Automatisch von KI übersetzt, Original lesen
SPMT-Markt wird durch Infrastrukturprojekte vorangetrieben
15 Oktober 2024
Der SPMT-Markt ist stark, weil die Benutzer mit diesen vielseitigen Maschinen immer wieder äußerst kreative Lösungen finden.
Die Einführung selbstangetriebener modularer Transporter, weltweit als SPMTs bekannt, eröffnete neue Wege für innovative Transportsysteme. SPMTs wurden ursprünglich für den Transport großer Ladungen entwickelt. Dank des modularen Designs konnten SPMT-Systeme beliebig breit und lang gebaut werden.
Während sie in erster Linie als Transportmechanismus dienten, ermöglichten neue Funktionen den SPMTs, auch als Schwerlasttransporter und Schleppgeräte eingesetzt zu werden.
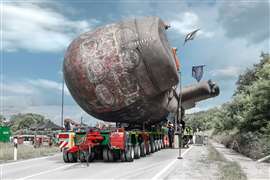
Laut Roland Fischer, Vertriebsleiter Nordamerika bei TII Scheuerle und TII Kamag, haben Kunden besondere Anforderungen, wenn sie ihren Fuhrpark um ein SPMT erweitern.
„Kunden suchen in erster Linie nach der sichersten, kostengünstigsten und zuverlässigsten Lösung, um schwere und große Strukturen sicher und effizient zu bewegen“, so Fischer. „SPMTs von TII-Scheuerle können nahezu alle schweren Lasten heben und bewegen, wie unser täglich wachsender Kundenstamm beweist.“
Es gibt nur eine Handvoll SPMT-Hersteller, die diese Maschinen für nordamerikanische Kunden produzieren, darunter Goldhofer, TII und Cometto (ein Faymonville-Unternehmen). Auch Enerpac ist auf dem SPMT-Markt aktiv, in der Regel mit kleineren SPMTs. Die Enerpac Tool Group hat kürzlich DTA übernommen, einen führenden Anbieter im Bereich des industriellen Schwerlasttransports, der mobile Roboterlösungen für die Handhabung schwerer und spezieller Lasten entwickelt und herstellt. Laut Enerpac stärkt diese Übernahme die Strategie des Unternehmens, sich ausschließlich auf industrielle Werkzeuge und Lösungen zu konzentrieren, indem das Produktportfolio des Unternehmens im Bereich Schwerlasttransport um Produkte für die automatisierte horizontale Bewegung vor Ort ergänzt wird.
Laut Fischer schreiten die Innovationen im Design und in der Entwicklung von SPMTs weiter voran.
„Telematik, ein Cloud-basiertes System, bietet Fernwartung, Diagnose und Fehlerbehebungsunterstützung von unserem Werk oder unseren Servicepartnern aus“, sagte er.
TII habe außerdem eine App zur Online-Ersatzteilbestellung entwickelt, die den Kunden eine weitere Möglichkeit biete, ihre SPMTs effektiv, sicher und effizient zu betreiben und zu warten, sagte er.
Der Elektroantrieb ist eine weitere Innovation, die laut Fischer für große Begeisterung sorgt.
„Der E-Antrieb wird in die gesamte Familie der TII SPMT-Produkte integriert“, sagte er.
Darüber hinaus werden batteriebetriebene Akkupacks für eine längere und effizientere Nutzung weiterentwickelt.
„TII-Scheuerle entwickelt die nächste Generation einer batteriebetriebenen Power Pack Unit (PPU),“ sagte Fischer.
Die größte Herausforderung auf dem SPMT-Markt in Nordamerika besteht weiterhin in der Produktverfügbarkeit, insbesondere der zur Herstellung dieser Maschinen benötigten Teile.
