Hands-on training pays off for Hydra-Slide customers
04 January 2018
Hydra-Slide offers hands-on instruction on every piece of equipment the company designs and manufactures.
Lower Colorado River Authority (LCRA) is a Texas-based electric utility specializing in electric substations and power transmission lines. Andy Cooper, safety and training manager at LCRA, along with his crew, recently received training on the LCRA’s new XLP150 skidding system and Hydra-Pac Synchronous power unit. This training included jacking and sliding a real transformer to test the entire system.
“If you don’t operate equipment as designed and intended, you can have negative results and potentially get someone hurt,” Cooper said. “The training ensures all the right steps are taken and understood. I would rate the technical training very highly. The Q&A and step-by-step instruction was perfect. Having a rep onsite during a move (albeit a practice move) was invaluable.”
An important step before the training is getting people comfortable working with the equipment.
Lower Colorado River Authority’s riggers are immersed in training on a Hydra-Slide XLP150 skidding system, moving a transformer in the yard.
“Sometimes I am on-site for the first project where the new Hydra-Slide systems are being used, and sometimes we do a dry-run in the client’s yard just to get them familiar with the set-up and operation of their equipment,” said Robert Young, director of operations and lead trainer at Hydra-Slide.
While hands-on training with the equipment is an ideal scenario, though it isn’t always possible.
