Read this article in French German Italian Portuguese Spanish
Power towers 3: large tower cranes for wind turbine work
28 January 2025
The third and final part of an epic series on new tower crane concepts for wind turbine installation written by Crane and Transport Briefing special correspondent and global tower crane authority Heinz-Gert Kessel
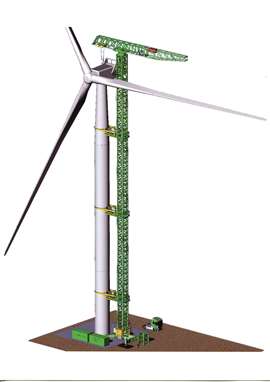
Having looked at more or less conventional tower crane designs aimed at wind turbine erection, this final part of the series examines an example of what may be seen as a more unorthodox concept.
By their nature wind farms are frequently in remote locations where it is difficult to gain access. To mitigate this, it helps to reduce the amount of equipment that needs to be transported to site and then assembled or installed, dismantled and taken away again. A significant reduction in the transport volume for a wind turbine installation crane can be achieved by the option of attaching the crane to the wind turbine tower that is under construction.
Following this principle is a patented, state-of-the-art crane design developed by Skyrex, based in Sweden. The modular system allows an under hook height up to 210 metres. Lifting capacity is 150 tonnes at a 9 metre radius. Maximum outreach is in the 16 to 21 metre range according to boom configuration.
The idea of attaching an external climbing tower crane to the wind turbine tower under construction is not new. Nor is the idea to use a self-climbing design to dramatically reduce rigging space requirements. What is different, however, is the way the crane mast can be anchored to the wind turbine tower in a flexible way. The aim of this is to reduce, as much as possible, any load transfer of the attached tower crane into the wind turbine tower. This is because it has a huge design impact for the wind turbine tower designers. Most prefer, in all circumstances, a self-supporting i.e. free standing, crane concept.
Unique features
With its revolutionary new and very specialized tower crane concept Skyrex overcomes these previous barriers. Two patented design features of the crane are unique, as follows:
1). The way the tie-in support is designed to fix the crane at any part of the wind turbine tower hull without needing a structural bolted connection devised on the wind turbine tower itself.
2). The way the crane is balanced with and without load to avoid any bending forces on the crane mast system and therewith side loadings to the wind turbine tower.
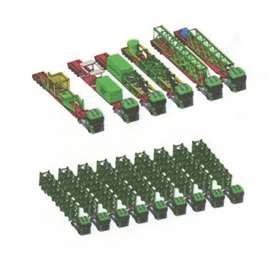
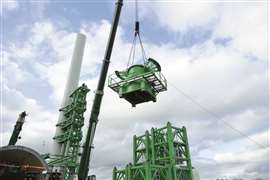
The tie-in supports are designed as three frames surrounding the crane mast. These frames can move freely on rollers alongside the mast chords, guided with the assistance of an external hoisting winch at the top of the mast. Clamping assemblies to grasp the tower structure are integrated in the connection beams to the wind turbine tower.
This means when climbing the crane to the next obligatory level for tie-in support, there are always at least two bracings, each providing two flexible arms and rope-operated clamping devices pressing plates on the turbine tower’s external surface to hold the crane mast. By gripping the wind turbine tower at two levels, one bracing unit is free to be relocated at any desired position of the wind turbine tower before the crane will be jacked.
Getting the balance
The second major improvement are the unique balancing devices in the design of the upper crane. Above the slewing platform the boom can be moved forwards and backwards with a rack and gear system. In addition, at the same time the counterweight travelling inside the boom can also be moved back and forth.
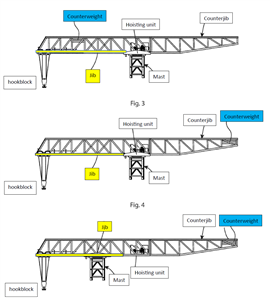
To some extent this concept can be traced back to the famous SGME K-series cranes of the 1960s. A rope system allowed the counterweight position to be changed in correspondence with the jib movement. In the case of the Skyrex, however, the saddle jib design principle with movable trolley, and the independent operation of movable counterweight and boom, are major improvements. They are made possible by incorporating modern electric steering and monitoring devices.
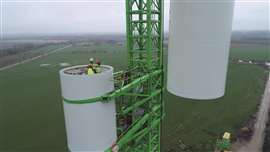
In the wind turbine installation application, the boom is retracted close to the tower for heavy loads. At the same time the counterweight moves to the back of the boom. For low weight, the counterweight moves to the front of the boom and for a longer outreach and small weight, the boom moves forward while the counterweight is moving in a way to balance the load moment.
