Crawler cranes serve as marketplace staple
11 July 2017
The ubiquitous crawler crane is a perennial favorite that enjoys a strong market following.
Simple, flexible and strong. These are the enduring attributes of a lattice boom crawler crane.
TNT Crane & Rigging CEO Mike Appling put it this way: “Crawler cranes continue to add many technological improvements and enhancements. Yet at their core they are very simple machines with great charts and flexibility across many applications.”
The crawlers in TNT’s fleet work across a myriad of industries – commercial construction, road and bridge building, refinery turnarounds and wind maintenance and construction work. Crawler cranes will always have a place in the fleets of crane service companies, Appling contends. Lampson International’s Randy Stemp agreed.
“Lattice boom crawler cranes will always be one of the most effective and most in demand tools on the market,” said Stemp, engineering project manager at Lampson.
With one of the largest crawler fleets in the world, Lampson has long embraced the many features of crawler cranes.
“They have mobility with the load and the ability to quickly set up between lift locations on a job site,” said Stemp. “They are also much easier to move on a congested site.”
Large-scale, long-term projects that have multiple lift locations almost always require a lattice boom crawler, Stemp said.
“Lifts that require the crane to travel, such as tilt-up operations and vessel erection necessitate the use of a crawler,” he said. “They are needed for a wide variety of projects throughout the U.S. and the world, ranging from infrastructure projects to wind farm erection, power plant construction to offshore work.”
TNT Crane & Rigging’s Liebherr LR1600/2 works in Wisconsin at Dairyland Power.
The oil and gas industry, both upstream and downstream operations, have a long history using crawler cranes, according to David Cowley, president of Boss Crane & Rigging.
“Crawlers have strong attributes in many applications, whether you are talking about new construction, the oil field business or at wind farms,” Cowley said. “At Boss, we run numerous crawlers in our oil field division. They are excellent machines for oil rig assembly and disassembly. Through the years, crawlers have transformed into being the preferred machine for rig movement. They offer versatility because they can walk with the load.”
In the oilfield, Cowley said the cranes of choice are in the 80 to 110-ton capacity range. Crawlers are also the crane of choice for work in petrochemical and natural gas plants. Currently, the Gulf Coast region has a huge concentration of crawler cranes working at petrochemical plants from Texas to Florida.
“Right now, the bigger crawlers are seeing higher demand,” said TNT’s Appling. “They are differentiated in the market, and there is no pressure from other alternatives. Larger rough terrains, all-terrains and in some cases tower cranes are putting pressure on certain applications of smaller crawler cranes. The slowdown in the oil field has also left a bit of a supply glut on this end of the market.”
Crawlers are also in greater demand in the wind industry that has picked up again due to favorable tax credits.
“In the wind business, you need the larger crawlers,” Cowley said. “These cranes still have better charts and you still need the capability of walking or traveling.”
VPC: unique selling point
When the Manitowoc MLC300 crawler crane debuted with the Variable Position Counterweight (VPC) and VPC-MAX heavy lift attachment, one of its unique selling points was the crane’s barge-lifting capabilities. The reduced footprint and floating counterweight meant that it would be more efficient to mount on a barge. Contracting teams could erect the crane onto smaller, water-based barges because the machine automatically adjusts its center of gravity for each lift.
Kraemer North America is using a Manitowoc MLC300 to help replace an 84-year-old truss bridge, the 2,482 foot-long Savanna-Sabula Bridge near Savanna, IL. The Illinois DOT hired the Plain, WI-based company to construct the new bridge, which spans the Mississippi River between Savanna and the island community of Sabula, IA.
While planning the project, which involves the construction of two 958.5 foot-long outer plate girder spans and a central 546 foot-long tied-arch span, Kraemer realized that a barge-mounted crane solution would be necessary to access the lifts for the tied-arch span. The company sought consultation from Dawes Rigging & Crane Rental, a member of the ALL Family of Companies, about a crane that could be mounted on the tight working quarters of a barge, but still provide high capacity lifts to great heights to aid in the bridge construction.
Until the advent of the VPC technology, contractors often used Manitowoc Ringer cranes for a barge-mounted solution. The round Ringer shape helped stabilize the crane and distribute the weight of the machine. Milwaukee-based Dawes suggested the newer MLC300 that could automatically adjust its counterweight to provide greater stability for each lift.
“With the VPC, the MLC300 is always finding a new center of gravity based on the load that’s on the hook,” said Patrick Shea, project manager for Kraemer. “This crane has helped us to achieve almost zero list while working on the barge, keeping every lift level while minimizing the barge’s rotation. And the VPC saves space, too – most crawler cranes with the required length of boom would not have fit on the barge in the first place.”