„Damit meine ich die Fähigkeit, alle für die Herstellung der Anlagen benötigten Teile rechtzeitig zu beschaffen“, sagte er. „Eine weitere Herausforderung für unsere Kunden ist die ordnungsgemäße Wartung der Anlagen angesichts des hohen Auftragsvolumens im heutigen Wachstumsmarkt. Glücklicherweise haben wir viele Systeme implementiert, die es uns ermöglichen, unsere Kunden mit angemessenen Lieferzeiten, Außendienst, Schulungen und technischem Support zu unterstützen, damit sie ihre Aufträge effizient erledigen können.“
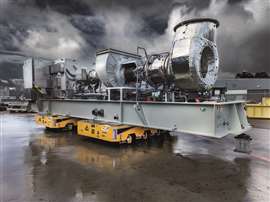
Da die Nachfrage nach SPMTs so hoch ist, besteht auch ein Bedarf an der Reparatur und Überholung älterer SPMTs.
„Das ist ein sehr wichtiges Thema“, sagte Fischer. „Die TII Group baut seit über 40 Jahren SPMTs, und wir sind sehr stolz darauf, dass fast alle noch im Einsatz sind. Wir bieten Überholung und Reparaturen in den Werken der TII Group in Deutschland und Florida sowie vor Ort beim Kunden über unseren Vertriebs- und Servicepartner TPSE, Inc. an.“
Goldhofer und Cometto bieten diese Dienstleistungen auch für die SPMT-Flotten ihrer Kunden an.
Eine Idee, die sich am Markt durchsetzt, ist die Kombination verschiedener SPMT-Marken. Obwohl dies nicht alltäglich ist, wird es praktiziert, obwohl die Hersteller es vorziehen würden, wenn ihre Marken ausschließlich kombiniert würden.
Unkonventionelle Nutzung
Mammoet ist ein Großanwender von SPMTs mit einer riesigen globalen Flotte aller Marken und hat SPMTs auf vielfältige, unkonventionelle Weise eingesetzt. Kürzlich baute das Unternehmen SPMTs zu riesigen Gabelstaplern für einen Offshore-Windpark vor der Küste Frankreichs um.
Das Projekt Îles d'Yeu und Noirmoutier liegt etwa zwölf Kilometer von der Insel Yeu entfernt und ist der fünfte Offshore-Windpark, der in Frankreich in Betrieb genommen wird. Es wird 61 Offshore-Windturbinen mit einer Leistung von jeweils 8 MW beherbergen. Mit einer geschätzten jährlichen Produktionskapazität von 1.900 GWh wird es ausreichend Strom für rund 800.000 Menschen pro Jahr erzeugen.
BOW Terminal, ein langjähriger Kunde von Mammoet, bat dessen Ingenieure um Unterstützung bei der Aufstellung, Bewegung und Zwischenlagerung der in Belgien gefertigten Übergangsstücke (TPs) der Offshore-Windkraftanlagen. TPs werden traditionell mit Raupenkränen oder SPMTs bewegt, die mit einem Portalkransystem ausgestattet sind, das die Montage und Takelage in einer Höhe von über 20 Metern erfordert.
Mit diesem Projekt präsentierte Mammoet erstmals eine Innovation, die den TP-Umschlag für die Offshore-Windenergiebranche sicherer und effizienter macht. SPMTs werden zu riesigen Gabelstaplern – das Ergebnis ist eine schnellere und sicherere Lösung für den Offshore-Windkraft-Rangierbetrieb, so das Unternehmen.
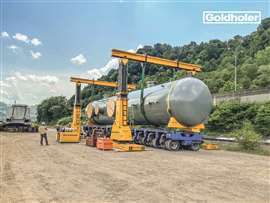
Alle 61 Übergangsstücke wurden von Antwerpen zum BOW Terminal Vlissingen in den Niederlanden verschifft. Jedes Übergangsstück wiegt 400 Tonnen und misst 30 Meter in der Höhe und 6 Meter im Durchmesser. Die TPs wurden in Vierergruppen per Binnenschiff angeliefert, von einem 1.200-Tonnen-Raupenkran an den Kai gehoben und auf temporären Betonstützen abgestellt. Anschließend wurde jedes TP auf einer 2 x 14-achsigen SPMT-Linienkonfiguration gesammelt und zu einem temporären Ablagebereich transportiert. Dort wurden sie auf Stützen abgelegt und warteten auf ihren Abruf. Anschließend wurden sie einfach angehoben und vom Lagerbereich zu einem Aufstellplatz am Kai zurückgefahren.
