JR Moran: ‘The people in the crane industry are second to none’
07 August 2023
Dedicated. In a word, this particular term fits JR Moran to a tee. He is dedicated to his family, his career, his clients, his colleagues and the industry at large. He is also dedicated to making things safer and better altogether.
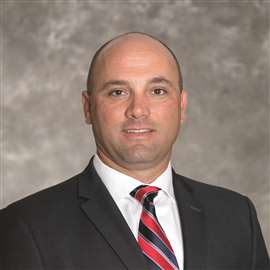
Moran graduated from University of Alabama at Birmingham in 2004 with a degree in industrial distribution. He immediately started with Brasfield & Gorrie as a trainee in the crane department. In the 19 years since, he has diligently worked his way up, first in product support and then as a branch manager. He worked in business development and was named Director of Crane Operations in 2015.
In this role, he manages the company’s crane and hoisting fleet which includes tower cranes, mobile cranes, material hoists and marine equipment. A leader in his field, he forges relationships with colleagues and the industry at large, plus he oversees the deployment, maintenance, mobilization and procurement of Brasfield & Gorrie’s fleet.
The group that Moran runs is a support division for Brasfield & Gorrie, a general contractor and one of the nation’s largest privately held construction firms..
“We take pride in providing first class products and support to each project,” Moran said. “Our performance is a representation of the crane and rigging industry and we believe that we perform and service our clientele as well as anyone.”
Familiar face
Moran is a recognizable face in the crane industry, and especially in the realm of tower cranes. He has been a presenter at several crane industry events, including KHL Group’s Tower Cranes North America conference. He is chairman of SC&RA’s Tower Crane Task Force.
I first met him in the summer of 2018 when he and a colleague, Russ Gibbs, gave a compelling presentation about improving tower crane operations with virtual design and construction at the Tower Cranes North America event in Miami. Gibbs and Moran shared personal experiences about how they have implemented building information modeling (BIM) processes to better integrate crane operations with their preconstruction and construction teams.
“Increased awareness of the importance of proper planning and communication around tower crane assembly on construction projects is a strategic area of focus for us, and we hope that our success will help guide the entire crane industry in a positive direction,” he said in that presentation. “As the planning phase of a project begins, models, including all aspects of the construction process, are being created and shared by the design team to provide more accurate detail and planning. In the past, equipment was one of the last components to be considered in the planning stages of a project. The current intent is for equipment to be part of the initial plan. The execution of these concepts involves all major stakeholders in the BIM process, which has in turn created increased communication, increased accuracy and safer projects.”
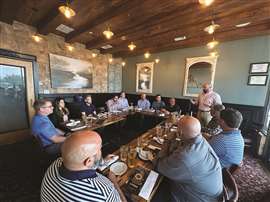
I also spent time with Moran during the early days of the pandemic, when he served on a panel at a “virtual” TCNA event. We rehearsed the panel discussion ahead of time, and I was impressed at how seriously he took the issues that were being addressed. Besides being well-schooled on all things tower cranes, he convinced me and everyone who participated that he genuinely wants to help make tower crane usage safer and more efficient.
Fast forward to a month ago in Virginia, where Moran chaired a special meeting of the SC&RA’s Tower Crane Task Force. The discussion involved the best minds in the business, according to Moran. I think we will see important results come from this task force. And from JR Moran.
How do you characterize the market for tower cranes?
Tower cranes continue to be a major fixture in the construction world. Manufacturers continue to diversify their product lines to provide solutions for a wide variety of applications. The accelerated growth of urbanization and clean energy initiatives continue to make the tower crane an integral part of the construction process. The use of tower cranes continues to evolve and adapt to service the energy and oil industries as well.
What are the biggest challenges facing tower crane-owning companies?
First and foremost, rising equipment costs and a very competitive rental rate structure. Another challenge is workforce development, attracting the next generation of talent and the retention of those employees.
With commercial high-rise construction starts down in many markets, and more emphasis on infrastructure, industrial and public development, how are tower crane owners competing?
A diversified fleet offering to provide solutions to a wide variety of scopes of work. The urbanization of many areas will continue to point toward the use of tower cranes because of the small equipment footprint.
The SC&RA’s Tower Crane Task Force recently met to discuss a range of tower crane industry topics. What was the result?
I am fortunate to chair a committee that is so talented; the best in the business have volunteered their time to make a difference. The purpose of the meeting, which was very productive, was to create a document to provide best practices to successfully plan, communicate, mitigate and identify roles and responsibilities that align with the manufacturer’s recommendations for tower crane erection, reconfiguration, climbing, tiebacks and disassembly processes. Atypical projects (multi-crane, multi-jump, hurricane-prone regions, self-erecting tower cranes, etc.) will require additional consideration in all phases of the project for successful execution.
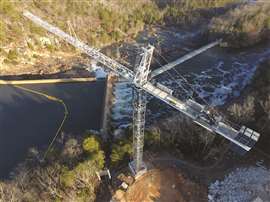
The multiple items require early planning, refinement, verification, confirmation and finalizing. Every project, site, customer, controlling entity, locality and crane is unique and may require additional procedures. Some procedures contained within these best practices may fall outside of your scope of services, but you might consider reconfirming to prevent any frustrations, delays and conflicts.
We want to provide a guide to the industry on how to plan and communicate in the most effective way when mobilizing tower cranes. We also want to provide information that will help mitigate risk and in time strengthen the industry confidence and credibility.
What is the best business advice you have been given?
Build relationships. Business is done with individuals who have a common bond.
What keeps you engaged in this business?
The people in the crane industry are second to none. I enjoy the people I work with. The work is challenging and diverse, its purposeful and in most cases a part of the critical path of a project.
