Air moves weighty industrial load
25 March 2008
A coal-fired plant branch feeds water into its boilers from a nearby lake to create the steam for turbines that drive the plant's generators. Feedwater heaters, large, heavy tanks that house heat exchangers, are used to pre-heat water for boilers and to recapture water from steamdriven turbines.
On the downside, these behemoth metal feedwater tanks are subject to corrosion and the stresses of continual heating and cooling. They don't last forever and getting them in or out for maintenance or replacement can take days.
On a recent feedwater tank move, the system engineer and his colleagues specified that air casters be used because of the plant's structural configuration. AeroGo's air caster equipment allows users to literally float heavy loads on an almost friction-free film of air. Unlike rollers or wheeled equipment, they're omni-directional and take remarkably little effort to move and maneuver – a valuable feature in tight spaces.
“We used the AeroGo air casters to drift the vessel into the mezzanine floor,” says Gary Barfield, Georgia Power's systems engineer. “We had columns, other pieces of equipment and valves in the way. It's like threading through the eye of a needle. The new heat exchanger had to be set back in the exact place we pulled the other one out of. We had a 30 foot long vessel, 6 feet in diameter, and weighing 60,000 pounds.
We needed to get it set within about a 1/4 inch of where the other one was set. Once we got it in there, the air casters made it easy to move the vessel around.”
This branch has used the AeroGo air caster system during three previous feedwater tank moves. The latest project limited options due, in part, by factors inherent in the power plant structure itself. “The issue is that the ceiling height between the floors may be only about 14 feet, whereas the height of the boilers and feedwater heaters themselves might be 12 feet.
It's just impossible to crane it out of there. If you slide it or roll it on rollers, you can run the risk of damaging the floor, tearing the plant up, or actually having one fall through the floor. AeroGo air casters solve the floor loading issue. The load is spread out over a huge area – it's virtually the same as you'd put on the floor by walking across it.”
The other advantage was the maneuverability “accurate to a 1/4 inch” that made placement possible. AeroGo equipment can traverse corners and make U-turns, or spin a load around and back it out or in. “There are no limits on its maneuverability,” Barfield says. “With wheels you're limited in what you can do when snaking something out of a really tight area. It's like trying to back a boat into a narrow garage. If you could just slide that boat side to side or rotate it and move it wherever it had to go, you'd easily fit it right in.”
Heavy loads can be moved by one person. The team required to move one of the feedwater heaters was a crew of six.
The air caster system can eliminate or sharply reduce the need, potential liability and cost of other heavier equipment such as large cranes that require an operator. Stressing the importance of minimizing plant downtime, Barfield says that the AeroGo equipment did the job in only half a day instead of a day or more, plus avoided several times higher manpower costs that would have been incurred by employing other techniques. “We are regulated,” the system engineer says, “but we're still competitive. We still have to keep our costs down if we want to keep customers.”
Reinforcing another point that's important in today's liability and safety conscious industrial environment. “It's a safer way to do it too,” says Barfield. “With rollers that thing could fall off – one tank we moved at the other plant weighed 200,000 pounds.”
STAY CONNECTED
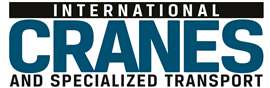
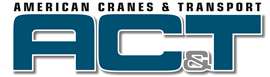
Receive the information you need when you need it through our world-leading magazines, newsletters and daily briefings.
