Read this article in French German Italian Portuguese Spanish
Apprenticeships help OEMs with employee recruitment, retention
06 February 2024
Manufacturers can make use of apprenticeship programs to foster loyalty in employees and gain a high-quality workforce.
Even though manufacturing facilities are no longer the dark, dirty and dangerous places they once were — thanks in part to dramatic advances in manufacturing technology as well as philosophies such as Lean, Six Sigma and Industry 4.0 — finding and retaining workers remains a challenge for many manufacturers. According to the National Association of Manufacturers’ Q4 2023 Outlook Survey, over 71% of manufacturers surveyed said the inability to attract and retain employees was their biggest challenge.
“We talk to so many industries every day that tell us they’re having a challenge finding a skilled workforce and to find the workforce that they need to grow their companies,” said John Ladd, administrator for the Office of Apprenticeship at the U.S. Department of Labor.
One way manufacturers are addressing this shortage as well as the skills gap is through apprenticeship programs. In the United States, they appear to be on the rise. According to a fact sheet from the U.S. Department of Labor about advanced manufacturing apprenticeships, FY2023 saw 59,000 apprentices participating in 2,900 advanced manufacturing registered apprenticeship programs across the United States. This is an increase from approximately 29,000 apprentices the previous fiscal year and the highest number in five years.
Common Apprenticeship Roles
Wisconsin is the U.S. state having the longest registered apprenticeship program in the country, according to David Polk, director of the Bureau of Apprenticeship Standards for the Wisconsin Department of Workforce Development.
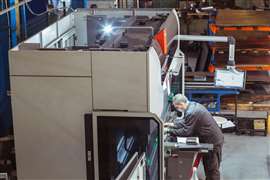
“I’ll say the top three manufacturing apprenticeships for our state are the industrial electrician —that’s the maintenance electrician,” he said. “The maintenance technician and the maintenance mechanic are our two largest manufacturing programs, and all three of those are roles that work to keep the assembly line moving.”
Nonetheless, they are not the only manufacturing roles suited to apprenticeships.
“To go down the list, we have tool and die machinists, electrical and instrumentation technicians, millwrights,” Polk said. “We have mechatronics technicians, which is a newer one — I think that program is only about five years old — injection mold, mold maker, IMTs (industrial manufacturing technician), and that’s an entry-level production worker that can then progress into a maintenance technician another role.”
Investing in Employees
When it comes to recruitment, retention and development, Polk said apprenticeship programs offer many benefits to manufacturers.
“For apprenticeships specifically, you are raising someone up and raising their skill level in a specific occupation, but you’re also building up their knowledge of your particular culture, of your workplace,” he said. “So not only ‘This is what it takes to be an industrial electrician,’ but ‘This is what it takes to be an industrial electrician at ABC Enterprises. This is what we do.’”
Ladd said this aspect of apprenticeship programs allows manufacturers to draw from a broader talent pool because workers don’t have to be fully trained for the specific job role.
“You’re committing to training them over time,” he said. “It really puts you on the foothold of how can I grow my own workforce versus what we have seen from a lot of industries where everyone tends to be fishing in the same pond. The pond tends to get smaller and smaller, and then you end up poaching from each other. And that can only go so far.”
Improving Employee Retention
Polk added that of any secondary education option — from job training to technical college to a four-year university degree — the apprenticeship model has the highest retention.
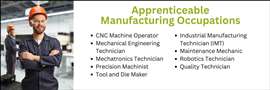
“When you’re investing in someone day-to-day, that individual is more likely to stay with your firm for at least five years,” he said. “That’s what our data shows. So in times like this, where finding talent is just few and far between, and keeping that talent is even harder, the apprenticeship model offers both. You’re training someone up in a skill set, so you’re not bidding against other companies to try to get this person to come to you, and you’re also more likely to keep that person long term because you’ve invested in them.”
According to Ladd, this investment sets employers apart in retaining talent.
“I think when it comes to retention, it’s also a really strong signaling tool,” he said. “You’re able to set your organization apart because your telling your workforce that you believe in them. You’re investing in them, and you’re developing them for long-term careers.”
Starting or Expanding
One of the challenges manufacturers have regarding apprenticeship programs is starting one. Those that have them may be looking to expand. Ladd said the Department of Labor can assist in a variety of ways.
“We are working every day providing technical assistance, support and information directly to companies,” he said. “They can work with us on a local level. If you’re working in Illinois or New Jersey — and those are states where there aren’t state apprenticeship agencies — they can work directly with our staff and we’ll provide them free technical assistance and support to help them stand up their programs.”
Ladd added that because the Department of Labor does not have the depth of manufacturing knowledge other organizations might have, they have contracted with industry intermediaries.
“For a lot of companies, it could be a little overwhelming or sometimes they’re not quite comfortable talking directly with DOL,” he said. “There’s an industry association that they work with regularly. They’re going to be more comfortable talking to them first. So they can go directly to one of these intermediaries, get technical assistance, get help developing a program.
“We’ve also made available funding that these intermediaries can provide — incentive funds for employers that want to start and need some help subsidizing the cost of standing up an apprenticeship program.”
STAY CONNECTED
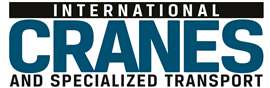
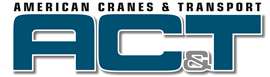
Receive the information you need when you need it through our world-leading magazines, newsletters and daily briefings.
