How the rope is pushing new boundaries to meet crane power
06 September 2021
Lifting safety starts with the rope and as cranes develop innovation is on the rise, writes Graham Anderson
A lattice boom crawler crane setting up wind turbines, a crane handling containers in port or an indoor crane in a paper factory have all at least one thing in common: the rope. Increasingly, in addition to steel wire rope, some or all of them on a crane might be made from synthetic fibre.
The rope has always been a critical crane component, and as cranes have become bigger and more powerful, companies are responding with investments in new products and technical innovation.
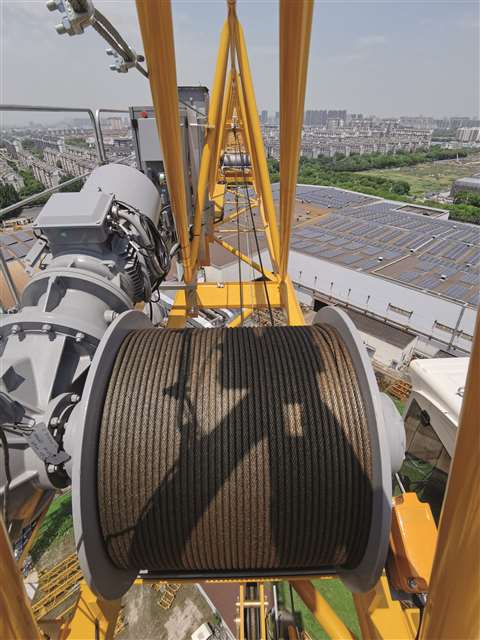
Two companies among those at the forefront of such thinking are German wire rope specialist Casar – part of WireCo WorldGroup, the global wire and synthetic rope manufacturer – and Konecranes, the Finland-headquartered crane manufacturer.
Casar has long invested heavily in research and development to acquire a comprehensive technical understanding of the behaviour of wire ropes in various applications.
Safety and innovation were also driving forces in Konecranes’ development of the Konecranes Rope Analysis, designed to provide expert consultation to answer customers’ wire rope and rope-reeving questions and has recently been introduced into Australia, New Zealand and Southeast Asia.
Casar says its ropes are designed and calculated in such a way that they show their discard status on the rope surface in good time, informing the operator when it is time to change the rope.
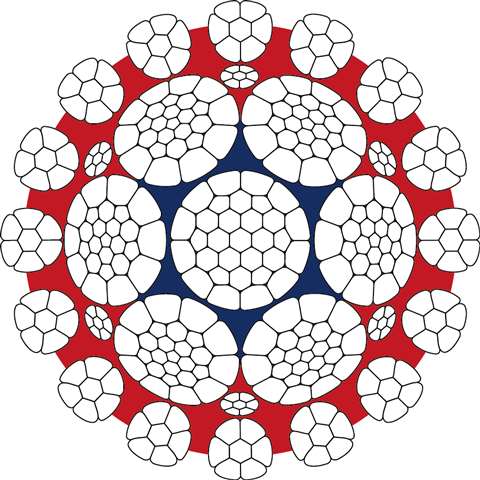
Its product testing machines help it understand how rope properties such as breaking strength, turning behaviour, efficiency, flexibility and diameter reduction under load are determined. This knowledge then flows directly into new product development.
Selecting the perfect rope for an application involves knowing exactly which requirements and wear mechanisms the rope will be exposed to. A heavy-duty application such as the installation of a wind turbine requires a hoist rope to be extremely stable in terms of rotation, the best possible winding behaviour with multi-layer winding and very high breaking forces.
In response, the company’s experts developed the Casar Doublefit, made from compressed strands and hammered twice. By compressing the strands and hammering both the heart rope and the slammed rope, a very round and smooth surface is obtained and, as a result, the required winding behaviour.
In contrast, the hoist rope on a factory crane in a paper mill requires a wear-resistant rope that moves flexibly over the multitude of rollers in the reeving. For this reason, Casar Superplast 10 Mix was created with 10 outer strands, a plastic-coated steel core and a parallel construction – that is to say, the lay length of all wires and strands are the same length and the linear contact points ensure optimal load distribution in the rope.
Wide load spectrum
This design leads to uniform wear behaviour over a wide load spectrum which opens up a large field of application options.
Also focused on efficiency and safety is Konecranes Rope Analysis which targets issues such as rope selection, rope life, component failures, unexpected rope behaviour, accident investigation and improvement opportunities, including recommendations on extending rope and component life.
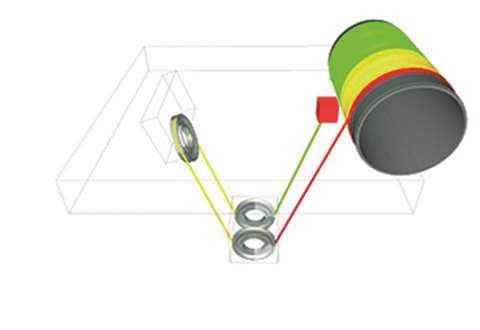
Using proprietary 3D modelling and calculation tools, Konecranes Rope Analysis provides an engineering assessment, calculation and inspection of ropes and reeving components.
