How specialized transport vehicles are driving green change
28 August 2023
With new technologies and electric options, specialized transport vehicles are paving the way to a sustainable, fossil fuel free future with more heavy loads on the move. Niamh Marriott reports.
The global energy transition to greener and more environmentally friendly fuel sources is being realised in the specialized transport sector, as well as the wider construction industry. Companies and governments are now considering how to supply sites with building materials and components in a green and clean way, and are actively looking at ways to lower carbon dioxide emissions.
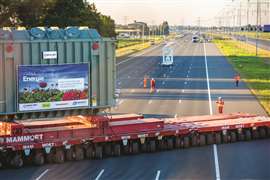
High goals and ambitions have been set by governments globally to reduce the dependence on traditional fossil fuels for transport. Though the charging infrastructure remains an issue worldwide for consumer transport, specialized transport vehicles are going electric.
Electric trailers
International heavy lifting and transport specialist Mammoet has launched a zero-emission electric power pack unit (EPPU), suitable for use with any of the company’s self propelled modular transporter (SPMT).
Mammoet is converting its existing SPMT power pack units (PPUs), replacing the diesel engine inside with an electric alternative. Once retrofitted, each trailer combination has comparable power to existing industry standard units, Mammoet says.
The PPU vastly reduces noise levels at project sites too, resulting in a safer and more productive work environment. The company says communication between staff is clearer, while at locations where sound restrictions are in place longer operational windows are now possible.
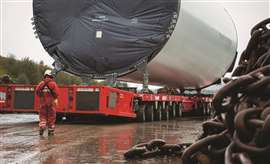
Mammoet says its new electric system represents another step towards zero emission on site, eliminating the carbon footprint of SPMT transport entirely.
All the electric batteries fit inside the existing PPU envelope and Mammoet is optimising the design to even make the units smaller. A 44 kW onboard charger is also installed within the original PPU frame.
Mammoet says AC charging takes 5 hours from empty to full but charging time can be reduced to 2 hours by using its unique “recharging“ technique using hydro-electric converting.
Dependent on usage, the Power Pack Units will last for 4 to 5 days before recharging is required.
A spokesperson for the company says the electric option “allows our customers to meet increasingly strict environmental legislation more easily, reducing the impact of transport phases on surrounding communities and infrastructure.
Retrofitting the fleet
“It also demonstrates Mammoet’s strong commitment to the energy transition, and to its own sustainability. Retro-fitting existing SPMT fleets cuts down on both waste and additional fabrication, compared to sourcing new zero emission equipment.”
There is government support available and state financing is helping innovation of new technologies.
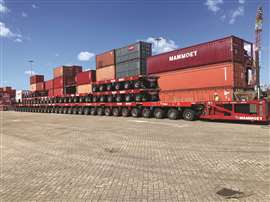
Mammoet’s solution was part-financed by the DKTI, a Dutch government programme to develop climate technologies and innovations in logistics. Mammoet also worked with a provider of zero-emissions powertrains for heavy industry to bring the electric power pack solution to market.
When asked about the difference between this latest development from the previously announced ePPU developed with Scheuerle, Mammoet says it has chosen to explore retrofitting its equipment which “turns out to work very well for us. This is different from developing a new ePPU, as Scheuerle does. Both developments are needed to meet the emission requirements for the future,” the spokesperson adds.
Moving without cranes
SPMTs continue to offer innovative transport options and can even remove the need for cranes.
Tunnelling system specialist Herrenknecht is using SPMT to transport its equipment without needing cranes to load and unload it.
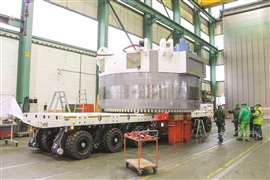
A new Eco1000 SPMT from Cometto has joined the fleet to carry out in-plant transport of individual parts for tunnel boring machines. It is a 6 axle vehicle that is driven under the load, lifted and then, after it has moved the load to its new location, lowers the load and drives out from underneath it. In doing so it makes full use of the transporter’s 700 mm suspension stroke.
Stephan Göggel, technical manager of the component factory at Herrenknecht, says, “With the Eco1000 we are ideally equipped for the in-plant movement of individual components weighing up to 200 tonnes for our tunnel boring machines.
“The payload of 260 tonnes, coupled with the fully electronic steering, speaks for itself. It allows the concept of transport without cranes to be implemented perfectly,” Göggel continues.
To help with running the transporter a remote maintenance system is incorporated into the control cabinet on the Cometto power pack. Operating parameters can be retrieved “over the air” at any time and allow Cometto to offer customer support in the event of a malfunction.
Historical moves
Spedition Kübler transported a 50 meter long U17 submarine weighing almost 500 tonnes on 30 Tii Scheurle InterCombi axle lines on public roads in Germany from the harbour at Speyer to the Technik Museum 4 kilometres away.
