Nuclear plant challenge
20 March 2008
The Detroit Edison Co. recently replaced two moisture separator reheaters at its Fermi Nuclear Power plant. The vessels are each 113 feet long and individually weigh 300 tons. The existing vessel locations and the location for the new vessels are deep within the structures and piping of the power plant. Traditional methods for extraction and installation would mean extensive removal of plant equipment and structures, and would need an extended plant outage to accomplish the work.
A standard approach, and the approach used during the plant construction, was to install each of the vessels in two half sections and to join the two by welding and then install piping to fit. In this case, however, it was time and cost prohibitive to remove the previously installed piping, and the vessels were housed inside reinforced concrete structures.
The project was further complicated by the fact that these components are within a radiological controlled part of the plant and were not accessible when the plant is operating due to a high radiation environment. Therefore, the new vessel needed to be made and moved to fit the existing plant within a very tight tolerance.
To accomplish the work the project team, which included Barnhart Crane & Rigging, developed a one-piece installation approach. This unique approach provided the shortest plant outage duration with all outage activity completed in a 35 day window. This saved more than $10 million in replacement power cost.
However, moving such large components from the fabrication facility in Oklahoma to the plant site in Michigan, and then moving those large components within the plant with clearances of less than two inches and to a final fit-up position within 1/8 inch tolerance was a formidable challenge. During initial planning for the project, the one-piece option was determined to be impossible. The team did not accept this and went back to the drawing board, this time employing innovative methods and a unique project approach to implement the one-piece approach to achieve their goal.
First, the existing plant equipment was meticulously mapped using laser surveying technology. This information was translated to a 3-D design tool. This produced a design tool that gave the team the ability to design and plan to the needed tolerances. A virtual construction plan was developed with 3-D animation, simulating the heavy rigging path and proving that a one-piece approach was in fact possible. The design data and the laser surveying tool were then used to first design the exact dimensions for the new vessels, including nozzle locations for piping up to 48 inch diameter, and then to confirm through exacting measurement that the vessels were a fit for the plant equipment.
The unique construction approach included application of a full array of specialized equipment. A special rail car was adapted to move the new vessels from Oklahoma to Michigan. Barnhart's modular lift tower and integrated slide system was designed and erected at the site to move the new vessels from the rail car up to and inside the power plant. A unique cantilever lifting beam was used to remove large concrete wall sections to give access for the new vessels. Once inside the plant, a hydraulic slide system was used to maintain positive control and to ease the vessels into their cubicles to the exact location required. The seamless hand off of the MSR from the module lift tower to the plant overhead turbine bay cranes further enhanced the overall project safety.
The project met all of its objectives, with more than 300 building trades' employees participating. The project was completed with no lost time and no OSHA recordable injuries. The vessels were a perfect match to the plant piping and the 800 required pipe welds were completed within the 35 day planned window.
The project demonstrated the value of exceptional planning, exceptional teamwork, and application of innovation to develop and execute a first of a kind project to achieve best in class results.
STAY CONNECTED
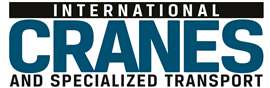
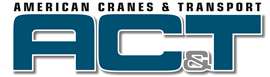
Receive the information you need when you need it through our world-leading magazines, newsletters and daily briefings.
