Rigging Review: Ground control
08 January 2015
In the modern Space Age, where scientific discovery remains a primary goal for NASA, a variety of aerospace, technology development and aeronautics projects are paving the way for future NASA missions.
Whether NASA is employing new technology to launch vehicles into near space or simply lifting heavy components with cranes on the ground, providing a safe setup is essential to the job. Recently, Safety Tech® outrigger pads from DICA played a small, but essential role, in two NASA projects.
“Whether you are conducting high-tech lifting operations for the government or making everyday lifts, knowing what’s under the outriggers and setting up the crane to correctly accommodate for the ground conditions is fundamental to safe lifting operations,” said Kris Koberg, CEO, DICA.
In OSHA’s Compliance Directive for Cranes and Derricks in Construction, issued in October 2014, item No. 1 on the agency’s site inspection checklist is to determine the adequacy of ground conditions beneath the equipment set-up area such as the support/foundation, matting, cribbing, blocking, etc.
“This sets the context for just how important an issue this is for crane operations,” said Koberg.
In early 2014 at the Kennedy Space Center in Florida, DICA Safety Tech® Outrigger Pads were used in a traditional crane lifting application. DICA DR422 Heavy Duty Safety Tech® outrigger pads, measuring 42 inches in diameter by 2 inches thick and weighing 93 pounds were used under a 75-ton Link-Belt HTC8675LB truck crane.
The crane was replacing roller bearing assemblies on the crawler-transporter that will carry the Space Launch System (SLS) and Orion spacecraft to the launch pad in 2018. The crawler-transporters have been used for more than 45 years, but now upgrades are necessary to increase the lifted-load capacity from 12 million to 18 million pounds to support the weight of the mobile launcher and future launch vehicles, including the SLS and Orion.
Over a series of weeks, 22 lifts were made by Jacobs Technology, which supports NASA’s SLS program. The larger lifts ranged from 4,500 to 26,000 pounds and were made with a Link-Belt truck crane. Several smaller lifts were made by a 9-ton Broderson carry-deck crane.
Jacobs Technology currently supports modifications to ground support equipment in preparation for the first SLS test flight, explained Michael Wisnom, a System Engineer responsible for operation, maintenance, and lift planning for mobile cranes.
Early in the lift planning process, Wisnom consulted with Civil Engineers regarding the maximum allowable bearing pressures for the areas where the crane would be set up. “Although most lifts were made on asphalt surfaces, we also needed outrigger pads for general lifting applications,” said Wisnom. Conservative calculations determined that the ground bearing pressure under each outrigger needed to stay under 8,600 psf.
Faced with replacing wood mats that were in poor condition, Wisnom turned to DICA after seeing an ad in a crane magazine. “They plugged our data into their FIT® performance calculator and presented us with several options. I liked that the company is family owned and proudly promotes their ‘Made in the USA’ products,” said Wisnom.
He noted that in comparison to common rules of thumb for sizing mats, DICA’s custom fitting process provided “what we needed but not more. Using the Rule of 3 or Rule of 5 would have left us with larger, heavier outrigger pads than we needed.” Safety protocols limit the weight that can be lifted by one individual to 50 pounds. Since the DICA thermoplastic outrigger pads weighed under 100 pounds, only two individuals were needed to handle them instead of the previous three with wood mats. “The round shape and TuffGrip handles were also a plus for ease of handling,” he said.
Ultimately, the decision to go with DICA over wood outrigger pads was a good one for Jacobs Technology. “DICA outrigger pads are the total package. Working with DICA and using their products is like hitting the EASY button,” he said.
Finding the best set up
Safety Tech outrigger pad features that crane users have come to rely on, such as industrial grade safety texturing and TuffGrip® handles, were equally important for the Low-Density Supersonic Decelerator (LDSD) project, which is sponsored by the NASA Space Technology Mission Directorate and managed by NASA’s Jet Propulsion Laboratory in Pasadena, CA.
The purpose of the project is to develop ways to get larger payloads of supplies and materials to Mars for long-term missions to take place there in the future. A large scientific balloon provided by NASA Wallops Flight Facility and the Columbia Scientific Balloon Facility lifted a solid-rocket powered test vehicle to an altitude of about 120,000 feet. In preparation for the launch at the Pacific Missile Range Facility, on Kauai, Hawaii, the LDSD was hung from a launch tower, equipped with two jacks and two outriggers.
