ACT rounds up specialized rigging projects
01 August 2018
In the realm of specialized rigging, everyone seems to be interested in what everyone else is doing. That’s why American Cranes & Transport’s Project Focus articles are so popular. These job roundups allow companies that provide lifting, rigging and specialized transportation to showcase some of their most intricate and compelling projects.
This month our focus is on specialized rigging. With these types of projects, new equipment is often created to meet a specific need, or everyday equipment is altered or used in conjunction with other equipment. The creativity and ingenuity required for these projects is a lesson in thinking outside the box.
Dryer installation
A 55-foot gap in the transport path provided Burkhalter an opportunity for engineering innovation in order to set a 380,000-pound Yankee dryer.
The Burkhalter team mobilized in-house equipment and support personnel to offload, transport, translate and set the Yankee dryer onto bearings at its final location. Burkhalter crews utilized a combination of tools to accomplish the challenging feat. Burkhalter used 56-foot barge ramps to create a navigable pathway for a SPMT to move the dryer onto a 70-foot jumper bridge and traverse over to the elevated concrete machine foundation. Steel mats that were 30 feet in length were used to cantilever a few feet beyond the width of the concrete machine foundation to allow room for the last axle of the SPMT.
Further challenged by the structural weakness of the path of the gantry track, Burkhalter used additional 30-foot steel mats to span the loadings of the gantry track to a strong area above the columns. This allowed Burkhalter crews to seamlessly transport the dryer to an awaiting 500-ton J&R Engineering
Lift-N-Lock hydraulic gantry system and translate over to the final location and set onto the bearings. Burkhalter utilized existing specialized rigging and transport equipment to overcome challenges, increase safety and ultimately reduce the client’s work schedule by three days.
Stator refurbish
A power station in Virginia contracted with W. O. Grubb to remove a 70-ton generator stator that needed refurbishing. W.O. Grubb’s team devised an innovative and economical solution that minimized impact on the facility.
The first idea was to take the stator out through the roof, but this option would have required cutting a roof opening that would need to be temporarily sealed while the stator was being refurbished and the use of a large-scale crane to lift it out.
Outside the building, Grubb’s 300-ton capacity Liebherr LTM 1250-6.1 lifted the stator off the runway and set it directly on a trailer.
W.O. Grubb’s solution was to erect a temporary elevated runway and jack-and-slide the stator through the side of the building, where a significantly smaller crane could be used to lift it onto the transport trailer.
“Our ability to complete the job while leaving the roof intact enabled us to be awarded the job over our competition,” said Keith Rind, Grubb’s vice president of major projects.
The stator had to be jacked up and spun in place to align it with the skewed jack and slide path. The path was carefully chosen and laid out for the stator to narrowly fit between the building columns. The runway consisted of one of Grubb’s 6-foot 5 inch by 60-foot-long barge ramps, with its jack and slide system mounted on top.
Once the stator was properly oriented, the barge ramp was set with a two-crane lift using a mobile crane outside the building and the facility’s overhead crane inside the building. The inside end of the runway was fed underneath the jacked-up stator and set on the elevated stator foundation. The outside end of the 58-foot runway span was supported 20 feet above grade on pipe stands and mats. With the runway in place, the stator was jacked onto the slide system and then slid through the wall opening.
Once the stator was outside the building, Grubb’s 300-ton capacity Liebherr LTM 1250-6.1 was waiting to lift it off the runway and set it directly on an over-the-road trailer.The clearances were very tight with the building columns. Grubb also had to contend with proximity to power lines that were energized while the adjacent generator remained in operation. After the stator’s refurbishment was complete, the process was reversed to reinstall the stator and get the unit back up and running.
Precast lifter
Mi-Jack’s Travelift RTG and autospreader are playing a key role in handling precast guideway segments on the new Honolulu Authority for Rapid Transportation’s (HART) 5.2-mile Airport Guideway and Stations project. The joint venture design and construction team established a precast yard for production of the precast box girder superstructure sections and called on Mi-Jack to supply the gantry crane, an MJ85 HD, and to design and build a specialized autospreader to handle the unique and varied guideway bridge segments.
“Mi-Jack’s engineers were tasked to develop a new autospreader (lifting beam) to lift the precast concrete bridge sections,” said Mike Lanigan, Jr., sales manager for Mi-Jack. “At first this task seemed straight forward but turned into a very complex job.”
