Record breaking heavy transport rail project
21 August 2023
Austrian lifting and transport specialist Felbermayr helped out with heavy transport on a record-breaking rail tunnel project in Europe. Alex Dahm reports.
At 55 kilometres, the longest underground railway connection in the world, is being built under the Brenner Pass. The Brenner Pass is a mountain pass on the border between Italy and Austria through the Alps mountains.
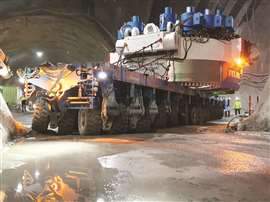
Early in 2023 Felbermayr transported two new tunnel boring machines (TBM) there and then assembled and installed them. The first part of the journey was relatively easy, by road above ground, early in 2023.
What followed was much more complicated. Driving the components, which weighed up to 270 tonnes, through sometimes very sloping and narrow tunnels underground to the assembly caverns was another thing altogether. On arrival the company then went on to assemble them.
The route from the temporary construction site, south and above Innsbruck in Austria, to the underground assembly caverns, was only six kilometres but it was challenging. It runs all the way in tunnels, three kilometres of which have a gradient as much as twelve per cent. Gaining traction is made difficult by the constantly wet mountain road surfaces.
Braking on the limit
“For these transports we used self-propelled modular transporter [SPMT] from Scheuerle with six, ten or twelve axles,” explains Markus Meusburger, project manager and department manager at Felbermayr transport and lifting technology in the town of Lauterach.
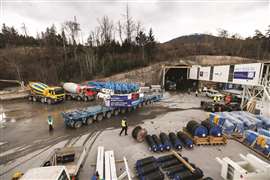
The twelve axle units were used for the two largest TBM components, weighing 270 tonnes each and with a diameter of 7.8 metres. These components were pre-assembled on the floor of the hall.
“With a total weight of almost 300 tonnes and the steep incline, we have come to the limits of the brakes. To be able to carry out these transports safely in any case, we have used a four-axle heavy-duty tractor as an extra braking vehicle. It took us about three hours for the first three kilometres with the steep incline, and five for the entire route,” Meusburger continues.
Exact manoeuvres
With around 30 transport loads per TBM, narrow junctions also had to be negotiated by each truck. “Manoeuvring with centimetre precision was necessary there, and that was probably the greatest challenge,” says Meusburger.
Where some of the TBM components were less heavy many were still bulky. “Parts of the so-called trailer are 15 metres long, 4 metres wide and 4 metres high. Because it got very narrow towards the tunnel ceiling, one employee spent five hours sitting on the load to be able to instruct his colleague who was driving the self-propelled vehicle in detail.”
In addition to the big special transport loads, there were many more journeys using smaller vehicles for small parts and assembly materials.
Putting them together
In the large assembly caverns, the parts were unloaded from the SPMT using a 1,000 tonne capacity telescopic hydraulic lifting gantry. This was supplied by Felbermayr subsidiary Wimmer Maschinentransporte. Following unloading the components were turned and set in their assembly positions.
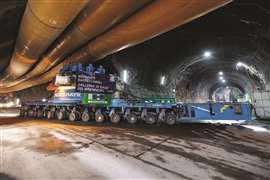
Individual parts were gradually assembled to form a large whole. Crowning glory was the TBM’s 250 tonnne cutter head with a diameter of 10.7 metres.
Assembled as one piece each of the two identical TBMs weighs 2,000 tonnes. That includes the ‘trailer’ or tail section which carries the machine’s infrastructure, for example, the mechanism to transport the spoil, electrical power transformers and controls, water pipes, a compressed air system, plus the materials used to finish or line the tunnel.
Felbermayr’s Engineered Solutions department was responsible for both planning and carrying out the technically demanding installations.
Initial delivery
As mentioned above, the initial part of the transport by road and above ground was relatively easy but still an extensive undertaking. “From the TBM manufacturer Herrenknecht in Schwanau in Baden-Württemberg [Germany], 97 road transports were required for one tunnel boring machine alone, and another 30 for the trailer, produced in Slovakia,” says Meusburger.
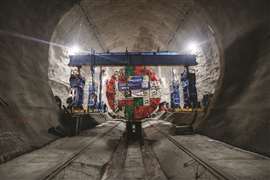
Handling the parts on the construction site was also done using a range of heavy cranes, co-ordinated by Felbermayr Transport- und Hebetechnik from the City of Wörgl in the Austrian Tirol. Felbermayr also employed some of its forklifts and aerial work platforms on the job.
At the end of May Felbermayr completed the project by transporting two railway locomotives. Each weighed around 40 tonnes and was transported on SPMT from the construction site set-up area to the underground transhipment point.
Years in planning
Meusburger spent years preparing for this major project. “We drew up route studies, identified numerous transport routes and were fortunately able to finalise the project with the client at the end of 2022.”
Felbermayr has previous experience of working on the Brenner Base Tunnel. In 2015 it delivered a smaller tunnel boring machine for the initial exploratory tunnel and transported to the cavern.
Felbermayr is based in Wels, Austria. It operates from 77 locations in 18 countries and employs around 3,000 people. Consolidated net sales were around €552 million in 2021.
STAY CONNECTED
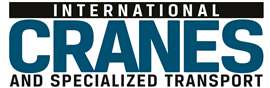
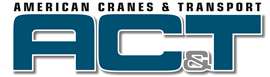
Receive the information you need when you need it through our world-leading magazines, newsletters and daily briefings.
