Great returns
24 April 2008
Safety and training can no longer be considered as ancillary, optional, or elective. With insurance premiums continuing to rise and increasingly stringent requirements by federal, state and local governments, safety and training have become a “make or break issue” for many companies, according to Jenny Sale, owner and president of Safety Resources Unlimited (SRU) based in Oklahoma City, OK.
“Our business has picked up 50% over the past two years,” says Sale, whose company develops customized mobile crane training programs and is an accredited training and testing location for NCCCO written and practical exams. “We attribute it to the marketing effort by the CCO and the lobbying being done in different states to require certified operators.”
Prior to two years ago, getting some companies to voluntarily train their mobile crane operators “was like pulling teeth,” Sale says, but today, those same companies are seeking out training programs, having realized that the investment pays off on every level. About half of the training Sale's company performs is for CCO certification and the other half is non-mandatory customized training for individual companies. A CCO certified crane operator and examiner, Sale says she and her instructors teach unskilled operators the basics of running a mobile crane, and they teach experienced operators what they will need to know to pass the CCO certification exams.
“The ground level training meets federal regulation and state requirements, assuring that the operator knows how to set up the crane and pull the levers,” she says. “The next level up is certification training, for experienced operators whose employers' want them to have the certification status.”
Crane operating companies are interested in assuring that their operators can operate any piece of equipment to comply with OSHA federal regulations and the ASME B30.5 standard and, she says, employers are “taking comfort” in the fact that they are lessening liability if OSHA calls on their doorstep.
Safety culture
For employees of Southway Crane & Rigging, safety training and safety accountability is as much a part of their job as running the equipment, according to Greg Fussell, who, with Jerry Reynolds, owns and operates the Georgia-based company.
“We have built our crane business on customer service and customer safety,” Fussell says. “The first thing our customers expect is well trained operators. All of them have been CCO trained and they have taken the additional MSHA and OSHA training. Plus we also do quarterly training updates at which time we will give them a pre-test and then a post-test so we can measure the information they digested and learned.”
The safety culture at Southway has been a mainstay for eight years, Fussell says, and yet it is still an evolving program. “You hate to use the word &leading edge,' but we want to make sure our operators are the best trained,”he says. “Our safety program not only involves our employees, but also their entire family. We want to make sure our men are taken care of and that they get home to their wives and families every night. In turn, these families appreciate the fact we are concerned about them. We want our employees to have a positive experience in working for us.”
Southway's investment in safety has reaped benefits in the relationship the company has with its brokerage group McKell, Wrath and Paris, Fussell says. “We have presented our program to our underwriters and by living up to our commitments we have received significant insurance savings,” he says.
Southway ties its safety goals to its employees' vacation and bonus programs, which means that the safer employees work, the more return on their individual bottom lines. “This is how we keep our employees involved in safety from day one,” he says.
There is also a close relationship between safety and the upkeep of cranes, vehicles and other equipment. Southway's safety program involves close inspection of cranes - daily, weekly and monthly. Operators and truck drivers write a maintenance report on the equipment they operate, and the reports must be turned in for a paycheck to be issued. “Based on that type of activity, we have direct communication between our master mechanics and our truck drivers and operators to keep the equipment in good repair,” he says. “In the crane business, if we do not take care of our equipment and our men and function in a safe operating practice, we don't really have anything. If the equipment deteriorates, the customers recognize it. The companies that take care of their people and equipment, those are the ones that succeed.”
Total buy-in
For Bennett Motor Express in McDonough, GA, safety has become a tenet of the philosophy of the company, according to David Lowry, president. “Two years ago we implemented a safety culture, which is different than being safety conscious or implementing training here and there. Our program has the buy in from the top level executives and filters down internally through our operations, sales department, dispatchers, all the way to log clerks and to drivers to owner/operators.”
Lowry says safety is now an everyday element of the company.“Before this program, we thought we were safety conscious,” he says.“We'd have a couple of safety meetings a year when we felt like we could grab the most people and jam a bunch of information in front of them and hope for the best. This year we are slotted to have 160 safety meetings throughout the country.”
