Automatisch von KI übersetzt, Original lesen
Wie Portalkräne Infrastrukturprojekte in den USA revolutionieren
05 August 2024
Wenn es darum geht, über den Tellerrand hinauszudenken und einzigartige Rigging-Lösungen zu entwickeln, sind Portalkrane oft eine flexible Alternative zu riesigen und teuren konventionellen Kränen. Portalkrane werden sowohl im Innen- als auch im Außenbereich eingesetzt und sind eine tragbare und beliebte Lösung im Rigging- und Spezialhebebereich. Diese einfachen, aber leistungsstarken Maschinen können direkt auf der Baustelle eingesetzt werden und sind sofort einsatzbereit.
Vom Heben von Reaktorbehältern in Kalifornien über das Aufstellen eines Generators und die Modernisierung einer Eisenbahnlinie der Chicago Transit Authority bis hin zur Restaurierung eines historischen Kanals hat American Cranes & Transport mehrere interessante Projekte zusammengestellt, die unter Einsatz von Portalkränen durchgeführt wurden.
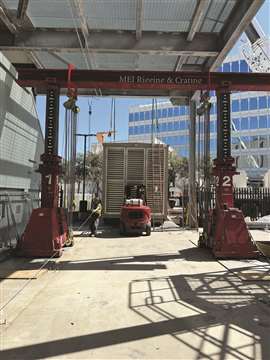
Schlittschuhe und Panzer
MEI Rigging & Crating wurde auf der Baustelle eines komplexen Rechenzentrumsprojekts eingesetzt, um einen Generator in einem begrenzten Arbeitsraum zu installieren. Aufgrund der engen Abstände und der genauen Positionierung des Generators musste das MEI-Team wochenlang Messungen, Berechnungen und kritische Designentscheidungen treffen. Jeder Zentimeter Platz, vom Deckenraum über die Portalkrane bis hin zur MEI-Plattform, wurde ausgenutzt, um den Plan umzusetzen.
Das MEI-Team lud den 50 mal 12 Fuß großen Hilfsrahmen ab, setzte ihn auf eine MEI-Plattform und befestigte den Generator darauf. Die Mannschaft befestigte und platzierte das Gehäuse und fügte alle drei Teile zusammen, um sie als ein Ganzes mit einem Gewicht von 126.000 Pfund zu bewegen. Mithilfe von acht Gleitschuhen und Winden schob das Team den montierten Generator unter die Stahlkonstruktion des Kunden. Vor Ort befestigte das Team den dreiteiligen Generator mithilfe der acht 10-Tonnen-Kettenzüge an dem 250 Tonnen schweren Portalkran. MEI hievte den Generator anschließend bis auf ¼ Zoll an die darüber liegende Stahlkonstruktion heran und platzierte zur Sicherheit kastanienbraune Blöcke darunter. Der nächste Schritt bestand darin, zwei 25 Fuß lange und 12 Fuß breite Stahltanks (je 25.000 Pfund) mithilfe der MEI-Plattform, 1-Zoll-Stiftrollen und Winden zu befestigen, abzuladen und mit Stiftrollen zu versehen. Das MEI-Team rollte jeden Tank vorsichtig mit Stiften unter den Generator, wobei zwischen den Tankstutzen und der Unterseite des Hilfsrahmens nur ein Abstand von 1,27 cm blieb.
Nachdem beide Tanks an ihrem Platz platziert und miteinander verbunden waren, ließ das Team den Generator mithilfe des 250-Tonnen-Portalkrans vorsichtig auf die Tanks herab und achtete dabei darauf, dass alle Bolzenlöcher sowie die Auspuff- und Kraftstoffleitungen ausgerichtet und miteinander verbunden waren.
Komponentenkonfiguration
Bragg Companies wurde beauftragt, vier Reaktorbehälter von Pier F in Long Beach, Kalifornien, zum Hauptsitz von Bragg Companies zu entladen, zu transportieren und dort zu lagern. Die vier Reaktorbehälter wogen zwischen 280 und 583 kip. Dieser Prozess erforderte eine Reihe von Umlade- und Bereitstellungsvorgängen, die von den Kernabteilungen des Unternehmens durchgeführt wurden.
