How you can decarbonise wind turbine construction
17 May 2023
Wind power, an industry seen as the poster child for a zero carbon future, continues to rely on outdated carbon guzzling technology for its installation. Lucy Barnard takes a look at the electric climbing cranes which could revolutionise wind farm construction
Rising up against the blue summer skies of Trøndelag, the Roan onshore wind farm in central Norway, one of the largest in Europe, offers a glimpse of a net zero future.
With every turn, its 71 stark white turbines, with their 117 metre diameter rotors, can each produce enough electricity to run an average home for a day.
Fuelled by targets to cut greenhouse gas emissions, a drive to boost energy independence after Russia’s invasion of Ukraine, and rapidly improving technology, European countries especially have been increasing wind farm construction since the pandemic. They are now producing amounts of power that would have been unimaginable just a decade ago.
Across Europe, wind energy on average now caters for 16 per cent of electricity demand. In Denmark that level rises to 55 % and in Ireland it stands at 34 %.
According to turbine information group Wind Europe, 2022 was a record year for wind installations across the continent, with power companies adding a record 19.1 GW of new capacity, a 4 % increase compared with the previous year. Moreover, 87 % of these new installations were built onshore, the majority in Germany, Sweden and Finland.
And demand will grow even further. According to the International Energy Agency, to meet current net zero targets, it is necessary to increase average annual capacity to almost 250 GW. Wind Europe expects European countries to install 129 GW of new wind farms over the period 2023-2027 which would still fall short of its 2030 targets by 10 GW a year.
For an industry seen as the poster child of a zero carbon future, the transportation and lifting process to get these things into operation has failed to keep pace with new developments and relies heavily on carbon-hungry technology.
Take the normal construction process: Typically, a construction team erecting a field of wind turbines needs to use a limited number of diesel-powered mobile or crawler cranes tall enough to erect the turbines. To get these cranes into position, construction teams then need to build thousands of square metres of hard stand – areas of compacted hard ground suitable for holding the heavy machinery necessary – as well as the high-load site roads needed to get them there.
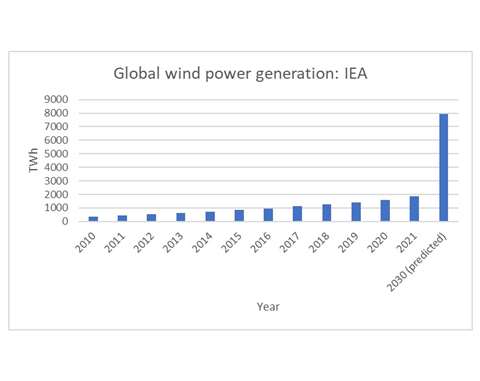
“Onshore wind farms offer a large step towards the energy transition. However, projects themselves remain carbon heavy,” says Pieter Jacobs, head of onshore wind at Dutch heavy lifting company Mammoet. “We, as a lifting industry, need to look at wind farm construction differently.”
For a start, Jacobs says, manufacturers are making turbines so tall these days that only a limited number of traditional cranes around the world can erect them.
In an attempt to reduce the overall cost of the electricity they produce, manufactures have been making larger turbines to produce more energy per unit. The average capacity of a turbine has grown from less than 1 MW in the 1990s to more than 6 MW today.
At the same time average hub heights have increased from around 40 metres above ground in the 1990s, to around 80 metres in the early 2000s and close to 100 metres by the 2010s. Currently hub heights in some parts of the world exceed 160 metres.
“The availability of the cranes is already an issue,” says Jacobs, “If you look at the Liebherr 1750, the onshore wind industry preferred crane in Europe, it is limited in the marketplace. With the IEA predicting that onshore wind capacity must almost double globally by 2025, demand for lifting equipment capacity will rise exponentially. The industry must reduce its dependence on conventional cranes to make this possible, otherwise, there are just no cranes available.
“Hub heights are rising to 200 metres – beyond the reach of any crane that works on ground level,” Jacobs adds. “With higher hub heights and bigger turbines, the cranes we use today will soon become obsolete.”