The MLC300 is now erected on a 70 by 195-foot barge in the Mississippi River. It is lifting 76-ton arch rib sections to a height of 165 feet using 295 feet of main boom, all from a 100-foot radius. To meet the lift radius and pick weight requirements on the job, Kraemer’s MLC300 had to be outfitted with its optional VPC-MAX attachment, which enhances the crane’s capacity and enables additional boom and jib length combinations.
“We’ve had a great experience working with Dawes on this project,” Shea said. “They provided the ideal crane for this work environment. The whole time we’ve been using the MLC300, we’ve seen the barge list by less than a degree – it’s a testament to the stability that this crane provides and it’s a big reason we’re able to keep to our schedule.”
Construction of the $80 million Savanna-Sabula Bridge replacement began in March of 2017 and is on schedule for completion in 2018. The new bridge will span 2,463 feet in length and will meet modern-day deck-width standards to improve the flow of two-lane traffic.
Rail road trestle
Sterett Crane & Rigging recently dispatched its Demag CC-2400 to Newport, IN to replace an old railroad bridge. The job site was a challenge from the get-go because of the limited space to set up the crane and a 48-hour window to lift and place the new bridge sections. During the setup and tear down of the crane, trains rambled back and forth.
The CC-2400 was rigged in the SSL configuration with the Vario System attached. The crane had 177 feet of main boom, 352,000 pounds of house counterweight, 88,000 pounds of car body counterweight and 176,000 pounds of super lift counterweight. The reason for all the counterweight was the 133-foot radius at which the crane would be lifting and placing the four railroad bridge sections that weighed about 94,000 pounds each.
“A railroad is never an ideal situation to set up in,” said Matt Crisp, crawler crane fleet manager at Sterett. “For this job, there was one way in and one way out. This presented quite the challenge when it came to bringing in the crane on the trucks. Once unloaded, the trucks had to back out.”
There were some 26 truckloads required. Plus, there was the dilemma of needing to set up adjacent to the sloped railroad track area.
“Every time a train would come by, we had to halt the work of setting up the crane,” Crisp said.
Ground conditions were optimal, with a rock base already at the site.
“They had a good rock base and did a great job of preparing the site,” said Crisp. “We brought in our own 4 by 20-foot mats, about 40 total.”
After the crane was set up, inspected and tested, the demolition of the old bridge took place. The job ran like clockwork, with CSX handling all of the demolition and installation of the new bridge section, Crisp said.
This crane was ideally suited for the job because of the Vario System, Crisp said.
“It allowed us to pick up these loads at short radiuses and we could actually move the counterweight under load,” Crisp said. “Once we float the tray we can shift the counterweight out and set the pieces at the 133-foot radius without have to stack and restack the counterweights.”
Being able to walk the crane was another benefit.
“We did walk it forward and back a little bit to get all the pieces ready to be set,” said Crisp.
While the crane only walked 20 to 30 feet, the ability to walk the crane was critical.
“That’s the beauty of a crawler,” said Crisp. “Once we are floated and off the ground we are at liberty to walk and get ourselves in the right positon to make a lift.”
The duration of the project was about six days, with the job under hook for just two days. Crisp said his team prepared a lift plan for the project to assure there wouldn’t be any surprises.
Sterett Crane & Rigging has about 28 crawlers in its fleet, ranging from 100 to 660 tons capacity.
Versatile lifter
Bigge Crane & Rigging is a major player in energy industry projects in the Texas Gulf Coast region. Currently, the company’s Kobelco CK1600G is working on a multi-billion dollar Liquefied Natural Gas Pretreatment facility spanning 12 acres in Freeport, TX.
The 160-ton capacity Kobelco crawler is on the job for 12 months, and most recently is erecting steel sections that weigh up to 10,000 pounds each. The CK1600G was chosen for this job due to its capacity and line pull, which is stronger than any other machine in its class, according to Joe Nelms, Bigge vice president.
One of the many new structures being erected by the Kobelco CK1600G is 180 feet tall and approximately 500 feet long.
“Typically, the challenges of this type of job require a balance between ensuring the safety of the working staff, the accessibility to operator-friendly equipment and knowledge about the atmosphere that this job needs to be performed in,” Nelms said. As a dealer for Kobelco, Bigge has 30 Kobelcos in its rental fleet.
“We believe they’re well built, operator friendly and easily transportable,” said Nelms. “Bigge uses Kobelco crawlers for a variety of applications including steel erection, precast walls, bridge girders, drilling, rig moving and general construction.”
At ConExpo, Bigge took delivery of its 100th Kobelco, making it the leading U.S. Kobelco dealer and rental company.
“We have spent a great deal of time and effort crafting the content and size of our crawler crane fleet,” Nelms said. “Crawler cranes are an essential component for the construction of larger civil, industrial and commercial projects, and they’re integral to development and maintenance of our nation’s infrastructure.”
