Articolo tradotto automaticamente dall'IA, leggi l'originale
Mammoet raggiunge il traguardo delle 3.000 tonnellate di carico
26 febbraio 2025
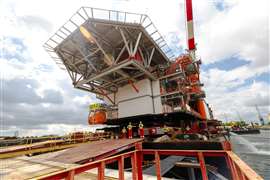
L'appaltatore HSM Offshore ha incaricato Mammoet, specialista internazionale di trasporti e sollevamenti pesanti, di effettuare il carico per un progetto epocale.
Si trattava della prima piattaforma eolica offshore per l'estrazione del gas nel Mare del Nord olandese. La piattaforma N05-A utilizza l'elettricità fornita tramite un cavo sottomarino dal vicino parco eolico offshore di Riffgat da 113,4 MW.
Si prevede che l'utilizzo dell'energia eolica ridurrà le emissioni di anidride carbonica di oltre l'85 per cento nel corso del ciclo di vita della piattaforma.
Mammoet ha affermato che il suo approccio ingegneristico ha consentito di assemblare la giacca in modo più efficiente e di ridurre i tempi di costruzione.
Il lavoro è stato svolto presso il cantiere navale di HSM Offshore a Schiedam, Rotterdam, Paesi Bassi, vicino al suo cantiere. Sono stati caricati il jacket da 3.150 tonnellate e il topside da 3.050 tonnellate da posizionare sopra di esso. Entrambi sono stati caricati su una chiatta e poi spediti via mare. ONE-Dyas, proprietaria della piattaforma, ha poi gestito la navigazione e l'installazione in mare.
Tornati al piazzale di produzione, il jacket e la piattaforma sono stati assemblati e pesati utilizzando gru mobili, rimorchi e un trasportatore modulare semovente (SPMT). Il jacket è stato fabbricato in sezioni e poi assemblato utilizzando mezzi pesanti. È stato quindi capovolto utilizzando quattro gru mobili telescopiche gommate Liebherr: due LTM 1650-8.1 da 700 tonnellate di capacità e due LTM 1450-8.1 da 450 tonnellate di capacità. L'installazione dei manicotti di sostegno del jacket è stata eseguita con una gru mobile gommata da 750 tonnellate di capacità.

Mettendolo insieme
Per l'assemblaggio finale in banchina, la sezione superiore è stata sollevata da due navi a sbalzo per carichi pesanti. Questo sollevamento ha lasciato spazio sufficiente per far passare la sezione inferiore su rimorchi, in modo da poterla unire.
Per la parte superiore, costruita all'interno, è stato installato un SPMT sotto di essa, in modo da poterla spostare all'esterno e raggiungere la banchina. Durante la sua permanenza, Mammoet ha utilizzato rimorchi e le sue gru mobili per montare una gru a piedistallo sulla sovrastruttura.
La parte superiore e il rivestimento completati sono stati caricati separatamente sull'SPMT prima di essere pesati utilizzando celle di carico Mammoet per determinarne il peso finale. Sono state disposte quattro file di 32 assi di SPMT.
Per rispettare i tempi previsti, entrambi i moduli sono stati caricati sulla stessa chiatta. Normalmente vengono spediti separatamente. In questo caso, si sono presentate sfide ingegneristiche e problemi di spazio. È stato necessario trovare spazio sulla nave per pompe e verricelli e si è resa necessaria una diversa disposizione degli ormeggi.
All'ormeggio
"L'ormeggio era piuttosto critico e abbiamo dovuto fare molta ingegneria", ha spiegato Sven Segeren, project manager di Mammoet. "Normalmente, avremmo utilizzato una configurazione di verricelli per ormeggiare e stabilizzare la nave, ma non è stato possibile a causa della forza dei carichi considerevoli.
“I carichi sugli argani erano troppo elevati e i bitte non erano sufficientemente resistenti, quindi è stata utilizzata una piccola chiatta con gambe di zampa per fissare l'imbarcazione e mantenerla in posizione prima, durante e dopo lo scarico.”
La preparazione della chiatta principale ha richiesto cinque giorni: installazione delle pompe di zavorra, pre-zavorramento e successiva verifica delle condizioni di navigazione per il viaggio.
Entrambi i moduli vennero caricati in un'operazione durata due giorni.
"Collaboriamo molto con HSM Offshore. Ci coinvolgono sempre fin dall'inizio dei progetti, così possiamo aiutarli con soluzioni intelligenti per l'assemblaggio", ha affermato Segeren.
RESTA CONNESSO
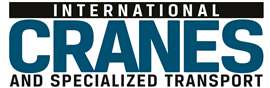
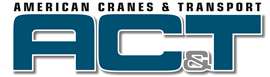
Ricevi le informazioni di cui hai bisogno, quando ne hai bisogno, tramite le nostre riviste, newsletter e briefing quotidiani leader a livello mondiale.
