Articolo tradotto automaticamente dall'IA, leggi l'originale
Mammoet sposta un enorme frantoio per Codelco
11 marzo 2025
Nel corso di 18 mesi, il team di Mammoet ha progettato il percorso, la metodologia e il piano per portare a termine l'operazione di spostamento delle parti del frantoio da una miniera all'altra.
Le attrezzature minerarie sono enormi e pesanti e vengono continuamente spostate da un luogo all'altro. Una volta estratte le risorse, le attrezzature devono essere smobilitate e spostate in un'altra sede per riprendere il loro lavoro.
Ma spostare le attrezzature minerarie è un processo complicato, come è stato il caso di Codelco, la società mineraria di rame di proprietà statale del Cile che gestisce miniere nei pressi della città di Calama.
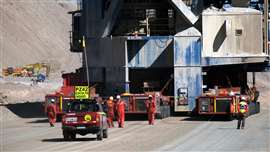
Codelco ha chiesto il supporto di Mammoet per spostare componenti chiave del frantoio da un sito all'altro, a circa 4,5 chilometri di distanza. C'erano 16 componenti da spostare, e i sei pezzi più grandi costituiscono la parte principale del sistema di frantumazione che estrae i materiali dalle miniere e li frantuma in pezzi più piccoli.
Codelco non aveva mai eseguito un'operazione di queste dimensioni prima. Si è rivolta a Mammoet per ottenere consulenza sulle migliori attrezzature per il sollevamento e il trasporto di carichi pesanti, nonché sulle soluzioni ingegneristiche necessarie per raggiungere il suo obiettivo. Gli ingegneri di Mammoet hanno proposto una serie di diversi metodi di estrazione per consentire lo spostamento dei componenti chiave come unità complete, riducendo i costi e portando il progetto a termine prima del previsto, secondo Mammoet.
Questo progetto ha segnato la prima collaborazione diretta tra Mammoet e Codelco, nonché la prima volta che questo sito ha dovuto spostare un frantoio. Il primo passo è stato pianificare il percorso, la metodologia e le attrezzature per il sollevamento e il trasporto di carichi pesanti per l'operazione, con il supporto degli ingegneri di Mammoet in ogni fase.
"Abbiamo collaborato con Codelco per un anno e mezzo alla pianificazione", ha dichiarato Vanessa Labana, responsabile vendite di Mammoet. "Abbiamo creato tutti i piani di percorso e gli schizzi e li abbiamo supportati nel rispondere a tutte le domande e le considerazioni che hanno dovuto affrontare in loco. Ad esempio, la pendenza corretta, i rapporti di sterzata e la larghezza della strada per facilitare il percorso di trasporto più rapido."
Una delle sfide più grandi è stata quella di reperire e mobilitare le attrezzature e il personale per un progetto di questa portata. Il team di Mammoet ha unito le sue risorse globali, utilizzando un trasportatore modulare semovente (SPMT) proveniente dalla Malesia, sistemi di trasporto con slitte dagli Stati Uniti e attrezzature aggiuntive provenienti dalla Colombia.
Diversi approcci
C'erano sei componenti chiave da spostare, e il metodo di rimozione e trasporto era diverso per ciascuno di essi. La maggior parte è stata sollevata utilizzando martinetti di sollevamento e poi spostata con SPMT dotati di travi di supporto. Per il sistema di azionamento, è stato utilizzato lo stesso approccio, ma con l'aggiunta di un sistema di scorrimento. Questo è stato utilizzato per far scorrere il componente per 12 metri, prima che potesse essere abbassato nella sua posizione finale. I due elementi più pesanti da trasportare e sollevare sono stati il silo (1.100 tonnellate) e il frantoio stesso (1.300 tonnellate), quest'ultimo il più complesso dei sei movimenti di carico.
"Abbiamo creato una trave di supporto appositamente adattata per questo carico", ha detto Labana. "Abbiamo dovuto apportare alcune modifiche alle nostre travi originali applicando rinforzi in piombo sulla parte superiore, in corrispondenza dei quattro punti di sollevamento, per evitare deformazioni".