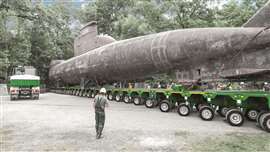
In combination with a tractor unit and a pusher machine, the complete vehicle combination had a length of almost 70 metres. At times, additional towing and pushing vehicles were required to protect the road surface from the immense traction so that the actual vehicle combination grew to around 90 metres.
Due to the low platform height of 1.2 metres in the driving position and the wide support base, the axle lines are also suitable for loads with high centres of gravity. As in the case of the U17 transport, InterCombi vehicle combinations are not only used as trailer combinations but also as tractor-trailer combinations or as self-propelled transporters.
Frieder Saam, professional driver and transport manager at Michelfeld-Erlin-based Spedition Kübler, explains, “It´s always very pleasing when the load has reached its destination without being damaged. After all, five years of planning went into this special transport.”
The submarine was being moved for restoration.
European demand
The demand for SPMT has been rising steadily since its invention four decades ago and continues to be particularly popular in Europe.
Portuguese transport company Laso has expanded its Italian operations with a new office in Milan. The company already has a branch office in Florence and is present in more than ten countries, predominantly in European countries such as Spain, France and Germany.
Wildeshausen, Germany-based construction machinery supplier Hüffermann has recently taken delivery of a turntable set for its Cometto SPMT axle lines.
Commenting on this new investment, Rocco Schimmel, plant manager at Eisele AG Crane and Engineering Group, says, “This means we are ideally set up for driving components weighing up to 450 tonnes in an open compound around the tightest bends.”
“These turntables can be assembled both as a 2-file combination or as a 4-file combination”, adds Cometto sales manager Joachim Kolb. “For this, the load distribution plate is simply turned 90 degrees.”
Turbine transport
Elsewhere in Europe, Italy-based wind turbine transport specialist Societa Autotrasporti Eccezionali (SAE) opted for two new 6-axle MegaMax lowbeds from Faymonville.
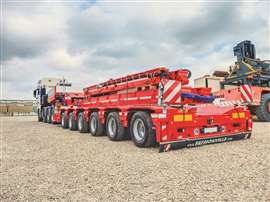
Wind turbine transport is tricky and requires specialized transport to get the huge components, blades and nacelles to a wind farm, either onshore or offshore.
The new lowbeds will allow SAE to transport heavy tower sections of wind turbines in a height-optimised way, the company says.
These trailers with their telescopic and hydraulically widening beams are specifically designed for wind turbine transport work.
The basic length lower deck is 8,950 mm with an additional extension of 5,500 mm. Thanks to the use of cranked axles, a minimum loading height of only 765 mm on top of the bogie can be achieved in driving position.
This allows to load towers over the full trailer length, usually with their bigger diameter in the lower part.
The company has worked with Faymonville for several years and its fleet includes quadruple extendable WingMax trailers, which are used to transport XXL rotor blades.
New transport options are ensuring that industry demands for moving heavy loads are met, and in an increasingly sustainable way.
18,000 tonnes moved on SPMT
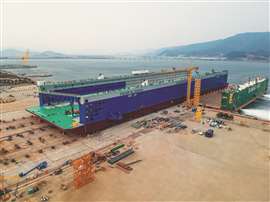
An 18,000 tonne dock module, 62 metres wide and standing more than 20 metres tall, is an undeniably impressive sight in its own right. Even more spectacular was when that colossus started to move, borne on 380 axle lines of self propelled modular transporter (SPMT).
It was a load out project in South Korea at SangSangIn Ship Machinery in GwangYang port. After much preparation work the 260 metre-long module was moved just 300 metres in the first part of its journey, loading out onto a barge for the journey by sea to Egypt.
Standing at 22.5 metres tall the module was carried on 380 modular axle lines of Cometto MSPE type SPMT. It was a combined fleet of axle line modules from three local heavy load companies: Anjeon, DaeMyung and Global.
“The three companies have sent their SPMT fleets to the site to master the challenge. A total of 380 modular axle lines of Cometto MSPE has been assembled, composed by sixty-two 6-axle units two 4-axle units,” says Alberto Di Stefano, Cometto sales manager.
The SPMT was arranged in 12 independent vehicles, each one driven by a 335 kW power pack unit. Four areas were supported under each corner of the dock, Cometto said. With the SPMT driven under the load the position of the supports was adjusted slightly before the load out was then completed.
“Such projects are realisable thanks to the payload capacity of the Cometto MSPE which reaches a value of up to 70 tonnes per axle line – the highest amount on the market. Additionally, the patented Cometto Dual-Link suspension offers an optimised force repartition in the suspension structure. The axle geometry gives the highest possible precision during the load positioning,“ Di Stefano continues.
