Precision-plus rigging
20 March 2008
When it was put in place decades ago, the 400 ton methanol reactor was probably a breeze to install at the Valero Refinery in Delaware City, DE. Back then, it stood alone in the middle of a paved draining area. But the refinery has seen a lot of development since that time: A heat exchanger was snuggled up closely to the reactor it served and concrete structures had been erected on three of the reactor's four sides.
In 2006, the plant was to be decommissioned, with the first task the removal of the reactor and its relocation to owners in Trinidad. Atlas Industrial Contractors of Columbus, OH was contracted for the project. After surveying the job, the Atlas team concluded that the reactor was so tightly surrounded by obstructions that the use of cranes to lift the unit up and out was impossible. They determined the job could best be accomplished using a tower lifting system, specialized tailing equipment, and trunnion lift links.
Using a tower lift system owned, operated, and fabricated by Atlas, and a small assembly crane supplied by United Crane and Rigging of Baltimore, MD, the tower sections and header beam assemblies were rigged to rise to more than 70 feet top elevation. The header configuration was two W36 by 359 by 50 foot beams. The lifting was done using four L-100 PSC strand jacks, each with 108 metric ton capacity. For the tailing equipment, Atlas employed two legs of its 500 ton Lift Systems hydraulic gantries supporting a W38 by 475 by 50 foot header beam.
The plan was that as the tower lifting system raised the reactor, the gantry tailing equipment provided the forward movement to “walk” the bottom of the reactor away as the top moved through its rotation to horizontal and the lowering process continued. At the same time, the reactor was raised to keep the bottom away from the ground as the top was lowered, then raised it to bring the entire reactor to elevation before lowering it into shipping saddles. As the top of the reactor was lowered, there was only inches of clearance between it, the concrete structure immediately adjacent and the reactor's heat exchanger and protruding nozzles.
To assure those inches were precisely accounted for, Atlas called on the engineering expertise of Ruby and Associates of Farmington Hills, MI.
Atlas designed and fabricated several of the components needed for the job, including two 180 ton trunnion links to attach the reactor's trunnions to the strand jacks for lift and rotation. Also, a unique tailing fixture to pass beneath, and be welded to, the reactor's skirt had to be fabricated to accommodate Atlas’ tailing equipment and reactor design loads, and a 100 ton lifting link to attach the tailing fixture to D-rings on the 500 ton gantry's header beam. All rigging attachments and fixtures were designed with a safety factor of 5:1 to account for any unknown or unexpected variables.
Atlas’ first task was to assemble the gantry track. Two 45 foot sections of the 800 ton heavy duty gantry track formed the tower lifting system's base. They were joined to an additional 30 feet of 400 ton gantry track to allow for a common runway for the tailing equipment. Due to the 6 inch difference in the height of the rails, and because the whole of the track passed over a bowl-shaped draining area, timbers were placed and shims employed to level the entire 75 foot length of the tower base and track. Engineers determined that the best way to stabilize the lifting tower was to bolt its bases directly to the 800 ton gantry track sections. The timbers also helped distribute the load from the tower.
To test the equipment, the reactor was lifted one inch above the foundation it rested on. Atlas personnel quickly determined that the weight of the reactor was in excess of the estimate provided by the owner's drawings. The tailing fixture was then inserted beneath the reactor's skirt, and the reactor returned to its former position on its foundation and support cribbing, as the lift entered a built-in hold point.
An engineering review was conducted to determine if the actual weight - 384 tons versus the anticipated 360 tons - was still within engineering and safety parameters. It was, and a “go” was given to continue.
The next day, the reactor was once again raised from the foundation and the Atlas crew, clad in are-retardant Nomex jump suits, completed the full penetration welding of the tailing fixture to the reactor's skirt. But then, unexpectedly, the wind started to blow. The lifting assembly and bracing had been engineered for maximum winds of 20 mph. With wind gusts clocked at 55 mph, Atlas returned the reactor to rest on the support cribbing and tailing fixture and work was secured for the day.
The next day the lift resumed and the reactor was raised from its foundation for the last time. As it was raised, the tailing equipment moved slowly away from the base of the tower lifting system, keeping the vessel clear of the ground and slowly raised the bottom as the top was lowered and rotated horizontally.
During this critical time, the need to keep the reactor trunnions and tower legs in a plumb attitude was closely monitored by Atlas personnel using precision theodolite instruments. With an out-of-plumb tolerance of only three degrees, successful coordination between the tower system and tailing gantry operations required close communications between the various Atlas teams on the project.
With a start of 7 a.m., by 1 p.m., the lift and rotation were complete and the reactor lay securely in its saddles ready for transport.
STAY CONNECTED
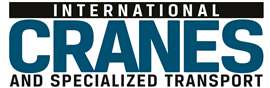
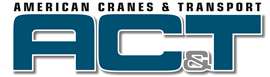
Receive the information you need when you need it through our world-leading magazines, newsletters and daily briefings.