Moreover, it is perhaps ironic that, according to the US Environmental Protection Agency, the process of erecting just one turbine, roughly corresponds to the same amount of carbon emissions as driving 247,382 miles by car, according to the EPA’s greenhouse gas equivalence calculator.
Cutting emissions
Mammoet estimates that on a recent project installing seven turbines on a separate project in Finland in 2022 using a Liebherr LG 1750 wheeled mobile lattice boom crane and a smaller assist crane, the construction process alone released 676 tonnes of carbon dioxide into the atmosphere.
This included the construction of seven hardstands measuring 5,000 square metres, 50 truckloads of deliveries needed to transport the main crane to the site and 40 truckloads to move it between turbine locations, plus 13 truckloads of deliveries to assemble the assist crane and 10 truckloads to move it between hardstands.
“Putting a turbine together only takes about ten lifts – and as soon as you do those ten lifts and the turbine is installed you move the whole crane to the next position,” says Jacobs. “With the current size of turbines, you need quite big machines so every time you move location you are relocating about 700 to 800 tonnes of equipment. It doesn’t make sense, not only because that is a lot of weight but also because you need to lift it high up in the air.”
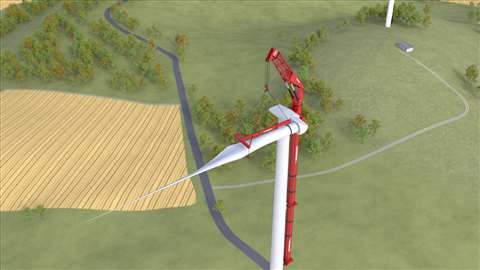
“These are logistical problems, not lifting ones,” he adds. “If we are able to reduce the amount of time spent on construction and simplify the operations, we will reduce the time people need to spend on site and all of the carbon emissions associated with getting them there and keeping them there too.”
In an attempt to solve this problem, Mammoet has teamed up with Swedish power company Vattenfall to design a specialist electric crane which can be attached to the turbine tower rather than the ground.
Under the current designs, the tower base and first two parts of the turbine tower would be erected by traditional methods using the assist crane. Then, the climbing crane is installed onto the tower using special adaptors (probably a welded bracket). From this position the climbing crane can be slowly moved up the turbine tower as it is constructed, using the turbine tower rather than the ground as a pedestal to support its weight.
This method allows the team not only to reduce the size of the crane significantly and all its associated infrastructure. It also removes the problem of current crane availability and capacity limiting turbine construction.
In the case of the seven-turbine project in Finland, they estimate that they could reduce the total amount of carbon emissions produced in the turbine assembly by more than a third to 433 tonnes of carbon emissions – simply by reducing the size of the crane, the specifications of the roads and hardstands, and reducing the size of the assist crane to an LTM 1500 (a 500 tonne capacity crane instead of a 750 tonner).
Reducing hardstands
Jelmer Boukes, programme manager at Vattenfall adds that not only would the climbing crane be able to reach greater hights than its traditional alternatives and be responsible for fewer carbon emissions, but it would also be able to operate in locations with up to 80 % more wind, unlocking new complex and remote wind farm sites.
“We are currently looking at locations which are a little bit remote and where we have to build a bit higher. There are big advantages of using a climbing crane system in these areas,” he says. “And eventually we hope that one the first turbine is spinning, we could use the electricity it generates to power the crane.”
And Mammoet and Vattenfall are not the only ones with a similar idea. Around the world a handful of manufacturers, operators and others are hoping to produce wind turbine climbing cranes.
Germany-based wind turbine manufacturer Enercon is perhaps the most advanced. In 2017 it acquired Dutch rival Lagerwey which had already developed concepts for a LCC60 climbing crane designed to assemble its own turbines (the name refers to the maximum 60 tonne hoisting capacity below the hook) and in 2019 began work on a larger LCC140 version.
