Automatically translated by AI, read original
Mammoet déplace un énorme concasseur pour Codelco
11 mars 2025
Pendant plus de 18 mois, l'équipe de Mammoet a conçu l'itinéraire, la méthodologie et le plan pour réaliser l'opération de déplacement des pièces de concasseur d'une mine à une autre.
L'équipement minier est volumineux et lourd, et il est constamment déplacé d'un endroit à un autre. Une fois les ressources extraites, il doit être démobilisé et déplacé vers un autre site pour reprendre son activité.
Mais déplacer des équipements miniers est un processus compliqué, comme ce fut le cas pour Codelco, la société minière de cuivre publique du Chili qui exploite des mines près de la ville de Calama.
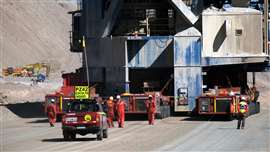
Codelco a sollicité l'aide de Mammoet pour déplacer les pièces clés du concasseur d'un site à un autre, distant d'environ 4,5 kilomètres. Seize composants devaient être déplacés, dont les six plus gros constituent l'essentiel du système de concassage qui extrait les matériaux des mines et les décompose en plus petits morceaux.
Codelco n'avait jamais mené d'opération d'une telle ampleur auparavant. L'entreprise a contacté Mammoet pour obtenir des conseils sur les meilleurs équipements de levage et de transport lourds, ainsi que des solutions d'ingénierie pour atteindre son objectif. Les ingénieurs de Mammoet ont proposé différentes méthodes d'extraction pour permettre le déplacement des composants clés en unités entières, réduisant ainsi les coûts et permettant l'achèvement du projet plus tôt que prévu, selon Mammoet.
Ce projet marquait la première collaboration directe de Mammoet avec Codelco et la première fois que ce site nécessitait le déplacement d'un concasseur. La planification de l'itinéraire, de la méthodologie et des équipements de levage et de transport lourds nécessaires à l'opération a constitué la première étape, avec l'assistance des ingénieurs de Mammoet à chaque étape.
« Nous avons travaillé avec Codelco pendant un an et demi sur la planification », explique Vanessa Labana, directrice commerciale de Mammoet. « Nous avons créé tous les plans et dessins d'itinéraire et les avons aidés à répondre à toutes les questions et considérations auxquelles ils ont dû faire face sur le chantier. Par exemple, la pente, les rapports de braquage et la largeur de la route pour faciliter l'itinéraire de transport le plus rapide. »
L'un des plus grands défis a été de trouver et de mobiliser l'équipement et le personnel nécessaires à un projet d'une telle envergure. L'équipe de Mammoet a mutualisé ses ressources mondiales, utilisant un transporteur modulaire automoteur (SPMT) venu de Malaisie, des systèmes de débardage venus des États-Unis et du matériel supplémentaire provenant de Colombie.
Différentes approches
Six composants clés devaient être déplacés, et la méthode de retrait et de transport était différente pour chacun. La plupart ont été soulevés à l'aide de vérins d'escalade, puis déplacés à l'aide de SPMT équipés de poutres de support. Pour le système d'entraînement, la même approche a été utilisée, mais avec l'ajout d'un système de glissement. Ce système a permis de faire glisser le composant sur 12 mètres avant de le descendre à sa position finale. Les deux éléments les plus lourds à transporter et à soulever étaient le silo (1 100 tonnes) et le concasseur lui-même (1 300 tonnes), ce dernier étant le plus complexe des six mouvements de cargaison.
« Nous avons créé une poutre de support spécialement adaptée à cette cargaison », explique Labana. « Nous avons dû modifier nos poutres d'origine en appliquant des renforts en plomb sur le dessus, aux quatre points de levage, pour éviter toute déformation. »
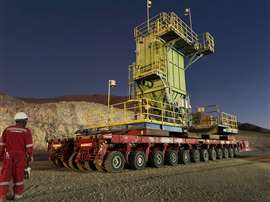
Le concasseur a été extrait de son logement à l'aide de chenilles et de patins, avant d'être soulevé suffisamment haut pour permettre au SPMT de passer en dessous. Des arrimages ont été utilisés pour renforcer le support et maintenir l'ensemble en position pendant le trajet de 4,5 km. Une zone proche du lieu de démobilisation a été créée pour permettre une rotation à 180 degrés du concasseur afin qu'il soit correctement positionné pour l'installation.
Une fois arrivé sur le site d'installation, le processus précédent a été répété en sens inverse : les remorques SPMT ont déposé la cargaison sur des chenilles pour la remettre en place. La galerie a également posé problème, le sol n'étant pas parfaitement plat, avec une pente de 1 %. Par conséquent, deux vérins hydrauliques ont été utilisés pour effectuer des levages lourds à l'arrière, à trois intervalles différents, afin de maintenir l'ensemble à niveau pendant le déplacement vers l'avant.
L'opération a été réalisée en un peu plus d'un mois, soit moins de temps que prévu, principalement grâce au retrait des pièces du concasseur en unités complètes. Cela a permis à la mine de reprendre rapidement ses activités. Labana a expliqué que Mammoet avait géré l'équipe, l'équipement et les étapes d'ingénierie pour mener le projet à bien en toute sécurité et efficacité, en mobilisant tout sur le site dans les délais et en évitant les retards et pénalités coûteux. Une équipe de 70 personnes et un total de 160 lignes d'essieux SPMT, huit patins (500 tonnes), huit systèmes de levage (400 tonnes), ainsi que des poutres de soutènement, des rails et des dispositifs d'arrimage, ont été utilisés tout au long du projet.
« Si ce projet avait été réalisé de manière conventionnelle, Codelco aurait dû découper et démonter l'équipement, ce qui aurait pris beaucoup de temps », explique Labana. « C'est la première fois que Codelco réalise une telle opération. Avec nous, ils ont un partenaire pour leurs futurs projets grâce à la confiance qu'ils accordent à notre expérience, à notre équipement et à notre expérience. »
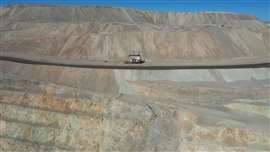
STAY CONNECTED
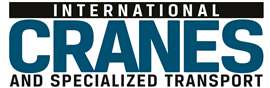
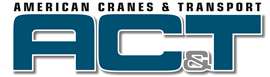
Receive the information you need when you need it through our world-leading magazines, newsletters and daily briefings.