CONNECT WITH THE TEAM
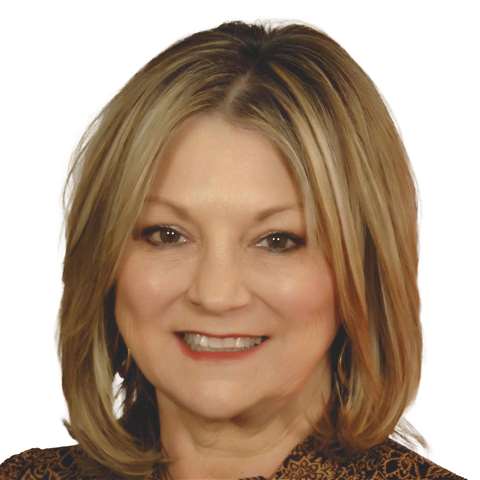
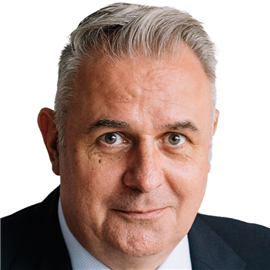
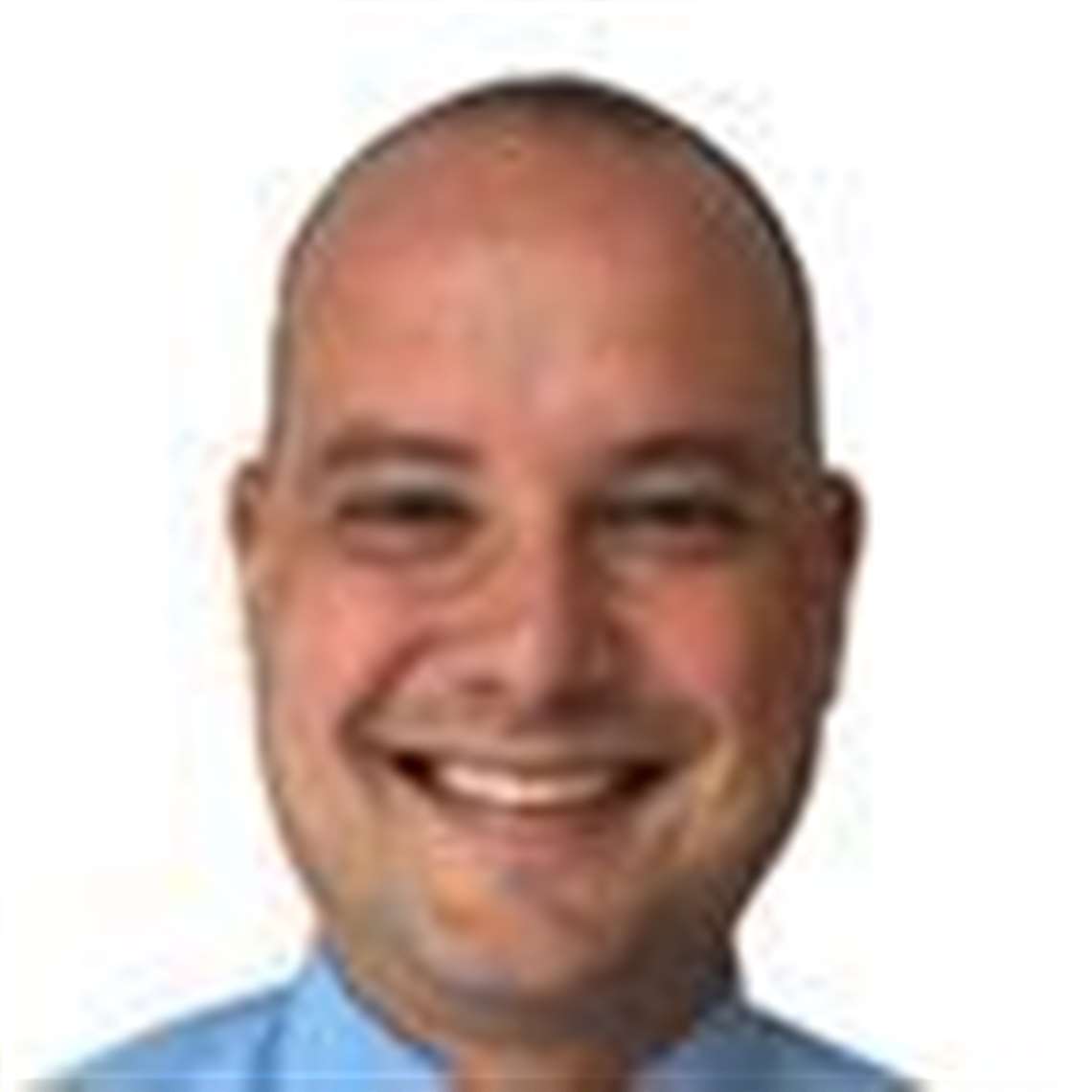
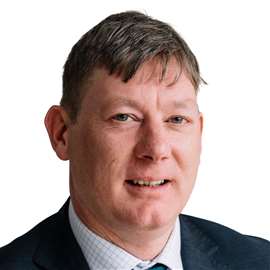