Mat technology from Greenfield
11 November 2019
Greenfield Products’ Smart Crane Mats bring a different concept to the market.
Greenfield Products is known for its expertise in producing custom products like boom dollies and other specialized equipment. Product development is a hallmark of the Hazel Crest, IL-based company. So, it’s no surprise that Greenfield is now in the crane mat business, and was recently awarded a patent for its crane mat design and construction.
“Greenfield’s line of Smart Mats features a two-point pick design that allows the operator to use the same round nylon slings used for the crane counterweights to handle the crane mats,” said Greenfield’s Gustavo Anzola. “The mats are designed so they can be lifted as a stack, four mats at a time, or individually. This translates into a very efficient operation when setting up the mats around the crane.”
The construction of the mats is not the usual steel mat made of tubing or I-beam, Anzola said. Greenfield’s mats are roughly 40 percent lighter than typical steel mats on the market, which means transportation savings, he said.
“They are also thin profile compared to wood or composite mats, so operators won’t have any issues getting the crane outrigger float on top of the mats,” he said.
Another advantage is that Greenfield Smart Mats have virtually no noticeable deflection when loaded.
“Our mats are stout and very rigid, offering good outrigger load distribution,” Anzola said.
Ease of use
Greenfield offers mats that range in size from 4-foot by 4-foot up to 8-foot by 12-foot and from 200,000 to 500,000 pounds in capacity. Anzola said the new mats provide an efficient and convenient lifting configuration for the crane rental market.
“The lifting points don’t protrude through the top or sides of the mats, greatly reducing trip hazards,” Anzola said.
The mat design allows for the set of four mats be stacked together and to be lifted as a single load and drop in sequence around the crane. The operator or oiler is able to use the same rigging for the counterweights of the crane to lift and place the crane mats.
Greenfield designs and manufactures this product in-house from its Union City, TN factory. Greenfield has been “quietly” manufacturing steel mats since 2013. The company decided to get in the mat business when existing crane customers were looking for a manufacturer that could design and fabricate steel mats.
“Most steel mats back then were home-made without any engineering documentation,” said Anzola. “We could offer customers engineered steel mats that matched the crane’s maximum outrigger load.”
Originally, Greenfield started designing mats from steel I-beams, but they were heavy and customers needed lighter solutions.
“We re-designed our mats to be lighter and very efficient to handle and position around the crane,” Anzola said.
The initial target for Greenfield’s mat line was all terrain cranes from 100 to 500 tons capacity.
“We are most competitive when large capacity and large areas are needed underneath the outriggers,” he said.
STAY CONNECTED
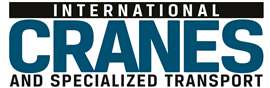
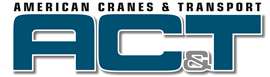
Receive the information you need when you need it through our world-leading magazines, newsletters and daily briefings.