Lift, haul and install
15 April 2008
Lifting, hauling and installing oversized and extremely heavy objects can make for some challenging times, especially when a tight schedule is in place. Th is was the case recently for Barnhart Crane &#amp;Rigging in its efforts to set various heavy and awkward components of a steam turbine generator (STG) at a power generation plant near Aurburn, AL.
Due to an accelerated schedule, Barnhart was given two days notice to mobilize to the site. The first unit was the stator, weighing 528,000 pounds. Barnhart picked up the unit at a rail siding station about five miles from the plant.
The challenge was the ambitious schedule. Th e rail line that operated the spur allotted 60 hours from the time of railcar delivery to the complete demobilization from the site. If Barnhart was unable to complete its work on the rail site in 60 hours, the customer, which held a temporary lease on the spur, would have faced substantial daily penalties from the rail line.
To make matters more complicated, Barnhart was given the constraint of working only one 10-hour shift per day. Th e railcar arrived on a Monday at 5 p.m., meaning that work needed to be finished by 5 a.m. Th ursday, requiring Barnhart's crews to complete the assembly of the equipment, remove the stator from the railcar, reload and remove the tooling in just two days.
Th e stator was lifted from the railcar using a 450 ton J&#amp;R gantry system and was transported to the jobsite on a 15-line Goldhofer transport system.
At the plant the STG components were to be set atop a 40 foot concrete platform. Using its Modular Lift Tower (MLT) in act a stator frame configuration on one end of the platform, Barnhart crews installed a gantry runway over the 100 foot platform, as well as two 60 foot long gantry track beams from the pedestal to the MLT legs.
A 450 ton self-propelled gantry system was installed on the gantry track, and then Barnhart's 500 ton capacity hoist was erected above the gantry system.
“Th e design of the 500 ton hoist, combined with the gantry, gave the ability not only to lift and travel down the length of the pier, but for side-to-side movement as well,” explains John Bullwinkle, project manager. “Th is configuration sped up the layout and alignment process when the equipment was set.” act
STAY CONNECTED
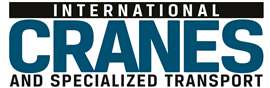
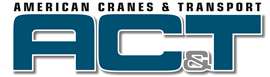
Receive the information you need when you need it through our world-leading magazines, newsletters and daily briefings.
CONNECT WITH THE TEAM
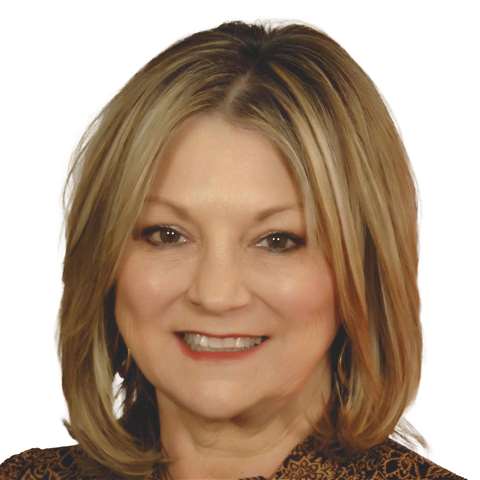
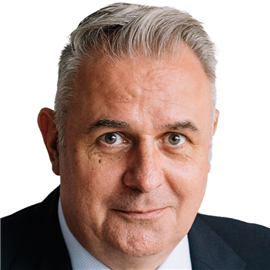
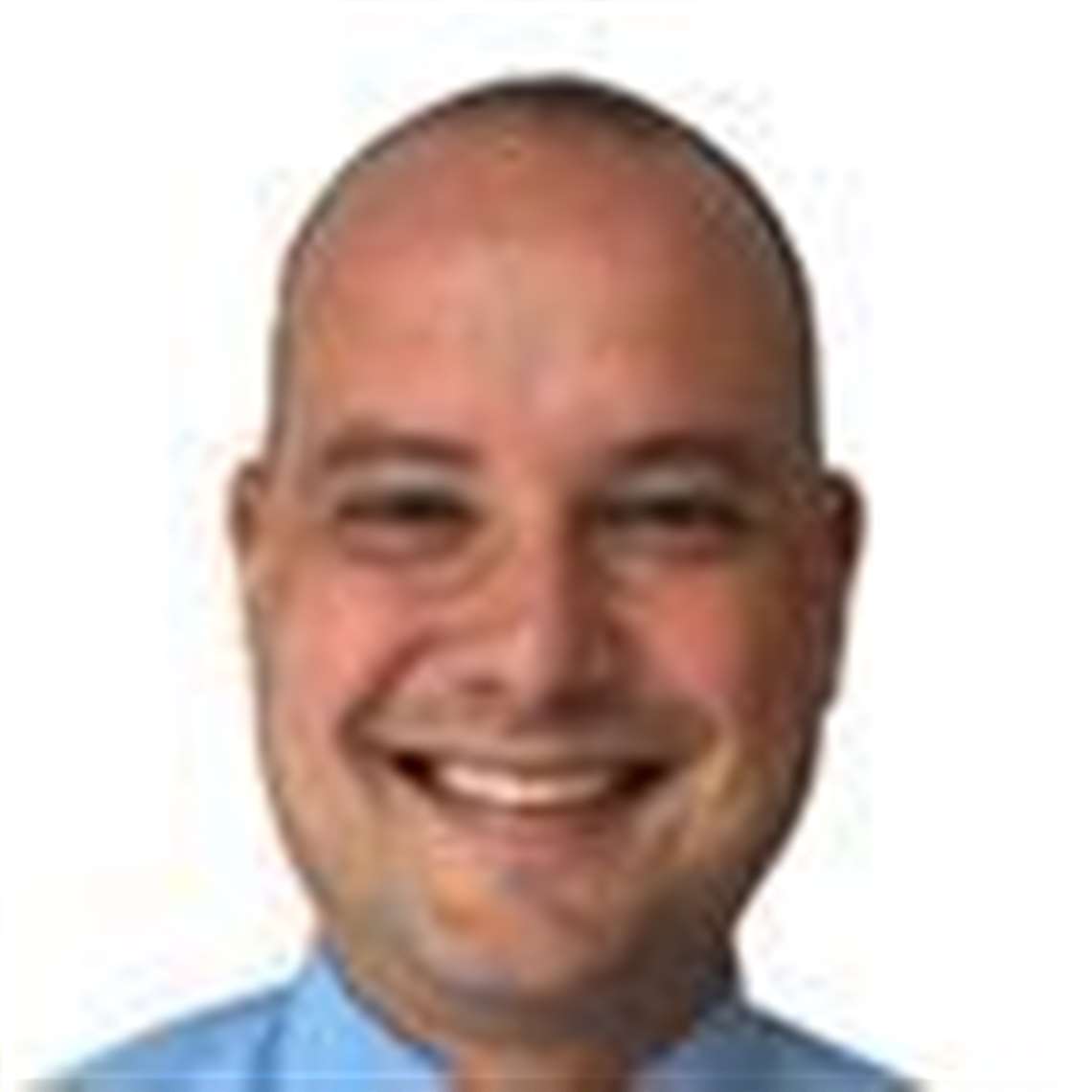
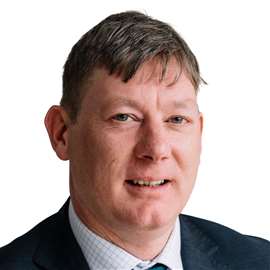