LMI technology remains indispensable tool
21 July 2020
The latest product round-up of load moment indicator technology and rated capacity indicators.
Operator aids come in all shapes, sizes, functions and designs as LMI and RCI technology continues to become more sophisticated. Sarah Nell, marketing assistant at WIKA Mobile Control said that even compared to just a few years ago, LMI’s have increased in size and have exceptional color and clarity, giving the operator a significantly improved viewpoint. Today’s sensors and load algorithms have improved system accuracy which gives the operators an increased level of confidence.
Eliminating operator guess work, LMI/RCI systems serve as the driving force behind safe and successful crane and equipment operations.
CraneSmart’s latest LMI4 touch-screen user interface benefits customers utilizing LMI systems.
“Today’s LMI technology helps the crane operator to ensure that the equipment is operating within the appropriate working capacities of the crane,” added Nell. “LMI systems improve operator productivity by providing valuable data regarding lift positions. In addition, improved work zone limitations have also helped to clarify the cranes critical lift areas and capacities. Having the ability to display geodata, combined with modern lift planning software, has also reduced setup time.”
System datalogging has also proven to be a valuable feature. Additionally, component quality has significantly improved which helps to reduce service cost, machine down time and consequently extends the life of the machine.
“The RCI itself is indispensable to the operator for efficient and safe lifting, said Manon Huard, OEM sales manager, RaycoWylie. “Remote access to the RCI is key to the fleet manager to optimize operation and maintenance, but furthermore to quickly identify if a crane is overused, avoiding unnecessary maintenance costs.”
With industry standards continuing to develop, LMI/RCI technology will also need to improve alongside it. This could include better quality, sensory technology and a more user-friendly interface.
“As system integration continues to evolve, this will offer more machine data at the operator’s fingertips,” said Nell. “There is also the potential that telematics for live system access will become an essential requirement in years to come.”
This development is reflected in the advanced telematics on the latest system from RaycoWylie which provides users the ability lock the machine or only allow slow speed from a distance. This could be useful for when the crane is being used by an unauthorized person, for preventing theft and misuse of the crane, said Huard.
As the technology continues to advance, ACT surveyed several leading manufacturers for information about their latest product.
CraneSmart
Cranesmart has been manufacturing wireless safety equipment, operator aids for cranes and other heavy equipment for over 30 years. The company’s newest LMI4 touch-screen user interface (display panel) serves customers with LMI systems, utilizing advancements in technology and industry feedback to make equipment simpler and more effective for operators.
Employing the LMI4 system on jobsites around the world will help crane service companies effectively and safely complete work, while having the assurance that they are meeting jobsite safety requirements for their cranes, the company said. Operators can expect to feel more confident in their daily operations with the additional aid or knowledge of real-time operational parameters; including any combination of load on the hook, boom angle, boom length/radius, wind speed, boom direction and list/trim of the machine. The modular panel design and wireless transducers allows for any combination of functionality to be added at any time with relative ease, the company said. The USB port in the back of the LMI4 panel provides easy access to operator logs and post-sale modifications in programming to be uploaded if required.
RaycoWylie
In response to demand, the RaycoWylie i4500 lift management system is now available with a telematics solution. The RAYCOnnect remote access service has all of the necessary features to facilitate fleet management and efficiency. RAYCOnnect is user-intuitive and can be accessed from a computer, tablet or cell phone. It uses simple icons and menus to present a live view of critical information for each piece of equipment, including GPS location, working hours, safe working load, over hoist input (ATB), wind speed, outrigger positions, engine data and more.
Alarm notifications can be set for specific critical safety occurrences or for maintenance cycles. This solution also permits remote diagnostics, eliminating useless travel to the job site for troubleshooting.
WIKA Mobile Control
WIKA Mobile Control offers three different LMI solutions that provide OEM’s and end-users flexibility in meeting their lifting requirements.