Bridging the gap
Bow, NH-based R.S. Audley was awarded the contract to replace four northbound lanes of Little Bay Bridge, a nine-span steel girder bridge that carries Route 4, NH Route 16 and Spaulding Turnpike over the Piscataqua River in southeast New Hampshire. Little Bay Bridge carries over 70,000 vehicles each day and is forecasted to carry 94,000 vehicles by 2025.
The first task for R.S. Audley was to remove more than 3 million pounds of old, 1960’s era steel. Crews performed this work using several cranes from the Audley fleet, including a 110-ton capacity Link-Belt 218 HSL lattice crawler crane.
By mid-2016, the replacement of steel for the refurbished northbound lanes of Little Bay Bridge had begun. Steel erection was performed by working from both ends of the new bridge structure – 1,589 feet in length – to the center, five girders across with diaphragms connecting and strengthening the superstructure over the existing piers.
To complete the final steel work, R.S. Audley purchased a new 150-ton Link-Belt 238 HSL crawler and rented a 250-ton 298 HSL from Link-Belt distributor Wood’s CRW.
One of the most difficult elements to the steel replacement was winds gusting up the bay from the Atlantic Ocean. For lifts toward the center of the bridge, both Link-Belts were used in the early morning before winds picked up – one crane for each 100-foot beam. The 155-foot long center beams weighed 78,000 pounds each. The cranes lifted in unison and the beams were adjoined in the middle to form the center span. Steel diaphragms were installed the rest of the day to space the beams alongside each other.
“Aside from the wind, the 3 percent grade change coming up the bridge is something else to take into consideration, you must adjust each pick point a little bit to make sure the beam is hanging correctly for final placement,” said Scott Stevens, Audley vice president. “Using two 25-ton Crosby beam clamps, the operator is able to reach out to the predetermined point, make sure it’s hanging correctly, pick it up and swing it out into position and marry it up to the previously set field splice.”
R.S. Audley’s crews only had a working space of about 28 feet wide to operate the two crawlers. The new span went five girders across with diaphragms connecting and strengthening the superstructure over existing piers.
“The only weight restriction we had was keeping the ‘moving’ load of our cranes down below 300,000 pounds,” Stevens said. “We were able to do this by removing counterweights as necessary during travel between pick locations. The stacked counterweights of the 238 and 298 made this a simple and straightforward process.”
Alley squeeze
Ness Campbell Crane+Rigging was tasked with providing a crane that could work in a narrow alley and lift over a 125-foot tall building to set mechanical and process equipment at a 220-foot radius. To make the lifts at the Hillsboro, OR job site, the company’s Liebherr LR1200 was configured with 154 feet of #2320 main boom and 233 feet of luffing jib, according to John Anderson, president. At one point the luffing jib will be changed out to a 293-foot luffing jib.
The crane was set up on 24 by 4-foot wide by 1-inch thick mats that were shimmed with 1.5 inches of plywood to achieve a level work platform.
Ness Campbell Crane+Rigging’s Liebherr LR 1200 works in an alley that provides for challenging lifting up and over a 125-foot building. The crane is setting mechanical and process equipment at a 220-foot radius.
“The reason this crane mat was selected was so we could meet a specific ground bearing requirement given to us by the plant owner,” said Anderson. For the lifts the crane required 181,440 pounds of main counterweight and 79,400 pounds of carbody counterweight.
“We used single part headache ball and numerous rigging configurations, depending on the equipment being hoisted,” Anderson said.
This crane was being used to service the customer’s ongoing improvement inside of their process facility. It was set to be on the job for a four to six month period.
Each day, the crane lifts numerous pieces that weigh all different weights and dimensions, changing with every lift.
The biggest challenge of the project is the tight assembly and work area.
“The Liebherr LR1200 was the right crane because of its tremendous long luffing jib length and capacity and its ability to work within the tight area that the customer needed,” said Anderson. “This crawler gave us the ability to be mobile during set up and work, with a long boom and luffing jib combination. The conventional boom also gave us the capacities that otherwise we would have had to use one of our 500 to 600-ton capacity all terrain cranes to achieve the same capacity.”
STAY CONNECTED
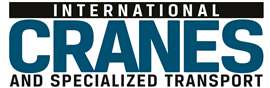
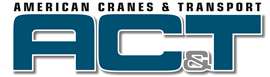
Receive the information you need when you need it through our world-leading magazines, newsletters and daily briefings.
