Barnhart completes intricate power plant project
04 May 2018
Barhart’s winning project took place at a nuclear power plant in Louisiana and required an innovative concept and aggressive execution plan.
One of the nuclear facility’s two clarifier units – the units which clean water from the Mississippi River so it can be used as cooling water to the plant – was in need of repair. The clarifier tank is a concrete structure with a wall height of 28 feet and an inside diameter of 178 feet. The “clarifier core,” which refers to the rotating equipment in the center of the clarifying tank, was supported by 16 lateral supports and tie rods that attached to the tank wall. The lateral supports had buckled, and ten out of the 16 were structurally compromised.
Immediate challenges
“The challenge for Barnhart began almost immediately,” said Gene Pugh, Barnhart project sales, “since once the clarifier tank had been drained and inspected from the observation platform, plant safety protocol prohibited anyone from entering the tank. There were many things to consider in evaluating repair options, but employee/worker safety was paramount to the plan that would eventually be approved by the customer.”
Barnhart’s scope was to provide a lift system capable of lifting from above the 600,000-pound clarifier structure so as to remove the damaged lateral supports, while also providing crane and rigging support for the subsequent reconstruction of the clarifier unit.
The customer initially suggested bringing in a heavy-lift crane to hold the structure while the lateral supports were removed, a method that would require the crane to hold the load for three weeks, and was ultimately deemed not feasible.
Barnhart next considered a girder configuration on the clarifier wall, and then a girder system independent of the wall. The concrete wall, which was 28 feet tall and 2 feet thick, would need to be evaluated for its vertical-load capacities, and the rigging design would be complex.
After all options were considered, a four-tiered girder arrangement on the concrete wall was proposed and accepted. The base tier was comprised of two eight-foot girders that were each 180 feet long with a 164-foot span. This was the largest span Barnhart had ever attempted.
The second tier was comprised of two temporary bridge girders that were each 76 feet long. The second tier was crucial
as it allowed for the load points on the eight-foot girders to be moved closer to the walls instead of being closer to the center. This reduced the deflection on the eight-foot girders to acceptable levels and gave Barnhart the headroom needed to obtain the necessary sling angles for the rigging method.
The third tier was comprised of two five-foot transition girders that were each 84 feet long with a 74-foot span. The top tier consisted of two trapezoidal girders that supported the rigging – each one was 72 feet long with a 55-foot span. The upper assembly also had slide systems on tiers three and four that enabled precise placement of the rigging over the structure.
Barnhart’s concept and execution plan adhered to all of the customer’s site-safety procedures. The rigging design and fabrication allowed for the 600,000-pound load to be lifted safely from 24 rigging locations, which ensured the stability of the structure. The lifting solution was resistant to virtually any severe weather events that could have occurred during the course of the project. Even the expected deflection was mitigated with several design innovations, including the strategic placement of the second-tier girders and rockers, also developed by Barnhart, which nullified the effect of deflection on the upper lift system.
Finally, the assembly and disassembly plans were created with worker safety as the number one priority. Barnhart held multiple job-hazard analysis meetings (JHA) each day and supervisors, operators and riggers went through additional site-specific training to secure their Qual-cards. Most importantly, the project was injury and accident free.
STAY CONNECTED
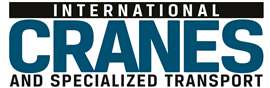
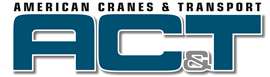
Receive the information you need when you need it through our world-leading magazines, newsletters and daily briefings.
