Manitowoc tackles power plant project
04 December 2017
A $500 million project is underway to upgrade the Sooner Generating Station, a coal-fired power plant in Red Rock, OK. A Manitowoc MLC650 crawler is at the center of the action on the “coal scrubber project,” as it’s been dubbed by contractors on the job. The project will help the plant reduce pollution as it aims to meet the EPA’s regional haze rules by January of 2019.
The biggest lift so far has been a 101-ton segment of duct work, which the MLC650 lifted to a height of 211 feet.
The project requires the plant to be retrofitted with a dry coal scrubber system called an Air Quality Control System (AQCS). The system works not unlike a car’s catalytic converter, filtering pollutants out of the plant’s emissions. It also burns the coal at a higher temperature, further reducing the amount of pollution it generates.
PCL Construction, based in Edmonton, Alberta, Canada, is handling all the project’s lifting work using the MLC650 on rent from Maxim CraneWorks. Maxim also has a crew onsite supporting the project.
A few key challenges were apparent from the outset: The job requires the lifting of components that weigh up to 101 tons within tight working quarters. A high-capacity crane is needed, but due to space restrictions, the crane must also have a compact footprint. The jobsite is fraught with conveyor systems, jutting pipe racks and electrical buildings, presenting obstacles to maneuverability and restricting the space available for crane erection. The MLC650 with VPC-Max attachment was the perfect solution.
“Before the MLC650, we would have had to use a more traditional crawler crane on this portion of the jobsite,” said Kurt Stephenson, erection supervisor for PCL. “There might not have been room for a crane with a counterweight wagon, and we would have had to spend time floating or swinging a standard counterweight tray away from obstacles.”
This functionality is enabled by the MLC650’s Variable Position Counterweight (VPC) and VPC-Max heavy lift attachment, which is enabling PCL to automatically adjust the counterweight for each lift. The company only had to erect the crane once, and it can now move the crane into place for each lift with minimal adjustments. The versatility of the VPC-Max allowed the MLC650 to make heavy lifts without the need for an auxiliary counterweight wagon or traditional floating tray, which require additional equipment to handle and would not have fit onto the jobsite.
“The components themselves take up a lot of the room on the jobsite,” Stephenson explained. “With the MLC650, we can move the counterweights in tight, stay in position for each lift and then walk the crane up and down the runway as needed without upsetting any of the loads. Our choice of crane really came down to mobility, which the MLC650 delivers.”
Working non-stop
PCL Construction rigged the crane with 200 feet of main boom and 190 feet of jib. It’s lifting a variety of loads for the project, including 75-ton insulated scrubber sections, 48 ton muscle rings and 100-ton baghouse sections, which act as the filters for the AQCS. The biggest lift so far has been a 101-ton segment of duct work, which the MLC650 lifted to a height of 211 feet.
The MLC650 is working non-stop on the project. When conditions are too windy to make the heavier picks, for example, PCL has the crane lift a variety of smaller components, such as scaffolding material and bracing that will support the inside of the baghouse. Lifting radii for the wide variety of picks have varied between 150 feet and 225 feet. The crane has been working since May 2017 and was scheduled to wrap up its portion of work last month (November).
In addition to providing engineering and lifting solutions on the project, Maxim CraneWorks provided full-time on-site support, maintenance and planning. Kirby Prince, site technician for Maxim, explained why the MLC650 was the ideal choice for the job.
“The MLC650 was perfect for this job because of its smaller footprint and added mobility compared with other crawler cranes,” he said. “It’s helping us to make the lifts where a larger crane might not have fit, and it’s able to easily go the distances we need.”
Efficient lifting
The project’s success is a testament to the support provided by Maxim, as the company’s extensive fleet enabled PCL to devise an innovative lifting solution.
“Maxim has the largest fleet of Manitowoc crawler cranes in the world,” said Rob Schultz, vice president for Maxim’s crawler division. “Our ability to select any type of crane for any project in the U.S.A. provides the type of flexibility that our customers need to meet every type of lifting requirement. The scrubbing project at the Sooner Generating Station is no exception.”
The AQCS installation seeks to eliminate some 99 percent of particulate matter from the plant’s emissions, bringing the 35-year-old facility in line with 21st century emission standards. PCL Construction is working on the project as part of Oklahoma Power Constructors, a joint venture with Overland Park, KS-based Black & Veatch, a global firm that provides EPC services for energy, water and telecommunications. Oklahoma Gas & Electric is overseeing the upgrade that is set to be completed in June 2018.
STAY CONNECTED
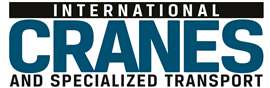
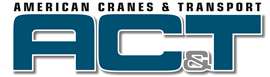
Receive the information you need when you need it through our world-leading magazines, newsletters and daily briefings.