CONNECT WITH THE TEAM
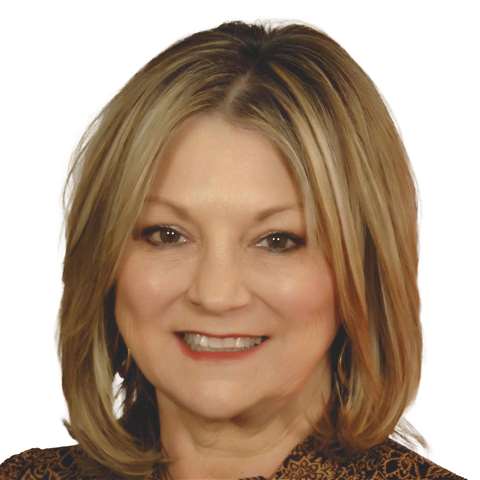
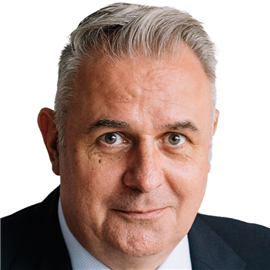
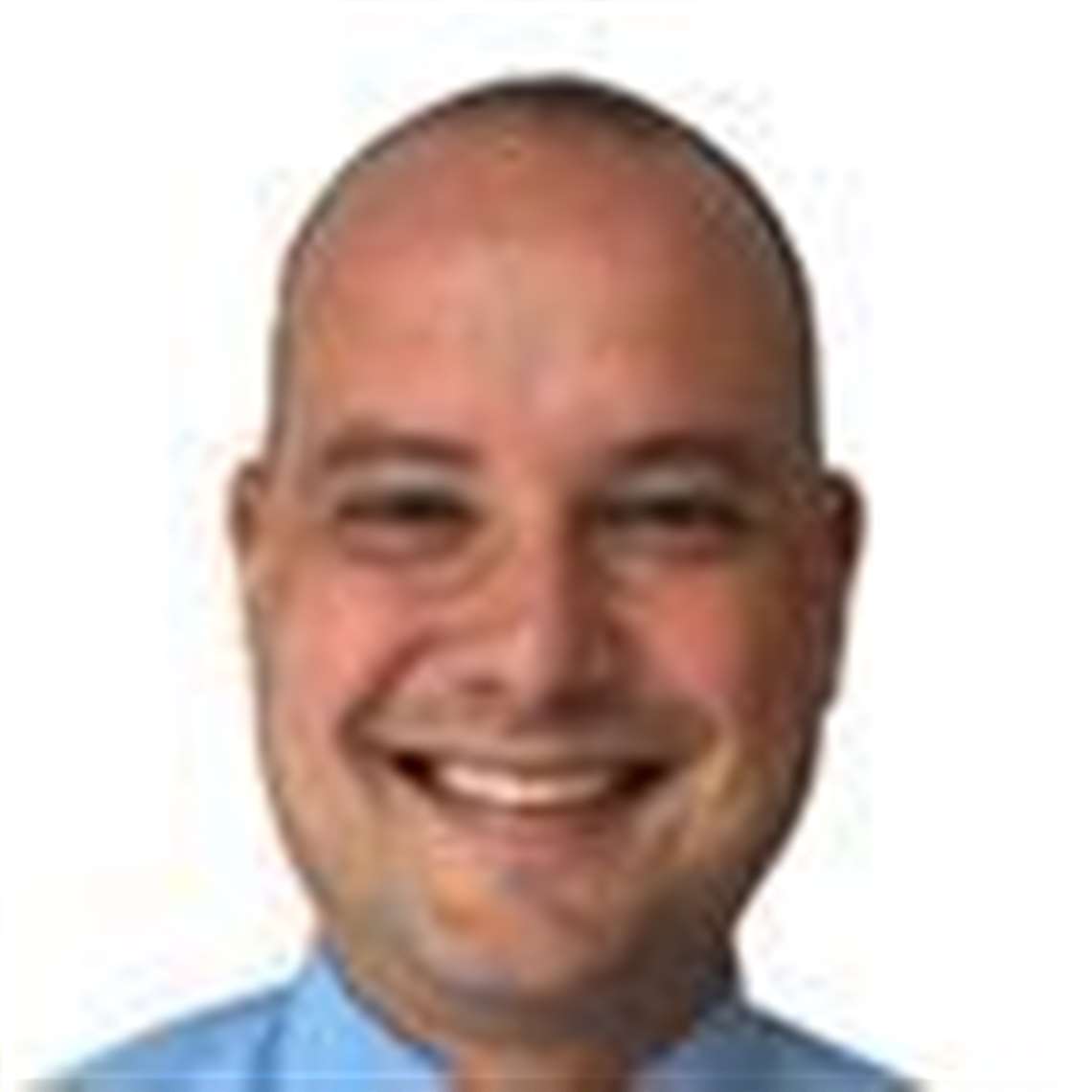
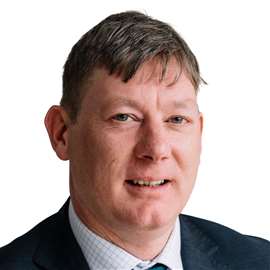