Examining the EMR barrier: critical but inaccurate
24 March 2025

Construction companies are often penalised despite them having strong safety records.
In the crane, construction, and heavy transport industries, safety is more than a regulatory requirement – it’s a critical factor in business sustainability. Companies across North America and Europe invest heavily in safety programmes, worker training, and oversight to minimise risk and maintain operational efficiency.
Yet, despite these efforts, one number – experience modification rate (EMR) – often dictates whether a company can even qualify for a project within the USA. Originally designed as an insurance underwriting tool, EMR has evolved into a gatekeeping metric that can determine a company’s eligibility for contracts.
EMR was developed to assess a company’s workers’ compensation claims experience, with a baseline score of 1.0 representing the industry average. A company with an EMR below 1.0 is considered safer than its peers, while a rating above 1.0 suggests higher risk. Because insurance premiums are calculated based on this metric, a high EMR can significantly increase costs. Many general contractors and project owners, however, now use EMR as a primary qualification factor, often disqualifying companies with a rating over 1.0 – regardless of the context behind the number.
“A recent discussion on EMR was held during SC&RA’s Insurance & Risk Management Committee meeting at the January Board and Committee Meetings and represents just one of many topics the committee addresses for member education,” said SC&RA CEO Joel Dandrea. “SC&RA’s committees enable the Association to identify key advocacy and education priorities, like this, that warrant attention and ultimately help deliver direct benefits to our members.”
EMR is critical but inaccurate
Jeff Haynes, at USI Insurance Services, is a member of that committee, and pointed out, “The problem is that EMR is not a real-time indicator of a company’s safety culture or operational risk. It’s based on a three-year rolling average of claims data, meaning past incidents continue to affect a company’s EMR long after safety improvements have been made. From a crane company’s perspective, EMR is critical, but this delayed reflection of past claims creates an inaccurate snapshot of current safety performance.”
Compounding the issue, third-party compliance platforms – such as ISN and Avetta – play an increasing role in contractor prequalification for major projects, requiring businesses to submit extensive documentation. These platforms act as intermediaries, determining whether a company meets a client’s safety standards. Their rigid processes, however, often fail to account for nuances, leading to well-managed companies being flagged simply due to statistical anomalies in their claims history.
“This inconsistency leaves contractors with few options,” Haynes added. “If a company’s EMR rises above 1.0, securing a variance from a general contractor becomes a daunting process requiring detailed explanations, mitigation plans and sometimes even personal meetings with decision-makers.”
This issue isn’t unique to the United States. Across Canada, Mexico and Europe, construction and transport professionals face similar challenges when navigating safety assessments and compliance requirements. Many jurisdictions have their own variations of EMR – such as Canada’s experience rating system for workers’ compensation or the UK’s employer liability frameworks – but the fundamental problem remains: companies are often judged by an outdated number rather than their actual safety performance.
Accurate reflection
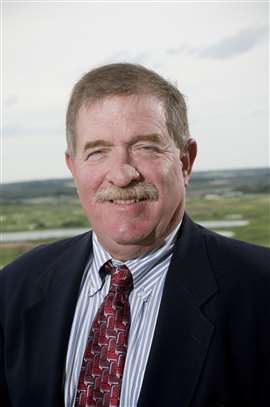
For crane and construction companies, understanding EMR and its implications is crucial. More importantly, advocating for a more holistic evaluation process – one that considers safety investments, training programmes and real-time performance – may be the key to ensuring businesses are judged not by a historical number but by their actual commitment to safety.
Robert Moore, at Moore & Associates Law, and a member of SC&RA’s Insurance & Risk Management Committee, emphasised that construction professionals must recognise EMR does not account for fault. “An employer may not be at fault at all but still must pay under the workers’ compensation system,” he explained. “For instance, if an employee ignores company safety rules and gets hurt, the employer still carries the financial burden – and that affects EMR. It’s just not an accurate reflection of a company’s safety record.”