Mark Beckwith, Australian service operations manager at Konecranes, said the rope analysis can improve the total lifecycle costs of equipment by optimising wire rope change intervals.
He said, “Using proprietary 3D modelling and calculation tools, we provide an engineering assessment, calculation and inspection of a company’s ropes and reeving components, based on the EN 13001-3-2:2014 standard.”
Tension, bending and abrasion
Beckwith explained that throughout the working life of a wire rope, the strands and core are subjected to tension, bending and abrasion, which can compromise its strength and safety.
“Routine maintenance often relies on predetermined replacement intervals regardless of the actual condition of the wire ropes, meaning that safe and operable ropes might be replaced too often or too soon, resulting in unnecessary downtime and increased costs.”
Konecranes’ consultations can provide a calculated estimate of rope life, recommendations for rope selection or rope reeving geometry improvement. They can also offer recommendations for extending rope life along with rope failure insights and investigations.
“It’s easy to see when a rope has broken or failed, but by that stage, the crane is already out of action, and there can be significant downtime as it is repaired. Rope Analysis can determine the exact state of a crane’s wire rope and reeving systems, including remaining design life, to provide an accurate recommendation of when it should be changed, to avoid any failures,” Beckwith added.
State of the art winches added to Mammoet fleet![]() Mammoet expanded its offshore services capacity earlier this year with the acquisition of Land & Marine’s linear winch equipment fleet - including two state-of-the art 800t capacity linear winches - from UK civil engineering contractor J Murphy & Sons for an undisclosed sum. Mammoet said the 800t capacity linear winches are unique to the industry. Their innovative design is patented and allows socket passing under load as well as utilizing advanced hydraulic controls for accurate monitoring. This results in reduced downtime and increased efficiency. The deal also adds several smaller linear winches - from 100t to 300t - and a range of drum winches to the Mammoet portfolio. The equipment will become part of Mammoet’s Offshore Services equipment fleet. |
GSR completes seabed mineral collector tech review![]()
Global Sea Mineral Resources (GSR), the deep-sea exploration division of international dredging specialist DEME Group, has completed two assessments of its seabed mineral collector technology, paving the way for an expedition in the Pacific Ocean. A new state-of-the-art umbilical and winch combination has been successfully evaluated mid-water in the Atlantic Ocean at a depth of 4,500m. In a separate exercise in Belgium’s Exclusive Economic Zone (EEZ) – the equipment demonstrated its ability to drive and manoeuvre along the seabed. GSR is collaborating with the European research project “Mining Impact” in which scientists will investigate the environmental effects of collecting mineral resources from the seafloor. |
MDL completes platform crane winch changeout![]() Maritime Developments Limited (MDL) completed the change out of a boom hoist winch for a North Sea Operator’s fixed platform crane after the client identified the winch replacement as the most efficient approach to safely extending the crane’s working life. The project was a result of a prior inspection and up-front survey by MDL’s in-house engineering team in which they modelled different scenarios to ensure continued safe operations on the client’s platform. |
MacGregor agrees SIA Solutions deal![]()
Maritime cargo and load handling specialists MacGregor - a subsidiary of Finnish corporation Cargotec - has secured an order from Texas-based engineering company SIA Solutions for 36 traction winch systems, 72 storage reel brakes and electrical control systems. The order is part of a project on the Mississippi River in the USA to prevent erosion and maintain the current waterway, as the river is a vital pathway for merchant vessels. The equipment is destined for the specialised concrete mat sinking unit, ARMOR 1, under construction at Thoma-Sea Marine Constructors in Houma, Louisiana, for the United States Army Corps of Engineers (USACE). The mat sinking unit is scheduled to start operating in the middle of 2022. MacGregor is part of a team comprising SIA Solutions, National Robotics Engineering Center (NREC), and Bristol Harbor Group, Inc. (BHGI). |
STAY CONNECTED
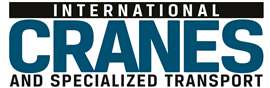
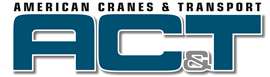
Receive the information you need when you need it through our world-leading magazines, newsletters and daily briefings.