The qSCALE Ix is a standard LMI solution which meets the requirements for both OEM and aftermarket applications. The system provides the operator with a graphic display of the crane’s boom length, boom angle, load radius and current load (both actual and allowable). The color graphic display is available in either 4.3 or 7 inches and includes an integrated bar graph to provide the operator with the crane’s current utilization. The system offers the flexibility of using both wireless and hardwired sensors, and also features a simplified calibration procedure using a menu-driven process, which reduces calibration time. For OEM’s looking to fully customize their LMI, the qSCALE offers the flexibility to modify and add system options beyond a standard LMI solution. This includes machine specific graphics and adding additional sensors based on specific application requirements. This system is also equipped with the option of custom communication with non-LMI functions such as air conditioning, engine diagnostics and outrigger monitoring.
The qSCALE maestro LMI is an aftermarket upgrade solution for the DS150G, DS350G/GW and existing maestro systems that are currently in the field. The qSCALE maestro offers a flexible design that converts existing software eliminating the need for recalibration. The system features a user-friendly 4.3-inch color display that exhibits actual and allowable load, boom length, boom angle and load radius. With an IP 66/67 rating, the console can be mounted either in or outside of the cab.
A team effort
The first Terex 4792 RCL system was installed by Custom Truck in 1999 under the supervision of Greer. Load King is continuing a long history of collaboration with Greer on their newest crane, the Stinger 80-160.
Greer’s MG6 computer system will be incorporated into the entire Load King line.
Greer has introduced a new computer – The MG6 – which will be incorporated into the entire Load King line. The most significant benefit of moving to the MG6 computer from the MG5 is the serviceability of the unit in the field. The MG5 had pressure transducers, relays and a power controller inside a sealed enclosure. Failure of any part in the enclosure meant replacing the entire assembly. The MG6 now utilizes external components that can be remote mounted and individually replaced. Remote mounting also simplifies hydraulic routings and removes points of failure. Power distribution has been moved to an upgraded wiring harness and a separate CAN-based controller. This increases serviceability, reliability and improves the diagnostic capability of the system.
Migrating to the MG6 also allows Load King to introduce the TS7 touch screen display on the new Stinger 80-160 boom truck. This display features a 7-inch glass-front, glove-friendly touchscreen, enhanced clarity and full color graphics in an IP67 enclosure. Load King boom trucks under 40 tons will continue to use the Insight display together with the new MG6 computer. Load King will be bringing more CAN-based controllers to the entire line. Moving to the CAN-based MG6 is a first step, the company said. Future enhancements will include things like CAN keypads for outrigger controls and upgraded remote controls.
“Load King values our long-standing partnership with Greer, which has allowed us to provide our customers with innovative and quality products,” said John Lukow, senior vice president, cranes, Load King. “The RCL enables our customers to work at a high-level of efficiency, furthering their business goals. We’re proud of the technology we’re able to offer within our product lines thanks to this collaboration.”
STAY CONNECTED
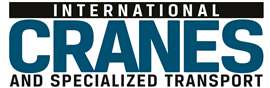
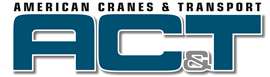
Receive the information you need when you need it through our world-leading magazines, newsletters and daily briefings.
