Articolo tradotto automaticamente dall'IA, leggi l'originale
Movimenti monumentali: all'interno di alcune delle complesse operazioni di trasporto e rigging del 2024
28 ottobre 2024
Edwards Moving & Rigging (EMR) ha recentemente completato un monumentale progetto di trasporto e rigging che ha richiesto competenze specialistiche aggiuntive. Per un delicato progetto di dismissione, EMR ha spostato con successo quattro componenti radioattivi di Classe 7 dalla Florida a un sito di smaltimento in Texas. Questa complessa operazione, che ha richiesto mesi di pianificazione, ha richiesto una logistica multimodale, un rigging sofisticato e un coordinamento preciso tra numerose agenzie statali e infrastrutture.
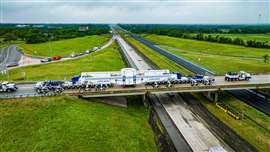
La prima fase ha previsto il trasporto dei componenti da un'area di stoccaggio in Florida a un punto di sbarco per chiatte. EMR ha utilizzato un Goldhofer PST a 3 file e 12 linee per far rotolare i quattro componenti – due unità più piccole e due più grandi – su una chiatta con ponte largo 15 metri e lungo 60 metri. Le due unità più piccole sono state fissate su supporti e travi, mentre i componenti più grandi sono stati posizionati utilizzando il sistema a bassa pressione di EMR, progettato per distribuire uniformemente il peso dei componenti. Ciò ha permesso di caricare tutte e quattro le unità su un'unica chiatta.
Una volta assicurata per i movimenti laterali, longitudinali e di sollevamento, la chiatta ha attraversato il Golfo del Messico, arrivando al terminal di Rockport ad Aransas Pass, in Texas. L'intero processo è stato poi invertito, poiché EMR ha utilizzato una tecnica RORO per scaricare il carico.
Mesi prima della partenza della chiatta, l'EMR ha avviato un'intensa attività di pianificazione del percorso con il TXDOT e gli ingegneri dei ponti di terze parti. Considerato il peso e le dimensioni del mezzo – che culminavano in un peso lordo di 1.553.344 libbre per 300 piedi di lunghezza, 21 piedi e 5 pollici di larghezza e 17 piedi e 2 pollici di altezza – era fondamentale garantire che strade e ponti potessero sostenere il carico estremamente pesante.
Il processo di pianificazione ha richiesto otto mesi e ha coinvolto 11 dei 25 distretti di trasporto del Texas. Ogni distretto presentava sfide specifiche, diverse delle quali richiedevano la chiusura di strade, la deviazione del traffico e piani di controllo del traffico. La rigorosa analisi di EMR ha garantito che il trasporto potesse procedere senza danni alle infrastrutture o disagi al pubblico.
Una volta ottenuti i permessi e definito il percorso, l'EMR ha iniziato il viaggio su strada di oltre 1450 chilometri verso il sito di smaltimento. Il convoglio ha attraversato 158 ponti, utilizzando carrelli su 150 di essi ed effettuando salti da un molo all'altro su tre ponti. Il team ha anche gestito due movimenti contromano, chiudendo temporaneamente tratti dell'autostrada e procedendo nella direzione opposta per far spazio al carico fuori misura. A un certo punto, un tratto dell'Interstatale 20 è stato chiuso per consentire il proseguimento del trasporto.
Oltre alle sfide tecniche, ostacoli logistici come la rimozione di 73 cartelli stradali e l'utilizzo di camion con cestello per superare cavi e semafori hanno reso l'operazione ancora più complessa. La scorta di polizia e civili ha garantito la sicurezza pubblica e il libero passaggio attraverso centri abitati e aree rurali.
Una delle sfide ingegneristiche più significative ha riguardato il trasporto dei componenti radioattivi più grandi utilizzando il sistema di ponti a trave alta Goldhofer Faktor 5. I componenti non disponevano dei tradizionali punti di ancoraggio, tipicamente necessari per il fissaggio del carico durante il trasporto. Il team di ingegneri di Edwards ha ideato una soluzione che utilizzava catene sintetiche per avvolgere e fissare il carico, in conformità con gli standard TXDOT.