It means the counterweight and boom are simultaneously movable in opposite directions relative to the crane’s mast. The advantage of this patented upper crane design is the possibility to balance the crane depending on the load being lifted and the position of the boom with respect to the mast.
The boom is made up of two square sections designed for easy transport. Inside the boom is the hoisting winch.
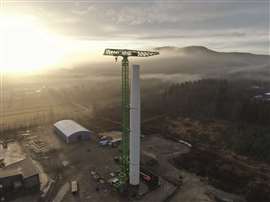
Making the climb
To achieve a safe climbing procedure the crane is designed to be climbed from the bottom. Additional tower sections are inserted in a climbing cage surrounded by four simultaneously operating hydraulic jacks. It means no dangerous jacking operations need to be carried out high up in the air. To keep the crane connected with the wind turbine tower during the mast jacking operation, the tie-in support framework is equipped with rollers moving alongside the mast corners. An important element of the crane design is that it is less sensitive to wind than traditional free standing top climbing tower cranes of European design. The mast itself is made up of identical monobloc sections connected by a screw and nut clamping arrangement along a vertical axis and it is quick to install.
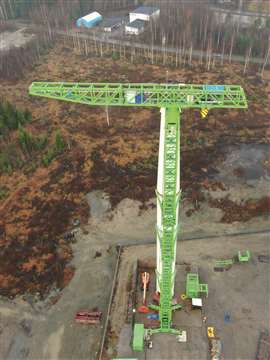
The whole crane can be transported on just 15 standard trailers or 40-foot containers. It means a 75 per cent reduction when compared to what is needed when using a conventional mobile crane for wind turbine installation. Using high strength steel minimises the weight of the crane.
To reduce installation time the tower crane base section is transported as one unit with folding outriggers. These can be hydraulically jacked to allow removal of the standard trailer from underneath the portal shaped crane base. Initial rigging of the crane only requires a medium size truck crane.
When the crane starts climbing it is self sufficient by using its own hook to handle the additional mast sections to be inserted at the tower base. Depending on the power source, it can be operated electrically or with a power pack and by remote control.
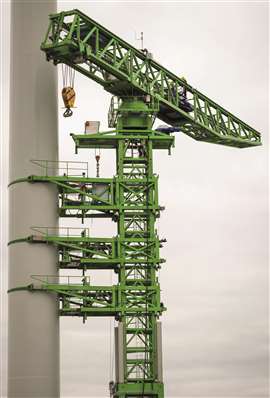
Scandinavian beginning
In 2021 Vestas joined as an active partner with Skyrex. Its first test operations were successfully carried out in Denmark and Sweden.
The technical features of this crane in conjunction with the low transport costs are remarkable. It is a very specialized machine and, as such, it is restricted to wind turbine installation jobs. Unlike all the other tower crane concepts discussed in this series of three articles, no transformation of the Skyrex into a heavy lift tower crane for general construction work is possible.
We will have to wait and see if such a niche market crane will be accepted by crane rental companies or if it will remain a prototype. The other cranes featured in the first and second parts of this report allow simple adaptation to heavy lift jobs outside the wind turbine installation industry. Their design-integrated features for fast installation and transport will become standard for sophisticated heavy lift tower crane design in the near future.
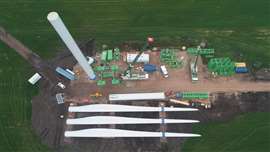
STAY CONNECTED
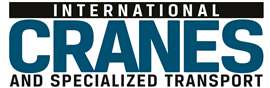
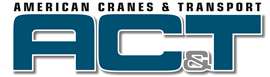
Receive the information you need when you need it through our world-leading magazines, newsletters and daily briefings.