The floating dock is for the Suez Canal Authority of Egypt. It can lift vessels weighing as much as 35,000 tonnes. The cost was around €64 million. Manufacturing started in May 2022 and less than a year later it was finished and ready to go.
Transformers transported to India
Pakistan-based shipping and logistics company Star Shipping has delivered two sets of 40 MVA transformers and breakbulk accessories from Karachi in Pakistan to Punjab in India.
The cargo was received under hook in Karachi port and loaded onto multi-axle hydraulic trailers, which were used to safely deliver the transformers to their destination site in Punjab.
Star Shipping delivered the additional breakbulk accessories for this shipment using multiple flatbed trailers, with all shipments made successfully.
Star Shipping Pakistan is specialized in handling turnkey projects, heavy-lift transportation, erection, engineering services, sea freight and offshore services.
Shodesh transports nuclear plant
India-based Shodesh Shipping co-ordinated a large shipment weighing more than 2,000 tonnes for the development of the Rooppur Nuclear Power Plant in Bangladesh.
The power plant is being constructed on the banks of the Padma river, 140 km west of Dhaka.
“The vessel carried 2,066 tonne (2,092 packages) of bulk cargo for the continued construction of the plant,” said a spokesperson for the company.
Since the beginning of the construction of the nuclear power plant, the company has played a significant role as a freight forwarding and logistics agent for the project.
During March and April 2023, the company handled another shipment of cargo using the breakbulk vessel MV Dragonball, which arrived at Chittagong Seaport towards the end of March.
The consignee for this shipment was the Bangladesh Atomic Energy Commission, and Atomstroyexport JSC, the main contractor of the power plant.
Ramps relocates drilling equipment
Ramps Logistics collaborated with and supported the team at Touchstone Exploration with the relocation of their drilling equipment in Trinidad.
The equipment, which included compressors and separators, was essential for Touchstone’s onshore drilling activities.
Transportation was completed from their Forest Reserve facility in Fyzabad to the Cascadura site in Rio Claro.
Both teams’ great effort and attention to safety made this movement a success, a spokesperson for the company said, adding – “We are excited to continue to support Trinidad’s energy sector.”
Goldhofer moves locomotive in Mexico
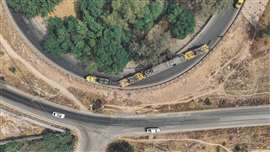
Mexico-based heavy haul company Pesado used a Goldhofer 12-axle THP/SL heavy-duty combination to transport a 180 tonne electric locomotive 2,250 kilometres from San Luis Potosi to Valladolid, Yucatan in Mexico.
The EMD GP-38-2 electric locomotive is 18 metres long and 4.7 metres high and will operate on the new Tren Maya railway.
The railway is part of a major infrastructure project involving the construction of a 1,500 kilometre railway line linking Mexico’s tourism destinations and Maya sites.
For the operation, Pesado chose the Goldhofer combination with a drop deck designed for a payload of up to 300 tonnes.
The drop deck was necessary because of the locomotive’s 4.7 metre overall height.
Thanks to the drop deck, it was possible to reach Valladolid, 2,250 km away, on direct route, mainly using federal highways.
The departure from the loading yard was the first test of the Pesado team’s capabilities with the 69 meter long combination. Power came from two 515 hp Western Star 6900XD 8x6 heavy-duty tractors, sometimes used in the push-pull mode.
With a 55° steering angle and +/-300 mm hydraulic axle stroke, no serious problems were caused by the tight spots on the route including roundabouts and junctions.
The 304 tonne rig, with an overall width of 3.3 metres and a total height of 5.06 metres, reached its destination in Valladolid, Yucatan in 14 days.
“It was a challenging journey through tourist areas with narrow roads and tight radii, but the precision steering available with Goldhofer’s THP/SL modules makes safe and accurate manoeuvring possible even under such conditions,” says Ramiro Muñoz Martinez, specialized transportation engineer at Pesado.
STAY CONNECTED
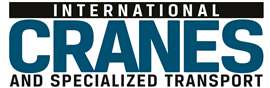
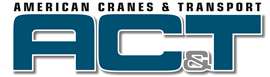
Receive the information you need when you need it through our world-leading magazines, newsletters and daily briefings.