Una volta raggiunto il sito di smaltimento, i componenti sono stati trasportati per l'ultimo miglio utilizzando un Goldhofer a 3 file e 12 linee e un sistema a portale da 900 tonnellate, che ha scaricato e posizionato i componenti a terra.
Impostazione di una stampa ONA
Taylor Crane & Rigging ha fornito supervisione, manodopera e attrezzature per lo scarico e il montaggio preliminare di una pressa ONA. Le attrezzature utilizzate per questo progetto includevano due martinetti da 690 tonnellate, bilancini, travi di sollevamento, tiranti di sollevamento e attrezzature di sollevamento, un Versa-Lift 40/60 e un carrello elevatore da 15.000 tonnellate.
Sostituzione dell'autoclave
Un'azienda manifatturiera di Arlington, Washington, ha deciso di potenziare la propria attrezzatura per il trattamento a pressione dei pali del telefono – un'autoclave lunga 46 metri e con un diametro di 2,4 metri – con un sistema più grande per aumentarne il volume di produzione. Tuttavia, l'autoclave da 72 tonnellate era situata in una fossa interrata sotto un capannone coperto con pali, con una fossa per i macchinari direttamente al di sotto.
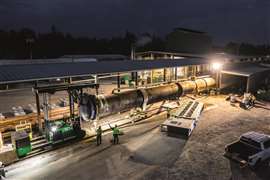
Contattando il team di Omega Morgan di Seattle addetto allo spostamento dei macchinari, l'azienda aveva bisogno di una soluzione completa per rimuovere il contenitore originale, trasportare la nuova autoclave e installarla nella sede attuale, riducendo al minimo i tempi di fermo della produzione. Le squadre di Omega Morgan si sono fatte avanti con una soluzione di livello mondiale.
Mesi prima del trasloco, la squadra incaricata dello spostamento dei macchinari ha richiesto il supporto dei team specializzati di trasporto e assistenza gru di Omega Morgan. Il loro ruolo sarebbe stato fondamentale per il prelievo e il trasporto della nuova autoclave da 100.000 kg da Sandy, Oregon.
Il team specializzato nel trasporto ha iniziato a richiedere i permessi per carichi eccezionali sia alle autorità dell'Oregon che a quelle dello Stato di Washington, il che richiede dai 45 ai 60 giorni, mentre la squadra addetta allo spostamento dei macchinari pianificava il trasloco in più fasi.
Pur mantenendo una lunghezza di 46 metri, la nuova autoclave ha aggiunto due piedi di diametro, posizionandosi nello stesso spazio del contenitore originale. Nel corso di diverse riunioni e visite in loco presso il sito di Arlington e lo stabilimento produttivo di Sandy, il team ha discusso le modifiche al design della nuova autoclave da 100 tonnellate e ha individuato le attrezzature necessarie per le operazioni di rimozione e installazione.
Dopo aver ottenuto i permessi, il team specializzato in trasporti di Omega Morgan si è concentrato sul segmento trasporti del progetto. Ha deciso di utilizzare un rimorchio modulare doppio costruito su misura da Omega Morgan, allestito per il trasporto tra Sandy e Arlington.
Il progetto è stato suddiviso in più reparti per garantire al cliente il minor tempo possibile di fermo macchina. Una volta ottenuti permessi, attrezzature e personale, il team addetto allo spostamento dei macchinari ha eseguito la prima fase del progetto.
Nel corso di tre giorni presso lo stabilimento di Arlington, la squadra di quattro persone di Omega Morgan ha utilizzato dei martinetti per sollevare l'autoclave prima di farla scivolare fuori e sopra le piattaforme che ne sostenevano la base. Ulteriori sollevamenti e puntelli l'hanno portata abbastanza in alto da superare la fossa, pur rimanendo sotto il tetto. La squadra ha quindi utilizzato il Tri-lifter per estrarla completamente. Facendo scivolare un SPMT sotto la nave, è stata allontanata dalla fossa per la dismissione.