CONNECT WITH THE TEAM
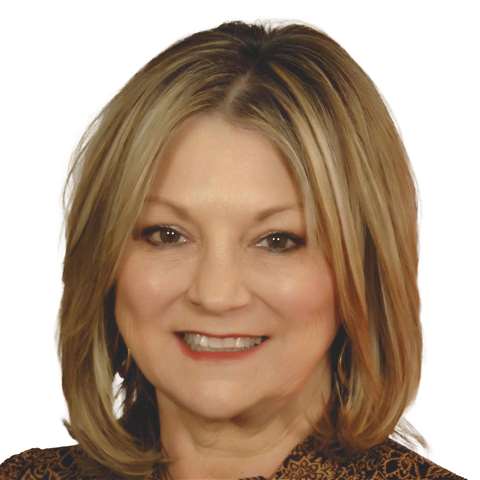
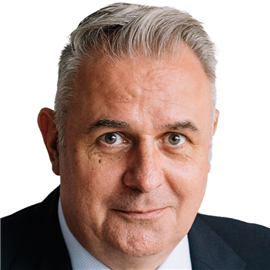
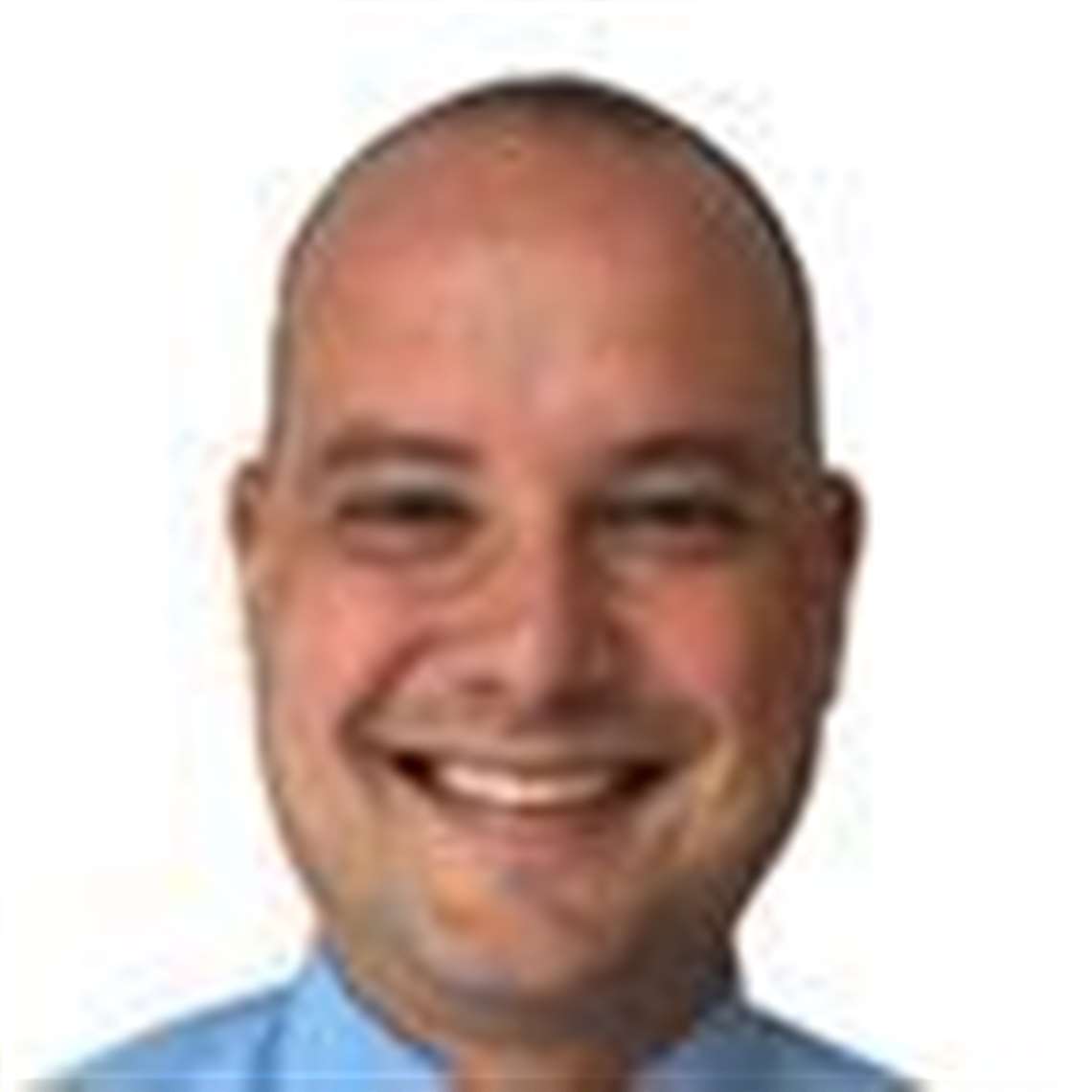
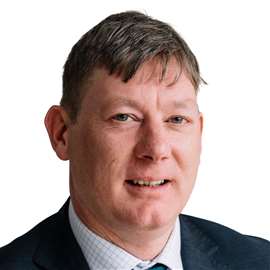