How crane size is increasing to support the evolving wind energy market
26 January 2022
The wind energy market is growing, and so is the equipment. With sizes increasing, new challenges have to be overcome to transport and install these massive monoliths of green energy. Niamh Marriott reports
The wind transportation market is changing and developing, as the technology itself ever-advances and grows. For the transport side, Frank DeVries, general manager at Pinnacle Logistics Solutions, says, “In addition to the conventional wind transport equipment, including schnables, half-schnables, extendable blade trailers, etc. we are currently developing blade-dolly systems for the longer and heavier blades we are starting to see in the market.
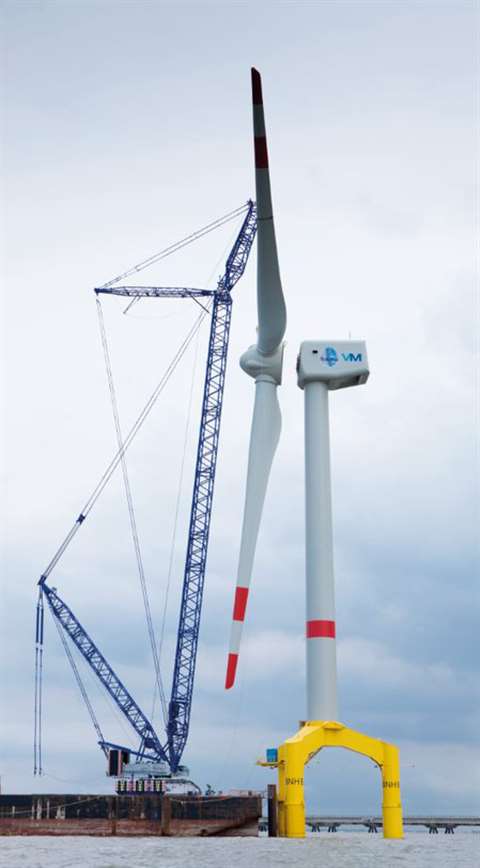
“With the increased size and weights, conventional extendable trailers may not be able to scale legally from an axle weight perspective, particularly in western Canada,” DeVries continues. “We currently have three sets on the ground, with others in development in both bunk mounted configurations, and schnable configurations for the root ends.”
The increased size of turbines is becoming almost unmanageable on regular roads. DeVries says, “Component size has always been a concern in the wind industry. Blade lengths are now reaching levels to where conventional equipment no longer has the ability to legally transport blades in many jurisdictions.”
Turbine crane size increases
Crane manufacturer Tadano also notes that turbine size is increasing massively. A spokesperson says, “The height of the turbines is definitely increasing. In Northern Europe, we can see turbines with a total height (tower and blade) of 300 metres.”
To deal with this, Tadano now has a range of cranes to lift and install, both crawlers and all terrain models. Its lattice boom crawler cranes are used extensively in this industry, with its CC 38.650-1, PC 38.650-1, CC 68.1250-1 being used mainly for erecting wind turbines in the field. Tadano says its CC 68.1250-1 and CC 88.1600-1 cranes are ideal for erecting larger wind turbines near-shore and offshore.
Tadano says all terrain cranes have their place in the wind energy market too. “Depending on the size of wind turbines, the AC 8.500-1 and AC 9.700-1 all terrain cranes can erect turbines. Repowering and maintenance are applications where larger all terrain cranes are used. Our new AC 7.450-1 all-terrain crane with its 80 metre boom and a lifting capacity of 37.9 tonnes on fully telescoped main boom with SSL will be ideally suited for this type of work.”
There’s more development coming. Tadano says, “We are working on new solutions that we want to introduce at bauma (October 2022), which will be perfectly tailored for wind turbines of 180 metres and higher.”
Equipment end user Mammoet also sees the trend of greater heights, beyond the reach of crawler cranes. It has introduced its own lifting system the wind turbine assembly (WTA) crane, which the company says allows theoretically infinite hub heights.
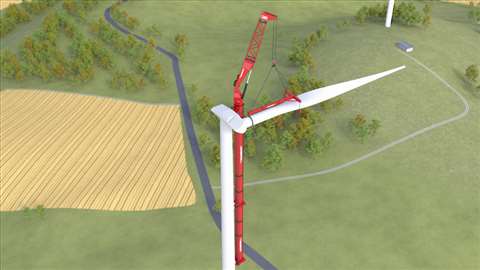
WTA assembles wind turbine generators by attaching directly to the tower itself, using a series of clamps to self-assemble and then climb to each lift location. It assembles tower sections, hubs and nacelles, and has a capacity of 150 tonnes. Maximum wind speed is 20 metres per second which reduces downtime during construction and extends the build season.