La fase successiva del lavoro è iniziata a Sandy, Oregon. Il team di quattro persone specializzato nel trasporto ha incontrato la squadra addetta alle gru e le gru da 200 e 350 tonnellate presso l'impianto di produzione delle autoclavi. Sollevando la nuova autoclave di 3 metri di diametro dai suoi blocchi, il team addetto all'assistenza gru ha posizionato il componente tra i due rimorchi modulari costruiti su misura, collegandoli. Dopo aver fissato l'autoclave, il team si è messo in viaggio. Nonostante le chiusure stradali, il controllo del traffico e la scorta dei piloti, il carico largo 5,5 metri ha completato il viaggio in tre giorni.
Tornati ad Arlington, la squadra di installazione ha sollevato l'autoclave utilizzando i sollevatori Tri-Lifter prima di posizionarla su una rotaia scorrevole e spingere il componente verso la fossa. L'installazione ha richiesto sei giorni, durante i quali la squadra ha sollevato e fatto scorrere il contenitore in posizione.
Sostituzione del ponte ferroviario
A luglio, nel Vermont, la Buckingham Heavy Transport ha sollevato e trasportato un ponte ferroviario a campata unica di 38 metri per 7,7 metri, con 15 cm di spessore, dalla sua area di stazionamento alle spalle definitive. Il ponte è stato costruito in un lotto adiacente, a circa 60 metri dalle spalle.
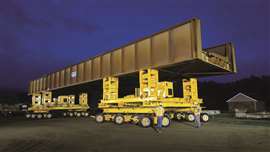
Il team di Buckingham ha sollevato il ponte da 555.000 libbre a un'altezza di 16 piedi utilizzando puntelli e martinetti, e poi ha assemblato carrelli trasportatori personalizzati composti da carrelli elettrici e carrelli da carico Buckingham, tre livelli di travi in acciaio e supporti da 150 tonnellate sottostanti.
Successivamente, un sistema di scorrimento Buckingham è stato integrato tra le travi per consentire la regolazione laterale. I sistemi di ponti sono stati quindi guidati attraverso il lotto e posizionati.
La flotta di attrezzature personalizzate di Buckingham ha permesso al team di completare il posizionamento del ponte entro i tempi ristretti del cliente. La capacità di sterzatura a granchio dei carrelli trasportatori di Buckingham ha permesso al team di guidare la sezione del ponte in diagonale dall'area di allestimento e di allinearla alle spalle senza manovre dispendiose in termini di tempo.
I sistemi integrati di scorrimento e sollevamento hanno consentito al team di regolare con precisione e rapidità il posizionamento del ponte in loco.
L'elenco delle attrezzature necessarie era lungo e comprendeva i carrelli Buckingham Power and Coaster, i martinetti Buckingham Crib da 30 tonnellate, le macchine di sollevamento unificate a 12 porte Buckingham, le unità di potenza Buckingham e il sistema di scorrimento Buckingham.
Movimentazione delle bobine
Presso Nucor Steel Gallatin a Ghent, Kentucky, l'efficienza nella movimentazione dei materiali è fondamentale per il mantenimento di processi produttivi fluidi. Per soddisfare questa esigenza, Nucor si affida alla gru a portale gommata da 70 tonnellate di Mi-Jack Products, dotata di un attacco personalizzato per la movimentazione di coil e di un gancio rotante idraulico, specificamente progettato per applicazioni di sollevamento specializzate.
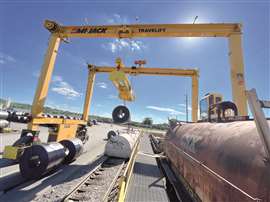
La gru a portale gommato (RTG) Travelift MJ70HD è dotata dell'accessorio specializzato per la movimentazione delle bobine Mi-Jack, che presenta un gancio rotante azionato idraulicamente progettato per
sollevare e ruotare con precisione pesanti bobine di acciaio mentre i vagoni ferroviari si muovono sotto.
