Article traduit automatiquement par l’IA, lire l’original
Mouvements monumentaux : au cœur de certaines des opérations complexes de gréement et de transport de 2024
28 octobre 2024
Edwards Moving & Rigging (EMR) a récemment mené à bien un projet de transport et de montage monumental nécessitant une expertise pointue en la matière. Dans le cadre d'un projet de démantèlement sensible, EMR a transporté avec succès quatre composants radioactifs de classe 7 de Floride vers un site d'enfouissement au Texas. Cette opération complexe, qui a nécessité des mois de planification, a nécessité une logistique multimodale, un montage sophistiqué et une coordination précise entre de nombreux organismes et infrastructures de l'État.
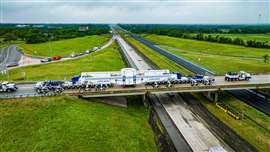
La première phase consistait à transporter les composants depuis une zone de transit en Floride jusqu'à un site de débarquement sur barge. EMR a utilisé un Goldhofer PST à 3 files et 12 lignes pour transporter les quatre composants – deux unités plus petites et deux plus grandes – sur une barge à pont de 15 mètres de large sur 60 mètres de long. Les deux unités plus petites ont été fixées sur des supports et des poutres, tandis que les plus grandes ont été mises en place grâce au système à faible pression d'EMR, conçu pour répartir uniformément le poids des composants. Cela a permis de charger les quatre unités sur une seule barge.
Une fois sécurisée pour les mouvements latéraux, longitudinaux et ascendants, la barge a traversé le golfe du Mexique pour arriver au terminal de Rockport à Aransas Pass, au Texas. Le processus a ensuite été inversé, EMR ayant utilisé une technique RORO pour décharger la cargaison.
Plusieurs mois avant le départ de la barge, EMR a entamé un processus intensif de planification d'itinéraire avec le TXDOT et des ingénieurs de ponts tiers. Compte tenu du poids et de la taille du transport, qui culminaient à 1 553 344 livres pour 300 pieds de long, 21 pieds 5 pouces de large et 17 pieds 2 pouces de haut, il était crucial de garantir que les routes et les ponts puissent supporter une charge extrêmement lourde.
Le processus de planification a duré huit mois et a impliqué 11 des 25 districts de transport du Texas. Chaque district posait ses propres défis, plusieurs nécessitant des fermetures de routes, des déviations de la circulation et des plans de contrôle du trafic. L'analyse rigoureuse d'EMR a permis de garantir que le transport puisse se dérouler sans endommager les infrastructures ni perturber la vie publique.
Une fois les permis obtenus et l'itinéraire finalisé, EMR a entamé un voyage routier de plus de 1 450 kilomètres jusqu'au site d'élimination. Le convoi a franchi 158 ponts, utilisant des chariots sur 150 d'entre eux et effectuant des sauts de pilier à pilier sur trois ponts. L'équipe a également géré deux mouvements à contresens, fermant temporairement des sections de l'autoroute et se déplaçant en sens inverse pour accueillir la charge surdimensionnée. À un moment donné, une section de l'autoroute 20 a été fermée pour permettre le transport.
Outre les défis techniques, des obstacles logistiques, comme le retrait de 73 panneaux de signalisation et l'utilisation de camions-nacelles pour franchir les fils électriques et les feux de circulation, ont complexifié l'opération. Des escortes policières et civiles ont assuré la sécurité publique et la circulation dans les villes comme dans les zones rurales.
L'un des défis techniques les plus importants concernait le transport des composants radioactifs les plus volumineux à l'aide du système de pont à poutres hautes Goldhofer Faktor 5. Ces composants ne disposaient pas de points d'arrimage traditionnels, généralement nécessaires à la sécurisation des marchandises pendant le transport. L'équipe d'ingénierie d'Edwards a conçu une solution utilisant des chaînes synthétiques pour envelopper et sécuriser la cargaison, conformément aux normes du TXDOT.
Une fois arrivés au site d'élimination, les composants ont été transportés sur le dernier kilomètre à l'aide d'un Goldhofer à 3 files et 12 lignes et d'un système de portique de 900 tonnes, qui déchargeait et déposait les composants au sol.
Réglage d'une presse ONA
Taylor Crane & Rigging a fourni la supervision, la main-d'œuvre et l'équipement nécessaires au déchargement et au réglage préliminaire d'une presse ONA. L'équipement utilisé pour ce projet comprenait deux vérins de 690 tonnes, des palonniers, des palonniers de levage, des maillons de levage et du matériel de levage, un Versa-Lift 40/60 et un chariot élévateur de 15 000 tonnes.