Like Southway, Bennett has added employee incentive programs to encourage safety. “The incentive program has some teeth,” he says.“This year it's worth a couple of grand if you comply with the program.”
Bennett's safety culture has allowed the company to lower its insurance costs, as well as prevent accidents. “We saw it was working, and we were able to take on more liability for deductibles and be more confident about it. We believe this program was something we really needed to do in our course of business. We believe it has saved us a tremendous amount of money in claims.”
Training mission
From the manufacturers' perspective, Terex training manager Soenke Eichhorn says training users on the safe operation of Terex cranes is a company mission. “Today, training on cranes is a very important aspect of ownership,” says Eichhorn. “Cranes now can do things and lift loads they could not achieve years ago because of technology, better steel and components and better engineering. These are high tech machines and the owner needs to know the proper way to operate, set up and safely use them. If something goes wrong, they need to know how to fix or trouble shoot a problem.”
Eichhorn also contends that cranes are safer today than ever before, especially with computer controlled operator aids that shut down the crane when unsafe operations are sensed. “Ten years ago these aids were optional on a crane,” he says, “but now they are standard items. They contribute to safety, no question.”
Terex operates large-scale training facilities in Iowa and North Carolina, where it offers advanced training, including training in simulators. With the delivery of each crane, Terex sends out a technician to teach the owner how to set up and run it.
“We are a very diversified company with our cranes made all over the world - France, US, Germany, Italy, Japan and Australia,” he says.“I specialize in training on the Demag line from Germany and the RT line made in the US. We have other instructors who do training on machines from other countries.”
Purchasing safety
Another aspect of safety and training involves the purchase of other equipment and accessories needed for crane, rigging and transport companies to do business. For instance, many rigging tools now on the market are directly related to job safety, which means the purchase of these products can no longer be left to chance, according to Dennis St. Germain, president of INI Slingmax.
“In the old days, when price was the only consideration, jobsite safety was more of a hope than an actuality,” he says, “But today safety takes precedence over any other issue.”
For instance, St. Germain points to the ASME B30.9-2003 American National Standard titled “slings,” which outlines specific safety requirements and states that sling users should be trained in the selection, inspection, cautions to personnel, effects of environment, and rigging practices. For this reason, a company needs to select suppliers who will help them insure all these standards are being met, St. Germain says.
“Ideally, a qualified rigging gear supplier can provide its customers with the information needed to be in compliance with B30.9-2003 standards, keep them abreast of advances in rigging gear and to educate employees on the safe use of this equipment,” says St. Germain. “Service after the sale also adds value to the end user, especially when it comes to assuring that a job will not be held up waiting for rigging gear.”
St. Germain says a quality supplier should also offer inspection and training services. “In-plant and on-site inspection by a trained and trusted supplier shares the burden with the user, and also helps maintain a foundation of safety,” he explains.
STAY CONNECTED
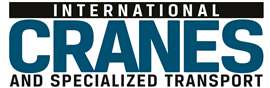
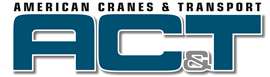
Receive the information you need when you need it through our world-leading magazines, newsletters and daily briefings.