CONNECT WITH THE TEAM
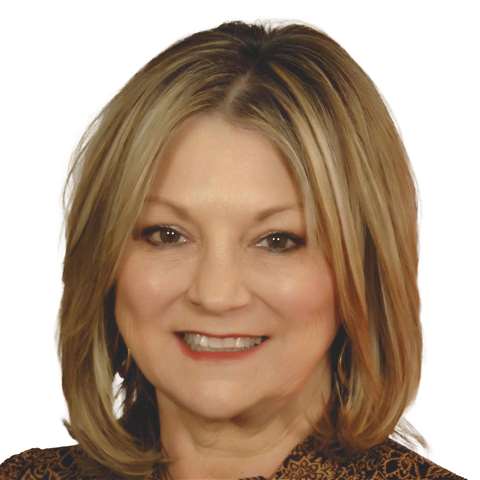
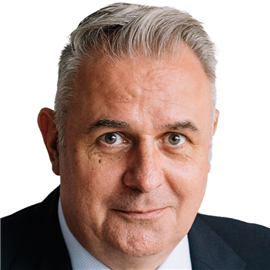
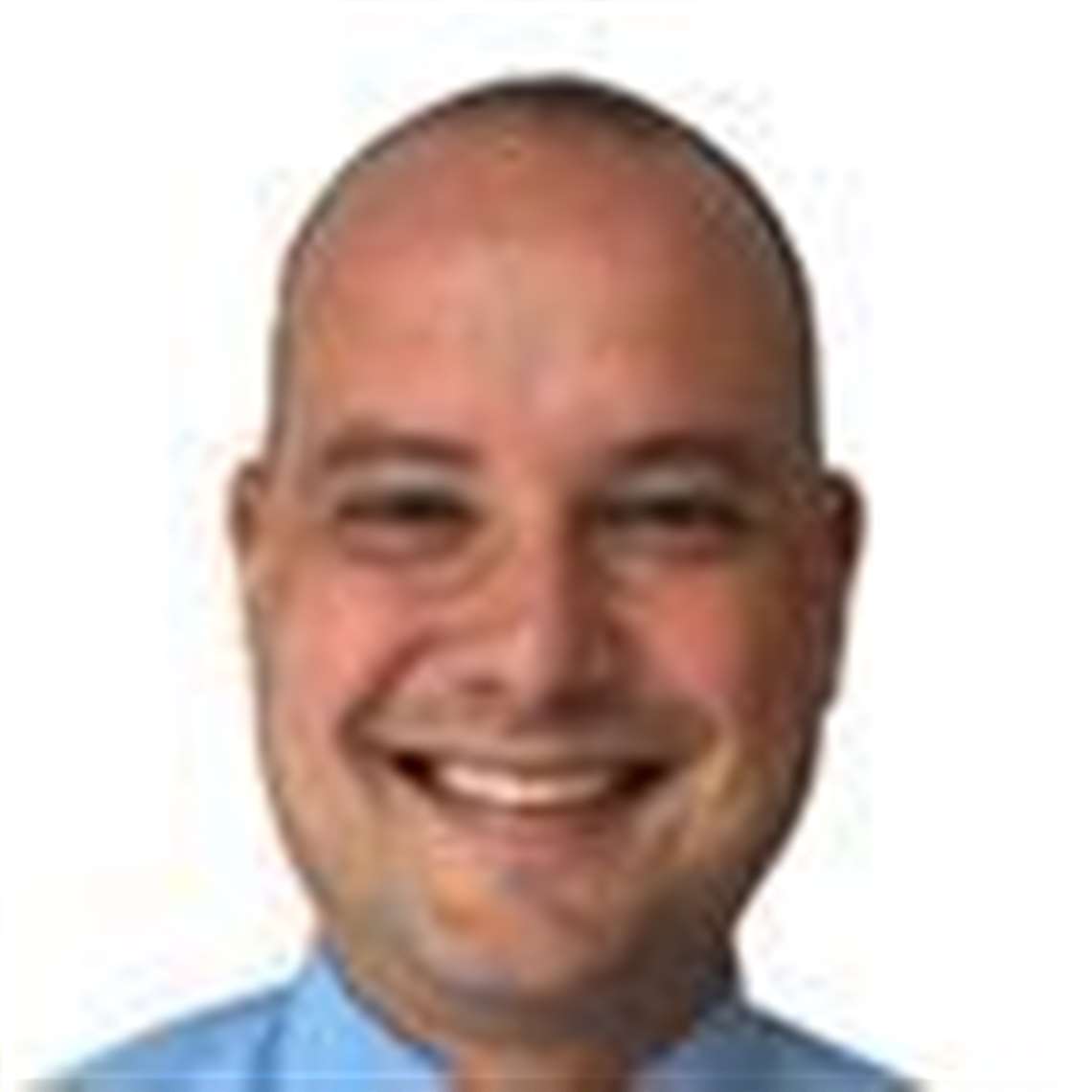
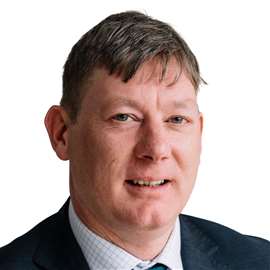