50-Spreiztraversen sowie vier Polyester-Rundschlingen für die obere und vier Polyester-Rundschlingen für die untere Takelage befestigt.
„Die Herausforderungen des gesamten Projekts bestanden darin, dass die Montage/Installation des Betonfertigteilgebäudes und der Windkanalausrüstung zeitlich so abgestimmt werden musste, dass die Windkanalausrüstung an den wichtigsten Haltepunkten der Fertigteilkonstruktion einbaubereit war. Verzögerungen auf Seiten der einen Seite führten zu Ausfallzeiten und Verzögerungen auf der anderen Seite“, so DeBrosse. „Jede Toleranzabweichung würde dazu führen, dass kritische Teile nicht problemlos platziert werden konnten. Wichtige Strukturelemente der Fertigteile mussten unvollendet bleiben, bis die Windkanalausrüstung platziert war, bevor zusätzliche Elemente eingebaut werden konnten.“
DeBrosse erklärte, die Windkanalausrüstung sei von Lieferanten aus aller Welt im Kaltbauverfahren hergestellt worden, ohne dass vor der Installation eine Vormontage erfolgte. Alle Anpassungen an Passform und Verarbeitung mussten während dieses gemeinsamen Installationsfensters geplant und umgesetzt werden.
„Lösungen mussten vor Ort umgesetzt und gleichzeitig vom NASA-Konstruktionsteam geprüft und genehmigt werden“, sagte er. „Windkanalausrüstung wie die innere Testzelle sollte als Stabkonstruktion aus Paneelen installiert werden. Um jedoch Zeit zu sparen, wurde sie als einzelnes 12-seitiges Paneelpolygon gebaut. Die Struktur der inneren Testzelle war nicht unbedingt für den Transport in einem Stück ausgelegt.“
Benutzerdefinierte Halo-Takelage
Das Rigging-Team von PSC berechnete die Belastungen, die durch die Hebepunkte der Testzelle ausgeübt werden, erklärte DeBrosse. Das PSC-Team entwarf und baute einen maßgeschneiderten Halo-Takelagerahmen, um die Struktur aufzunehmen und durch das Gebäude in Position abzusenken.
Der Einsatz von Modulift-Spreiztraversen beim Bau der NASA-Forschungseinrichtung wirft ein Licht auf die Hebegeräte, die bei Pionierprojekten wie diesem zum Einsatz kommen, so Modulift-Geschäftsführerin Sarah Spivey.
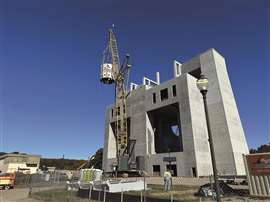
„Modulift ist weltweit für seine ikonischen gelben Spreiztraversen bekannt und setzt in der globalen Hebebranche Maßstäbe für Sicherheit, Effizienz und schnelle Lieferung“, sagte sie. „Wir sind sehr stolz, Teil dieses bahnbrechenden Projekts zu sein.“
Seit den späten 1930er Jahren nutzen NASA-Forscher einen 12 Fuß langen Niedriggeschwindigkeitstunnel und einen vertikalen Spin-Tunnel. Die neue FDRF-Anlage wird deutlich leistungsfähiger sein als die beiden bestehenden Tunnel und gleichzeitig die Wartungs- und Betriebskosten deutlich senken. Die Forschungsanlage ermöglicht es der NASA und Industriepartnern, die Luftströmung um Raumfahrzeuge zu untersuchen.
„Mit dieser Anlage werden wir die Welt buchstäblich verändern“, sagte Clayton Turner, Direktor des NASA Langley Research Center. „Der bescheidene Geist unserer Forscher und dieses Engagement werden es uns ermöglichen, neue Höhen zu erreichen, Unbekanntes zu entdecken und so der Menschheit ein besseres Leben zu ermöglichen.“
PSC Crane & Rigging wurde 1933 von Earl Sever, Sr. gegründet und hat seinen Sitz in Piqua, Ohio, USA. Modulift wurde 2002 gegründet und hat seinen Sitz in Dorset, Großbritannien.
BLEIBEN SIE VERBUNDEN
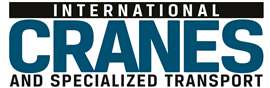
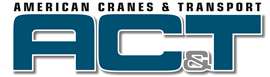
Erhalten Sie die Informationen, die Sie benötigen, genau dann, wenn Sie sie brauchen – über unsere weltweit führenden Magazine, Newsletter und täglichen Briefings.