CONTATTA IL TEAM
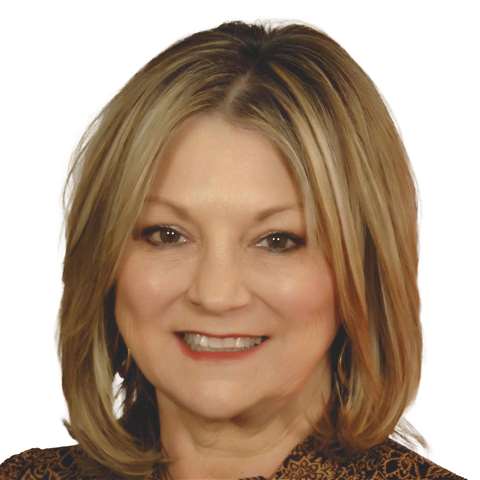
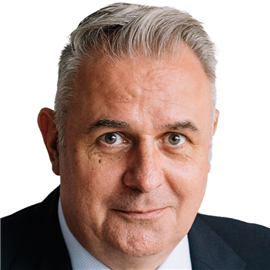
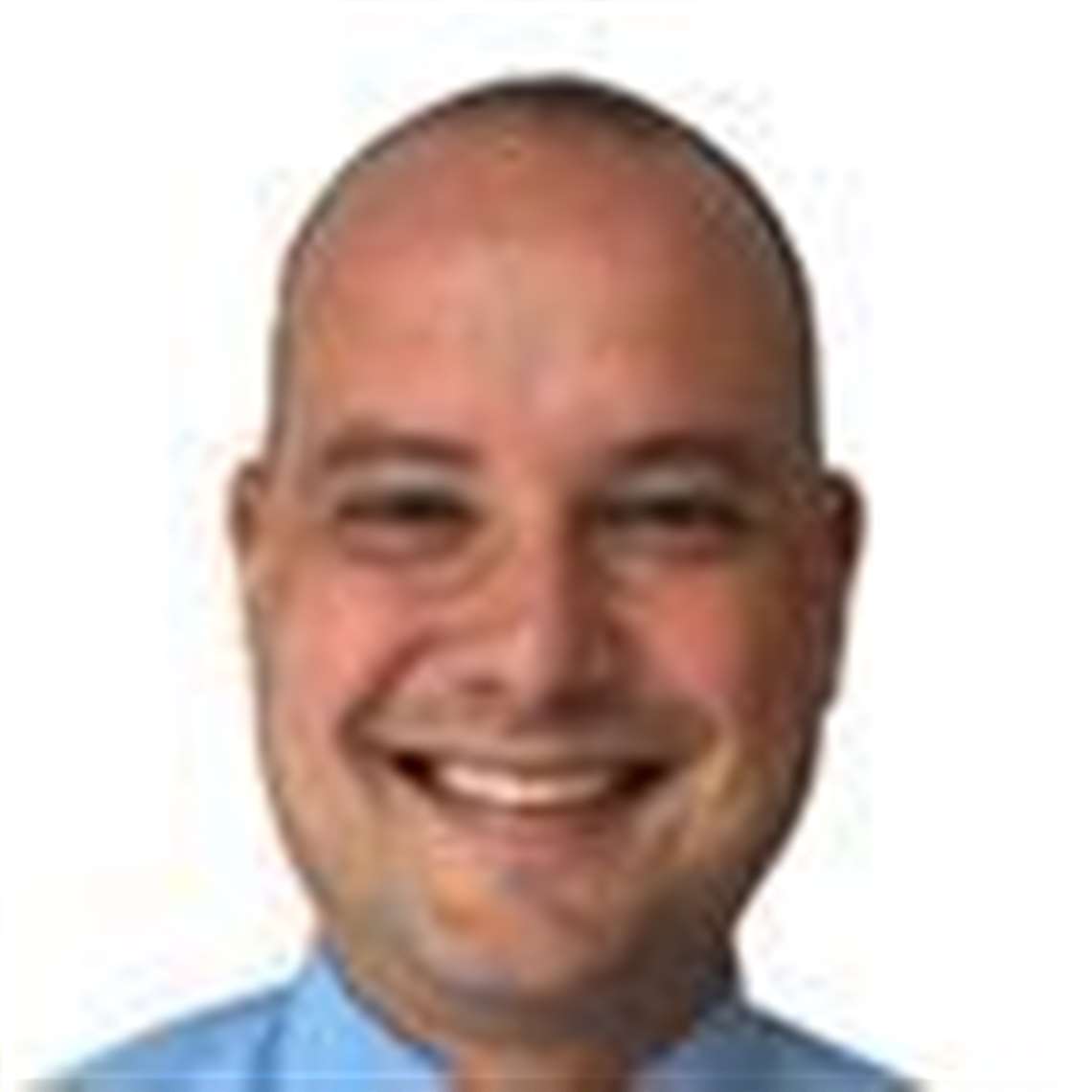
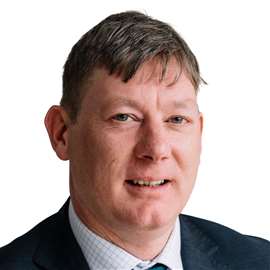