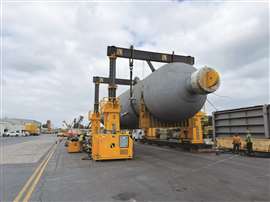
Das 700-Tonnen-Portalkran Modell T1402-4-39 von J&R Engineering wurde für den Transport der Schiffe zur Endlagerung und Lagerung in Long Beach eingesetzt. Die Hydraulikpumpe des Portalkrans wird mit einem Dieselmotor oder 480-V-Drehstrom betrieben. Jedes Schiff wurde angehoben und 1,52 m über dem Boden gehalten, bevor es in die Plattform des Portalkrans eingebracht wurde. Die Besatzung führte bei jedem Umladen ein vorgeschriebenes fünfminütiges Heben und Halten durch.
Die von der internen Konstruktionsabteilung von Bragg entworfenen Kopfträger für diesen Aufzug weisen ein modulares Design mit sieben Komponenten auf, die in fünf verschiedenen Längen von 30 bis 120 Fuß konfiguriert werden können.
Schnelle Bearbeitung
CalPortland Cement mit Sitz in Redding, Kalifornien, befand sich im Frühjahr 2024 in einer schwierigen Lage. Eine ihrer Kugelmühlen benötigte sofort einen neuen Kopf. Die Zeit drängte. Die Mitarbeiter des Werks wandten sich an Machine Repair International – allgemein bekannt als Vezers Industrial Professionals.
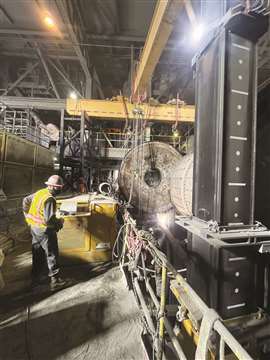
Vezers wurde innerhalb weniger Wochen mit der Arbeit beauftragt. Dieser Auftrag war mit zahlreichen Herausforderungen verbunden. Die Anlage war extrem beengt. Der Mühlenkopf war zwischen einer niedrigen Deckenkonstruktion eingeklemmt, die das Heben auf wenige Zentimeter beschränkte. Um die Mühle herum befand sich eine kleine Öffnung, die nur wenige Zentimeter größer war als die Breite des Kopfes. Unterhalb der Mühle befanden sich Stützen, die den Ein- und Ausstieg des Kopfes in das Gebäude einschränkten. Das Team arbeitete unter Zeitdruck, da CalPortland den Kopf sofort austauschen musste. Vezers wurde außerdem mit der Planung und Konstruktion aller weiteren Stützstrukturen beauftragt, die für die Demontage des Kopfes erforderlich waren.
Die unternehmenseigenen Ingenieure entwarfen ein Doppelstützsystem, das von Rigging Gear Sales geliefert wurde. RGS lieferte und transportierte innerhalb von zehn Tagen ein Hebesystem mit einem 500-Tonnen-Kraftturm (Modell 34FBG5400WTI), zwei 40-Fuß-Hohlkastenträgern, einem 400-Tonnen-Seitenschieber mit verstellbaren Hubverbindungen, vier 10-Fuß-Abschnitten einer 20-Zoll-Laufbahn, zahlreichen Gleishebebühnen und mehreren hochqualifizierten Bedienern querfeldein. Die Montage war innerhalb eines Tages abgeschlossen.
Geladen und entsichert
Clark Rigging and Rental hat seinen Hauptsitz in Lockport, New York, am berühmten Eriekanal und bietet einen Jahresvertrag für alle Kran- und Takelagedienstleistungen im gesamten New Yorker Kanalsystem an. In diesem Jahr umfasste das Projekt des Teams die Entwicklung eines Konstruktions- und Bauplans für die Wartung der unteren Schleusentore an Schleuse E4 in Waterford, New York.