Il progetto consente il carico e lo scarico senza interruzioni delle bobine nei vagoni ferroviari presso lo stabilimento di Gallatin, dove ogni anno vengono prodotte oltre 3 milioni di tonnellate di bobine a nastro caldo.
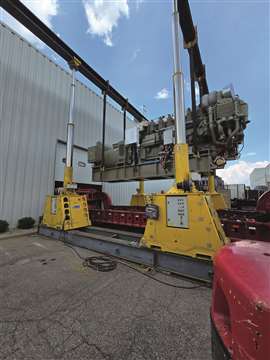
“La combinazione del Mi-Jack Travelift, della barra divaricatrice rotante e del gancio a C migliora sia la produttività che la sicurezza eliminando la necessità di attrezzature a terra e mantenendo il personale a una distanza di sicurezza durante il sollevamento delle bobine
o calati nei vagoni ferroviari", ha affermato Mike Lanigan, vicepresidente delle vendite di Mi-Jack.
Presso Nucor Steel Gallatin, il Mi-Jack Travelift riduce drasticamente i tempi di movimentazione delle bobine. Il design personalizzato della gru le consente di operare sopra i vagoni ferroviari in movimento, grazie alle specifiche di larghezza e altezza personalizzate. La sua capacità di 70 tonnellate, abbinata al gancio rotante e al gancio a C, consente agli operatori di caricare quattro bobine di acciaio per vagone ferroviario in meno