DICA supplied Safety Tech outrigger pads measuring 117 inches by 36 inches by 4 inches thick, which were used under the jacks of the launch tower. The balloon launch tower is essentially a custom-built trailer with a mast at one end. Two jacks with 18 inches by 9-foot pontoons – one at the front of the trailer and one at the rear – support the 150,000-pound weight of the trailer plus 8,000 pounds of rocket weight. It was under these jacks that the Safety Tech® outrigger pads were used.
Each pontoon carried half the total load weight and had to do so without slipping. “The mats worked really well and played a big part in the project,” said Erich Klein, aerospace engineer and project leader for the Columbia Scientific Balloon Facility, which is based in Palestine, TX. “They helped distribute the load weight.”
“The textured surface of the mats provided good friction to grip the supports so that the tower did not slide around,” said Klein. Known for being lightweight, the custom Safety Tech outrigger pads weighed just 590 pounds each – significantly lighter than wood or steel alternatives.
According to Klein, the team was concerned about the ground’s ability to withstand the pressures applied to it. The launch took place on old U.S. Navy runways built quickly during World War II. “These runways were built in a hurry by pouring a concrete mix directly on the ground. We were concerned that the sand/soil mixture could not take the pressure and that the pontoons would crush through the ground,” he said.
The trailer also featured outriggers that extended perpendicular to the trailer. The side outriggers provided side-to-side stability only and did not take any load weight, explained Klein.
Crane industry solutions
Prior to the successful launch in June in Hawaii, Klein’s team from Columbia Scientific Balloon Facility conducted several test runs at a U.S. Navy Base in New Mexico. Klein was still searching for a solution to the ground bearing pressure issues when the they took delivery of the launch tower.
“It took four 18-wheeler loads to deliver all the components and mast. As the mobile cranes were setting up to assist with assembling the launch tower, I watched as the crane operator used DICA outrigger pads under the crane’s outriggers,” said Klein. “The operator said he uses them all the time and that they were indestructible.” Constructed of engineered thermoplastic, SafetyTech outrigger pads and mats provide exceptional strength and durability.
Klein called DICA to determine if the outrigger pad manufacturer had a product that could work for the LDSD application. “They were very specific about the ground bearing pressures and the desire to disperse the load to less than 30 psi. We worked through the math and calculations for ground force to demonstrate how the Safety Tech® outrigger pads would meet their need,” said Chris Hingst, DICA fitting specialist.
Ultimately the LDSD vehicle operated perfectly, said Klein, who will continue to use Safety Tech mats for the two additional test launches planned for 2015.
“Safety Tech Outrigger Pads are an excellent solution to help spread the load of outrigger supported equipment. Whether the application is in the utility industry, construction, road building, or maintenance activities, Safety Tech outrigger pads provide a strong foundation,” said Koberg.
“DICA calculates pad and mat specifications based on the customer’s equipment, outrigger reaction force, soil bearing capacity, and application,” said Koberg. “The outrigger pads used on the LDSD project are a custom solution created by our team working in collaboration with NASA engineers. The DR422 pads used by NASA in the crawler-transporter upgrade are a standard item in our product line. DICA is very proud to have a continuing role in the safe setup of launch and maintenance programs for NASA,” he said.
STAY CONNECTED
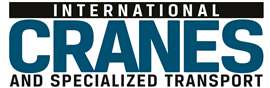
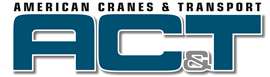
Receive the information you need when you need it through our world-leading magazines, newsletters and daily briefings.
