Standing tall
03 July 2014
As a show of respect to the commitment to freedom symbolized by the American flag, Acuity Insurance shattered what was already their own record by replacing the largest flagpole in North America with a new one that is almost 70 feet taller than the one that previously stood at their Sheboygan, WI headquarters. The new flagpole tops out at 400 feet, almost 100 feet taller than the Statue of Liberty.
Such an engineering feat — designing a flag pole that could stand up to its own record-breaking immensity but also erecting such an enormous symbol — would take an experienced team. And, while building, planning for, and erecting record-breaking flagpoles isn’t exactly a cottage industry, Acuity looked to leaders in wind power, to get the job done. The design, creation and erection of the flagpole was a team effort by several companies, leveraging the experience and knowledge of dozens of workers.
The structure, constructed from A-36 carbon steel, was designed by Texas-based U.S. Flag & Flagpole Supply. Since the pole and its component parts resembled a typical wind turbine, on a much larger scale, the manufacturing was performed by Cicero, IL-based Broadwind Energy, known for their production of wind turbine towers. The flagpole’s parts comprised six tower cans, each just shy of 70 feet tall.
Acuity called on Mortensen, a leader in renewable energy and one of the earliest U.S. contractors to enter the wind market some 20 years ago, to handle construction management. Previous flagpoles on the site had faltered in the brutal Wisconsin winds, so it was understood that precise planning by qualified, experienced professionals would be required to achieve a safe and sustainable flagpole installation.
The final team member was Dawes Rigging & Crane Rental, a member of the ALL family of companies, which would erect the massive structure in challenging weather and under a strict timeline.
Mortensen selected Dawes based on their longstanding relationship; the two companies had worked together on a number of wind projects.
Teaming up
“I believe it’s fair to say that no crane rental company has been involved in the erection of more poles/towers in Wisconsin, Minnesota Iowa, and the rest of the Upper Midwest than Dawes,” said Scott Jerome, senior branch manager, Dawes’ Kaukauna, WI yard. “We knew we could put together the right combination of equipment, people and lift planning so that we could handle the job as a unified team.”
Dawes developed a lift plan using their web-based 3D lift-planning program that produced illustrations detailing every stage of the job. The plan included load charts, equipment dimensional information, wind ratings, lifting crane main boom and luffing jib capacities, along with crane ground-bearing pressure estimations.
A 440-ton capacity Manitowoc 16000 Series III crawler was selected for the job, with a 120-ton capacity Terex RT1120 selected as the assist and tailing crane.
At every phase of crane operations, including pre-assembly, actual lifting, three machine reconfigurations, and final machine disassembly and load-out operations, Mortenson and Dawes held pre-job safety meetings that included field personnel and supervisory staff to discuss all facets of the project.
“We covered everything in these meetings,” said Jerome, “The space required, ground condition verification, wind condition review, machine dog-off procedure in the event of an emergency, signalperson assignments, rigging package review.”
With powerful pick-and-place capacity at a variety of radii, the 16000 is a well-known lift crane in the wind sector. It was rigged with 177.2 feet of main boom to set the first two flagpole tower cans at a 70-foot lifting radius. Because of the physics involved in building a tall, freestanding tower, after the first two cans were lifted, the crane had to be reconfigured to add a 236.2-foot luffing jib and repositioned to increase the radius to 100 feet from the previous 75 feet.
Calculations showed that, for the next three cans, the nearest allowable lifting radius was 95 feet. However, Dawes, out of concern for safe lifting operations, opted to set the remaining tower cans at the 100-foot radius.
“We felt that there was the potential for the lift to exact excessive strain on the machine’s luffing jib backstops were we to operate at the minimum allowed radius,” Jerome said. “By backing off an extra five feet, to get to a 100-foot radius, we were able to take a great deal of strain off the machine backstops and we only lost 500 pounds of lifting capacity.”