This disconnect between reality and calculation has led to growing frustration among construction and transport professionals worldwide. Many companies are seeking better ways to represent their safety culture beyond EMR. Haynes suggested that insurance brokers can help by auditing and verifying EMR data for inaccuracies.
“You can’t change NCCI’s [National Council on Compensation Insurance] calculation, but as a broker, you can scrub the data to ensure payroll figures are correct and verify that all claims actually belong to the company,” he said. “If errors are found, they can request a recalculation.”
Moore added that companies are increasingly fighting back against unfavourable EMRs by meticulously documenting their own safety performance. “Keeping accurate and detailed records of incidents – especially those where the company was not at fault – is crucial,” he said. “If you can show clients that certain claims had nothing to do with your company’s safety practices, you can offset a bad EMR.”
Making it work
Another effective strategy is tracking commercial general liability (CGL) claims alongside workers’ compensation claims. “If you can demonstrate zero losses on your CGL policy over multiple years, that reinforces the argument that your EMR isn’t an accurate reflection of your actual safety culture,” Moore noted. “That’s something we’ve used successfully in conversations with clients.”
Haynes agreed that companies must take control of their own narrative. “ISN and Avetta rely on checkboxes rather than a nuanced safety assessment. Companies have to put in the work to track and present their safety data rather than relying on third-party systems to do it for them.”
Control the controllables