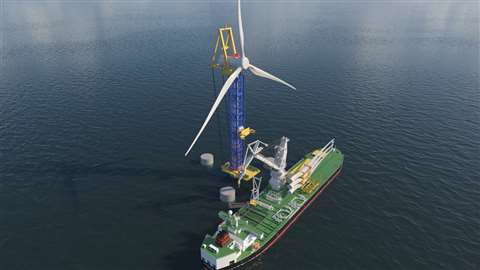
According to Enercon, its cranes attach using three levels of pre-cut reinforced holes already drilled into the turbine tower. The 30-meter central main body of the crane also incorporates four specially designed “gripper arms” to distribute the weight of the crane and the lifting loads while hoisting operations are remotely controlled from ground level.
In 2021, Enercon built two LCC140 self-climbing cranes, which it has deployed on a number of its own turbine installations in the Dutch Eemshaven region.
Basque-based engineering company HWS Concrete Towers is another company with a similar idea. In December 2020 it demonstrated its AirCRANE system, a 30 tonne net lifting capacity unit which climbs concrete turbine towers using a girder and is anchored by spikes inserted into holes in the tower.
In December 2022 German energy company RWE signed a letter of intent with Norway-based manufacturer WindSpider which is developing a modular self erecting crane system which surrounds the wind turbine tower like the web of a spider and can be used both on land and at sea.
Like the Mammoet-Vattenfall climbing crane, WindSpider also uses the tower of the wind turbine as part of the crane, giving it an effective lifting capacity of more than 1,200 tonnes and eliminating motion between the crane and the tower.
So, if the idea of turbine climbing cranes is so good, why are they not being used more widely?
Vattenfall’s Boukes says that the main reason is that although the new crane would save money and carbon in the long run, the cost of developing it is off-putting for many.
Taking the financial risk
“From my point of view, it has to do with the availability of traditional cranes,” he says. “Until now it has been easier to construct turbines with traditional cranes, looking at heights and weights. It’s a completely new technology so it requires investment. The advantages are for the full value chain, but somebody has to be the first mover and needs to take the risk.”
He adds that the design of the climbing crane must be inextricably linked to the design of the turbines it services. This means there are few fallback options for using it if the manufacturer the crane has been designed for ceases to function or provide the crane owner with work. Moreover, for the manufacturers, making a large investment in such a project would effectively force them to work with the partners and remove the competitive bidding process for construction.
Jacobs says that these issues could be overcome if manufacturers came together and agreed standardised interface designs which would fit on all brands of turbines and climbing cranes.
“We have to move to carbon free construction – not just for wind turbines but for the whole construction industry,” he says. “And I think renewables construction we should be the front runner in that.”
STAY CONNECTED
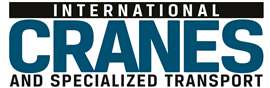
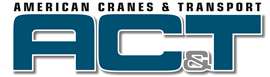
Receive the information you need when you need it through our world-leading magazines, newsletters and daily briefings.