CONNECT WITH THE TEAM
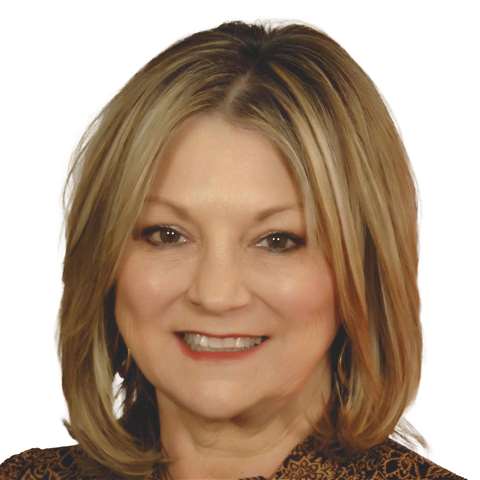
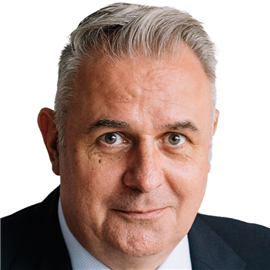
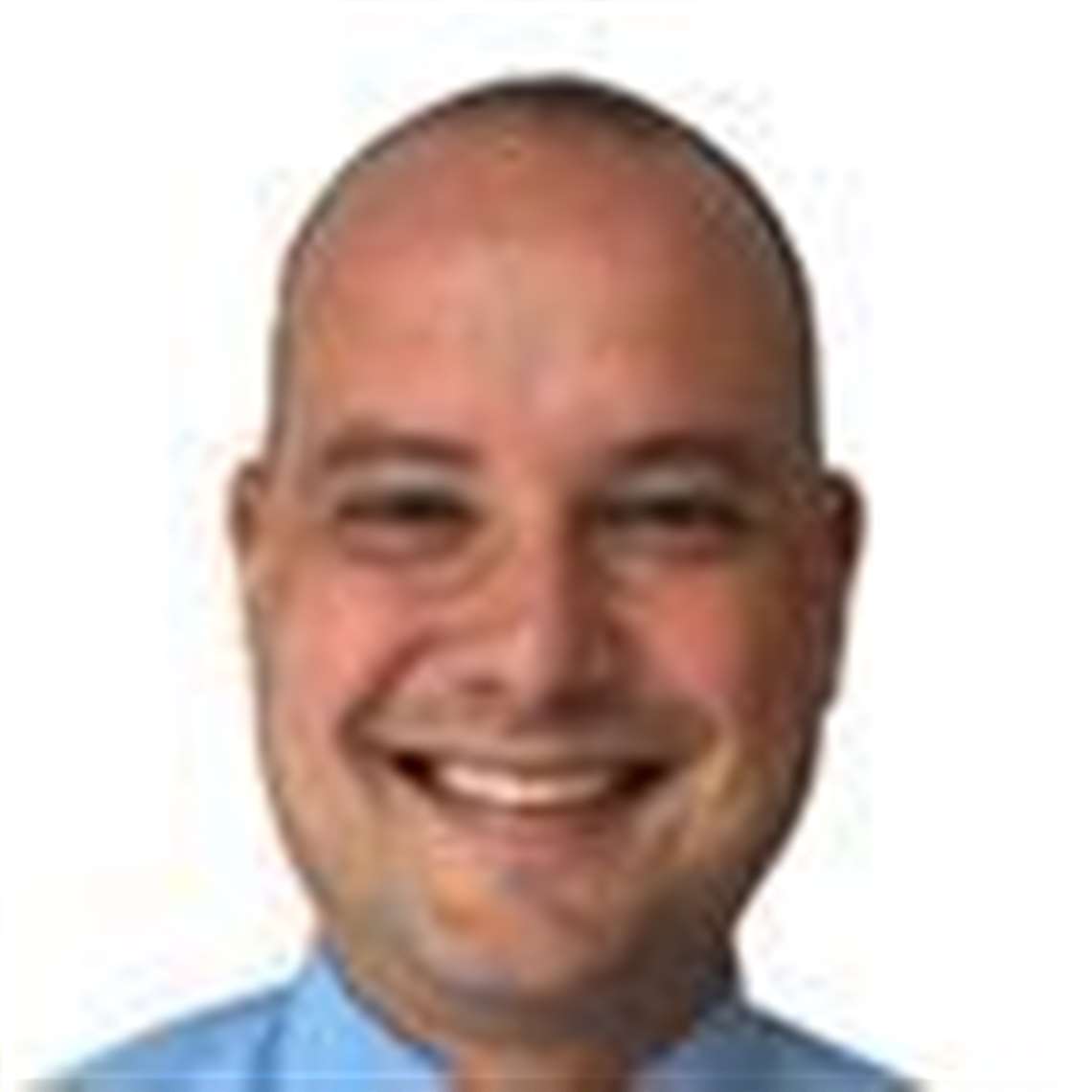
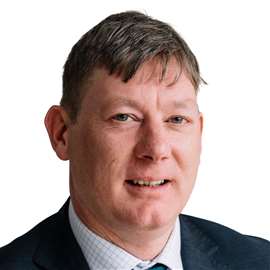