CONNECT WITH THE TEAM
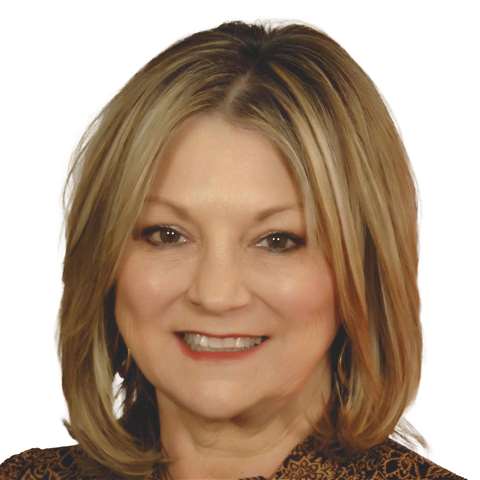
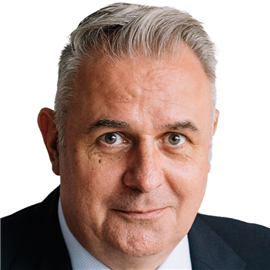
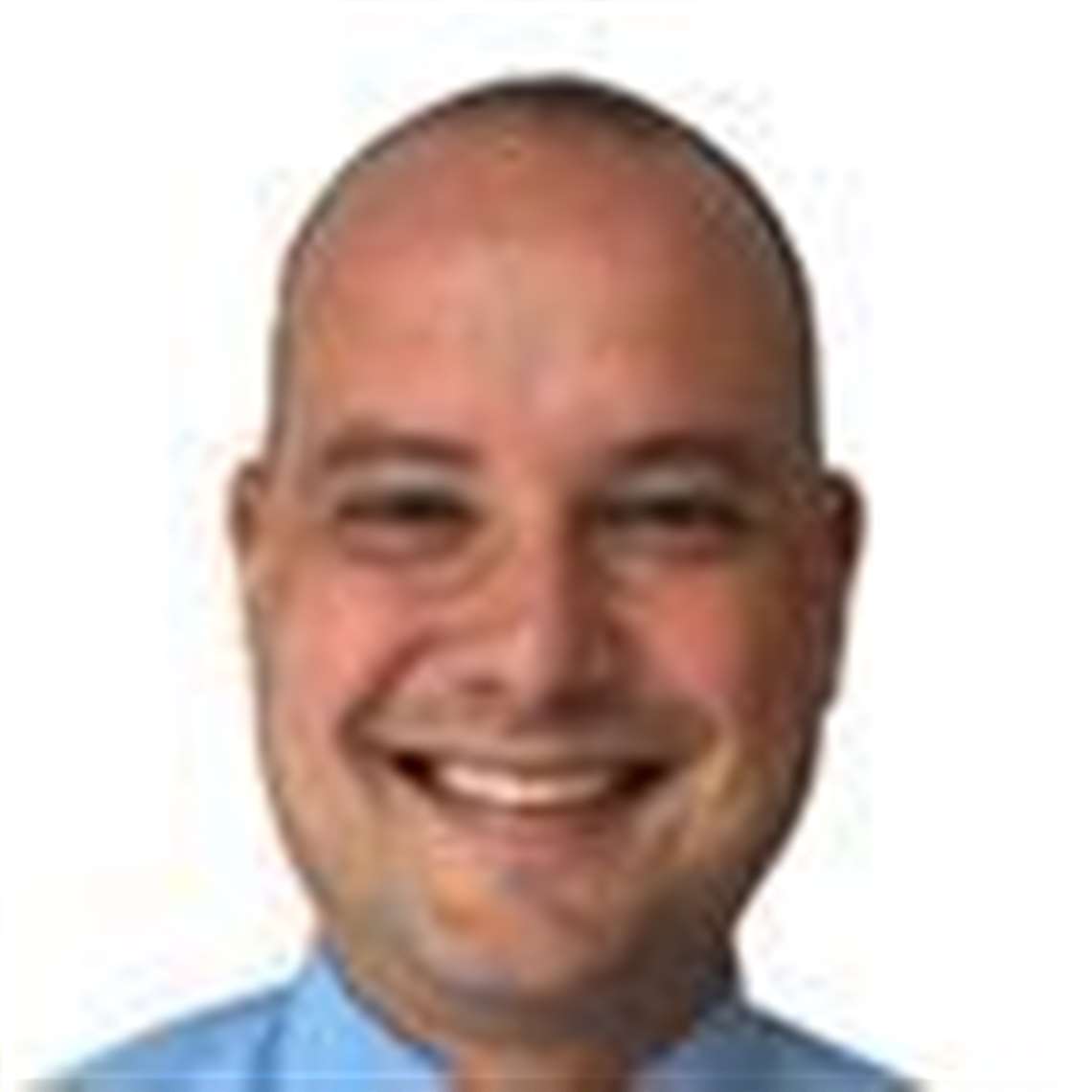
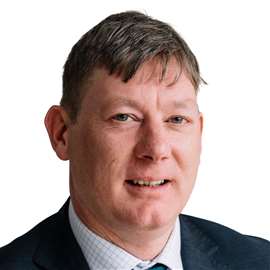