CONNECT WITH THE TEAM
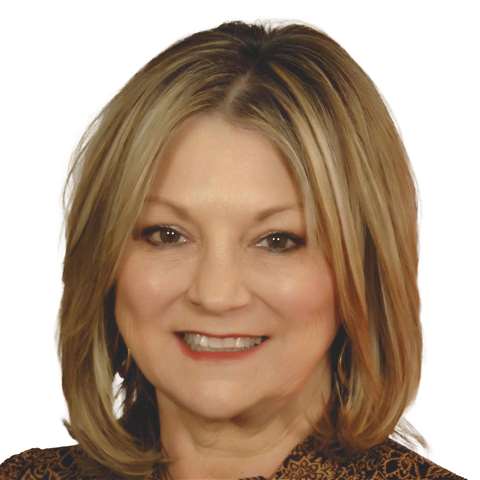
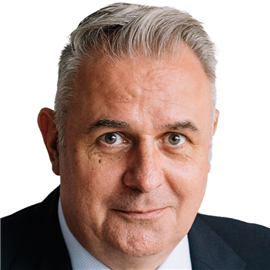
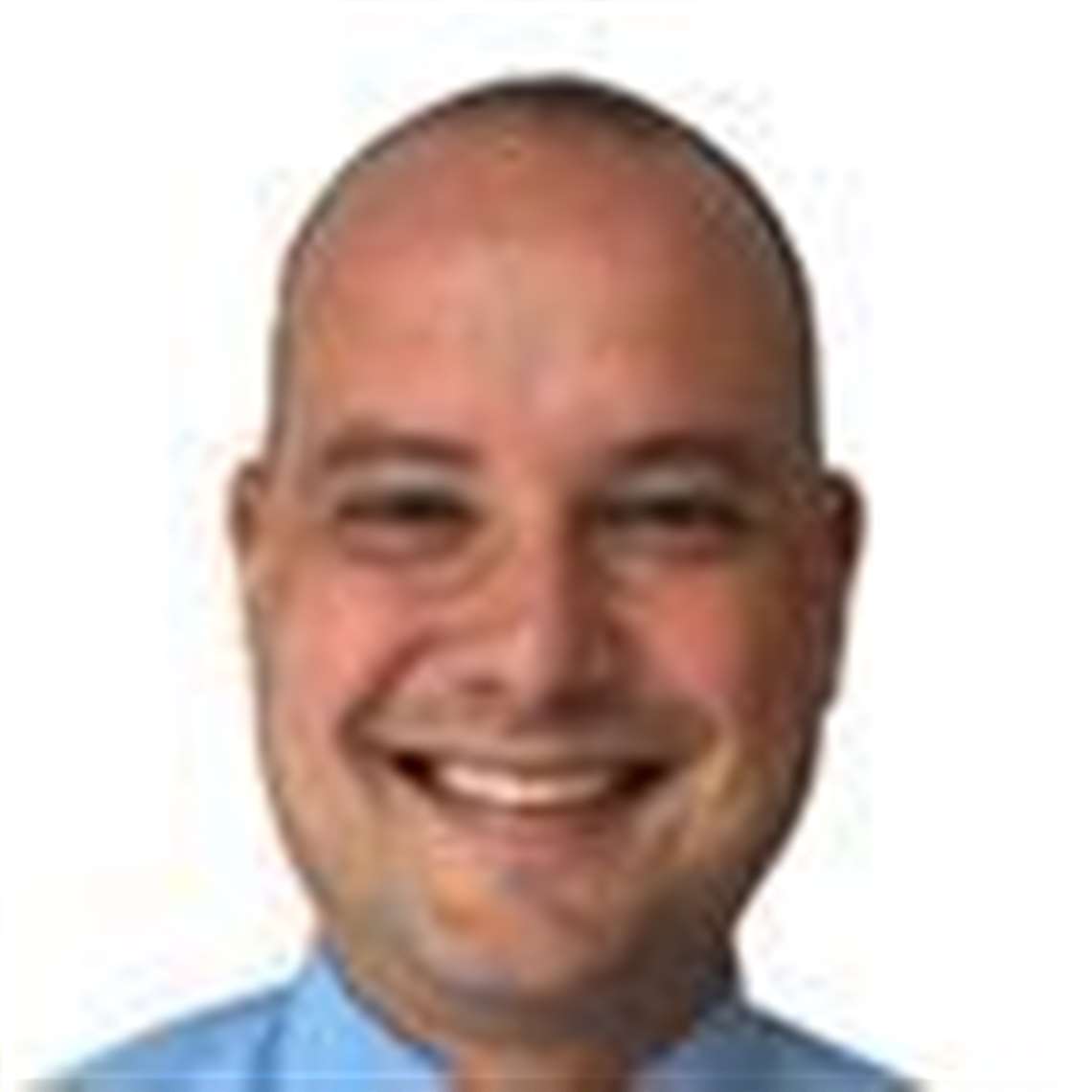
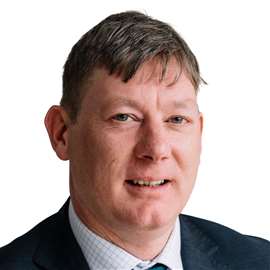