Mammoet says that with no boom laydown requirement, far fewer components and a lower total weight, the WTA is also faster to move from one pad to another. The system’s small size also means quicker and more cost-effective mobilisation. The company says while a conventional crawler crane can require up to 50 truck loads to reach site, the WTA uses just nine.
What are the obstacles for offshore crane instillation?
Precision is key when it comes to the installation of offshore wind farm equipment. Enerpac’s hydraulic levelling and fixation systems are being used by Smulders and T&I contractor Deme Offshore for the installation of 80 units of the GE Haliade 150-6 megawatt turbines at the Saint-Nazaire offshore wind project in the Loire-Atlantique region of coastal France. The Enerpac system is being used to provide accurate levelling and fixing of the transition pieces on their monopile foundations.
Grouted connections are widely used in offshore wind turbine construction to transfer multiple loads from the transition piece fitted on top of the monopile. The transition piece is first lowered onto the monopile and levelled. It is then grouted into position to fix the transition piece to the monopile. Levelling is important to ensure the turbine will generate maximum yield.
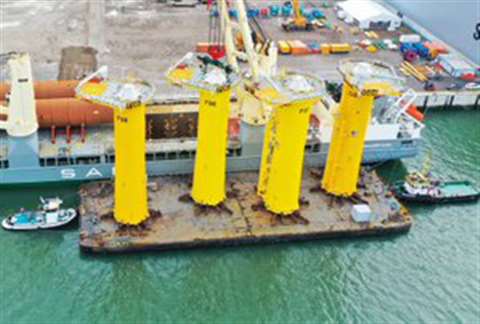
The levelling uses twelve pre-installed Enerpac 150 tonne capacity aluminium hydraulic cylinders inside the TP such that the cylinders rest on the MP. By adjusting the spring return cylinders, precise levelling of the TP is achieved, even if the MP was not completely level in the first place. Once levelled, the 25 tonne steel fixing cylinders positioned subsea at the bottom of the TP are activated to hold the TP in position during completion of the grouting process.
The subsea fixing cylinders have a reinforced return spring that eliminates the risk of point load and contact corrosion with the monopile.
“Enerpac cylinders are a robust and proven solution for the levelling and fixation of TPs,” says Patrick Frencken, key account manager for North West Europe at Enerpac. “We delivered the cylinders and hoses to Smulders in Belgium where the TPs were being assembled ready for installation. Deme Offshore then transported the TPs by barge to the project site in France.”
As demand for greener and cleaner energy grows, the wind energy industry and its enormous components are set to grow exponentially too.
Estonian Island InstallSarens recently deployed a 500 tonne capacity Liebherr crane to help client Five Wind Energy lift and install several Siemens wind turbine components on the Estonian island of Saaremaa. Sarens transported all the crane components, including ballast, superlift, and fly jib, to the job site on twelve trucks. It then took one day to set up the Liebherr LTM 1500 8.1 wheeled mobile telescopic crane with 105 tonnes of counterweight in TAY3S configuration. An auxiliary crane, the Liebherr LTM 1070 with 70 tonnes of counterweight, was also used. Over the course of a week, Sarens lifted the wind turbine components, including the 40 tonne gearbox and main shaft, as well as the 54 tonne rotor and blades. Once erected, the wind turbine tower, with rotor, reached a height of 70 metres. While weather conditions were frequently changing, Sarens was able to complete the job over the course of several windless days. |
STAY CONNECTED
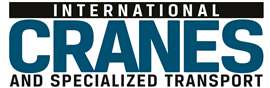
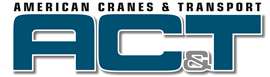
Receive the information you need when you need it through our world-leading magazines, newsletters and daily briefings.
