Necessary gadgetry
20 March 2008
With very little effort, crane owning companies looking to update the Load Moment Indicator and other operational aid systems on their equipment can do so without stealing major production time, whether an OEM installation or retrofit. The end result can be an upgraded system that is long-lasting and that can increase jobsite productivity and safety.
Computerized operational aids are staples on new cranes, enhancing productivity and safety on many levels with the ability to monitor load capacities safely and accurately, and to monitor the cranes’ operating system. Indications on these devices consist of warning and/or monitoring types. The warning typically consists of an audible and visual alert, while the monitoring will communicate when a crane has reached or is near its capacity limit, with readings of the load or angle, radius, as well as length or load moment.
The latest trends in this industry have customers turning towards advanced technologies, such as CAN-based systems wiThengine, transmission and event recording features. All these features allow the system to manage data for the entire machine.
Manufacturers of crane operational aids contend their respective systems are easy to install and that they are user friendly as well. Wayne Mitchell, managing director of 3B6, says user training requires very little time. The company offers turnkey solutions for OEMs, with a complete components range, including CAN BUS sensors, sized dashboards and control panels and more.
“We focus on user friendly operation,” he says. “The system informs the operator of the condition of the machine, as well as self-diagnostics.” For system upgrades, software is easily the typical solution, which can accommodate the older products, as well as the newer systems.
“I will indicate 3B6 can provide a complete in-cab solution to any OEM,” he says. The company's View Tech system features a load limiter, a movements speed modulation, boom section extension sequence, load table management, and an area limitation reading on a color display. Th is system can be used on mobile cranes and reach stackers.
The installation process varies betwe OEMs and retrofits. For the former, the proc is typically a two to three day project. F retrofits, the upgrade can be done in less tha half a day. Furthermore, end users for the mo part, can install the systems themselves.
“Ninety-eight percent of our systems ar installed by the end user,” says Jeff Crane vice president with Cranesmart Systems Inc “Engineering crane safety instrumentation to be simple for the end user also accomplishes robustness in the tough work environments.”
The company is a specialty manufactu of load monitors, anti two-block system LMIs, wind speed indicators and boom angle indicator systems for all cranes and other winch line applications. The company says that more than 26,000 systems are in use globally.
Once installed, getting the end user up and running is easy. Most systems have a start-p screen that walks the operator through e operations process.
“An LMI display should be kept simple to ensure the status of the load on the hook can be recognized with a glance,” says Crane. He warns first-time users and those unfamiliar with its systems to pay attention to the arms provided at the panel. “Too often tors ignore [those] and sometimes g operator aids.” wn force in development of operational Hirschmann Automation and Control Inc. (no longer known as PAT in the market), which according to Marketing Manager Gary Peck, has a long history in the crane market working with OEM and retrofit customers. Hirschmann offers an extensive line that includes the PRS 80 EZ, a design that allows for monitoring single or multiple sensor inputs including combinations of load, anti-two block, boom angle and wind speed. The inputs are shown on a large, backlit, graphic display, which is capable of showing up to seven sensors at one time.
Most recently, the company has developed a newer system called Hirschmann Maestro, which is a LMI upgrade system. The company has been installing LMI systems since the late-1980s, and for those older models that need an upgrade, the Maestro provides a solution for der systems that need parts or repair. em includes a new console, central unit ssure transducers, with many of the sensors and components incorporated new system. The company says the advantage of the product is that it require re-calibration because of the software. wireless out-of-the-box systems can be d in an hour to three hours and depends w many sensors are being put on,” says egarding the retrofit installation. “The wired systems require more installation et up time; a couple hours to a day.” th 20 dealers in North and SouTherica, Hirschmann's reach is large-scale. st locations offer training schools in ir territory for crane end-users on topics ch as maintenance, troubleshooting d system operation.
STAY CONNECTED
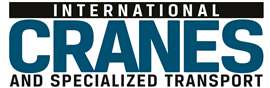
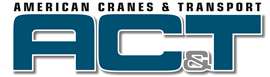
Receive the information you need when you need it through our world-leading magazines, newsletters and daily briefings.
