Easy up and around - a new generation of specialized lifting equipment
17 April 2008
The demand for specialized lifting has produced a new generation of equipment that offers innovative solutions for increasingly complicated jobs. American Cranes & Transport reports.
Building a better mousetrap for lifting and moving heavy, sensitive and sometimes even unconventional machinery, vessels and other items is a growing sector of the lift industry.
Innovation is the name of the game in designing specialty or alternative lifting products that are cost-effective and get the job done right.
Following is an overview of some of the new and improved specialty lifting devices on the market.
Lift-n-Lock
J& R Engineering is enjoying strong demand for its Lift-n-Lock hydraulic boom gantries. “Our gantries offer the ultimate in structural strength when lifting heavy loads to ever-increasing heights,” says Ken Della, at J& R Engineering.
“The safety features include strong telescopic booms and a Cam Lock system to ensure that projects can be completed effectively and, most importantly, safely.”
Recently J& R Engineering's Series 1400 Lift-n-Lock gantry was used by Casper, WY-based Energy Transportation Inc for a tailing operation for the tip-up of a 500 ton, 145 foot long reactor at a plant in El Paso, TX. Della says the gantry was the perfect solution, offering the stability needed for such a precise operation in tight quarters.
Shuttlelift gantries
Shuttlelift recently used its SLl 150 rubber tired gantry (RTG) crane to pick up 125 ton natural gas pump sleds and move them within the Hanover manufacturing plant in Houston, TX.
The sleds are assembled at one place in the plant and must be moved through the plant as they are assembled and completed. With a capacity of 150 tons, the SLl 150 picks up the sleds, and then travels through the plant, negotiating tight curves and turns.
The company assessed several solutions for moving the sleds, says Dan Reinholtz of Shuttlelift. “The option was to either re-design the plant and install an overhead rail crane or use the Shuttlelift gantry crane,” he says. “The SLl 150 handles the sleds easily and without a problem.”
Shuttlelift rubber tire gantries are also serving the wind power industry, moving blades throughout the plants in which they are manufactured.
“We have been quoting more cranes to that industry as of late with the increase in oil prices,” says Reinholtz. “There are many projects in Canada and the US for which we are quoting wind power equipment.”
Flint Energies in Edmonton, Alberta, Canada is using a Shuttlelift ISL 50 to transport oil refining modules to the tar sand extraction sites in Fort McMurray. Rated at a capacity of 50 tons, the ISL 50 is used to move modules and miscellaneous piping and equipment.
Traksporter
Beck Inc., owned and operated by Rob and Lynn Beck, has introduced the Traksporter, its latest alternative lift and move invention, a self-propelled, hydraulically driven, radio-controlled machinery skate with 360 degree turning radius.
After a decade in development and use in Beck's rigging business, the Traksporter has been well received in the market, according to Lynn Beck.
“The Traksporter was designed as a slow-moving crawler system with a compact profile of 6 feet high and can push or pull 120,000 pounds and more,” she says.
“The crawler has smooth track pads that are easy on floors yet allow it to climb a quarter-inch floor difference without disturbing the load.”
Beck says the machine has a “great wow factor,” and that when it is used in a new clients' factory or plant, workers from all over come to watch the little 500 pound crawler move a tremendous amount of weight.
She says that although the product is not that well known, once people see what it can do they are impressed.
Among the most complicated jobs for the Traksporter was the in-plant relocation of a 106,000 pound punch press that needed to be moved 800 feet from its original location.
Beck explains that the press was raised with jacks and set on a three-point system including rollers and the Traksporter. It took two men two hours to complete the move.
“Our customers tell us we have a valuable piece of equipment,” she says.
Slide track and lift tower
Barnhart Engineering has used its custom slide track and small footprint lift tower to remove two aging moisture separator reheater (MSR) units at a nuclear plant in Michigan and then install new ones.
Located at DTE Energy's Fermi 2 nuclear plant in Newport, MI, the MSRs are 110 feet long and weigh 300 tons each. When the plant was constructed it was necessary for the MSRs to be placed in position in halves and then welded and insulated in place.
Initially the plan was to remove the aging units and install the new ones the same way but Barnhart engineers devised a better and more cost-effective plan.
“By using the slide track and modular lift tower, Barnhart was able to remove and reinstall both the old and new MSRs respectively as a single piece, according to Chris Teague, director of marketing.
“The plan also eliminated the need to weld the two new MSR halves and insulate the MSR in place.”
In the end the Barnhart solution allowed DTE to save several days in its critical path timing, lower project risks, improve “as low as reasonably achievable” (ALARA) exposure to radioactive materials and to increase project safety.
Modular lifting beams
A quick solution was needed for a specialized lift in Tyler, TX, where the goal was to build a 2,160 square foot house in less than three hours. A charity project of the Tyler Area Homebuilders Association, the job involved placing a roof system on the house in one swift lift.