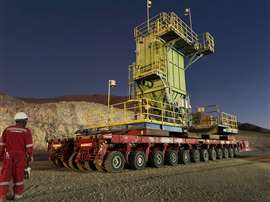
Il frantoio è stato estratto dal suo alloggiamento utilizzando cingoli e pattini, prima di essere sollevato in aria a un'altezza sufficiente a consentire il passaggio dell'SPMT. Sono state utilizzate delle cinghie per fornire ulteriore supporto e mantenere il tutto in posizione durante il percorso di 4,5 km. È stata creata un'area vicino al luogo di smobilitazione per consentire la rotazione del frantoio di 180 gradi e posizionarlo correttamente per l'installazione.
Una volta giunto al sito di installazione, il processo precedente è stato ripetuto al contrario, con i rimorchi SPMT che abbassavano il carico su cingoli per farlo scivolare nella nuova posizione. Anche l'unità della galleria rappresentava una sfida, a causa del terreno non completamente livellato, con una pendenza dell'1%. Di conseguenza, sono stati utilizzati due martinetti idraulici per sollevare carichi pesanti sulla parte posteriore a tre intervalli diversi, in modo da mantenere il tutto in piano durante lo slittamento in avanti.
L'operazione è stata completata in poco più di un mese, impiegando meno tempo del previsto, principalmente perché i componenti del frantoio sono stati rimossi come unità complete. Ciò ha permesso alla miniera di tornare rapidamente operativa. Labana ha affermato che Mammoet ha gestito il team, le attrezzature e le fasi ingegneristiche per portare a termine il progetto in modo sicuro ed efficiente, mobilitando tutto in cantiere nei tempi previsti ed evitando costosi ritardi e sanzioni. Per l'intero progetto sono stati utilizzati un team di 70 persone e un totale di 160 linee d'assi di SPMT, otto pattini di scorrimento (500 tonnellate), otto sistemi di sollevamento (400 tonnellate), oltre a travi di supporto, rotaie e ancoraggi.
"Se questo progetto fosse stato realizzato in modo convenzionale, Codelco avrebbe dovuto tagliare e smontare l'attrezzatura, il che avrebbe richiesto molto tempo", ha spiegato Labana. "È la prima volta che Codelco fa qualcosa del genere. Con noi, hanno un partner affidabile per progetti futuri, grazie alla fiducia nella nostra esperienza, nelle nostre attrezzature e nel nostro background."
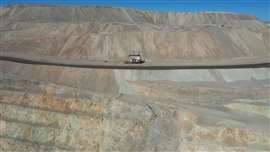
RESTA CONNESSO
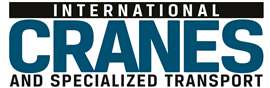
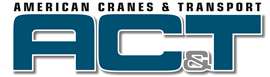
Ricevi le informazioni di cui hai bisogno, quando ne hai bisogno, tramite le nostre riviste, newsletter e briefing quotidiani leader a livello mondiale.