CONNECT WITH THE TEAM
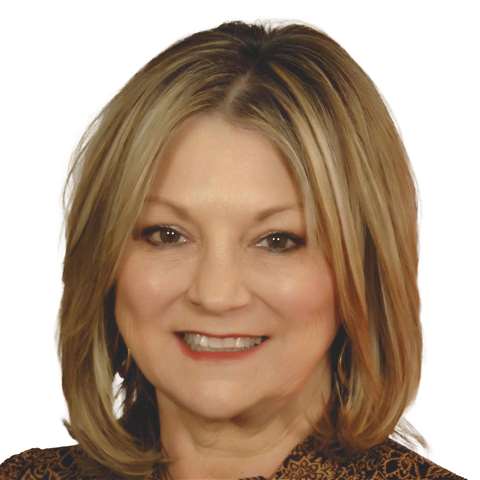
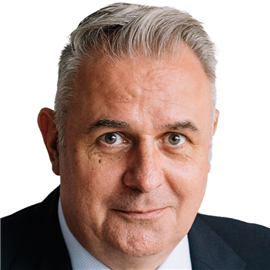
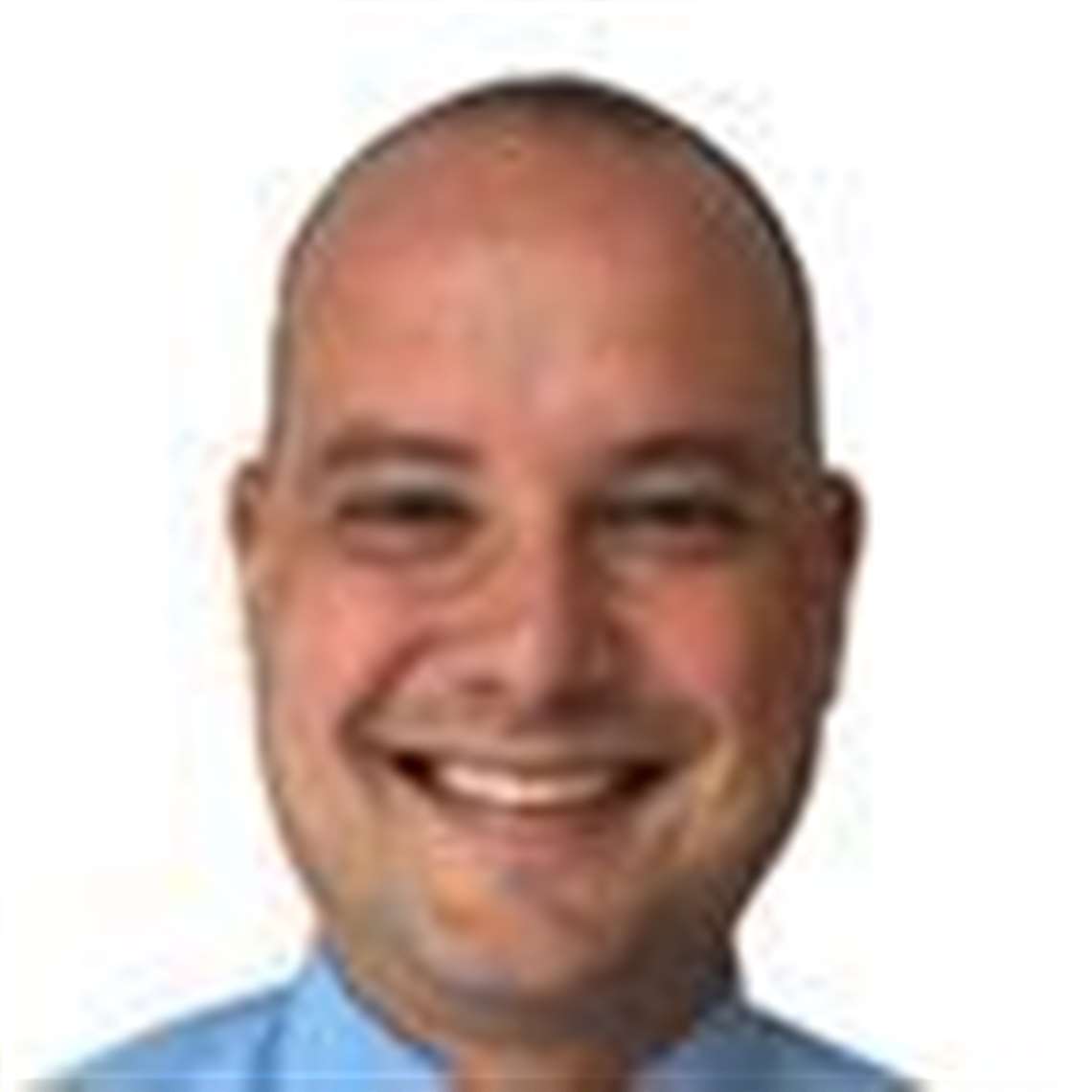
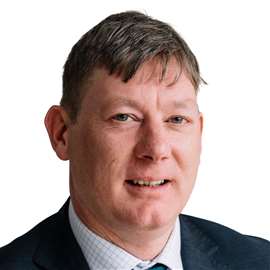