Luckett Crane of Commerce, TX provided the 240 ton Grove truck crane and operator while Lifting Gear Hire provided the modular lifting beams and rigging from the crane hook to the roof attachment points, according to Chris Hyatte at Lifting Gear Hire in Dallas.
“The dilemma was that they needed a spreader bar system to lift the entire roof in one piece,” Hyatte says. “The lift was a success and the house was completed in the record time of two hours and 50 minutes.”
Harold Luckett of Luckett Crane says the roof system, which had been pre-assembled complete with the electrical wiring, duct work and even the ceilings and shingles, weighed about 30,000 pounds and was designed to cover the 2,000 square-foot footprint of the home.
After being lifted into place it was attached at certain points on the walls, which were already set in place.
Luckett says he relied on Lifting Gear Hire to rig the job and he just provided the crane and the operator. “We had the client contact LGH so they could do all the rigging,” he says.
The house, which has three bedrooms, two baths, a two-car garage and full landscaping, was set to be added to the Guinness Book of World Records as the fastest built single family house in the world, Hyatte says.
Rowles-A-Long skates
Rigging skates are getting positive attention from the manufacturing sector. Roger Hedderick, president of Erie, PA-based Rog's, uses the Rowles-A-Long line of rigging skates to move heavy machinery.
“One of the main pieces of equipment that we depend upon daily are our skates to move heavy machinery,” says Hedderick. “They are easy to use, roll easily and are strong enough to take the abuse that is familiar with rigging.”
The Superior Tire/Rowles-A-Long line includes steer skates ranging in capacity from 7.5 to 50 tons. The newest model is the 15-ton Rowles-A-Long steer skate, according to Tim Rowles.
“The Rowles-A-Long skate line is floor safe with high carrying capacity and low rolling resistance polyurethane load wheels,” explains Rowles. “ We use a 1 inch shaft, heavier than the industry standard, to avoid breakage. Special 6205ZZ bearings are standard hardware.”
In addition, as a manufacturer of polyurethane tires and wheels, and also being a machine shop, replacement parts for the Rowles-A-Long skates are available directly from the manufacturer.
Aero-Caster
AeroGo's Aero-Caster can be used to move machinery, equipment and components weighing from one to 6,500 tons. Connect AeroGo's products to standard compressed shop air and one operator can easily move or “float” 5,000 pounds or more.
Omnidirectional, low friction positioning offers tight space maneuverability, allowing for efficient equipment installations and plant reconfigurations. AeroGo was formed in 1967 to provide engineering, design and manufacturing for specialized assembling and tooling fixtures for the aerospace industry.
Since then AeroGo has provided what it describes as practical and efficient methods of rotation, alignment, transfer, location and movement of heavy materials and equipment. The company offers custom solutions for load moving problems using wheel transporters, rails, Aero-Casters or stationary manipulators.
Kvichak Marine, a design and construction facility, uses AeroGo technology to move its vessels out of the facility without damaging the building or boat, even with the tight clearance overhead and on either side of the load. Mono-hull or dual hull catamaran styles can both be moved with one system
Strand jacks
Recently, two huge spans of the San Francisco Bay bridge, under construction in San Francisco Bay, were lifted off a barge and put in place using computer-monitored Hydrospex brand strand jacks.
While strand jack technology is not new (it was first used in the early 1970s), interest has heightened, and in the last few years strand jacks have become one of the most sophisticated specialty lifting devices.
The strand jack lifting technique originates from the concrete post-tensioning principle.
A bundle of steel cables is guided through a hydraulic cylinder. Above and below the cylinder is an anchor system with a number of grips. Those grips clamp the cable bundle.
Stroking the cylinder in and out and engaging the grips in the anchors result in a lifting or lowering movement. The cylinders are powered by diesel or electrically driven hydraulic power packs.
A software program synchronizes the motion of the strand jacks and adjusts the motion to the loads per lifting point. This program can be used to simultaneously control up to 20 strand jacks. In operation all loads and anchor positions are visually displayed.
The number and type of strands used in a jack determine its safe working load. For lifting applications Hydrospex strand jacks are calculated with a 2.5 safety factor of breaking load to working load.
STAY CONNECTED
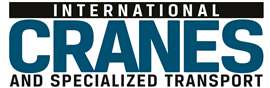
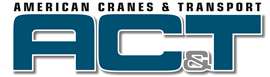
Receive the information you need when you need it through our world-leading magazines, newsletters and daily briefings.
