News from below the hook
04 September 2019
Technologies in below-the-hook rigging gear are constantly advancing. ACT invited below-the-hook makers and distributors to share their product and application news.
Tuff-Ash sling armor
Tuff-Ash sling armor takes sling protection to greater heights with high performance Dyneema sleeves.
This armor offers exceptional resistance to cutting and abrasion by protecting load-bearing slings from edges, corners and abrasive surfaces, the company said. Sling Armor is designed for use with roundslings, web slings and synthetic slings, and is manufactured from Dyneema fiber. Dyneema is used by some of the largest crane and construction companies in the world. The company claims it is seven times lighter than steel at the same strength and diameter.
Although no material is cut proof, Dyneema offers a level of cut protection that is unprecedented in sling protection textile products, the company said.
“Tuff-Ash sling armor has proven to be the ultimate sling protection through quality testing on Ashley Sling’s 1.8-million-pound test machine,” Ashley Sling said. “Additionally, the sleeve’s lightweight material offers exceptional flexibility, which is crucial for handling large and delicate rigging loads.”
HPZ Extreme Lift Roundsling
The HPZ Extreme Lift Roundsling is a high-performance Sling made from a custom blend of HMPE and Aramid Fibers. Its superior strength-to-weight ratio promotes easier handling, transporting, and rigging, according to the company.
The fibers are enclosed with Ashley Sling’s Tuff-Ash two ply red-outer and contrasting yellow-inner jacket, which help the user to spot any possible snags and tears. Additionally, it has seamless edges to help prevent rupturing, and it can also conform to the shape of a load allowing an easy grip. The HPZ Extreme Lift can be manufactured in either endless or eye and eye configurations.
ACS Industries
East Hazelcrest, IL-based ASC Industries fabricated a 331-ton capacity lifting beam along with the Slingmax high performance Twin Path slings to pick the concrete girders being made for the support structures building the Tappen Zee Bridge in New York. The combination of the low-profile lugs and lightweight twin path slings made the pick much more cost effective and safe for the contractor, according to Tony Fastuca, vice president, ASC Python America.
“Our engineering department made sure the lugs were proof loaded in the position of the actual lift and the twin path slings as well were proof loaded to twice the working load,” Fastuca said. “For many of the projects across the U.S. and abroad, ASC Industries has provided this type of service to a variety of industries, from energy to the military, that sometimes exceed the requirements set by OSHA - ANSI. ASC Industries is honored to be part of the building of the Tappen Zee Bridge, and a proud member of the SCRA.”
The Caldwell Group
The Caldwell Group manufactured a customized lifting device that is being used during assembly of cryomodules at the Fermi National Accelerator Laboratory (Fermilab) in Batavia, IL. The project was awarded to Caldwell distributor John Sakash Company, also based in Illinois.
Fermilab builds SSR1 cryomodules (sections of modern particle accelerators) for its Proton Improvement Plan-II (PIP-II), an essential upgrade to the Fermilab accelerator complex. The Caldwell system, specified red in color, offers multiple configurations and can be raised and lowered with surgical accuracy by hand-wheel, an operational requirement of the end user.
The centerpiece of the solution, which meets the ASME B30.20 BTH-1 standard, is a 6,000-pound capacity main beam, while two 1,500-pound extension beams can be added at either end. All three beams span 371 inches, but it will be adapted to suit various assembly processes. Cryomodules are positioned on a track directly beneath the beams and tooling is utilized to accurately position components beneath various lifting points.
“Fermilab provided very detailed specifications for the lifting device, with the principle challenges for the contractor being low headroom, uneven flooring, and critical stability,” said Pete Sakash of John Sakash Company. “Our system provides a foot or so of adjustability but in use they’re only really going to need to utilize about 6 inches of that.”
The project is notable for the accuracy of assembly that had to be accommodated, according to Dan Mongan, a product development specialist with Caldwell.
“Fermilab is a facility at the sharpest point of scientific investigation,” Mongan said. “Using threaded rods, the hand-wheel can position the beams to millimeter accuracy. Only the columns remain rigid as the system provides Sakash’s customer with every possible lifting point cryomodule assembly will require.”