The bridge sections are part of a series of new elevated guideways for the Hawaiian mass transit system. The project consists of thousands of interconnected bridge sections. The autospreader had to be designed to lift each bridge section that could vary in size, weight and physical dimensions. Some sections could be as large as 30 feet long and weigh as much as 70 tons.
“What made this job complex is how the bridge sections had to be lifted and the different shapes of the bridge sections,” Lanigan said.
Mi-Jack’s solution was the development of a triple beam autospreader that can eliminate manual operations and securely handle each of the precast box girder superstructure section’s unique characteristics: predetermined lifting points; different lengths, widths and weights; and lifting points that are not level and not always of the same geometry. In some cases, the edges can be beveled or square or both. The lifting positions are not always on the same plane, and just to add interest to the lift, some segments’ dimensions are designed not to be square.
The Mi-Jack Travelift RTG and custom autospreader lifts bridge sections at the Honolulu Authority for Rapid Transportation’s 5.2-mile Airport Guideway and Stations project.
“We are quite proud to have provided such a complete solution to expedite the handling of such a large project,” said Lanigan. “By the time this project is complete we will have helped to save thousands of hours in material handling.”
Bay Ltd. uprights refinery column
Bay Ltd. used a Manitowoc 21000 with a wheeled Maxer to lift a 626-ton CDHDS column at a refinery in Corpus Christi, TX. Due to a limited amount of space, Bay’s team utilized its Transporter Mounted Tailing System (TMTS), known as “Dino,” to erect the vessel. For lifting the column, Bay engineered, fabricated and tested a custom modular spreader bar system as the primary spreader bar, according to Ruben Calderon, project manager.
“We purchased Holloway’s Hammerhead Plasma 12-strand slings for the top and lower rigging of the primary spreader bar in order to allow for maximizing capacity with a lower weight for rigging than conventional wire rope slings,” Calderon explained.
Press replacement
Movement of large and oversized objects are a challenge that can be overcome with strategic planning and specialized rigging equipment. Many times, accessibility is limited, space is tight and traditional lifting equipment, such as a crane, just won’t work.
M-L Holdings Crane Group company Chellino Crane, and its Alternative Movement Division (AMD), recently helped a customer in Illinois with such a challenge. The customer had a 200,000-pound press that needed to be replaced quickly and efficiently to minimize downtime.
Chellino Crane and AMD used its 500-ton slide system to carefully slide the huge press 100 feet out of the building. Using a 450-ton capacity Grove GMK 6400, the press was then loaded onto a modular transport trailer and taken off site. In reverse order, the new press was then slid back into position and installed, allowing the customer to resume production. With a fleet of SPMTs, gantries, slide systems and custom-engineered products, AMD is providing alternative movement solutions for all M-L HoldingsCrane Group customers.
Servo Press installation
Indianapolis, IN-based Cardinal Contracting recently installed a 2,200-ton Servo Press for a manufacturing facility. Diamond Heavy Haul of Shandon, OH handled the transportation of the press, while Cardinal Contracting unloaded, installed and aligned the bed, slide and crown.
Cardinal used a bevy of equipment including a Scheuerle SPMT Light, a 500-ton capacity Lift Systems 34PT500LT Power Tower gantry, a 400-ton capacity Lift Systems 34PT5400LS Power Tower gantry, a 75-ton Lift Systems Mobilift crane and a Versa-Lift 40/60 heavy duty rigger truck. The bed weighed 330,000 pounds, the slide weighed 286,000 pounds and the crown weighed 370,000 pounds.
Pre-cast infrastructure asset
Shuttlelift recently delivered two 180,000-pound capacity Shuttlelift DB 90 rubber-tired mobile gantry cranes to Oldcastle Precast, a premier provider of engineered building product solutions for infrastructure projects. Each DB 90 features custom spreader assemblies, allowing them to lift a wider variety of construction components and to handle future needs in the transportation market. Based in Perris, CA, Oldcastle Precast specializes in precast/prestressed bridge girders.
“The investment in the two Shuttlelift DB90 gantry cranes allows us to lift a wider variety of product and has given us the versatility needed to become more efficient in our staging and loading area,” said Scott Hicks, Oldcastle site manager. “The added capacity, along with the quality and reliability of the Shuttlelift cranes, is something we didn’t have with our older off-brand gantries.”
These Shuttlelift rubber-tired gantry cranes are equipped with additional features and options. The cab is mounted on the lower side beam opposite the engine compartment with a custom stair system to make entering and exiting the cab easier. Low mounted hoists, linkage-less steering, and the remote diagnostic feature all minimize maintenance costs while maximizing production time.