CONNECT WITH THE TEAM
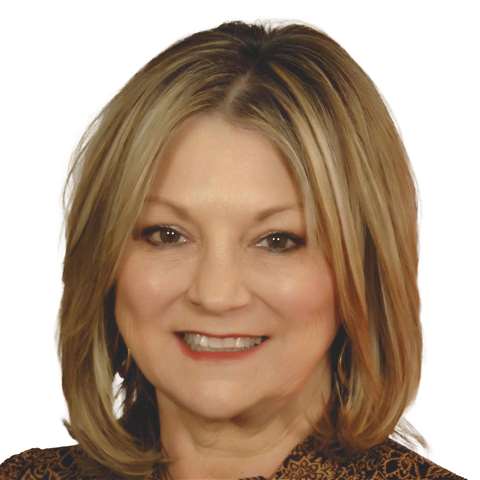
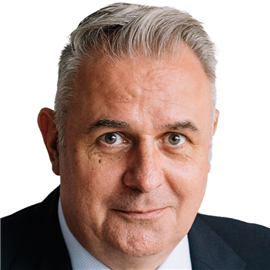
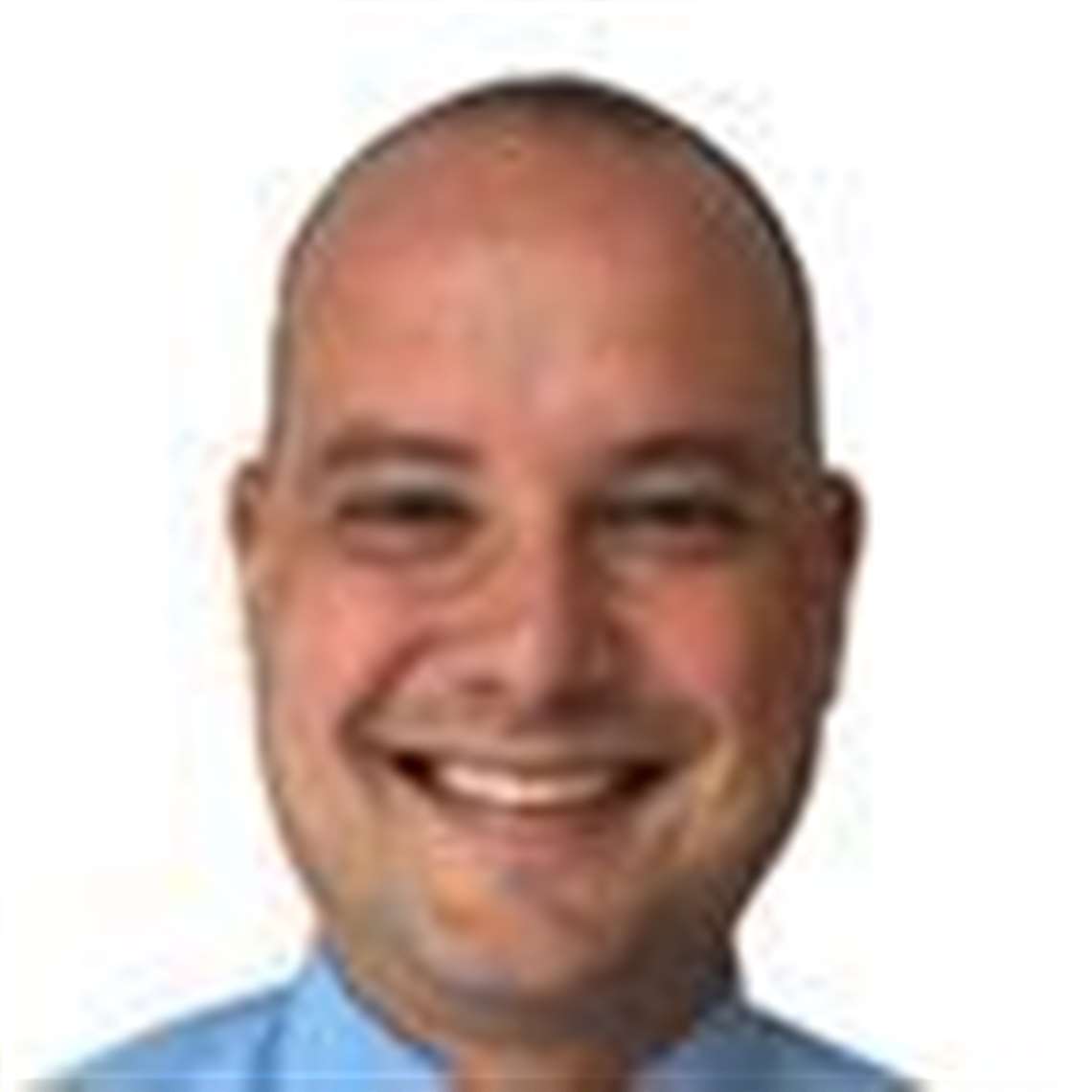
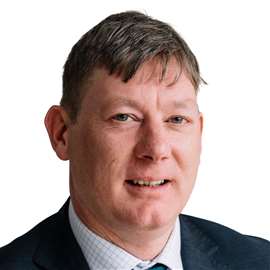