At the heart of the PIP-II accelerator is a technology that provides for a highly efficient way to accelerate particle beams. Superconducting radio-frequency (SRF) cavities make it possible to accelerate intense proton beams to higher energies in relatively short distances. A string comprising several of these cavities nestles in a cryomodule, which bathes them in liquid helium and keeps them at the ultra-cold temperature that is key to their operation and efficiency.
John Sakash Company and The Caldwell Group are currently working on two additional lifting equipment projects for the Fermi National Accelerator Laboratory.
Holloway Houston
A leading supplier of lifting products and services in Houston, Holloway Houston launched the world’s largest load testing bed, a milestone in the proof-load testing, break testing, and cycling testing industry.
The testing bed provides rigorous proof-load testing and has a testing capacity of up to 10,000 tons.
“This is one of the many efforts by HHI to bring the advanced testing equipment to meet the stringent safety and testing regulations for various industrial lifting products,” the company said. “The company had the world’s largest test bed of 5,000 tons capacity before which still continues to function. They also have a 3,000 tons capacity test bed and more than 12 small test beds available throughout the facility.”
The new testing bed is specially designed to help verify engineering models, prototypes, calculations, and software specifications for various equipment built by industries like oil and gas, power and energy, marine, nuclear, manufacturing, petrochemicals, and mining. Along with the testing capacity of 10,000 tons, the proof-load testing bed has 12-foot strokes.
The testing bed provides manufacturers with the ability to complete almost all the testing indoors. The easy-to-handle controls allow users to set up testing parameters, determine the capacity of the equipment under inspection and get the complete test report quickly. The advanced safety features incorporated in the testing bed design allow manufacturers to test their products under perfectly safe conditions.
Cortland Sling
During an upgrade at a steel plant in Indiana, an overhead bridge crane – in operation for more than 20 years – had to be removed to allow for a new model. The bridge crane had to be safely removed in two large sections using a crawler crane. It required basketed rigging, and some contact surfaces were extremely sharp. As the lift was to be performed at 85-feet, this was a key hazard for the load-bearing ropes.
The ropes used would have to be strong enough to lift the structure, be highly durable and align with the correct size shackles to accommodate D/D ratio limitations. It was essential to understand where the connection points would be and adjust the calculations, accordingly, helping to know which size of rope to use. Cortland Company’s Plasma synthetic rope slings were selected to eliminate 18,000 pounds of the weight from the rigging plans versus traditional wire rope slings.
The assembly included eight 3-inch by 25-foot grommet slings, attached from the crane hook to the shackle. A series of eye-to-eye slings were also used. This was a particular requirement on the second lift as the eye-to-eye slings were used in a basket configuration around a rolling block, which would not have accommodated a standard rope set-up.
The Cortland sling solutions reduced rigging time from 20 hours to five hours during this one-day project, which was six to eight months in planning.
Western Sling
Western Sling recently debuted its Double Grommet Rope Slings made of 12 strand HPME fiber. The new sling is designed to replace heavy, messy wire rope slings that kink and can contain broken wires.
Smaller than comparable polyester round slings, Western Sling chose to have the rope dyed Hi-Vis green to make them more visible for safety. They are incredibly hard to cut and resist abrasion better than other synthetic materials, the company said. These slings are available in 1/2-inch, 5/8 inch and ¾ inch diameters and are 8 feet in length.
Yale Cordage
Yale Cordage LOUPS are currently being used for the Weeks Marine heavy lift project at Pier55 along the Hudson River in Manhattan. Yale Cordage LOUPS were chosen by Weeks Marine based on their light weight, compact, high strength design, according to Yale Cordage.
The company’s wish list also included a non-marring soft synthetic sling to handle the weight of the large piles being driven into the sea floor. Yale LOUPS fit that description to a tee. Using a series of LOUPS hitched around the pile, the customer could easily achieve their tasks set forth by their customers. These LOUP Model 13N10 50 Ton slings were just what the doctor ordered.