CONNECT WITH THE TEAM
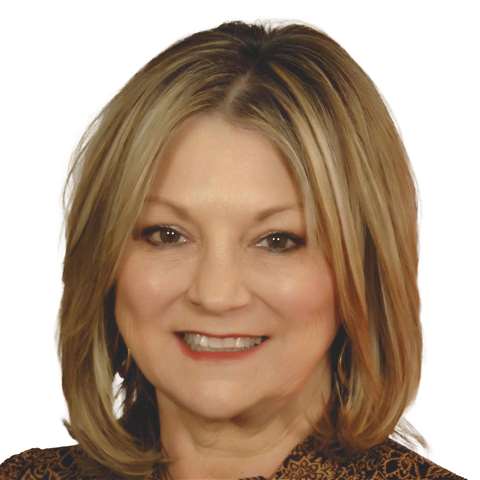
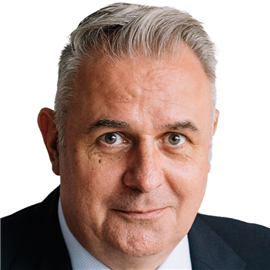
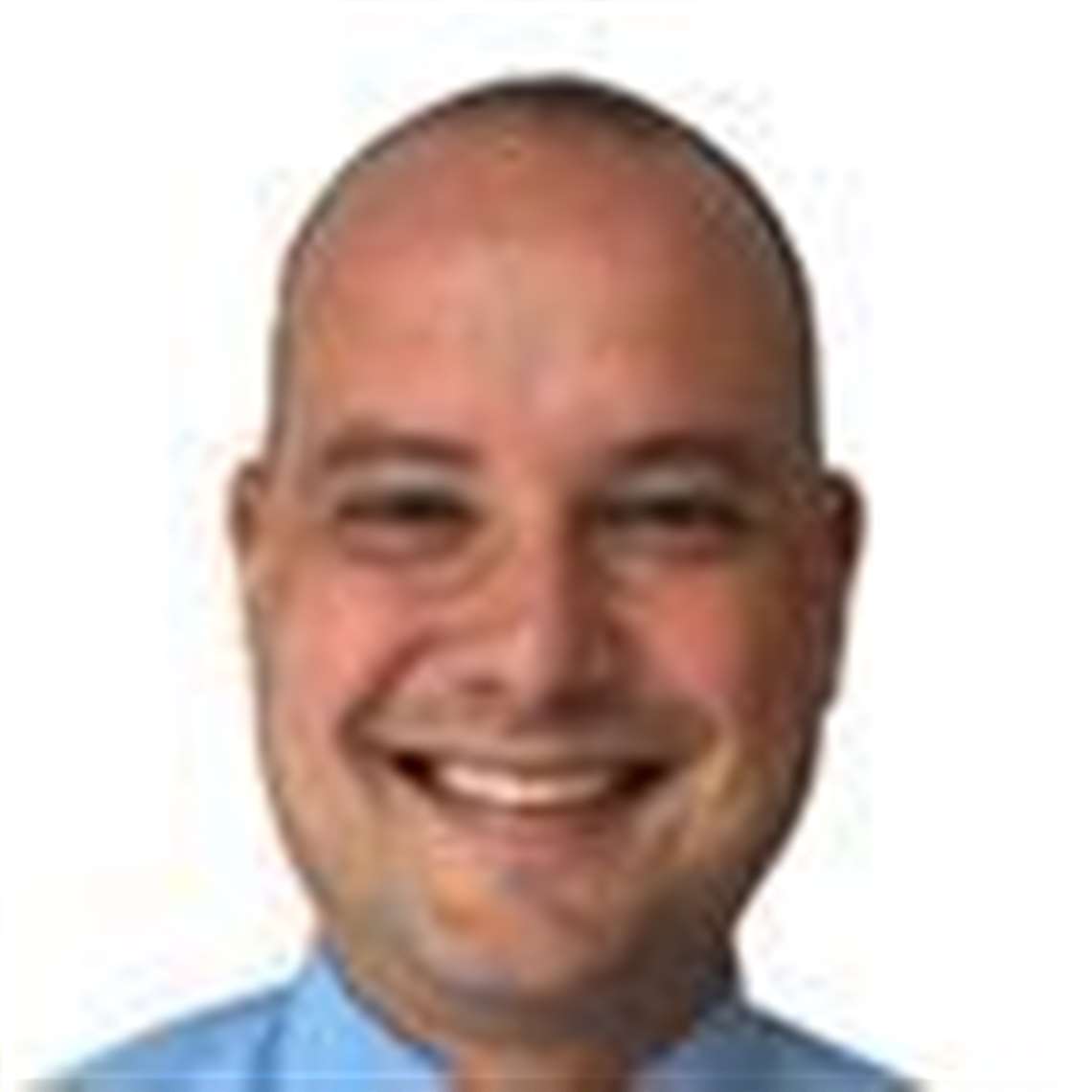
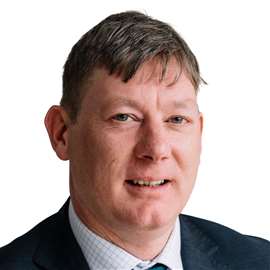