In a hole
19 March 2008
Last year, Portland, OR–based Campbell Crane provided a Link–Belt HC 278HII to build a parking garage in Spokane, WA. In a tight space between the buildings, the parking garage was purposely built up and around the crane. When the job was done, the crawler crane was sitting in a pit about 15 feet deep.
Campbell Crane called on Morgan Machinery Moving of North Plains, OR to lift the crane out of the pit. Using its gantry system, Morgan workers tediously lifted the crane to ground level and then built a platform so the crane could be driven out under its own power.
The obstacles in lifting the crane out of the hole were huge. First of all, the crane would need to be moved with its 160 foot boom attached, as well as its counterweight still a. xed. The combined weight of the crane was 420,000 pounds. On the first day of the operation, workers from Morgan Machinery moved its 440 ton capacity Lift and Lock gantry system, cribbing and platform materials into the pit. Crews spent a day setting up the equipment for the lift the next day.
A one-inch steel plate was placed under each of the gantry legs to assure their stability. Four individual gantry legs were used, each rated at a capacity of 220,000 pounds. Olympic polyester slings rated at 200,000 pounds in a basket were attached to the outriggers of the crane.
On the day of the move, the gantries lifted the machine 10 inches. At that point, crib piles were placed under each outrigger. The crane was lifted 10 inches at a time, with the crib piles built up after each lift. “We built a crib pile under each outrigger and followed the crane up,” says Steve Spurlock, Morgan's corporate safety manager. “After each lift, we extended the crib pile up to the base of the outrigger.”
After getting the crane just above the height of the wall, the plan was to drive the crane away from the garage. Crews began buildingthe platform system when the crane was at the height of the wall. The platform was built with four large wooden crane mats that were 4 feet wide by 20 feet long by 12 inches thick and comprised of thick hardwood. The mats were placed next to the concrete retaining wall, which was at the front of the crane. The base of the platform was laser leveled to ensure its stability. For the sake of safety, Spurlock says they built an additional stabilizer system using cribbing material on each side of the platform toward the back of the platform away from the retaining wall. Th is was interlocked away from the platform aboutact eight feet, getting wider at the base.
As the platform was being built, the crane slightly rested on the outrigger crib piles with the majority of its weight supported by the gantry system.
Once the platform was to the height of the retaining wall, crews tested it by gently resting the crane on the platform while still using the gantry system for safety. Assured that the platform was adequate, the crane was gently released from the gantry system. The crane's outriggers were then retracted, the crane started and the operator slowly moved it forward.
“There wasn't even a wiggle in the platform system,” says Spurlock.
The entire e. ort spanned 15 hours, starting at 6 a.m. with the crane out of the pit by 9 p.m., Spurlock said.
STAY CONNECTED
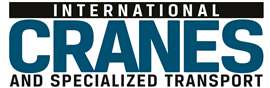
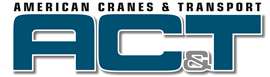
Receive the information you need when you need it through our world-leading magazines, newsletters and daily briefings.