LOUPS are far lighter than steel or conventional round slings. They are made up of just one continuous looped piece of rope which has been end-for-end spliced to itself. The diameter of the LOUP core and the number of wraps vary by the tensile strength of the LOUP Yale is building. Since the strength element is small, the D/D ratio (or bending radius) is improved. Simply put, LOUPS are less affected by sharp bending radii than larger ropes of comparable strength. LOUPS can be produced as small as 3 inches in length and as large as 5 million pounds tensile.
Tandemloc
Tandemloc has expanded its “build your own spreader beam” system by adding a telescopic option to the End Cap Kit product line. Where once Tandemloc End Cap users were stuck with fixed and several lengths of pipe in order to create various sized spreader beams, now they can purchase a telescopic pipe kit. The telescopic kit provides for an incremental adjustment of a length of pipe with end caps every 6 or 12 inches, depending on size of beam.
“What makes this particular product expansion so outstanding is the end user’s ability to make incremental adjustments quickly out in the field, something that no other modular or kit style spreader beam is currently capable of doing,” said Tandemloc President John DiMartino.
Tandemloc also created and revised its End Cap App to include the necessary data information to confirm whether the user’s End Cap Telescopic Kit will meet the lift’s requirements. The new App is one of a kind and is available to all Tandemloc customers – providing their safety departments with an evaluation of the lift specifications against their end cap system size. The app can be used with a smartphone, iPad, or desktop computer. A printable data sheet is available for every lift possibility.
Tandemloc AT14 Spreader Beam Series
Tandemloc has also introduced the AT14 Spreader Beam series. This series is Tandemloc’s biggest product line yet with some 180 beams offering a range of minimum and maximum lengths in increments. Capacities vary from 2,000 pounds WLL to 100,000 pounds with top rigging included.
Modulift safety warning
Modulift provides technical expertise alongside the manufacture and supply of specialist lifting equipment, including spreader bars. The company has become aware of other brands launching products that they say are compatible with the Modulift spreader range. However, Modulift warns that this is not the case.
The company said that not all spreader beams are the same and if another brand is combined with a Modulift product, the Modulift certification will no longer be valid.
“This means that anyone purchasing this type of product must get it proof load tested to ensure the product adheres to safety standard,” said Modulift’s Techinical Director Sue Spencer. “This is for every lift where Modulift products are combined with another brand. Safety is at the heart of everything we do here at Modulift. We feel it’s our duty as a respected brand in the lifting industry to let everyone know the issues that arise when combining products.”
STAY CONNECTED
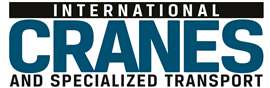
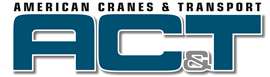
Receive the information you need when you need it through our world-leading magazines, newsletters and daily briefings.