CONNECT WITH THE TEAM
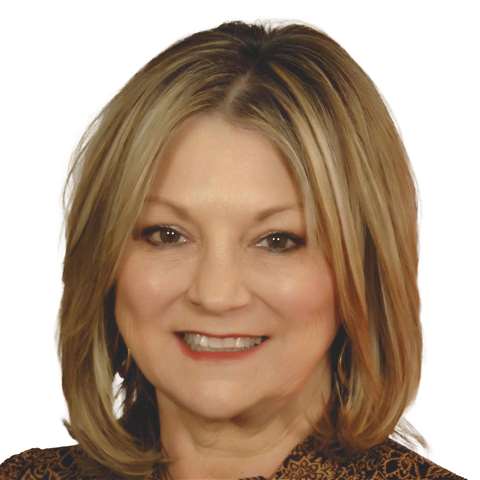
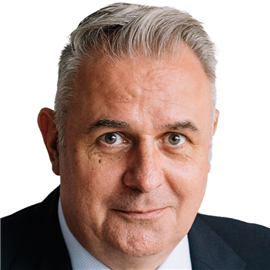
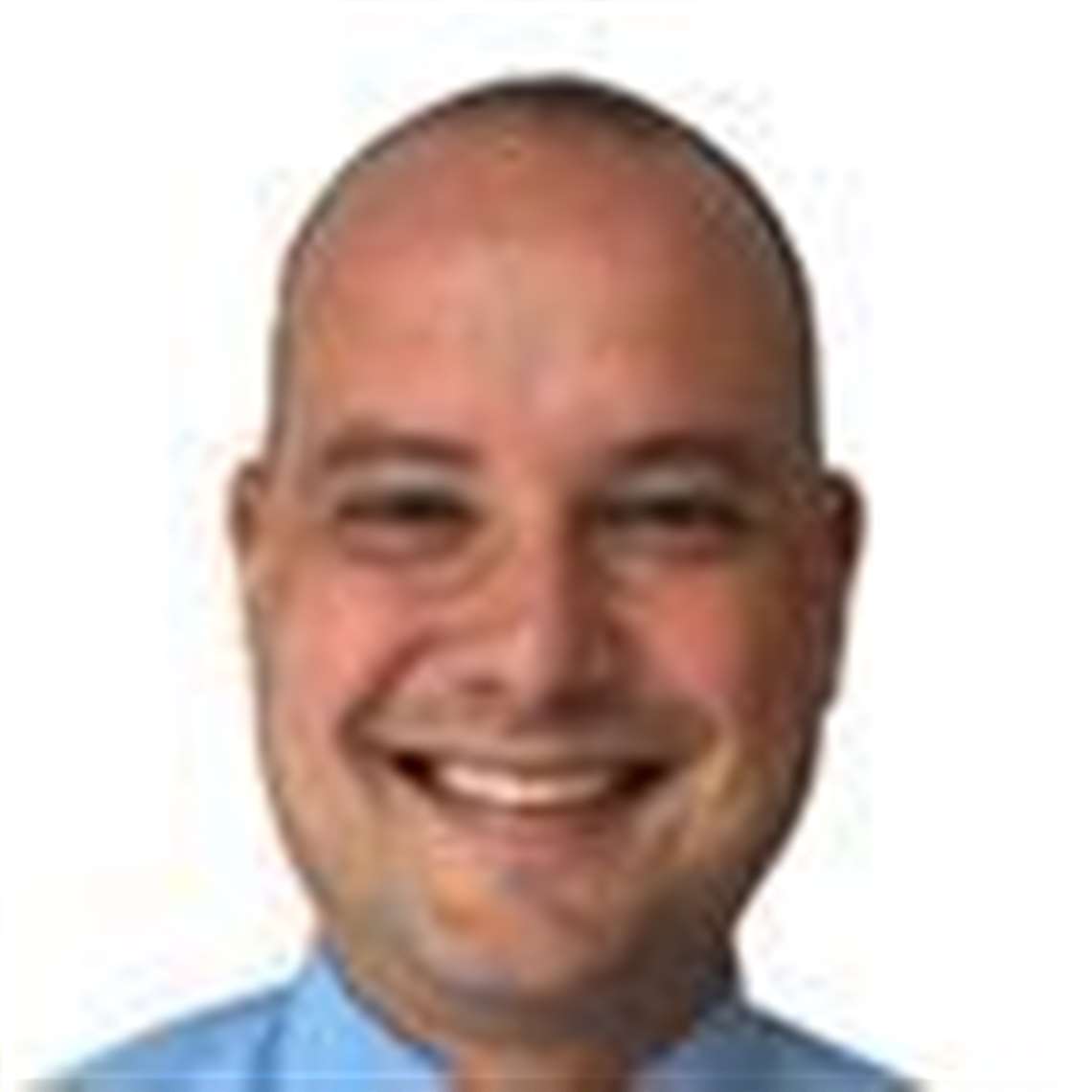
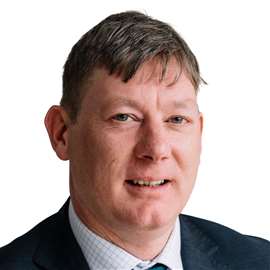