Looking ahead, both Haynes and Moore see room for improvement in how EMR is used. “ISN and Avetta’s clients are realising that they’re boxing out good, safe companies based solely on EMR,” Haynes emphasised. “I expect alternative evaluation methods will emerge, allowing contractors to demonstrate safety beyond a single metric. The current approach eliminates qualified companies based on a narrow and outdated calculation, and some are beginning to recognise the flaws in the system and look for better ways to evaluate safety. The industry needs a broader set of criteria beyond EMR, such as loss-time rates and CAB scores, to provide a more accurate picture of a company’s safety culture.”
Moore believes artificial intelligence and advanced data analytics could also play a role. “AI has the potential to identify trends in safety culture that EMR calculations miss,” he said. “But at the end of the day, a true safety culture has to come from leadership. AI might help with tracking data, but it won’t replace a strong top-down commitment to safety.”
For now, according to both men, companies navigating EMR challenges should focus on what they can control: record-keeping, transparency and advocating for a more comprehensive view of safety. “If you’re struggling with EMR, look at your data, analyse trends and take proactive steps to prevent future incidents,” Moore advised. “The more documentation and proof you have of your safety efforts, the better positioned you’ll be to challenge a number that doesn’t tell the full story.”
STAY CONNECTED
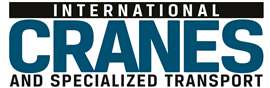
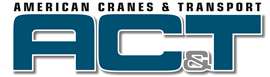
Receive the information you need when you need it through our world-leading magazines, newsletters and daily briefings.
CONNECT WITH THE TEAM
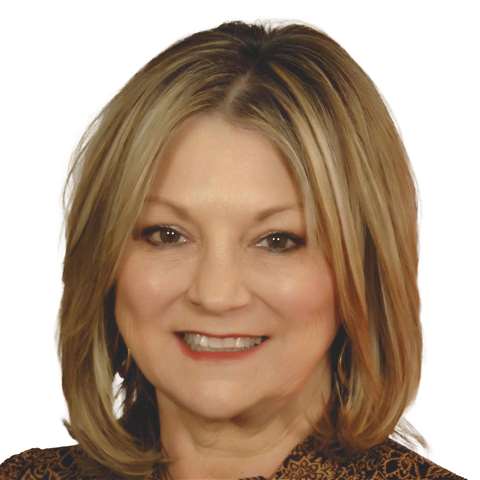
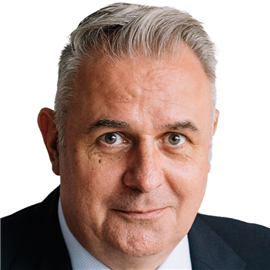
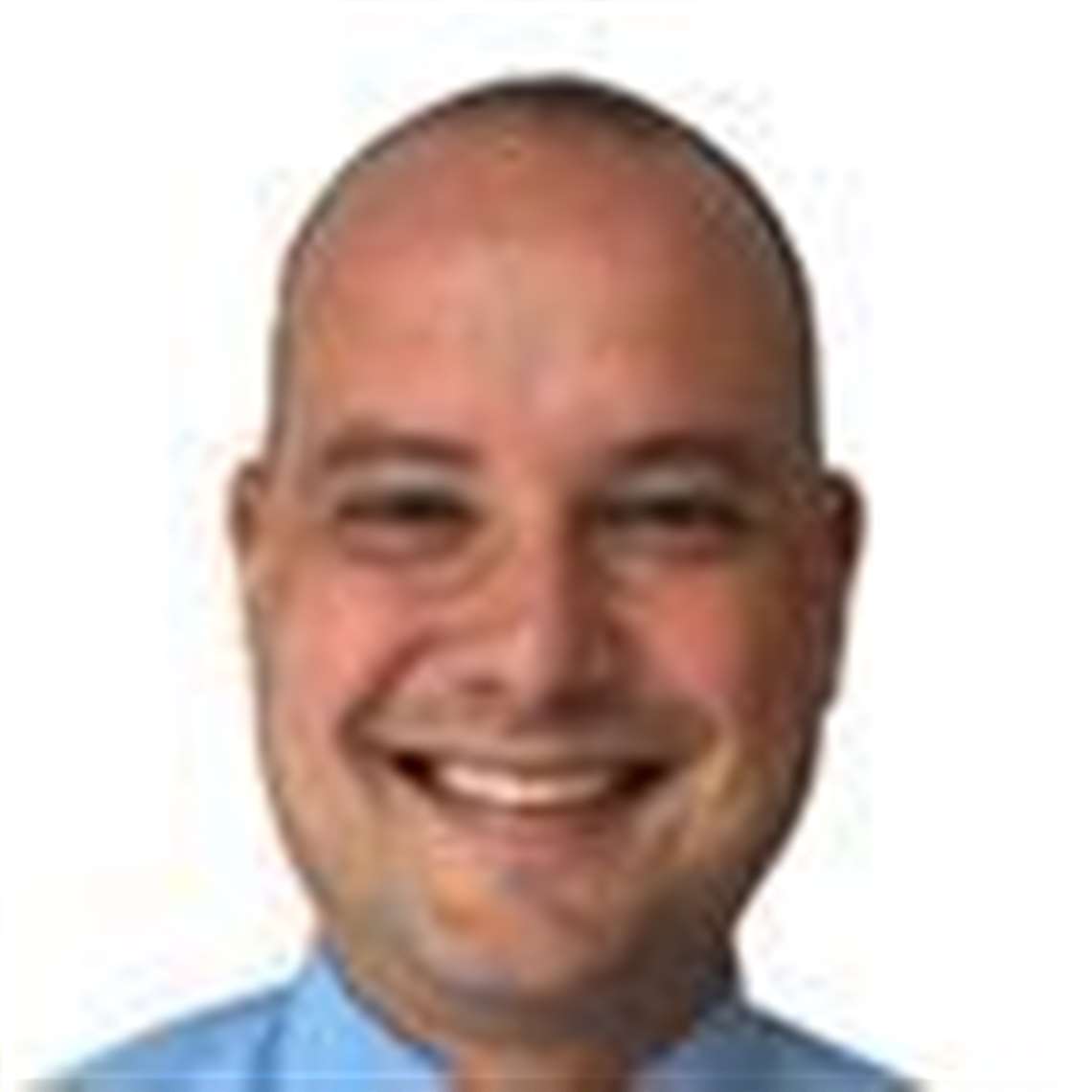
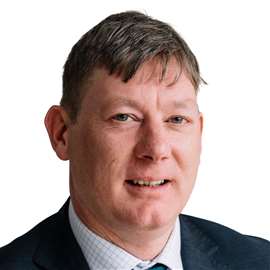