After the fifth tower can was in place, the machine was reconfigured with a 275.6 foot luffing jib to install the sixth tower can and the tower cap, or “truck,” as it’s called.
Last minute calculations
An evolving work plan dictated by last-minute calculations to further enhance safety and structural stability required changes to the timeline, even before the first lift. For example, about two weeks before the erection was scheduled to start, Mortensen and Dawes learned that a more desirable design had been decided on, changing the structure from a 5-section pole to a 6-section. The change required revisiting all aspects of the job to ensure proper machine configurations. The weight of the cans changed as well, which also had to be factored into the revision.
And then there was the Wisconsin weather. Some lifts had to take place on the weekends when there was no rain or risk from high winds. Crews had to be available 24 hours a day to ensure completion safely and on time.
“My crew of guys supporting this job, they did a spectacular job,” said Jerome. “They performed way above and beyond the call of duty.”
Further, once the team reached a certain point in the tower’s construction, they had to move forward continuously with the remaining cans, otherwise, vortex shedding – the force from a pattern of multiple winds alongside a tall, freestanding structure – could build up force and suction, causing the structure to collapse (a “Kármán vortex street”). Only by incorporating all of the engineered features designed to counter this force would the structure achieve required stability.
“At a certain point, there was no looking back, so we had to plan forward and commit all our resources to the continued buildup,” said Jerome, explaining that the Kármán vortex street is common in construction of structures such as turbines. He explained that they occur when an air stream flows past a cylindrical body at certain velocities, depending on the size and shape of the body. As the air flows past the cylinder, alternating low-pressure vortices are created on the downstream side of the object, and the object will tend to move toward the low-pressure zone. This potential for instability forced a rapid buildup once a critical height was reached so that the structure’s weight, along with built-in internal stabilizers, could counter the force.
“With a major project like this, and given the time of year, we just came into the project expecting the unexpected,” said Jerome. “We just reconfigured and adapted as was necessary.”
“The American flag truly is a symbol of freedom and inspiration to the world,” said Ben Salzmann, president/CEO, Acuity. “We proudly fly this flag because we are blessed to live and work in the United States of America.”
The flagpole took just two weeks to erect, and the flag was flown for the first time on May 22, 2014. The flag was formally welcomed for public viewing with a dedication ceremony on June 16, 2014.
“In all my years with ALL Crane, it’s one of the jobs I’m most proud to have been involved with,” said Jerome. “Everyone was very proud to be involved with this project. You’ve got a company with the moxie to want to put up the tallest flagpole in North America, and, well, everyone got caught up in the job.”
Marathon, WI-based B&K Trucking handled the hauling work.
STAY CONNECTED
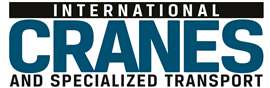
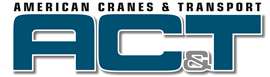
Receive the information you need when you need it through our world-leading magazines, newsletters and daily briefings.