CONNECT WITH THE TEAM
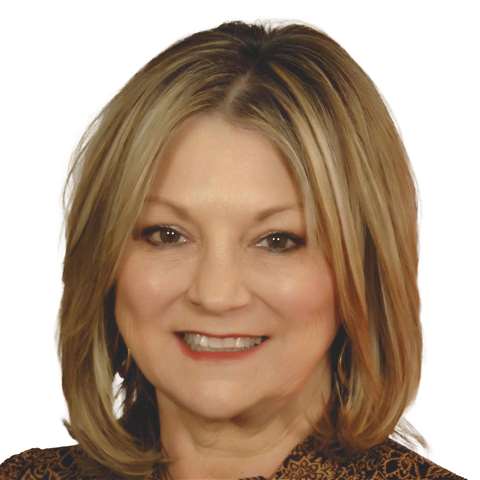
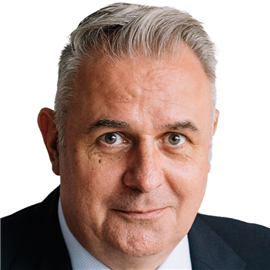
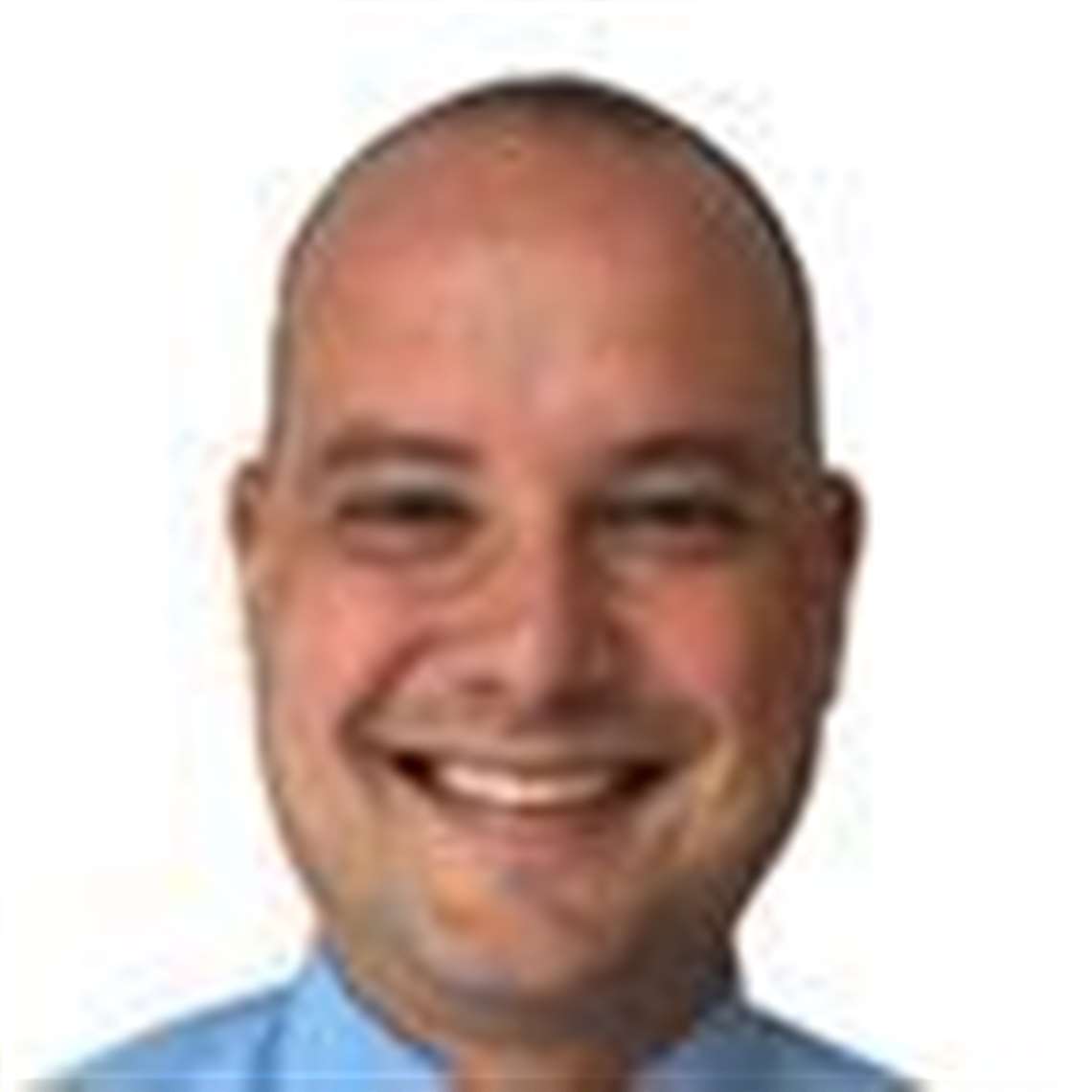
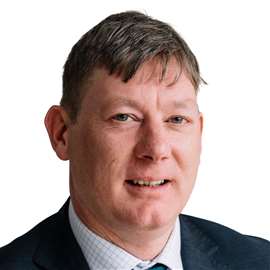