‘Roadability’ is the word in the expanding US all-terrian crane sector
05 April 2010
While popular in Europe for decades now, the all-terrain crane is just gaining traction in the North American market. Lindsey Anderson talks with manufacturers about why the market is expanding and what new technologies will propel it even more.
All terrain cranes might have been the brainchild of European manufacturers and might still today have a major manufacturing hold in Europe (Germany, specifically), but they've crept into the North American market and continue to expand as design needs are met.
"In the past, all-terrain cranes were primarily designed to meet European road regulations which limit axle loads to 26,500 pounds per axle in most countries," says Andreas Cremer, all-terrain crane product manager for Manitowoc Cranes. "In addition to this weight restriction, compact size is also a requirement for cranes designed for use throughout Europe."
Georg Diesch, president of Liebherr Cranes, Inc., says his company's manufacturing facility in Ehingen, Germany started building AT cranes in the mid 1970s but estimates the company didn't sell any into the US market until the mid or late 1980s.
"If you look on the current statistics about AT cranes, you will see that for instance, in Western Europe for 2009 [there were] 1,522 new units that have been reported but only 292 units (10 percent) for North America as the second largest market," Diesch says. "Africa has a similar quantity on new cranes reported [with 248]."
Diesch says he believes that the US is historically a traditional market for truck cranes, rough terrain cranes and crawler cranes, which could explain why the market hasn't been penetrated by all terrain cranes.
"In addition, the AT cranes are more expensive and therefore, if a truck crane or RT crane can do the job you can't always ask for more rent for the same job," Diesch says. "Moreover, TC and RT cranes are less sophisticated and therefore need less-educated operators. Plus, a TC has a higher speed capacity and less fuel consumption [for long distances.]"
But the all-terrain crane market is continually gaining momentum in the US as manufacturers become more sensitive to customer and design needs, Cremer with Manitowoc says.
US focus
"Part of the success of the all-terrain crane concept in the US can be attributed to the cranes' ability to combine the off-road advantages of rough terrain cranes - pick-and-carry capabilities, movement over rough terrain on a jobsite, all-wheel steer - and the transport advantages of truck-mounted cranes - highway travel speeds, no trailer necessary," Cremer says. "In addition, the capacity range of all-terrain cranes separates them from other mobile telescopic products."
Diesch with Liebherr says an AT crane's light weight for road permissions also goes hand-in-hand with axle distances on the crane.
"Road ability and transportation have become more and more a concern for the users," Diesch says. "If you get the crane legal without stripping off too much of the attachments, and [utilize] less trucks to move stuff, the less time and cost you have to spend. This goes so far that even the design of the counter weight slab counts more and more."
North American transport requirements have a higher priority in the specification of new models as axle loads in the US usually have to weigh below 26,500 pounds per axle, Cremer says. To reach these requirements, options such as removable outrigger boxes, axle spacings which meet US bridge formulas, dollies or boom removal systems improve the transportability of AT cranes, which makes them a more profitable choice for contractors and crane owners when choosing what type of crane to use.
Also, whereas the US market below 110-ton and 130-ton capacity is somewhat dominated by RT and truck-mounted cranes, Cremer says, AT cranes are used in capacities above the 130-ton range with capacities that reach 1,200 tons.
"In these capacity ranges, all-terrain cranes are competing with crawler cranes, which have completely different transport logistics to move them between jobsites," Cremer says.
Design trends
New technologies are also influencing the North American market's use and purchasing of AT cranes. New factors such as high-strength steel and boom pinning technology have allowed manufacturers to save weight within the limits stated by regulations and turn that weight into higher capacity and longer booms.
For example, in the 1990s, 200-ton capacity cranes required a carrier with seven axles, Cremer says. Today, those cranes can be transported with typically five-axle machines. "Roadability and cost of ownership are influencing our design more and more these days, but also increasing safety requirements," Cremer says.
"Also driving by globalization, today we have almost twice as many models in our all-terrain crane product range than 10 years ago," Cremer says citing the company's eight models in 1999 versus its present day 15 model count.
"Looking forward, new materials that allow us to gain even more capacity and boom length by reducing weight will be a factor, but transportation and reducing cost of ownership will remain top priorities," Cremer says.
Popular ATs
Liebherr's most popular all-terrain units are the five axle cranes between 100 and 250 tons, Diesch says. These units offer customers a wide range of job possibilities as well as the needed roadability. "They can do a simple AC unit exchange on top of a high rise building, supporting larger cranes or just almost any lifting job," Diesch says.
But the company's most-selling crane is the Liebherr LTM 1250-6.1; a 300-ton crane with six axles and right behind it is the LTM 1400-7.1; a 500-ton capacity unit.
"Albeit the 600-ton crane LTM 1500-8.1 (eight axles) is about to replace the 500-ton crane," Diesch says. "This is because the 600-ton crane can erect wind turbines due to the capacity and reach height but is still easily movable."
Cremer says Manitowoc's popular models are the GMK5135/GMK5165-2 because both five-axle cranes are easy to transport due to a variety of counterweight configurations which allow each to adapt to different road regulations. "Both models are building on the success of the very popular GMK5120B, which had been in production until 2008," he says.
Manitowoc's other popular units include the GMK5275, which Cremer says is the market's strongest offering in the five-axle category because it offers a 223-foot boom while remaining "relatively easy to transport."
"In most states, owners are not even required to remove the boom, also due to an optimized axle spacing," Cremer says. "This model is a great successor to the GMK5210 and GMK5240 models in a historically very strong segment for the Grove brand."
As AT cranes continue to gain popularity on North American soil, look out for the machines to be used for a ride range of lifts, Birgit Kettermann with Terex Cranes says. "Wind power plant erection is a still-growing market, which makes for popularity of larger ATs," Kettermann says. (See box story.)