CONNECT WITH THE TEAM
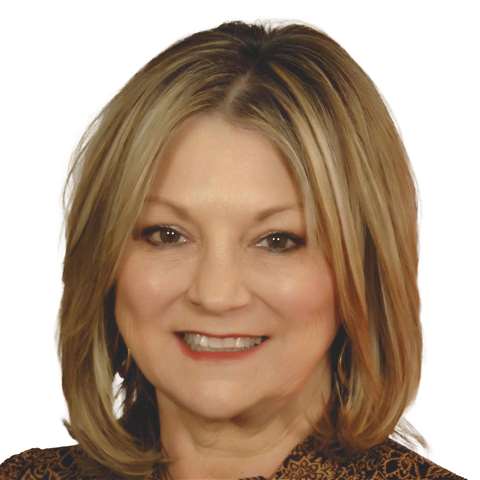
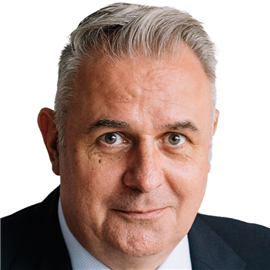
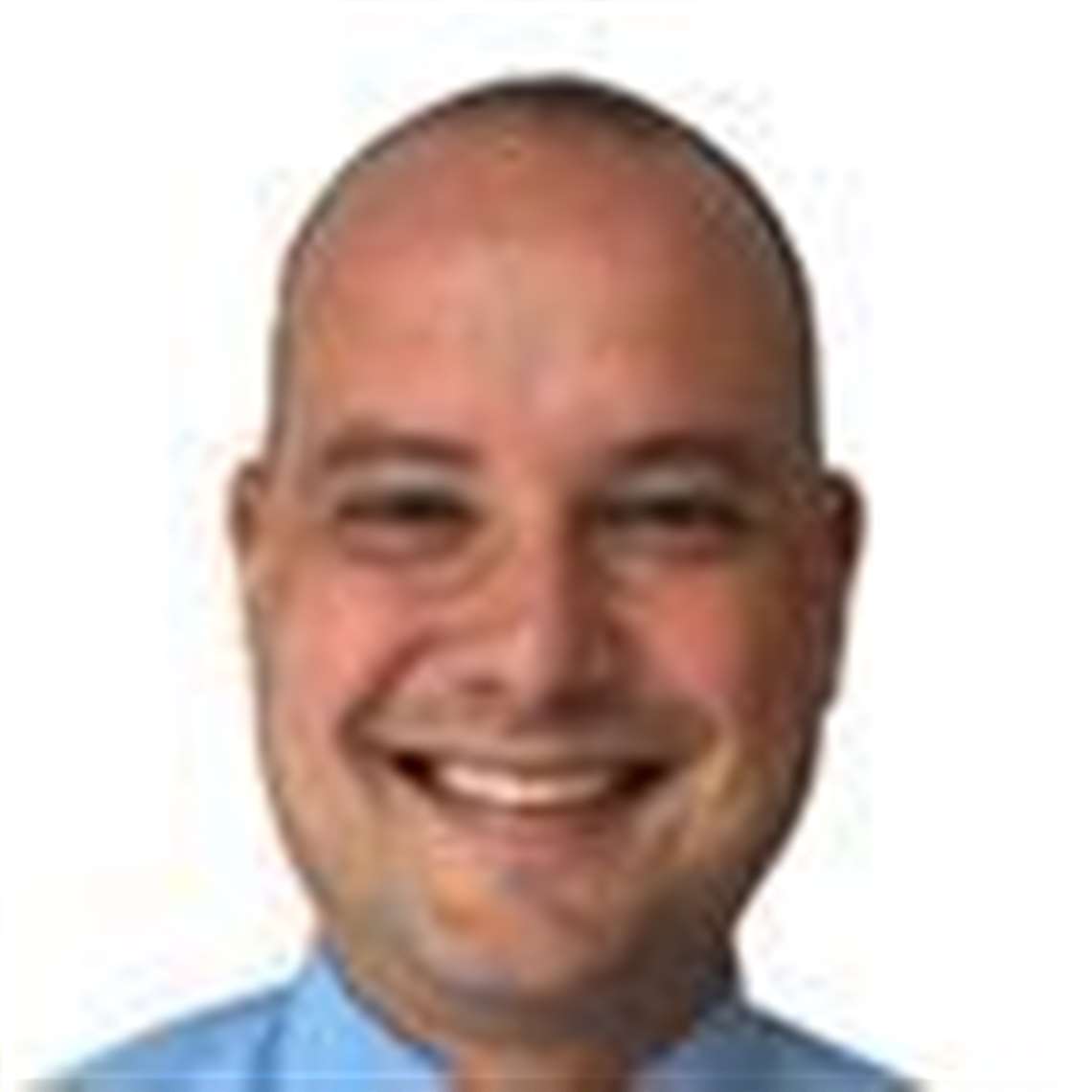
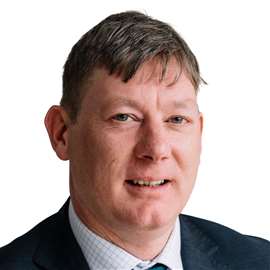