“We are developing an online video training program now so that our clients can have remote access to practical, step by step instruction,” Young said. “It’s going to be very valuable for training new personnel or refreshing the crew’s knowledge before a project. Both on-site and video training focus on operation and troubleshooting. We know in the real-world things don’t always go perfectly. For example, hydraulic hoses get connected backwards, or skid tracks aren’t set up completely parallel. We want our clients to feel prepared to safely handle these situations.”
Janine Smith, vice president of Hydra-Slide, said that 2017 was a big year for on-site training as the company performed training at facilities in the United States, Canada, Singapore and Qatar. While the scope of the training does not cover how to execute the job or comment on the client’s rigging plan, when the client fully understands how the equipment functions and how it is intended to be setup and operated, they are much more confident and better prepared to safely and successfully complete their tasks.
“We encourage all of our customers to read and fully understand the operating manuals that come with the equipment, as well as ask any questions that they have about the intended applications, limitations or use of their Hydra-Slide systems,” said Smith. “The goal is that everyone is confident and prepared to operate these systems, and we will provide whatever level of after-sales support is requested.”
STAY CONNECTED
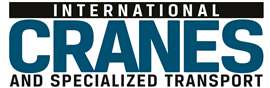
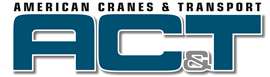
Receive the information you need when you need it through our world-leading magazines, newsletters and daily briefings.
CONNECT WITH THE TEAM
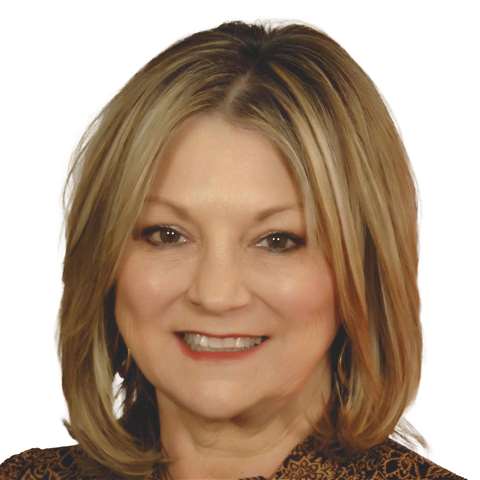
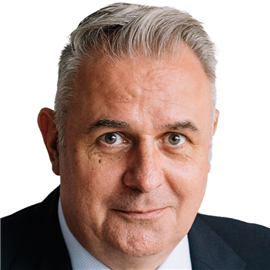
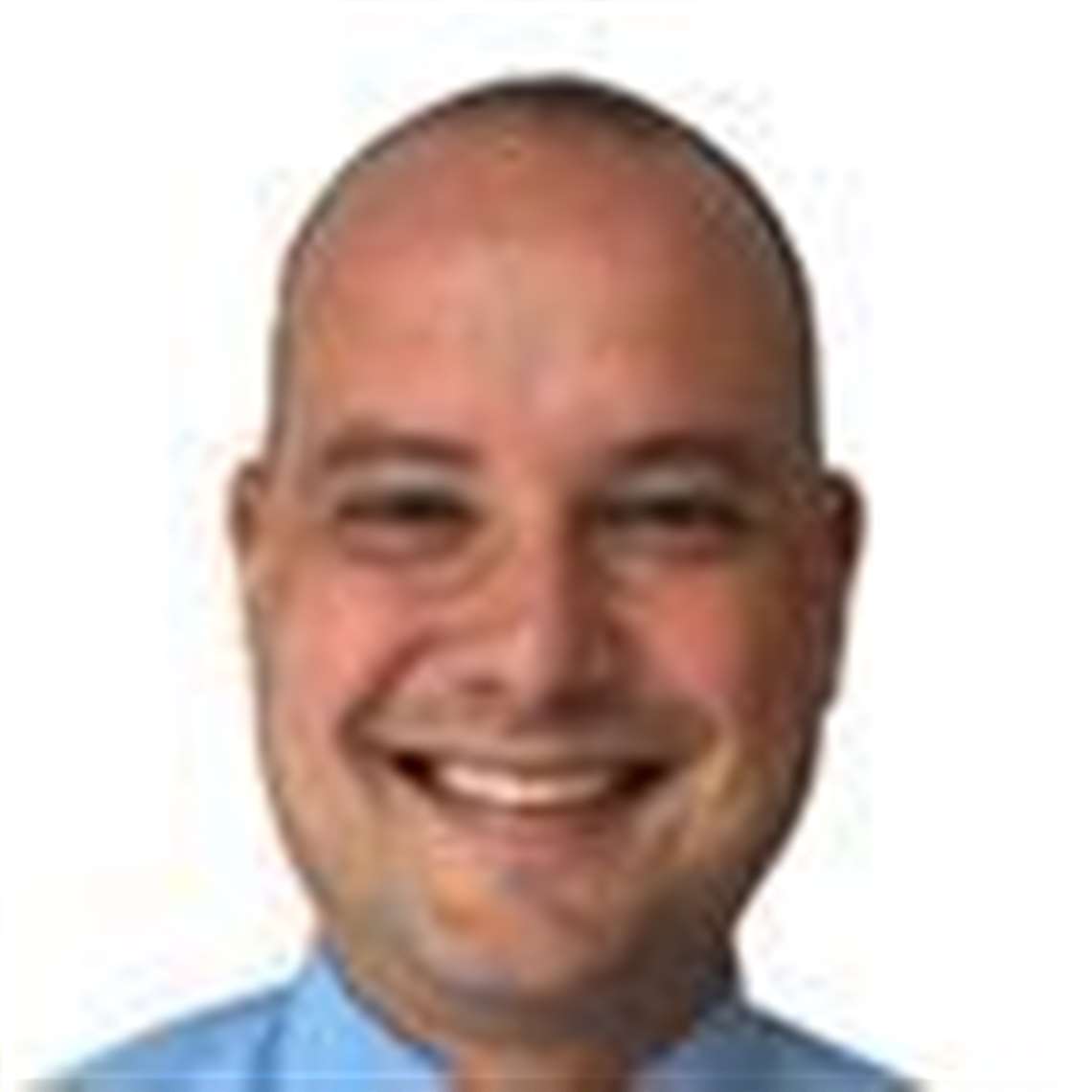
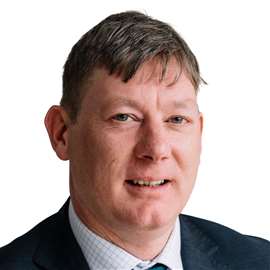