Remplacement de l'autoclave
Une entreprise manufacturière d'Arlington, dans l'État de Washington, a décidé de moderniser son équipement de traitement sous pression des poteaux téléphoniques – un autoclave de 45 mètres de long et de 2,4 mètres de diamètre – en l'équipant d'un système plus grand afin d'augmenter son volume de production. Cependant, l'autoclave de 72 tonnes se trouvait dans une fosse souterraine, sous un hangar à poteaux couvert, avec une fosse à machines juste en dessous.
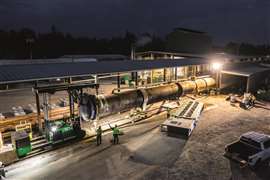
En faisant appel à l'équipe de déménagement de machines d'Omega Morgan à Seattle, l'entreprise avait besoin d'une solution complète pour retirer la cuve d'origine, transporter le nouvel autoclave et l'installer sur son site actuel, tout en minimisant les temps d'arrêt de production. Les équipes d'Omega Morgan ont répondu présent et proposé une solution de pointe.
Plusieurs mois avant le déménagement, l'équipe de déménagement des machines a fait appel aux équipes spécialisées en transport et en grue d'Omega Morgan. Elles allaient jouer un rôle essentiel dans la prise en charge et le transport du nouvel autoclave de 104 000 kg depuis Sandy, dans l'Oregon.
L'équipe de transport spécialisée a commencé à demander des permis de super chargement auprès des autorités de l'Oregon et de l'État de Washington - ce qui prend entre 45 et 60 jours - tandis que l'équipe de déplacement des machines planifiait le déménagement en plusieurs étapes.
Bien que sa longueur soit maintenue à 45 mètres, le nouvel autoclave a gagné 60 centimètres de diamètre pour occuper le même espace que la cuve d'origine. Au cours de plusieurs réunions et visites sur le site d'Arlington et dans l'usine de Sandy, l'équipe a discuté des modifications à apporter à la conception du nouvel autoclave de 104 tonnes et a déterminé l'équipement nécessaire aux opérations de démontage et d'installation.
Après avoir obtenu les permis, l'équipe spécialisée en transport d'Omega Morgan s'est concentrée sur le transport du projet. Elle a opté pour une remorque modulaire double, construite sur mesure par Omega Morgan, pour le transport entre Sandy et Arlington.
Le projet a été réparti entre les différents services afin de minimiser les interruptions de production pour le client. Une fois les permis, les équipements et les équipes prêts, l'équipe de déménagement des machines a exécuté la première étape du projet.
Pendant trois jours passés sur le site d'Arlington, l'équipe de quatre personnes d'Omega Morgan a utilisé des crics pour soulever l'autoclave avant de le faire glisser sur les patins qui soutenaient sa base. D'autres levages et calages ont permis de le hisser suffisamment haut pour qu'il puisse franchir la fosse, tout en restant sous le toit. L'équipe a ensuite utilisé le Tri-lifter pour le sortir du reste du chemin. Un SPMT a été glissé sous la cuve et l'a éloigné de la fosse pour son démantèlement.
La phase suivante du chantier a débuté à Sandy, dans l'Oregon. L'équipe de transport spécialisée, composée de quatre personnes, a rejoint l'équipe de grue et les grues de 200 et 350 tonnes à l'usine de fabrication d'autoclaves. Après avoir soulevé le nouvel autoclave de 3 mètres de diamètre de ses cales, l'équipe de maintenance a placé le composant entre les deux remorques modulaires sur mesure, les reliant. Après avoir arrimé l'autoclave, l'équipe a pris la route. Malgré les fermetures de routes, la régulation du trafic et l'escorte des pilotes, la charge de 5,5 mètres de large a effectué le trajet en trois jours.
De retour à Arlington, l'équipe d'installation a soulevé l'autoclave à l'aide de Tri-lifters avant de le placer sur un rail coulissant et de repousser le composant vers la fosse. L'installation a duré six jours, le temps que l'équipe soulève et glisse la cuve en place.
Remplacement du pont ferroviaire
En juillet, dans le Vermont, Buckingham Heavy Transport a soulevé et transporté un pont ferroviaire à travée unique de 38 mètres sur 6,7 mètres et 15 centimètres, de sa zone de préparation jusqu'à ses culées permanentes. Le pont a été fabriqué sur un terrain adjacent, à quelques centaines de mètres des culées.
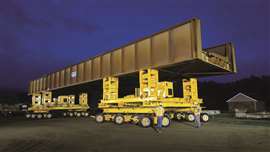
L'équipe de Buckingham a soulevé le pont de 555 000 livres à une altitude de 16 pieds à l'aide de cales et de vérins, puis a assemblé des transporteurs de chariots personnalisés composés de chariots électriques et de montagnes russes Buckingham, de trois niveaux de poutres en acier et de supports de 150 tonnes en dessous.