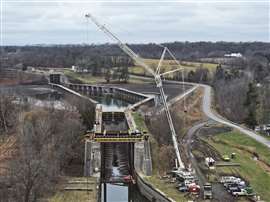
Schleuse E4 hat einen vertikalen Hub von etwa 10,7 Metern. Das bedeutet, dass sich der Wasserunterschied zwischen der oberen und unteren Kammer während der Schleusenfahrt um 10,7 Meter ändert. Große Stahltore dienen als Türen zum Verschließen der Kammer. Anschließend reguliert eine Pumpe den Wasserstand, sodass Boote sicher flussaufwärts oder flussabwärts fahren können. Die unteren Tore von Schleuse E4 sind 7,6 Meter breit, 18 Meter hoch, 1,2 Meter tief und wiegen jeweils 57.600 Kilogramm.
Clark schlug vor, ein Portalkransystem zu entwerfen, zu konstruieren, herzustellen und zu implementieren, mit dem beide Tore aus ihren Angeln gehoben, in die Schleusenkammer hinein verschoben und in der vertikalen Position stabilisiert werden könnten, sodass wichtige Wartungsarbeiten an den Toren sicher durchgeführt werden könnten.
Eine kritische Komponente
Fagioli war am Transport und der Installation eines neuen Gepäckabfertigungssystems am internationalen Flughafen von Houston beteiligt.
Fagioli transportierte eine Brücke mit SPMTs und Gittermasten vom Fertigungsbereich zum Montagebereich. Am Ende der Brücke befestigte Fagioli Hebebalken mit vier Litzenhebern (je 50 Tonnen Tragkraft), die dann für den letzten Hebevorgang verwendet wurden. Zusätzliche Stützplatten an den Enden der Balken waren erforderlich, damit die festen Anker und Litzenheber korrekt auf den Strukturbalken sitzen konnten.
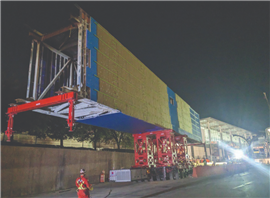
Fagioli plante drei Nächte für Straßensperrungen ein. In der ersten Nacht bewegten SPMTs die Brücke in weniger als 30 Minuten. In der zweiten Nacht bereitete Fagioli weitere SPMTs mit sechs Achslinien vor, die auf 120 hölzernen Kranmatten positioniert wurden. Die in der Mitte positionierten SPMTs wurden entfernt, und die hinten positionierten begannen mit dem Manövrieren, um die Brücke für den letzten Hebevorgang auszurichten. Die Brücke wurde hydraulisch auf die geplante Höhe gehoben. Anschließend wurde die Brücke mit dem Litzenhebesystem verbunden, das an den Enden der Träger unter dem schweren Gegenstand positioniert war. Das Litzenhebesystem hob die Brücke an. In der letzten Nacht wurde die Brücke auf ihre endgültige Höhe gehoben.
Riverside-Takelage
Oxbo Mega Transport Solutions wurde von JH Kelly Industrial Contractors mit dem Heben, Transportieren und Installieren eines neu gefertigten Galerieförderbands beauftragt. Es ist 95 Meter lang, 3,6 Meter breit, 4,8 Meter hoch und wiegt fast 250 Tonnen. Das Projekt wurde im Dezember 2023 am unteren Columbia River zwischen Oregon und Washington durchgeführt.