KONTAKTIEREN SIE DAS TEAM
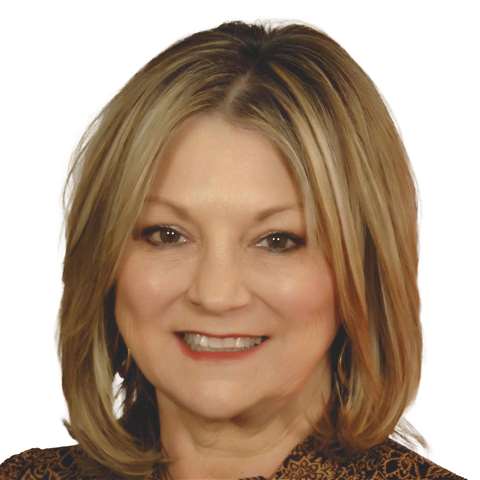
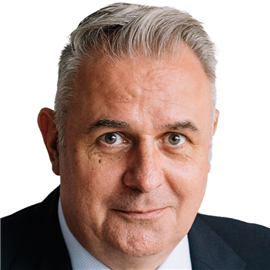
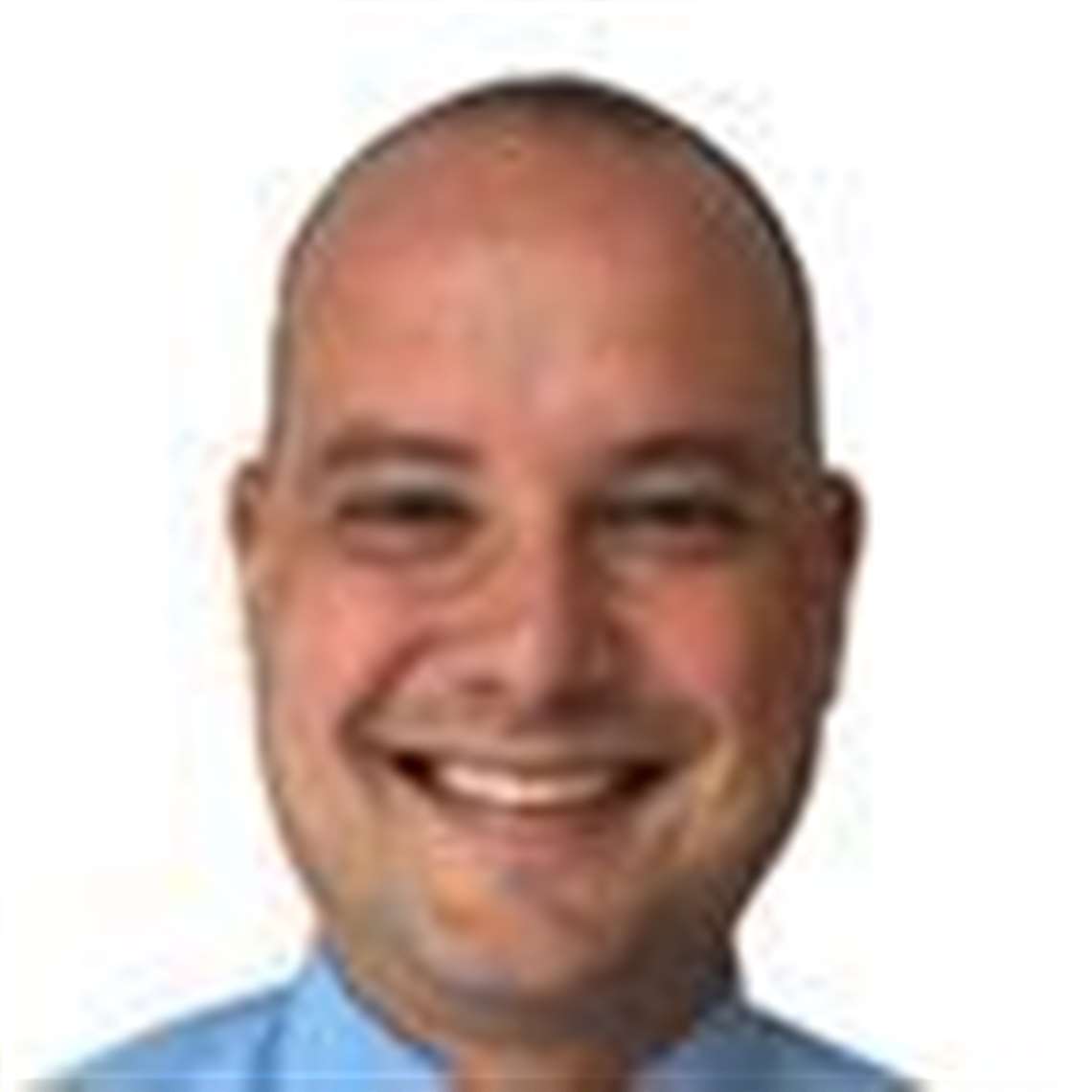
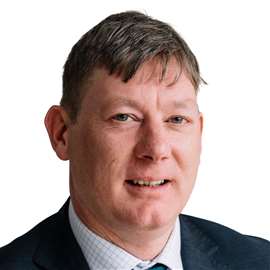