Un système coulissant Buckingham a ensuite été intégré entre les poutres pour permettre un réglage latéral. Les ponts ont ensuite été installés sur le terrain.
La flotte d'équipements sur mesure de Buckingham a permis à l'équipe de terminer la pose du pont dans les délais serrés du client. La capacité de déplacement en crabe des chariots de Buckingham a permis à l'équipe de déplacer la section du pont en diagonale depuis la zone de préparation jusqu'à son alignement avec les culées, sans manœuvres chronophages.
Les systèmes intégrés de coulissement et de levage ont permis à l'équipe d'ajuster le placement du pont avec précision et rapidité sur place.
La liste des équipements requis était longue et comprenait des chariots Buckingham Power et Coaster, des crics Buckingham Crib de 30 tonnes, des machines de levage unifiées Buckingham à 12 ports, des unités d'alimentation Buckingham et le système de glissière Buckingham.
Manipulation des bobines
Chez Nucor Steel Gallatin à Ghent, dans le Kentucky, une manutention efficace des matériaux est essentielle au bon fonctionnement des processus de production. Pour répondre à cette demande, Nucor s'appuie sur le portique sur pneus Mi-Jack Products d'une capacité de 70 tonnes, équipé d'un accessoire de manutention de bobines sur mesure et d'un crochet rotatif hydraulique, spécialement conçu pour les applications de levage spécialisées.
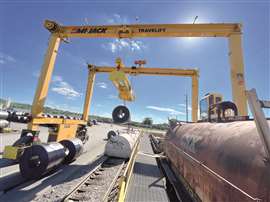
La grue à portique sur pneus en caoutchouc (RTG) Travelift MJ70HD est équipée de l'accessoire spécialisé de manutention de bobines de Mi-Jack, qui comprend un crochet rotatif à commande hydraulique conçu pour
soulever et faire pivoter de lourdes bobines d'acier avec précision tandis que les wagons se déplacent en dessous.
La conception permet le chargement et le déchargement transparent des bobines dans les wagons de l'usine de Gallatin, où plus de 3 millions de tonnes de bobines à bande chaude sont produites chaque année.
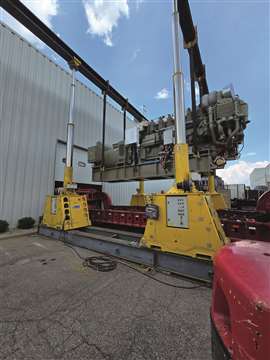
« La combinaison du Mi-Jack Travelift, de la barre d'écartement rotative et du crochet en C améliore à la fois la productivité et la sécurité en éliminant le besoin de gréement au sol et en maintenant le personnel à une distance de sécurité pendant le levage des bobines.
« ou descendus dans des wagons », a déclaré Mike Lanigan, vice-président des ventes de Mi-Jack.
Chez Nucor Steel Gallatin, le Mi-Jack Travelift réduit considérablement le temps de manutention des bobines. Sa conception sur mesure lui permet de travailler au-dessus des wagons en mouvement grâce à ses spécifications de largeur et de hauteur adaptées. Sa capacité de 70 tonnes, associée au crochet rotatif et au crochet en C, permet aux opérateurs de charger quatre bobines d'acier par wagon en moins de 30 minutes, puis de les acheminer vers leur destination suivante, garantissant ainsi une chaîne d'approvisionnement optimisée entre les aciéries et les usines de transformation de Nucor.
Installations de générateurs
Tri State Rigging a récemment déplacé et installé plusieurs groupes électrogènes de 67 000 kg dans des cellules d'essai grâce à son système de portique de 400 tonnes. Travaillant pour TRP Laboratories à Colombus, dans l'Indiana, l'équipe de Tri-State a pu déplacer chaque groupe électrogène sur des plots isolants grâce à son système Hillman Traksporter alimenté par batterie et à des vérins hydrauliques.
RESTEZ CONNECTÉ
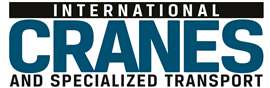
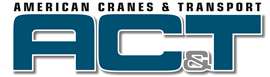
Recevez les informations dont vous avez besoin, au moment où vous en avez besoin, grâce à nos magazines, newsletters et briefings quotidiens de renommée mondiale.
