How did Saudi Aramco tackle a flare tip removal project?
31 May 2022
As a giant producer of oil and gas, Saudi Aramco constantly performs critical lifts. Height was a particular challenge on this flare tip removal project. Zubair Ur Rehman Ansari reports for International Cranes and Specialized Transport.
Saudi Aramco performs massive critical lifting operations as part of its activities to maintain the reliability of its facility processing equipment. One of these particularly challenging lifts is the removal of flare tip assemblies, in this case performed in the flare area of the company’s Khursaniyah Gas Plant in Saudi Arabia.
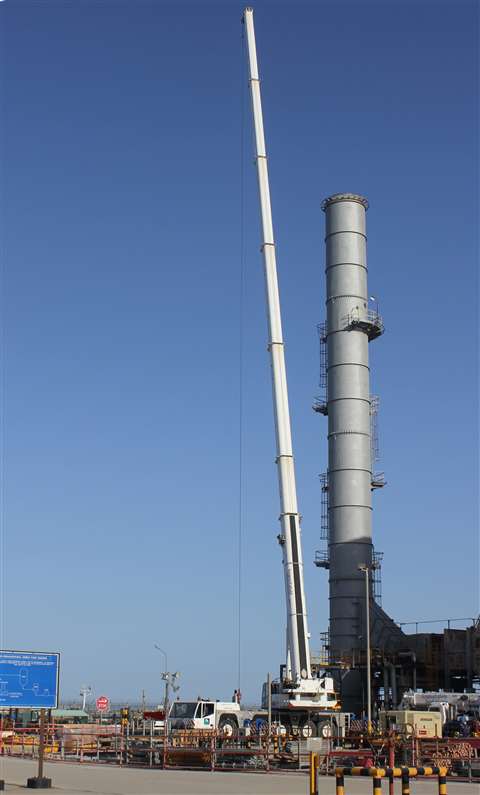
Flare systems are an important piece of equipment for hydrocarbon plants. Multiple flares are typically installed to allow one flare to be taken offline for maintenance without shutting down the entire facility. The whole maintenance period needs to be as short as possible so the flare can be returned to service and keep the contingency of the production system.
Regular and effective inspection of the flare is vital to ensure the safety and compliance of the facility.
Improvements in the photography and video capabilities of remote-controlled drones has helped with infrared sensing features used for in-service inspections. There are, however, still areas of the flare system that cannot be inspected until the flare is out of service.
Components such as the flare system knockout drum, molecular seal, and liquid seal drum, must be internally inspected while the flare system is out of service and cleared. The steam and air tubes, and the knockout and liquid seal drums need to be examined for any weld failures, fouling, and internal corrosion issues.
Gas plant inspection and maintenance
The Transportation and Equipment Service Department is the entity responsible to provide lifting services at Saudi Aramco. It has a long history of supporting plant inspection and maintenance activities for the flare system through lifting personnel baskets and transferring workers and carrying out inspections over the platform. It also performs the final removal of the flare tip for out-of-service inspections and maintenance activities.
Saudi Aramco has developed and implemented crane operations general instructions for controlling the critical lifting activities and required certification levels for the crane operator and riggers to safely perform the critical lifting activities inside hydrocarbon areas. Special emphasis is given to activities involving lifting of crane-suspended personnel platforms (man baskets), such as derating of crane capacity to 50 per cent and reduction in the allowable wind speed to 25 km/h.
The flare system inspection and removal at the Khursaniyah Gas Plant was conducted using a 350 tonne capacity Terex AC 350 wheeled mobile telescopic crane. The weight of the flare tip assembly was around 5 tonnes and the working radius was 22 metres. A requirement to operate at high elevation saw the main boom set at 56 metres, plus a 37.50 metre fixed jib and 32 tonnes of counter weight.
Transferring workers to an elevated platform and a long radius made this lifting activity critical. It requires large cranes working with full or partial auxiliary attachments.
Crane operator and rigger communications
In addition to working at high altitude and having to deal with a large load, there are further challenges, including the need for radio communication channels between crane operator and rigger, high wind speed in the open and exposed flare area and finally, controlling the slewing and orientation of the basket via taglines held by assisting riggers on the ground.
