Read this article in French German Italian Portuguese Spanish
Mammoet completes zero emission bridge project
06 March 2024
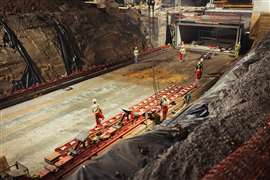
A new tunnel section was installed using battery-powered jacking and skidding equipment in an emissions-free operation in Belgium.
It started out as a standard skidding operation and turned into a demonstration of how to reduce the carbon footprint of a civils project.
Stadsbader Contractors approached Netherlands-headquartered international heavy lift and transport specialist Mammoet to lift and skid an 850 tonne concrete tunnel section 40 metres underneath railway lines.
Prior to this 850 tonne job Mammoet gained experience on smaller emissions-free projects to install transformers.
Mammoet determined that this big job could be done without pollution and its engineers worked to combine conventional skidding technology with new battery-powered equipment.
Accurate calculations and precise implementation were needed to lift and skid the 850 tonne concrete tunnel section. It was 25 x 8.5 metres and had to be moved 40 metres into position below a railway track near Brussels.
To minimise rail disruption for commuters it was a tight schedule to get it done before Monday morning.
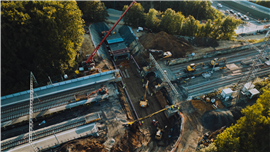
Going to work
Mammoet used its own tunnel adaptors and a skidding system with a battery-electric hydraulic power pack. Prior to skidding the load was lifted using hydraulic jacks. When there was enough ground clearance, hydraulic cylinders pushed the tunnel section along the 40 metre skid tracks with their polytetrafluoroethylene (PTFE) pads to minimise friction.
With everything ready the skidding operation took less than an hour and it came out 2.5 hours ahead of the estimated schedule.
The electric Mobile Power Unit for the skidding system has a 50 kWh lithium battery pack. The batteries are recycled in that they are salvaged from old or scrapped electric cars and upcycled, giving them a second life. The MPU, including its trailer, weighs 1,460 kg. An additional 1,000 kg of auxiliary equipment can be loaded on its roof rack. It accepts standard mains AC electricity inputs at 16, 32 or 63 Amps. A solar battery charger is an option that further adds to the sustainability element.
Another benefit of the entirely battery-powered setup is that it allows works to be carried out ‘off grid’ in remote areas.
Safe sustainability
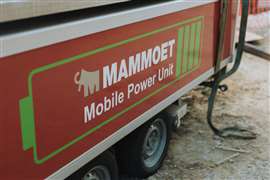
Additional benefits of the electric system on the project included lower noise and there was less impact on the surrounding environment because there were no exhaust emissions on site. Time was not an issue either as the operation took no longer than using conventional equipment.
“We have demonstrated that through innovative engineering and combining new and existing technology we have the ability to execute zero emission heavy lift projects for our customers – and that’s the future,” said Pascal Eeken, Mammoet Europe manager, improvement and innovation.
STAY CONNECTED
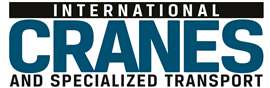
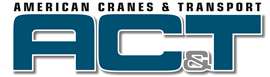
Receive the information you need when you need it through our world-leading magazines, newsletters and daily briefings.