CONNECT WITH THE TEAM
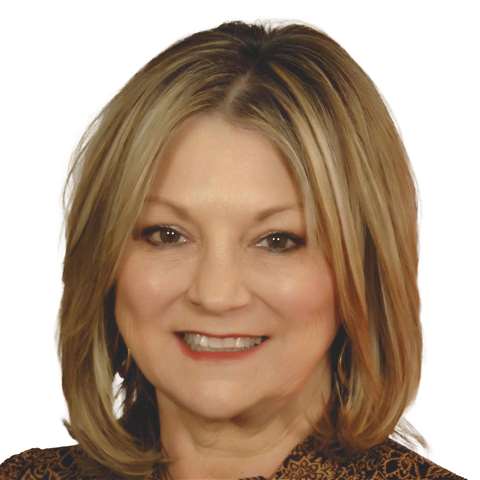
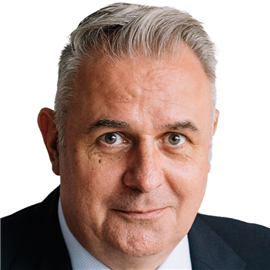
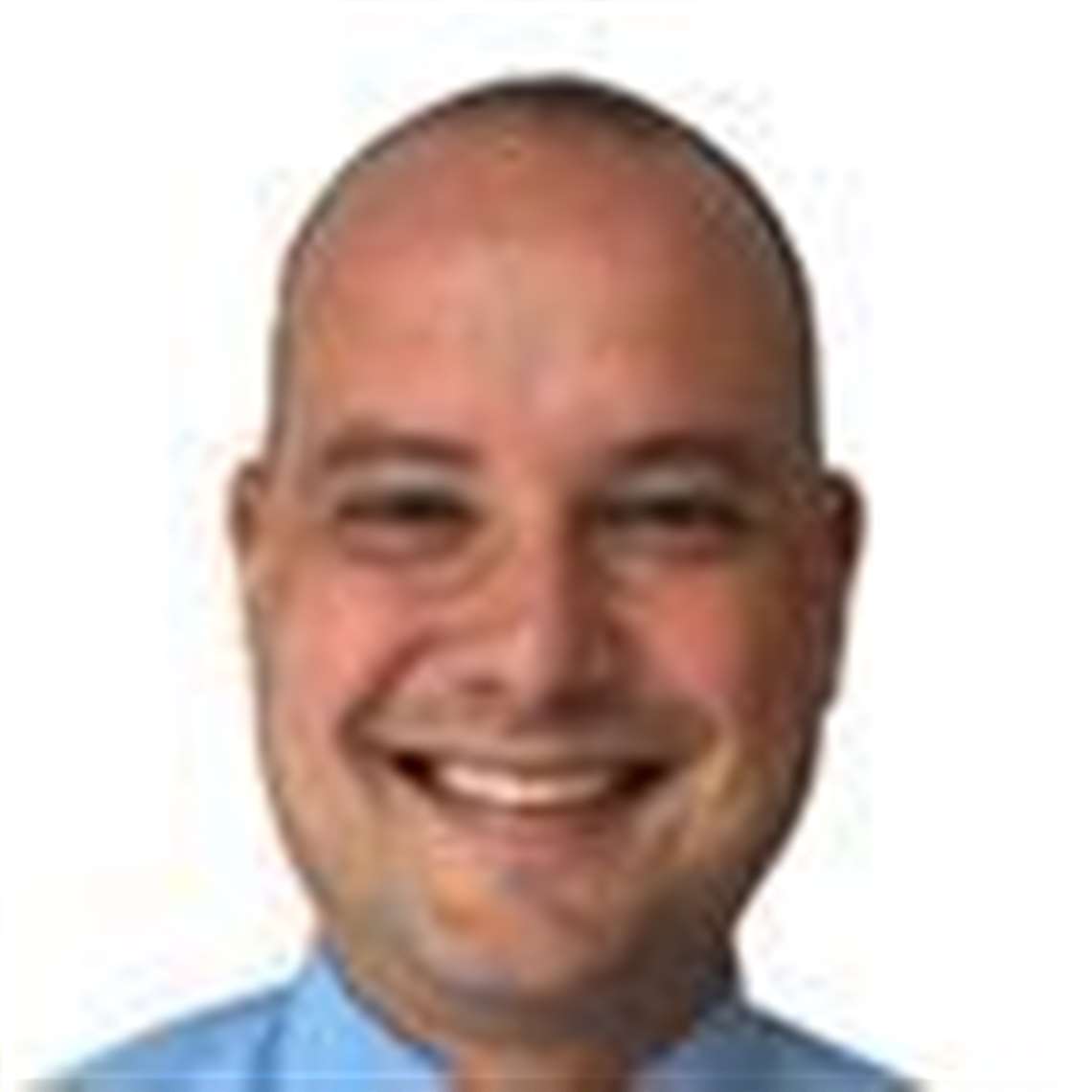
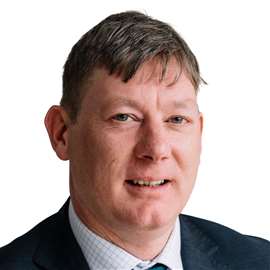