Diesch says AT cranes are not limited to any specific job, either, and that the main reason to have an AT crane in a fleet is that it combines safety and roadability, giving it ultimate flexibility for any job.
STAY CONNECTED
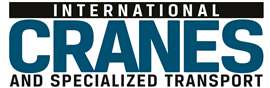
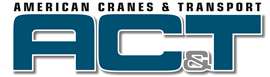
Receive the information you need when you need it through our world-leading magazines, newsletters and daily briefings.
CONNECT WITH THE TEAM
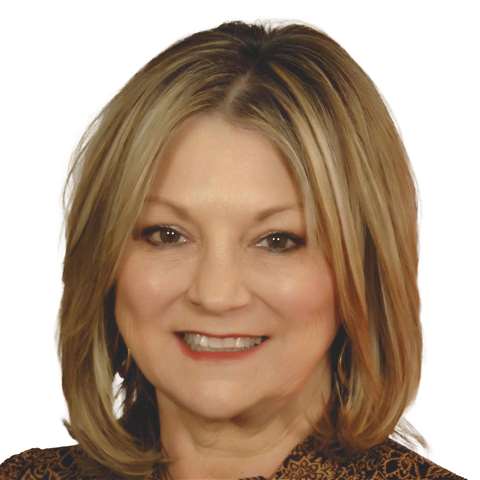
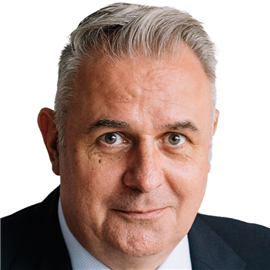
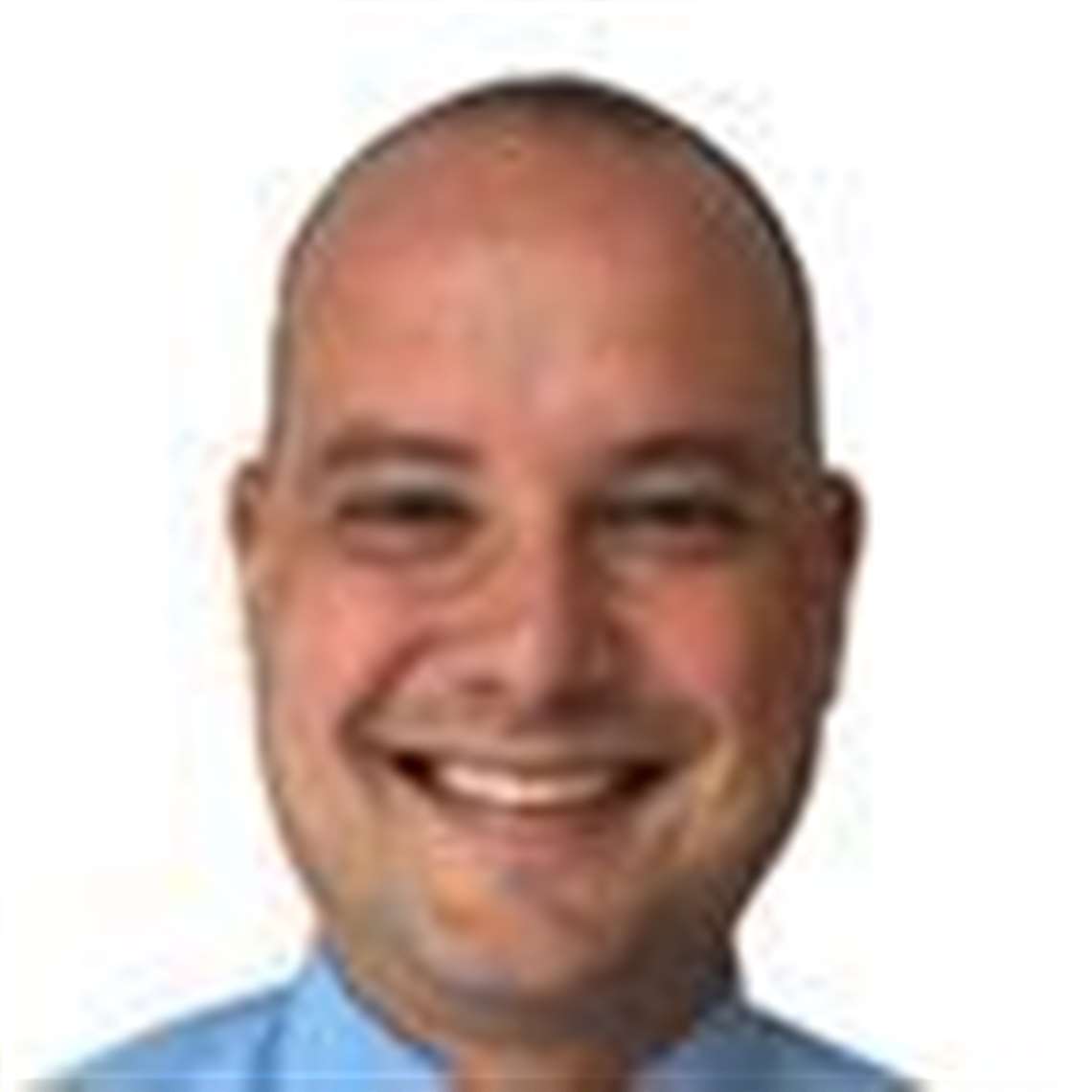
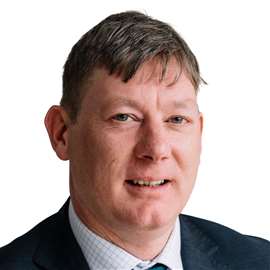