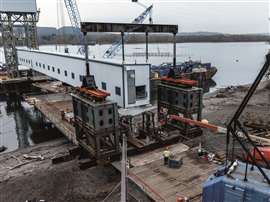
In der Fertigungsanlage hob das Oxbo-Team die Struktur um 4,5 Meter an, um sie für die Montage der Stahlkonstruktionen vorzubereiten. Die Mannschaft nutzte SPMTs zum Anheben der Galeere und setzte anschließend ein Blockiersystem ein. Das Förderband wurde mithilfe von 28 Reihen von Oxbo Goldhofer PST/SLE-Modulen ferngesteuert auf ein Lastkahn gefahren. Die Mannschaft musste die Galerie vom Offshore-Lastkahn zwischen zwei festen Türmen mit weniger als 15 Zentimetern Abstand manövrieren. Anschließend wurde das landseitige Ende der Galerie an einen 300-Tonnen-Derrickkran übergeben, um die Positionierung auf einer Arbeitsbrücke zu unterstützen.
Das landseitige Ende der Galerie musste etwa 7,3 Meter über ein bereits erhöhtes Fundament an der Flusszufahrtsseite angehoben werden. Diese endgültige Erhöhung ermöglichte die Installation des permanenten „Ständers“.
Schwere Querträger wurden auf dem Fundament installiert, um das modulare Fachwerksystem von Oxbo zu stützen. Die 400 Tonnen schwere Galerie wurde anschließend mithilfe des 400-Tonnen-Portalkrans in einer langen Takelagekonfiguration um drei Meter angehoben, um sie vorübergehend zu stützen und neu zu rüsten.
Reden wir über den Transit
