Mine expands
01 May 2008
It does not get much more remote than the Chuquicamata open pit mine 1,650 km (1,000 miles) north of Santiago at 2,870 m (9,416 feet) above sea level. Conditions are tough but progress has been swift on the project to construct a processing plant for copper andmolybdenum production.
The $20 million project is the responsibility of main contractor, BARA, a joint venture between Bechtel and local contractors. Industrial engineering and construction specialist Sigdo Koppers, working for BARA, is handling the civils and engineering work, mainly on the “dry” side of the process–construction of the primary and secondary crushing and screening plant.
Sigdo Koppers started on site in January 2005 and completion is expected this month. Progress has been rapid–all progress above ground, including erecting the structural steel and conveyor system, has been made since March. To help maintain the schedule SK is working three shifts. On site SK has about 95 pieces of equipment and 130 people for the machinery, explains Jose Luis Chapa, SK equipment manager on site. To minimize problems from the harsh environmental conditions, and reduce downtime, SK services its cranes every 200 hours instead of the usual 250.
Of the 20 SK cranes (about half the company's feet) permanently on site 90% are Groves. Most of the cranes are rough terrains–Groves and a Link–Belt 8050–but there are also two Manitowoc model 4100 crawlers, and a couple of Grove GMK4090 (GMK4075 in Europe) all terrains. The Grove rough terrains are RT9100, RT875, RT530, RT855 and RT760 models. Tower cranes on site are a Potain MC 85B and an 8 ton maximum capacity, 40 m boom
Looking along the conveyor between the pit and the stockpile. A Palfinger PK 23080 on an International 7600 truck being used to unload plastic pipe
BPR Cadillon GTA 82 from about 1980.
The conveyor from the main crusher in the pit to the processing plant is more than two miles long. In between, near the plant end of the conveyor, is the conical blue steel structure of the stockpile. The basic frame of this structure was erected in a tri–crane lift that involved 77 tons (typical lifts here are around 33 tons) of steel being picked and placed at a 20 foot radius.
From the stockpile the material will be conveyed to the secondary and tertiary crushers and to the screening plant before being transferred to the wet side of the process.
STAY CONNECTED
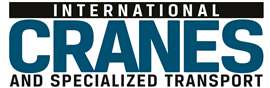
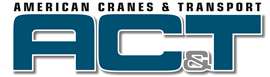
Receive the information you need when you need it through our world-leading magazines, newsletters and daily briefings.
CONNECT WITH THE TEAM
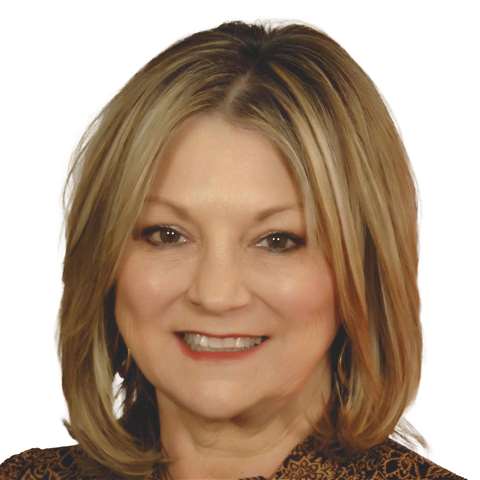
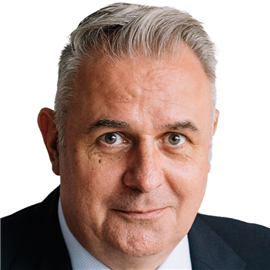
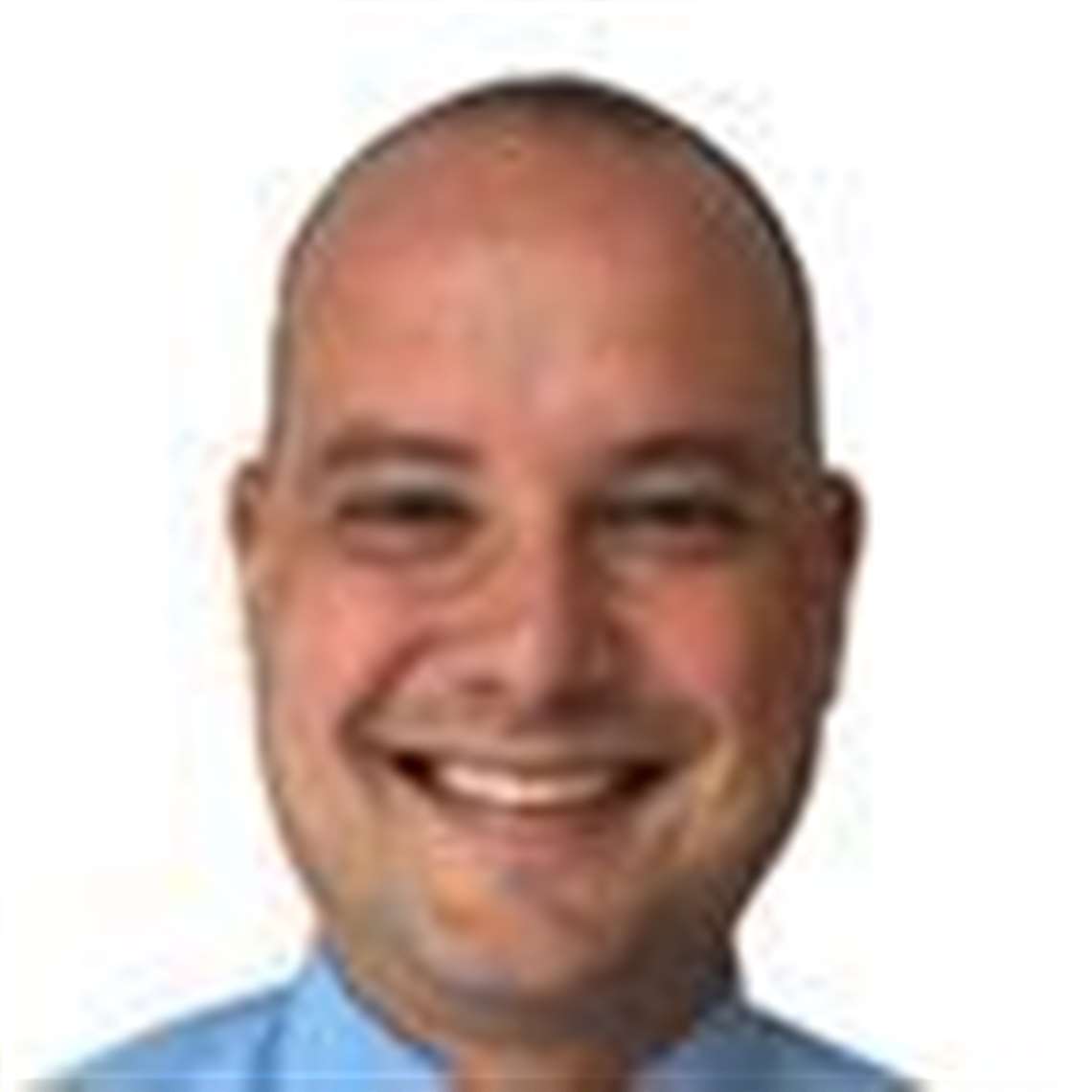
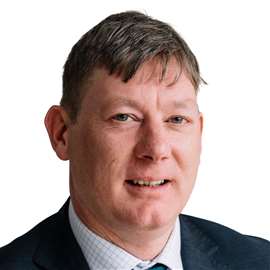