Before crane mobilisation and erection at site, the ground conditions are inspected for ground bearing pressure values and overall ground levelling by Saudi Aramco certified Rigger-I, along with a heavy lift engineer, as well as plant and site access to bring this heavy lift crane is also studied by the team. Continuous close monitoring of the wind speed for a suitable window to perform the lifting operation is carried out by the team.
During the man basket lifting, the rigger in charge stays inside the basket along with the other workers to ensure required basket position as per the work requirement. The rigger is also responsible for attaching the rigging hardware to the flare tip for its removal and re-installation.
This job requires an initial work permit, a critical lift plan form, plus the crane suspended personnel platform permit, all to be initiated and approved by relevant authorities. This is to ensure a safe and smooth operation to execute the assigned task.
Specific rigging hardware, including slings and shackles, were used. A through visual inspection was conducted before use of the rigging hardware by the rigger.
An effective job plan and adherence to all Saudi Aramco standards and general instructions while performing the lifting activity ensured this job was completed successfully. Saudi Aramco performs numerous similar lifting activities in its various plant flare systems. Typically, these activities are planned during scheduled T&I operations.
About the author
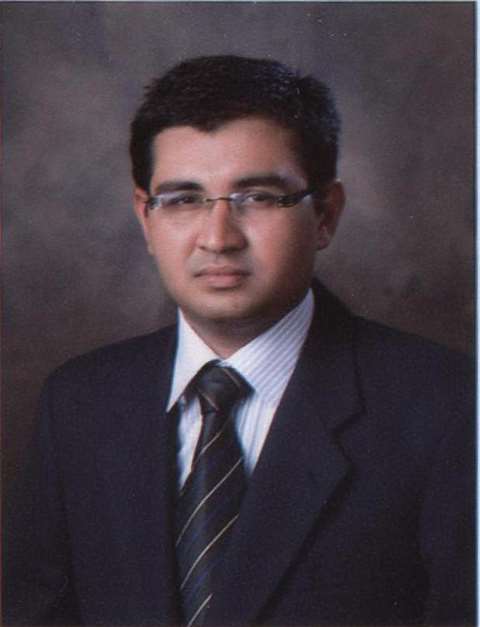
Zubair Ur Rehman Ansari has worked in the field of crane and heavy equipment operations for more than ten years.
He is employed by Saudi Aramco as a heavy lift engineer. Ansari’s experience focuses on managing heavy lift technical activities related to crane and heavy operations.
STAY CONNECTED
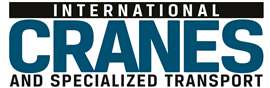
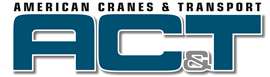
Receive the information you need when you need it through our world-leading magazines, newsletters and daily briefings.