CONNECT WITH THE TEAM
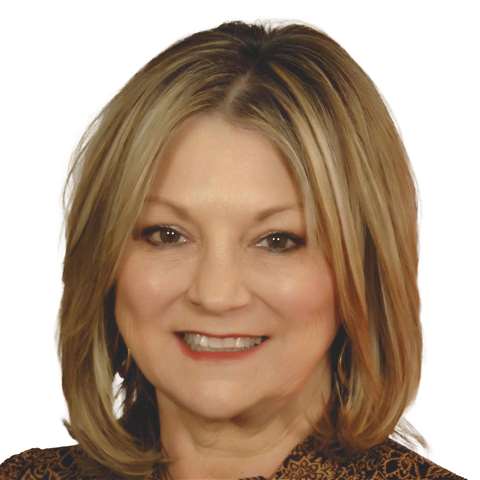
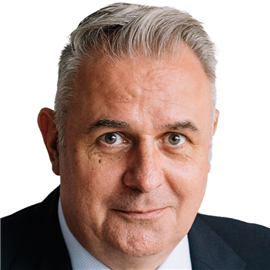
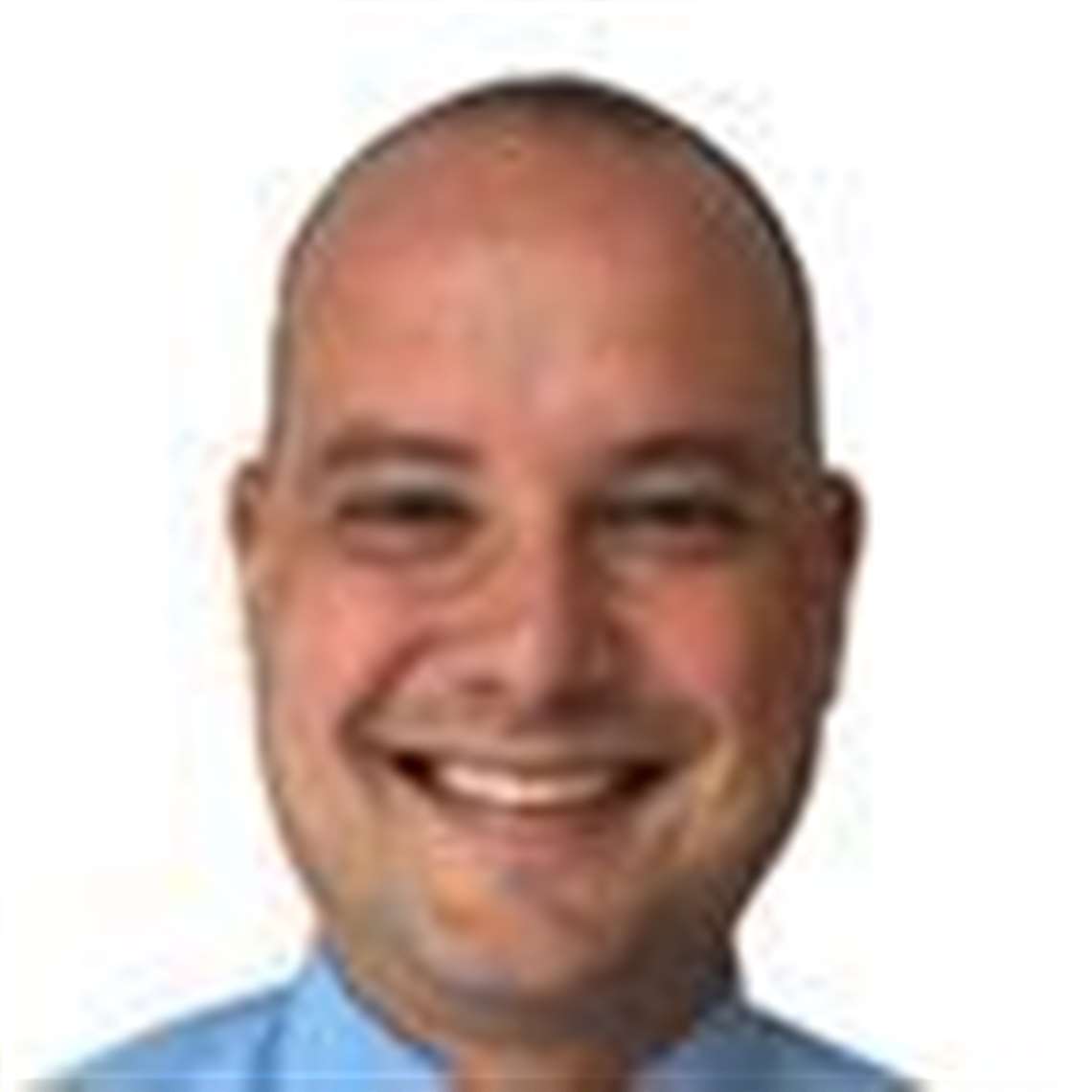
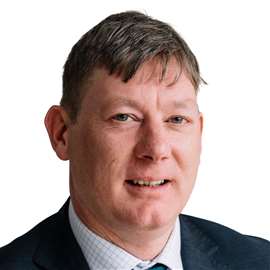