CONNECT WITH THE TEAM
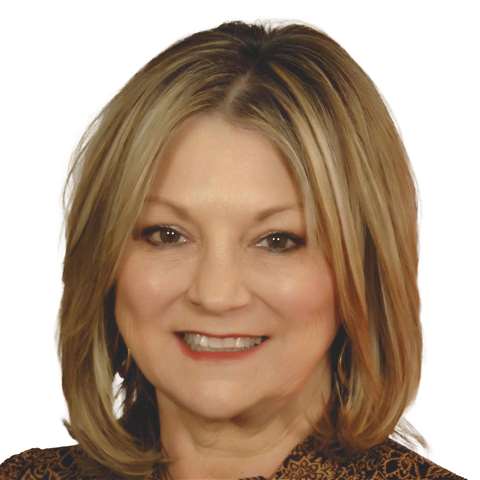
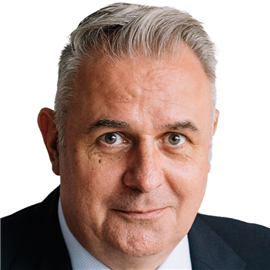
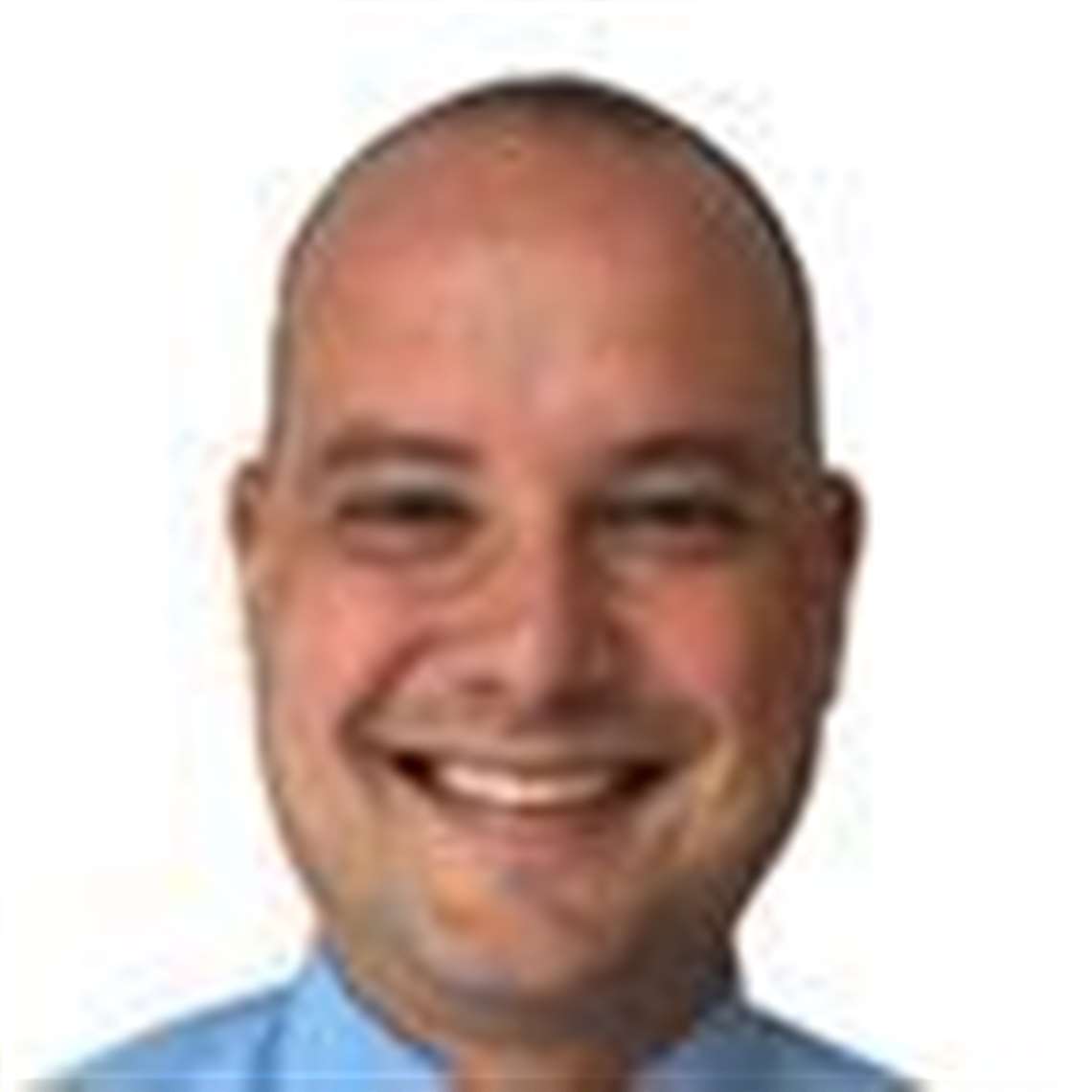
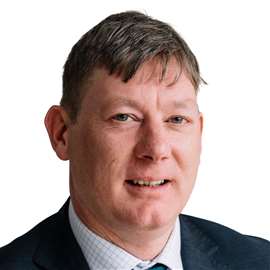