“We were seeing increased demand for a gantry crane with 90-ton capacity,” said Brock Rubens, director of industrial sales at Shuttlelift. “Instead of just offering our 110-ton capacity machine we wanted to design the DB90 in order to offer our customers a solution at a value that was more in line with the capacity they actually need.”
With a maintenance-friendly design, reliable engineering and service support, the Shuttlelift gantry cranes will aid in the continued success of Oldcastle for years to come, the company said. Shuttlelift engineers worked with Oldcastle to design custom spreader assemblies to maximize versatility and the cranes’ ability to work independently or in tandem, ensuring that the DB90 mobile gantry cranes can assist in current and future projects.
Dryer switch-out
Irving Equipment used a 350-ton capacity LP350 Hydra-Slide low profile hydraulic skidding system to change-out a 55-ton Yankee dryer at Irving Tissue in New Brunswick, Canada. Both the old and new dryers were 12 feet 5 inches in diameter and 13 foot 4-inch long cylinders. They had 4-foot-long shafts sticking out of either end.
The scope of work presented four standout challenges: travel route, second floor location of the dryer, floor strength and tight confines for blocking up the loads, according to Ryan Long, Irving Equipment operations manager.
In addition to the LP350, Irving employed an Enerpac EVO power pack system and four 50-ton capacity jacks for vertical jacking of the dryer and a pair of 8-ton capacity Broderson carry deck cranes for material handling. A 250-ton capacity Liebherr LTM1200 all-terrain crane was used to hoist the Yankee dryer off the second-floor temporary mezzanine that the dryer was slid out onto. Since the dryer was a primary component of an in-line paper machine, it was deeply embedded within the plant. The project team would need to make three directional changes and three elevation changes to avoid existing infrastructure.
“As the dryer was on the second floor of the plant, in order to get it to ground level a temporary mezzanine was designed and installed outside of the plant at the same elevation as the sliding system, and the back wall of the plant was removed,” Long said. “This allowed us to slide the dryer completely outside of the building and onto the mezzanine before lifting it off with our Liebherr LTM1200.”
Early on it was determined that the concrete floor of the building could not support the heavy dryer system. To mitigate this, a steel grillage system was engineered and installed to bridge the floor between supporting columns under the floor for the entire route. Since the dryer removal was part of a larger overall shutdown, the grillage system had to be installed in a sequence that didn’t impede that scope of work.
The underside of the installed dryer was approximately five feet off of the floor, which meant a lot of blocking was needed when lowering it down to the floor. To overcome this, Irving’s Mike Neill hatched the idea for a ratcheting jack-post design that eliminated the need for blocking. The dryer’s three directional changes were at 31 feet, 38 feet and 135 feet increments, with the challenging elevation changes along the way. The slides took place across two 12-hour shifts. Outside, the Liebherr LTM1200 lifted the dryer using a Modulift spreader beam beneath the hook and slings basketed around the dryer shafts. The paper machine was shut down while the dryer was being replaced.
Edwards Moving & Rigging received two 640,000-pound combustion turbines, offloaded them from a rail car and placed them onto a deck barge using a barge crane. They were barged to a port in the Great Lakes region. Using a 12-line Goldhofer SPMT, Edwards offloaded (RORO) the first turbine and transported it to a waiting 16-axle HD railcar. Edwards’ 700-ton capacity J&R Engineering gantry system and four 175-ton Power Links were used to offload the turbine from the transporter to the rail car. The second turbine went to storage to load at a later date.
STAY CONNECTED
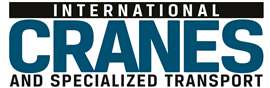
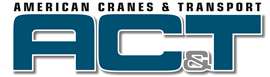
Receive the information you need when you need it through our world-leading magazines, newsletters and daily briefings.