di 30 minuti, che vengono poi spedite alla destinazione successiva, garantendo una catena di approvvigionamento semplificata tra le acciaierie Nucor e gli impianti di lavorazione.
Installazioni di generatori
Tri State Rigging ha recentemente spostato e installato diversi gruppi elettrogeni da 147.000 libbre (circa 67.000 kg) all'interno di celle di prova utilizzando il suo sistema a portale da 400 tonnellate. Lavorando per TRP Laboratories a Columbus, Indiana, il team di Tri-State è riuscito a spostare ciascun gruppo elettrogeno su piazzole di isolamento utilizzando il suo sistema Hillman Traksporter alimentato a batteria e martinetti idraulici.
RESTA CONNESSO
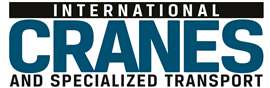
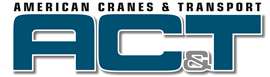
Ricevi le informazioni di cui hai bisogno, quando ne hai bisogno, tramite le nostre riviste, newsletter e briefing quotidiani leader a livello mondiale.
CONTATTA IL TEAM
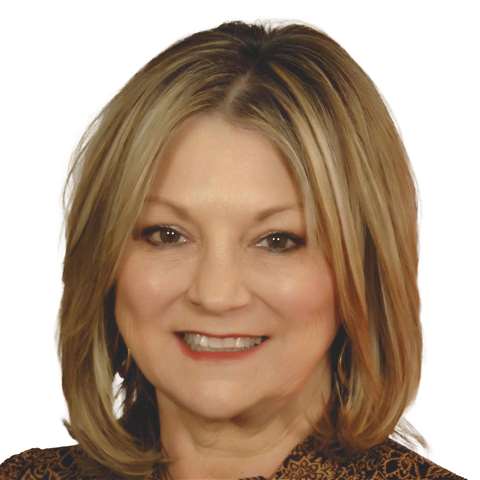
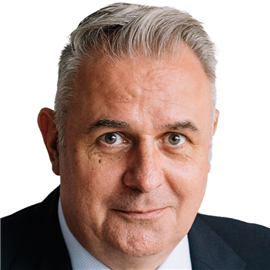
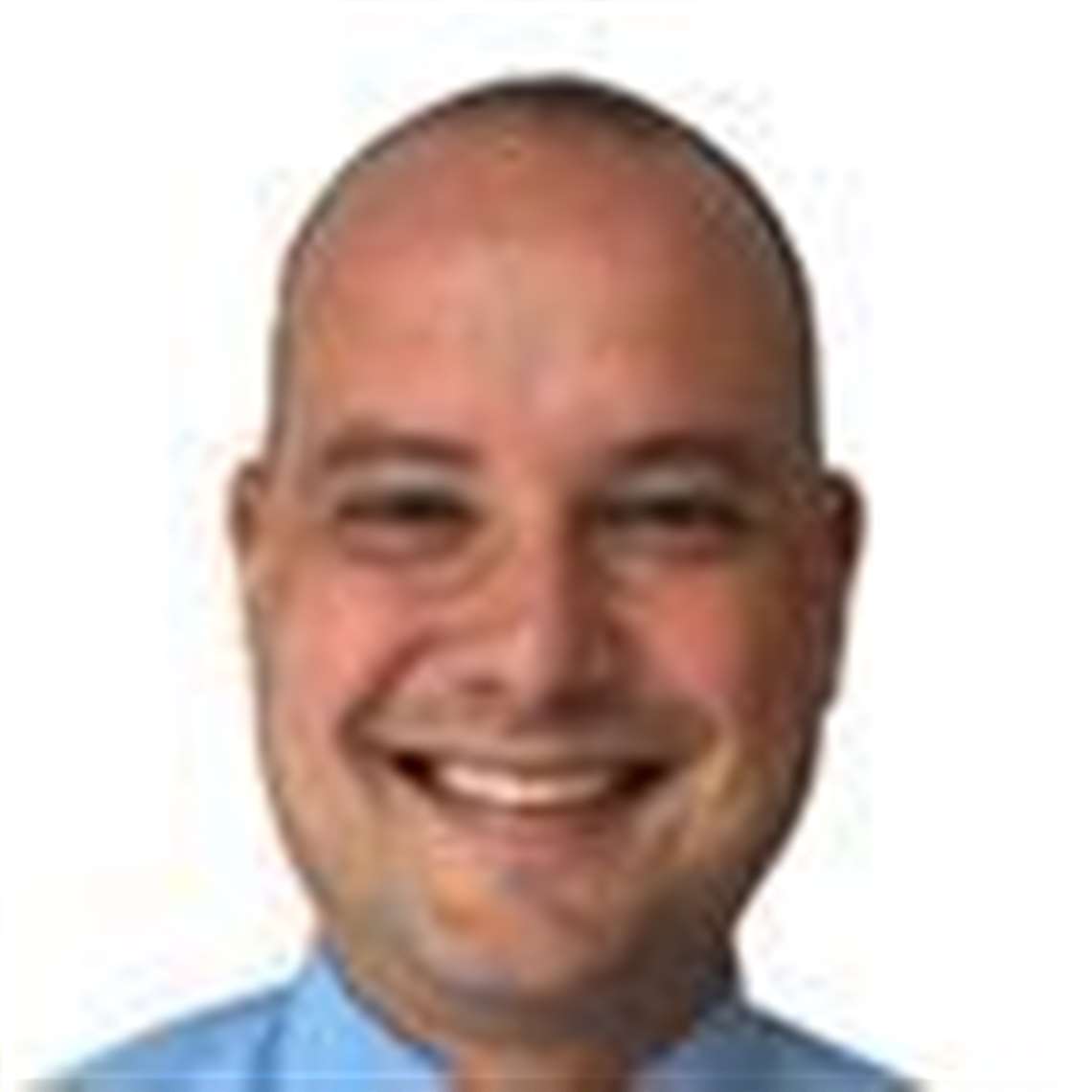
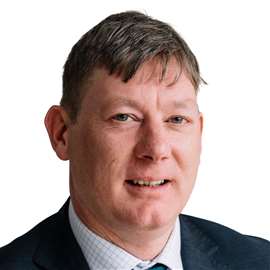