Bisher waren die SPMT-Anhänger mit einem Portalkransystem ausgestattet, das über dem Übergangsstück montiert und abgestellt wurde, sodass es von oben angehoben werden konnte. Mammoet nutzte nun einen neuen Aufsatz für den SPMT, der ihn praktisch in einen riesigen Gabelstapler verwandelte und so ein schnelleres und einfacheres Anheben der Einheiten von unten ermöglichte.
„BOW Terminal kam auf uns zu und fragte, ob wir ein solches System anbieten könnten“, sagte Lars de Haas, Projektmanager bei Mammoet. „Wir erklärten, dass bereits ein Konzept in Arbeit sei und wir es nur noch entwickeln müssten. Dies dauerte rund vier Monate, einschließlich der gesamten Fertigung und Prüfung – die bei BOW Terminal durchgeführt wurde.“
Der TPH800, wie er genannt wird, verfügt über eine Schwerlasttragfähigkeit von 800 Tonnen. Er besteht aus zwei Hauptquerträgern, die auf zwei Reihen von SPMTs sitzen. An den Querträgern hängen zwei untere Träger, die wie Gabelstaplergabeln wirken. Nähern sich die SPMTs dem TP, hebt sich der vordere Querträger wie eine Parksperre, damit die unteren Träger unter das Übergangsstück geschoben werden können. Sobald diese in Position sind, senkt sich der vordere Träger ab, und der TP wird durch Verstiften beider Querträger mit den beiden unteren Trägern fest fixiert.
Für das Entladen und Beladen der TPs bietet der TPH800 eine RoRo-Lösung, die auf den Einsatz von Kränen verzichtet. Dieser Ansatz wurde bei diesem Projekt jedoch nicht verfolgt. De Haas erläuterte die Gründe.
„Der Kran wurde hier eingesetzt, weil wir im Falle eines Roll-offs größere Lastkähne benötigten und die Gezeiten berücksichtigen mussten“, sagte de Haas. „In Vlissingen beträgt die Flut etwa vier Meter. Mit einem Kran sind wir gezeitenunabhängig und können bei Bedarf rund um die Uhr arbeiten.“
Die Stärke des TPH800 liege darin, dass er ein System zum Heben und Bewegen von Übergangsstücken biete, das sicherer und effizienter sei als bisherige Methoden, doch auch die Flexibilität von Mammoet habe zum Erfolg des Projekts beigetragen, sagte de Haas.
Da zwischen Antwerpen und Vlissingen nur ein einziger Lastkahn pendelte und die Schiffe in Abständen von sieben bis zehn Tagen ankamen, konnte das Team von Mammoet flexibel und schnell eine Mannschaft für die zweitägigen Zeitfenster mobilisieren, die zum Entladen und Lagern der TPs erforderlich waren.
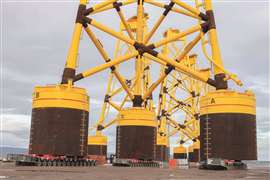
Drehen eines U-Boots
Auch der Transport des 350 Tonnen schweren U-Bootes U17 vom Technikmuseum Speyer zu seinem Schwestermuseum in Sinsheim war eine spektakuläre Demonstration der SPMT-Technologie. Das Kübler-Team transportierte das U-Boot auf 30 Scheuerle InterCombi-Achslinien über Land. Die anspruchsvolle Route und die spezielle Fracht erforderten präzises Manövrieren und zahlreiche Balanceakte. Bei diesem Schwertransport handelte es sich um die weltweit erste Rotation eines U-Bootes auf einem modularen Transporter.