CONNECT WITH THE TEAM
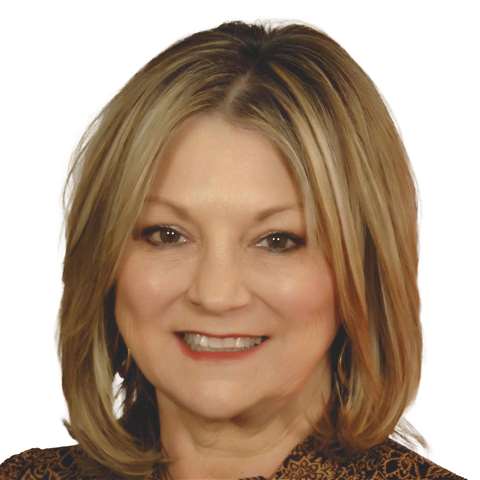
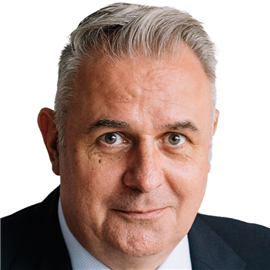
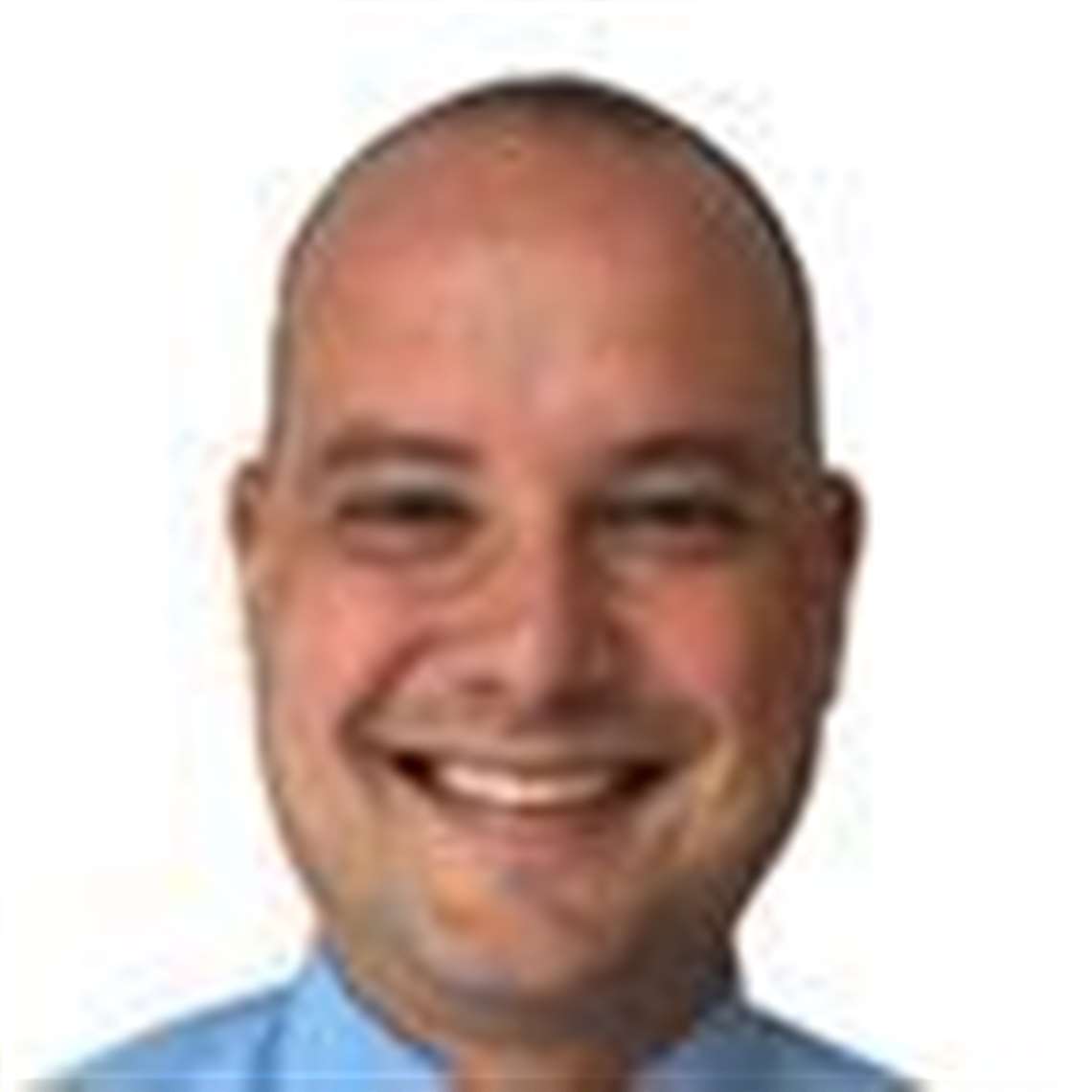
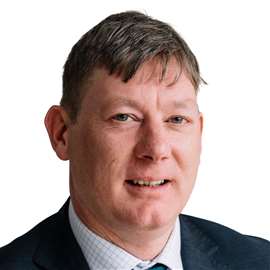