Der MJ55HD Travelift von Mi-Jack spielt eine zentrale Rolle im Modernisierungsprogramm der Red & Purple Line (RPM) in Chicago, dem größten Investitionsprojekt in der Geschichte der Chicago Transit Authority (CTA). In Zusammenarbeit mit dem Walsh-Fluor Design-Build Team übernimmt der MJ55HD von Mi-Jack die effiziente Positionierung von Betonsegmenten in der bestehenden Infrastruktur, was für den Erfolg des Projekts entscheidend ist.
Der speziell für städtische Baustellen konzipierte MJ55HD kann dank seiner kompakten Größe problemlos unter einem Verschubkran betrieben werden und bewältigt enge Bereiche problemlos. Diese Fähigkeit ist entscheidend für maximale Effizienz und minimale Störungen für Arbeiter und Pendler. Seine Geschwindigkeits- und Sicherheitsfunktionen machen ihn zudem für stark frequentierte Bereiche geeignet und gewährleisten einen reibungslosen Bauablauf ohne Beeinträchtigung der Sicherheitsstandards.
BLEIBEN SIE VERBUNDEN
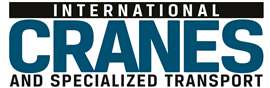
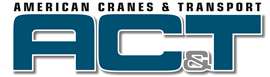
Erhalten Sie die Informationen, die Sie benötigen, genau dann, wenn Sie sie brauchen – über unsere weltweit führenden Magazine, Newsletter und täglichen Briefings.
KONTAKTIEREN SIE DAS TEAM
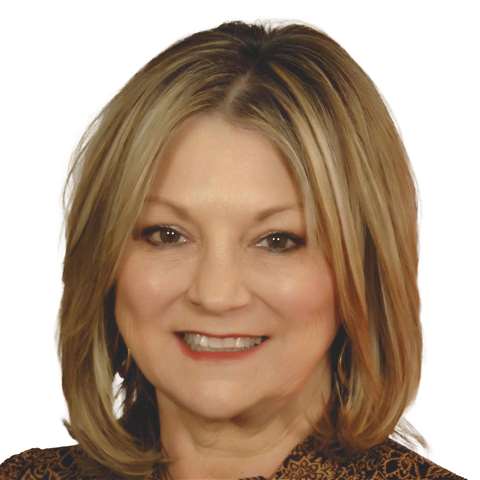
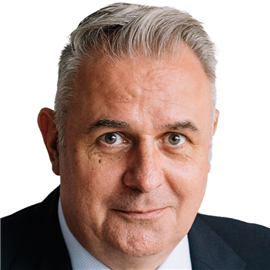
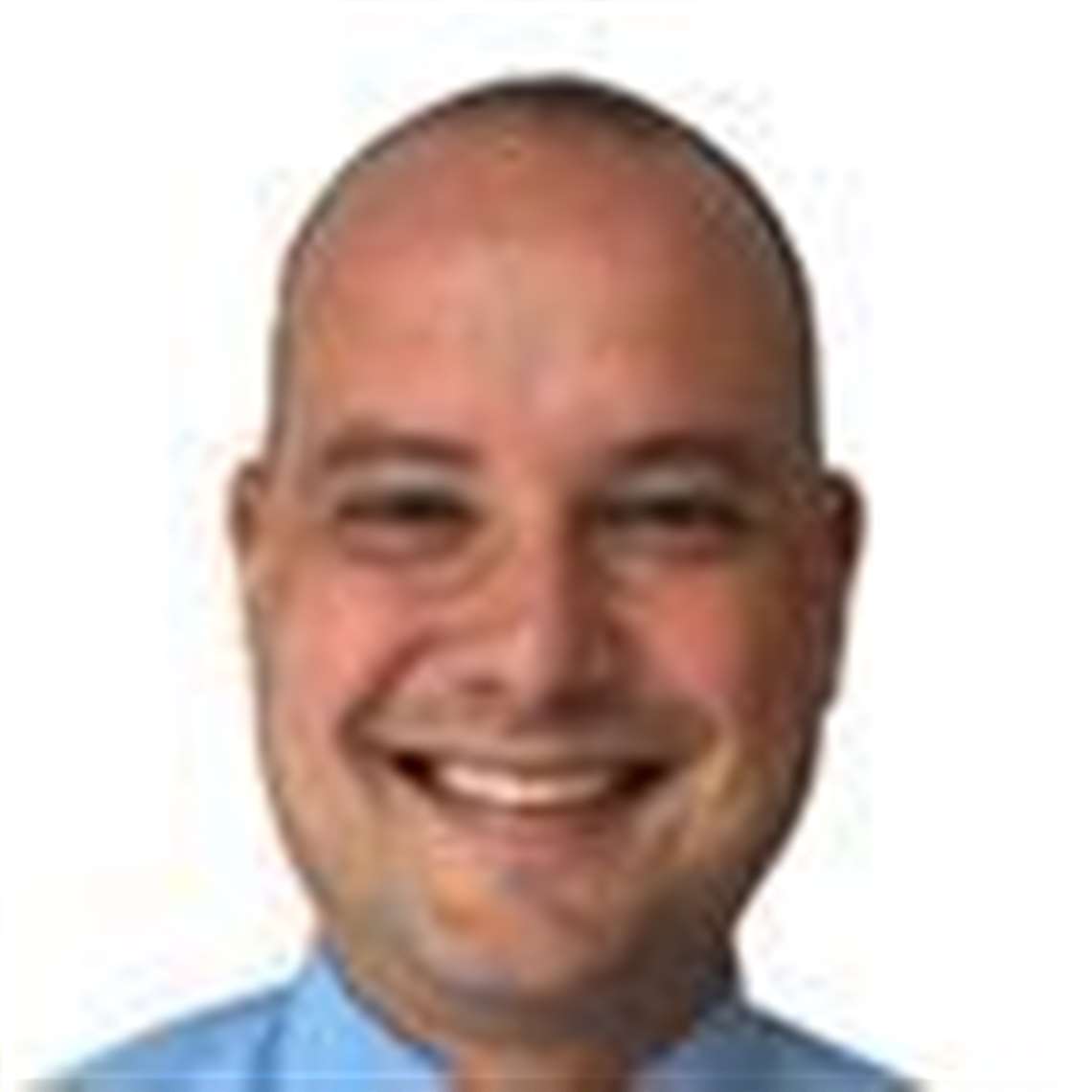
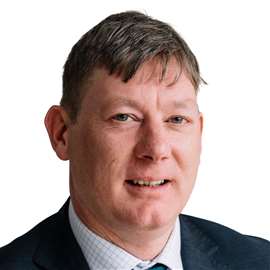