CONNECT WITH THE TEAM
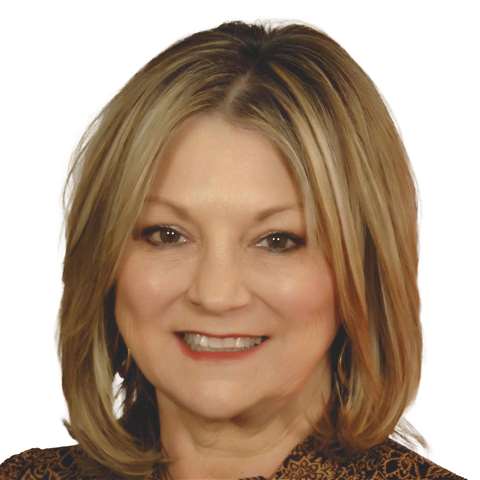
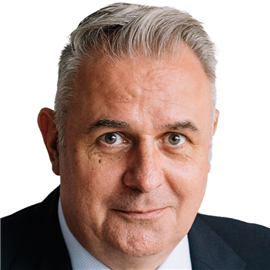
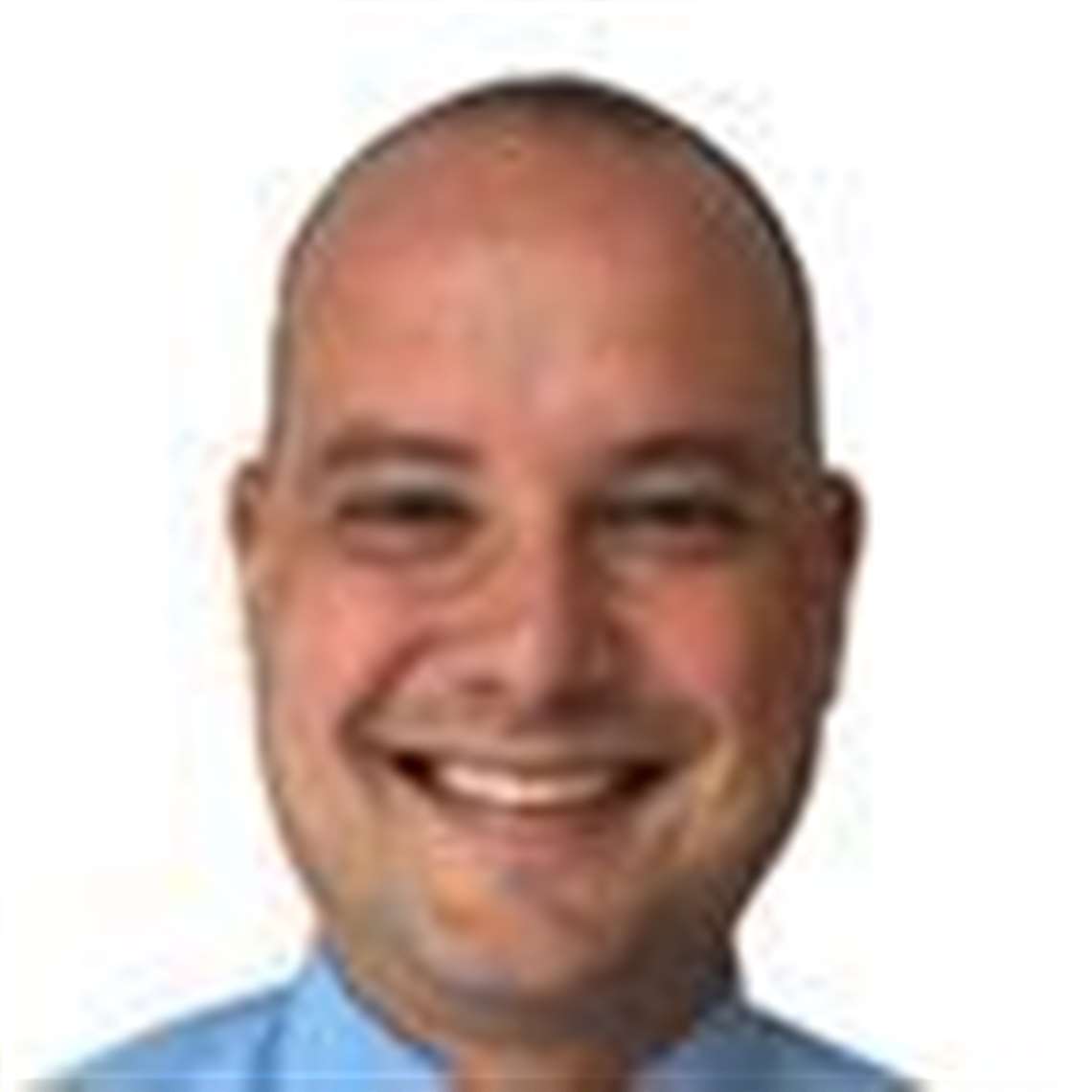
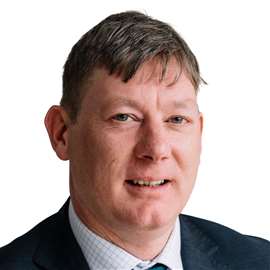