What do you do when you are not working?
I have a wife and two children. Our children are extremely active, and they take up most of my time. My family is my priority.
STAY CONNECTED
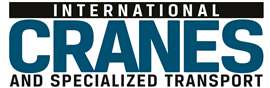
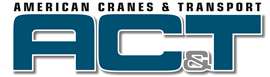
Receive the information you need when you need it through our world-leading magazines, newsletters and daily briefings.
CONNECT WITH THE TEAM
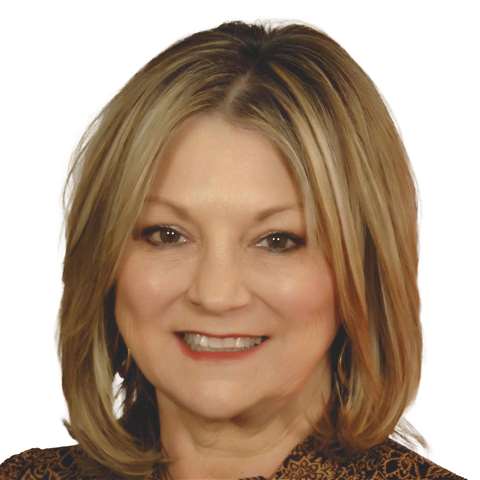
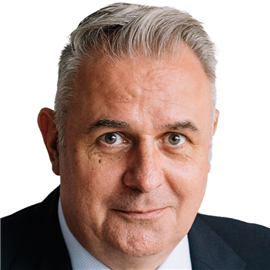
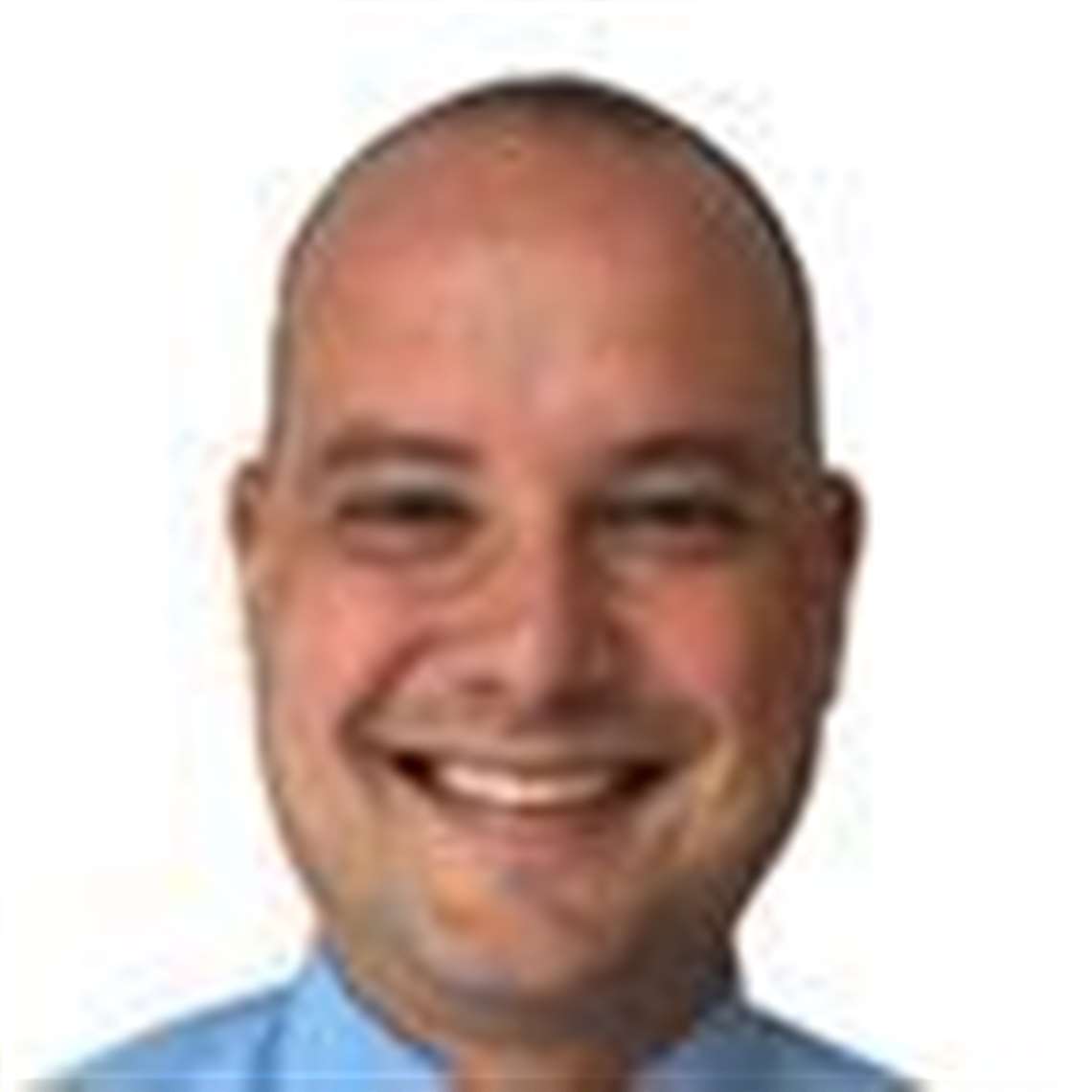
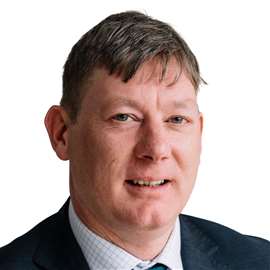