Zehntausende verfolgten im August den Transport des U-Bootes im Fernsehen und im Internet. Das 90 Meter lange und zehn Meter hohe U-Boot musste unter niedrigen Brücken und Hochspannungsleitungen hindurchfahren und die engen Straßen und Wege des hügeligen Kraichgaus befahren. Um sicher unter den Hindernissen hindurchzufahren, musste es mithilfe einer Spezialvorrichtung wiederholt um 70 Grad und mehr um seine Längsachse gedreht werden. Dadurch wurde der Turm zur Seite geschoben, und innerhalb weniger Minuten war die Höhe des Transporters auf die erforderliche Durchfahrtshöhe reduziert.
Der Transport begann auf Rhein und Neckar, wo das U-Boot zunächst auf einen Flussponton verladen wurde, der auf 30 InterCombi-Achslinien der TII Group positioniert war. Sowohl das Be- als auch das Entladen des rund 500 Tonnen schweren Transports auf den schwimmenden Ladungsträger war ein Balanceakt. Der 66 Meter lange und 11,5 Meter breite Ponton musste ständig neu nivelliert werden, um die sich ständig ändernde Ladesituation auszugleichen.
Bevor es zum Roll-off in Haßmersheim kam, mussten die Teams von Kübler, Fischer Kran Transporte, Van der Wees und den Technikmuseen Sinsheim-Speyer gemeinsam die U17 mittels acht Hydraulikzylindern auf eine Höhe von 1,4 Metern aufbocken, damit die 30 Achslinien des Scheuerle InterCombi anschließend zur endgültigen Landung wieder unter das U-Boot fahren konnten.
Auf dem letzten Kilometer zum Technikmuseum Sinsheim strömten Musikkapellen und Tausende Schaulustige herbei. Die Menge bereitete dem U-Boot einen würdigen Empfang, während das Team von Frieder Saam die letzte Kurve auf das Museumsgelände nahm und das Relikt vor seinem zukünftigen Standort abstellte.
BLEIBEN SIE VERBUNDEN
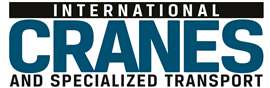
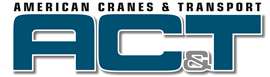
Erhalten Sie die Informationen, die Sie benötigen, genau dann, wenn Sie sie brauchen – über unsere weltweit führenden Magazine, Newsletter und täglichen Briefings.
KONTAKTIEREN SIE DAS TEAM
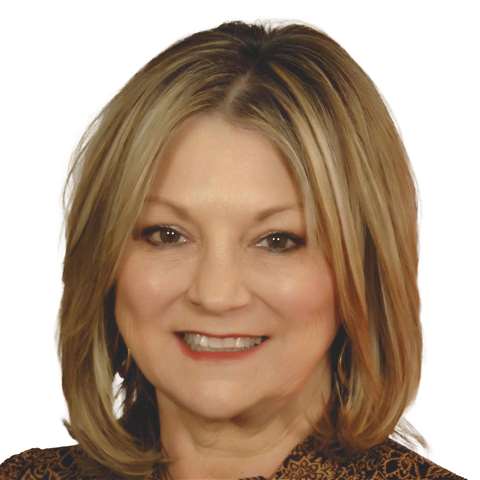
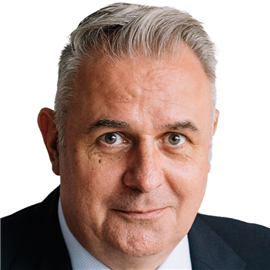
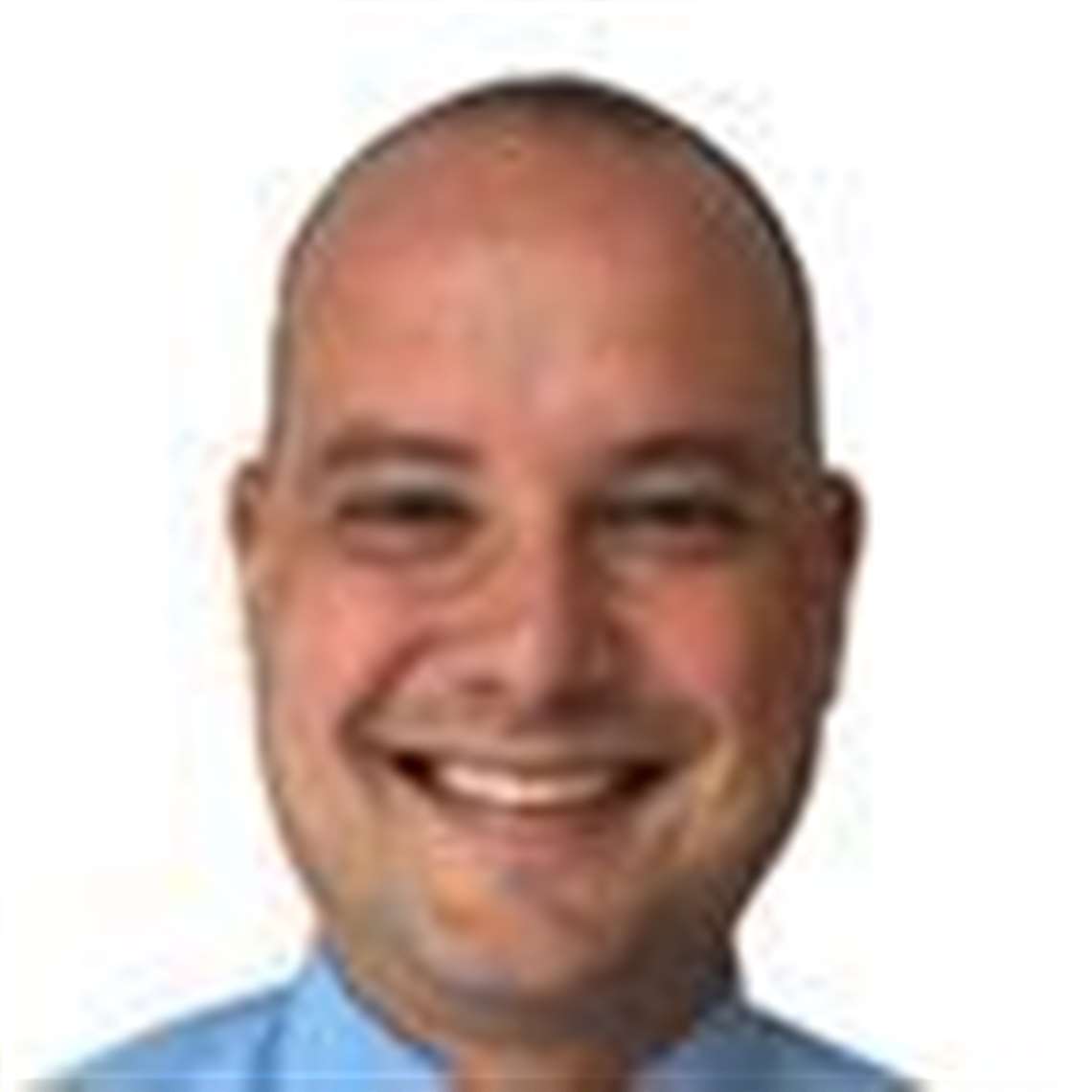
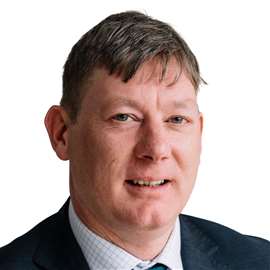