CONNECT WITH THE TEAM
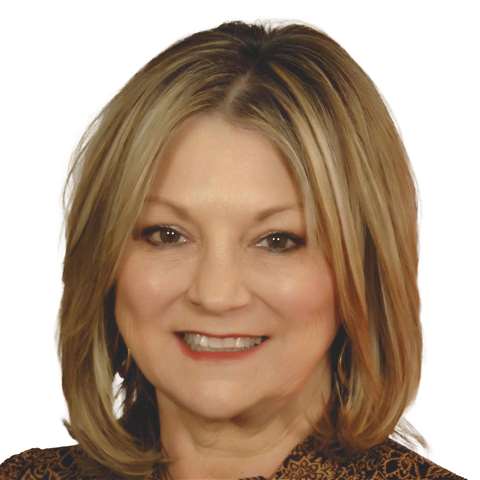
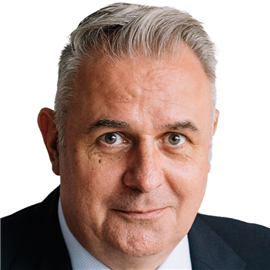
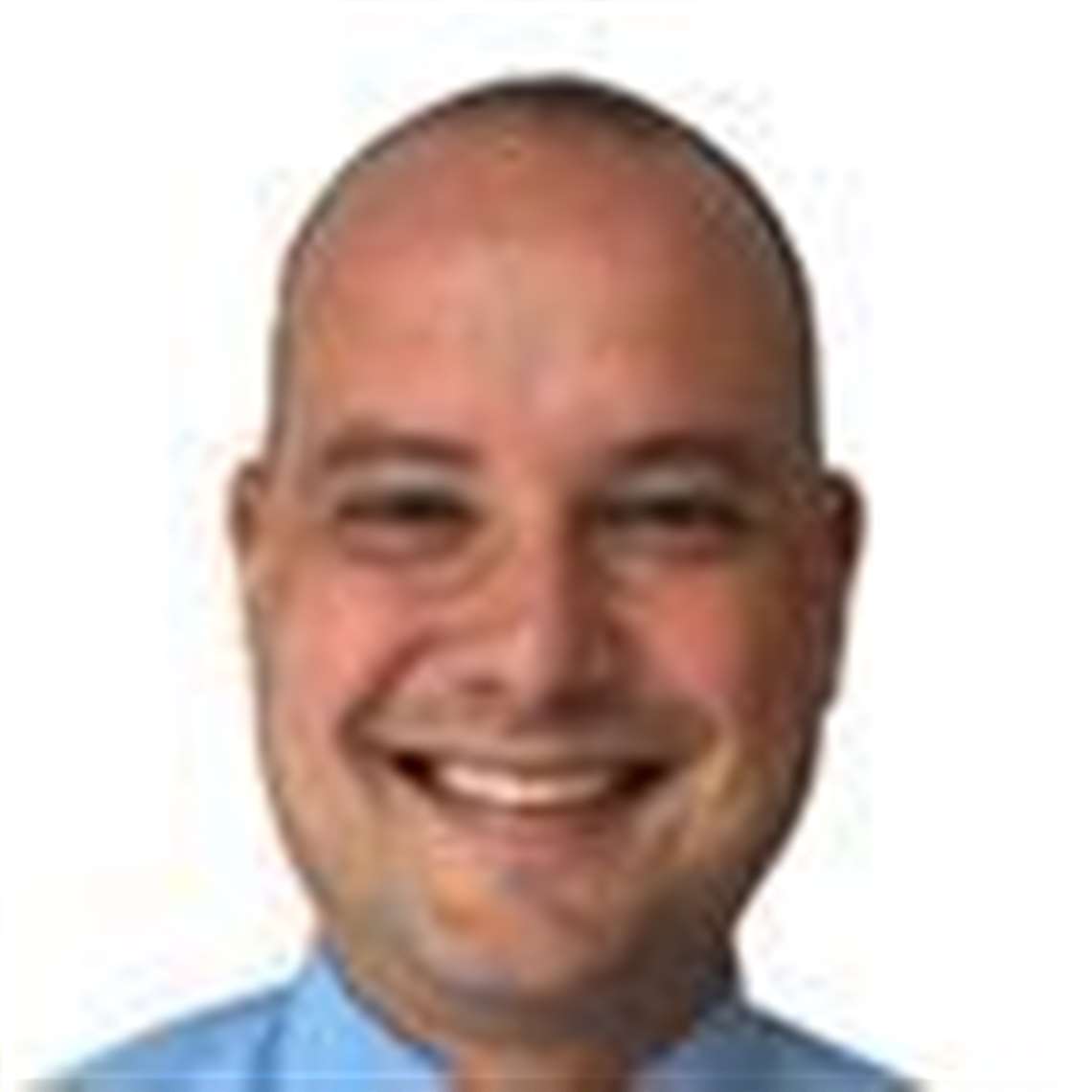
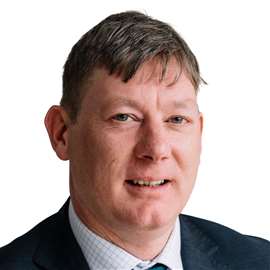