CONNECT WITH THE TEAM
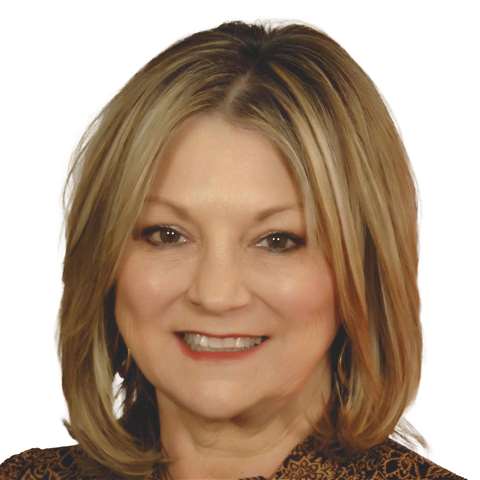
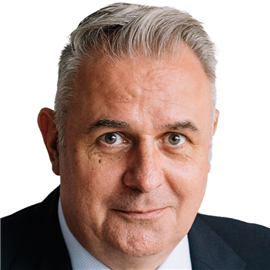
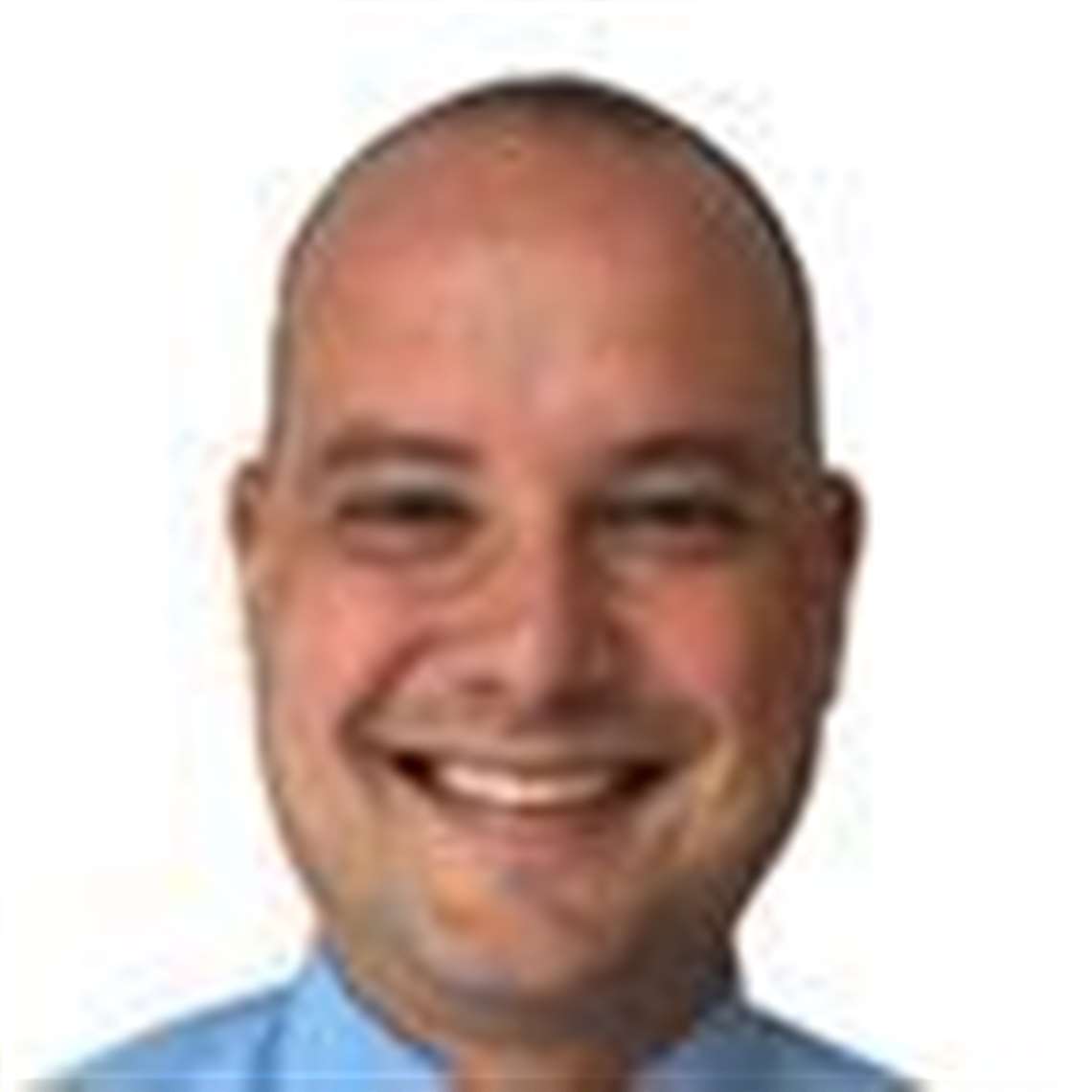
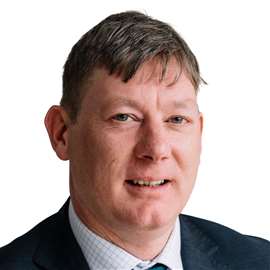