CONNECT WITH THE TEAM
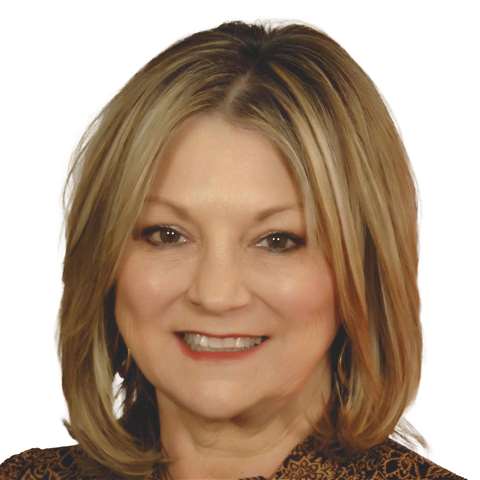
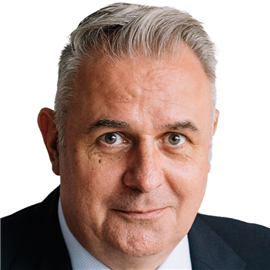
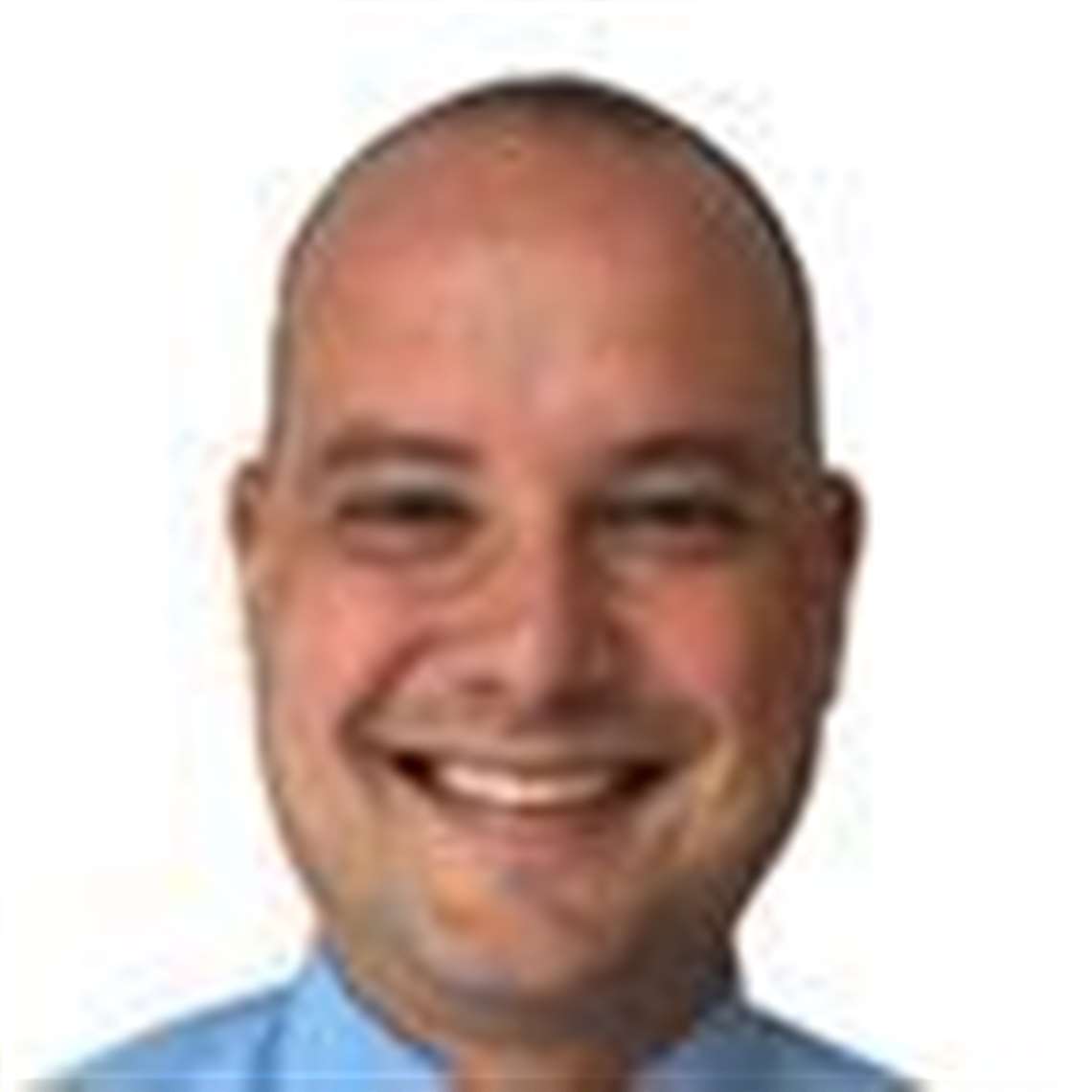
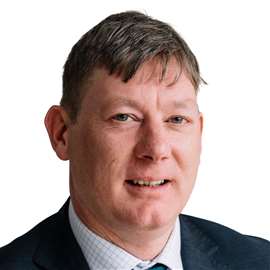