CONNECT WITH THE TEAM
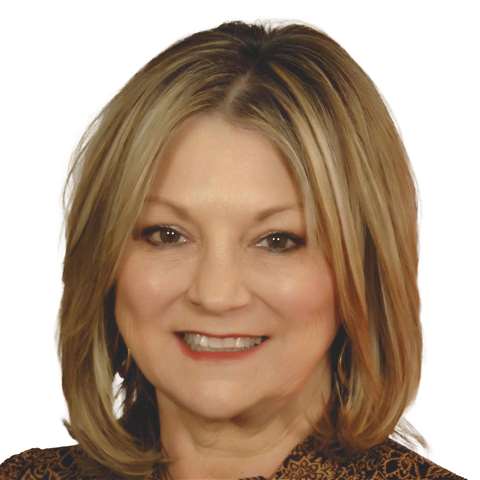
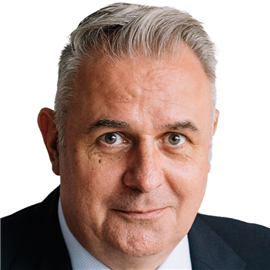
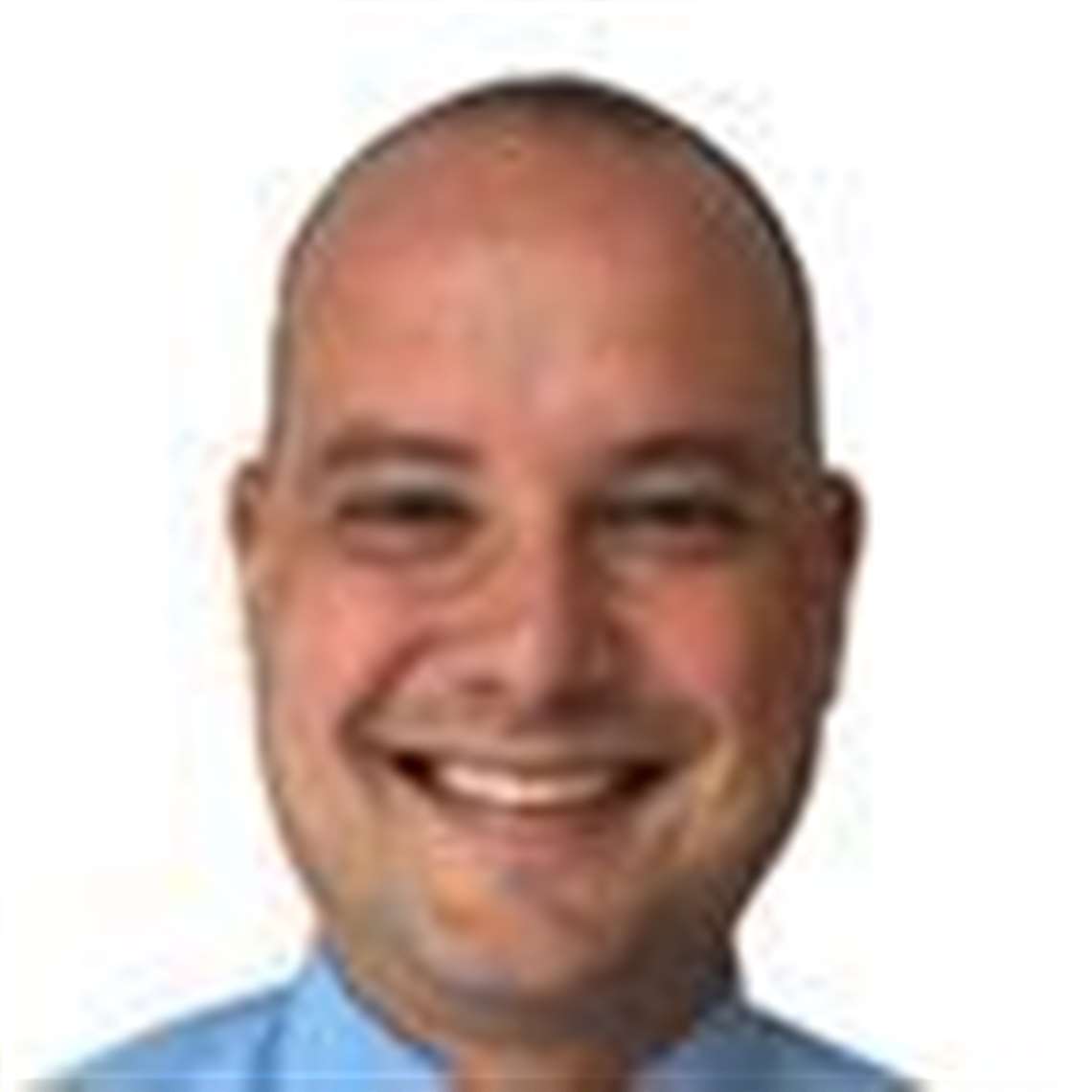
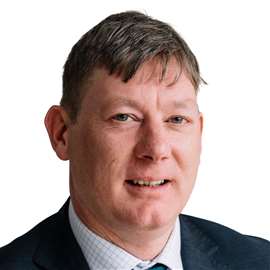