CONTACTEZ L'ÉQUIPE
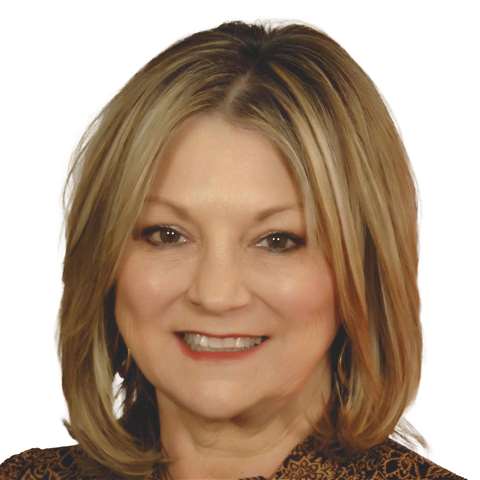
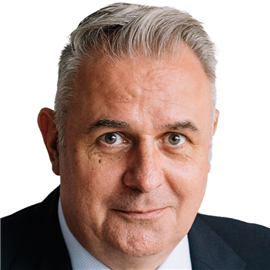
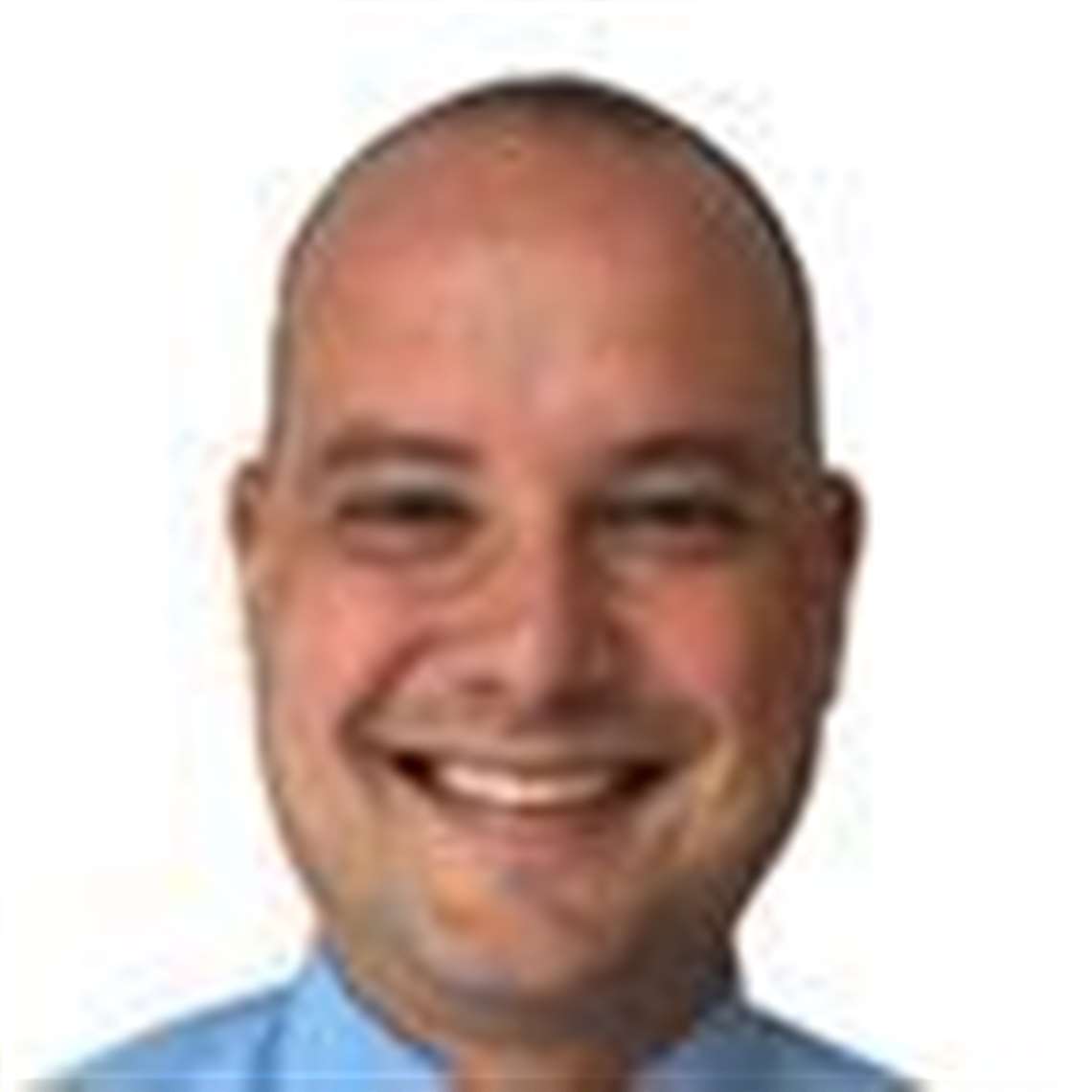
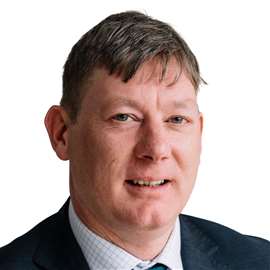