CONNECT WITH THE TEAM
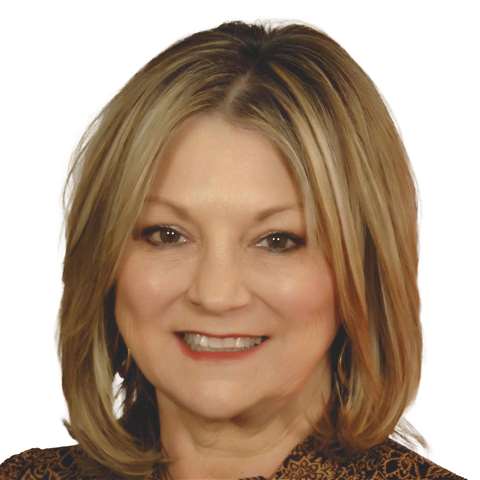
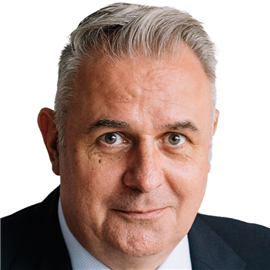
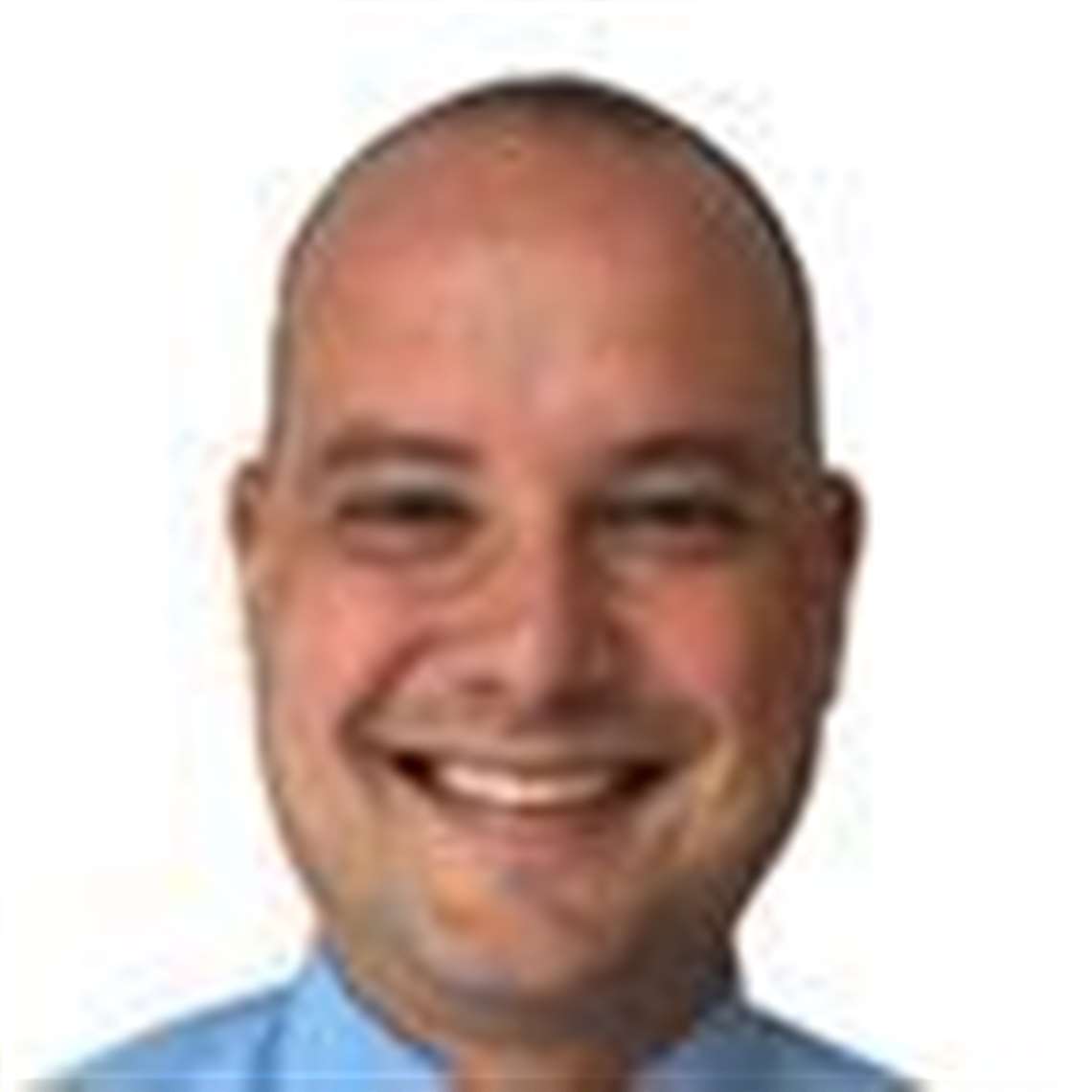
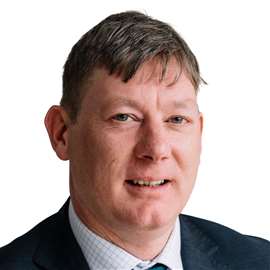