CONTATTA IL TEAM
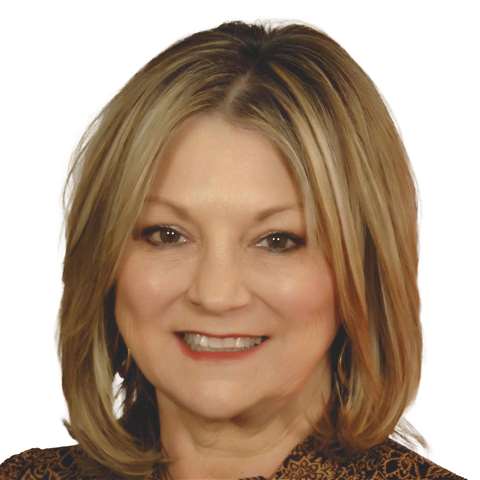
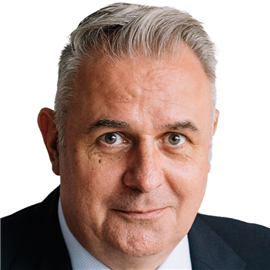
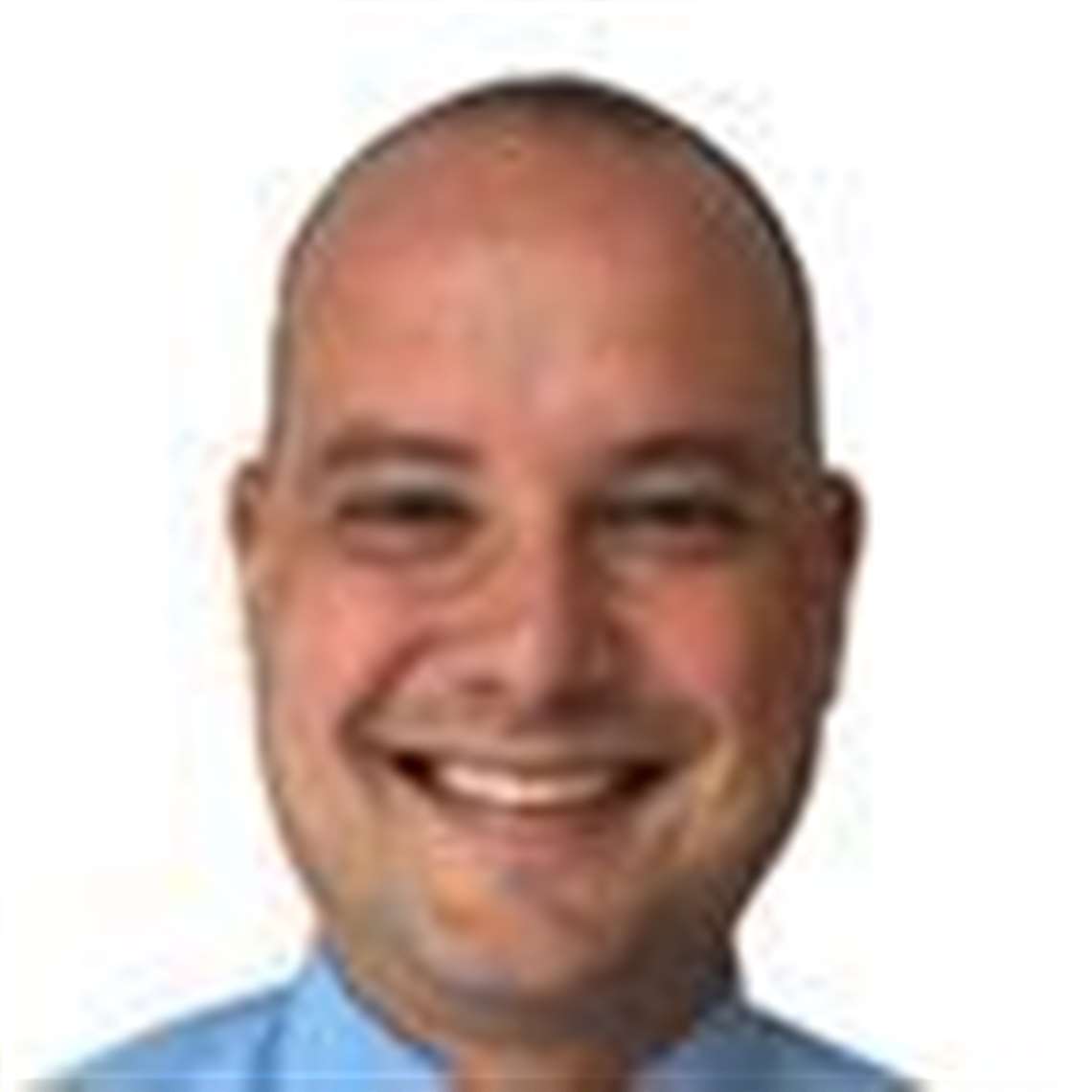
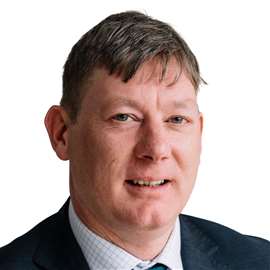