CONNECT WITH THE TEAM
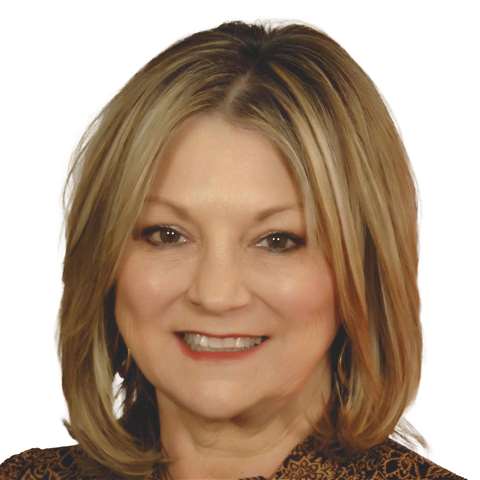
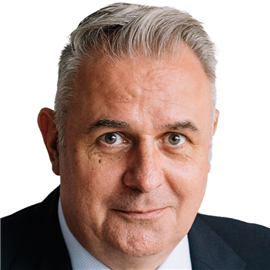
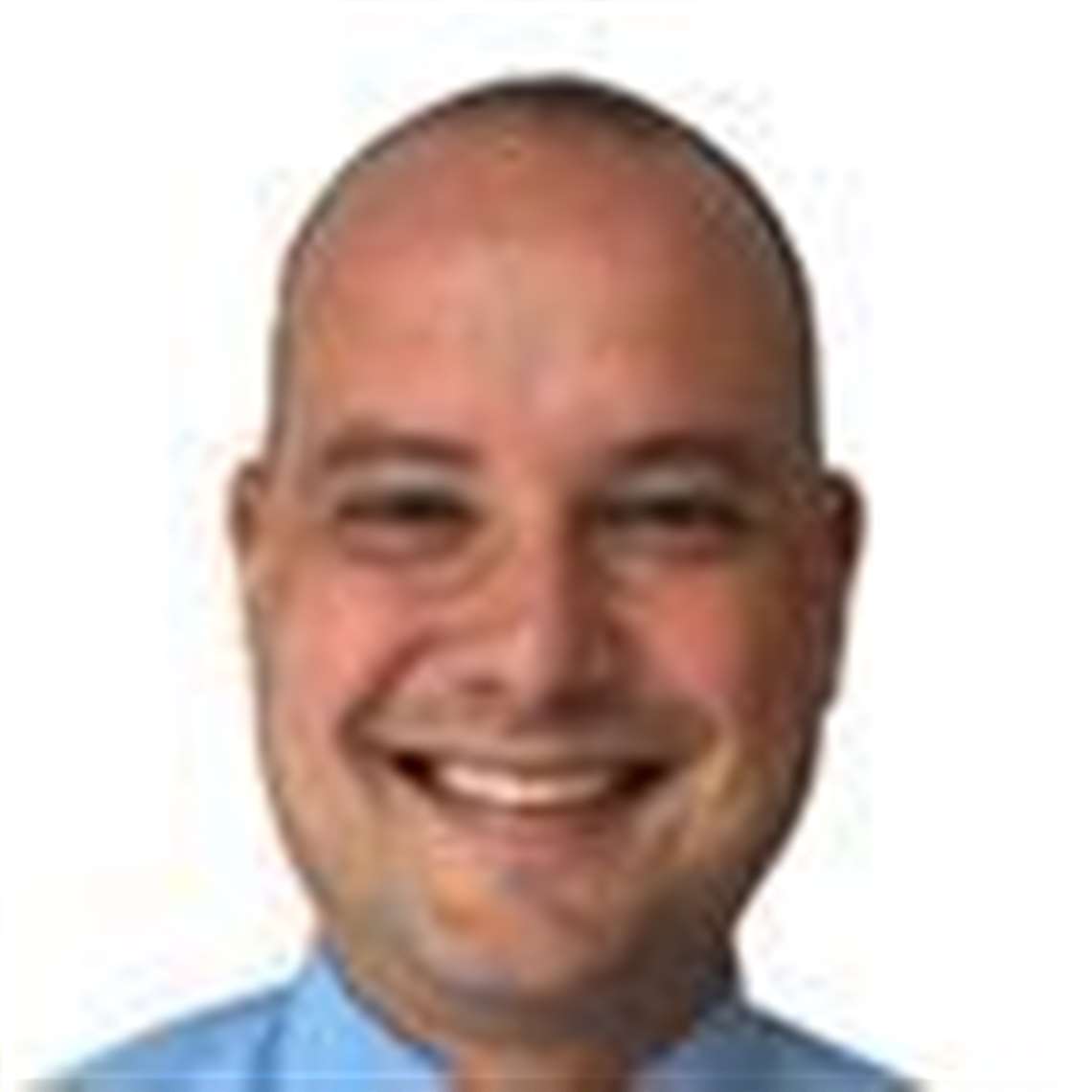
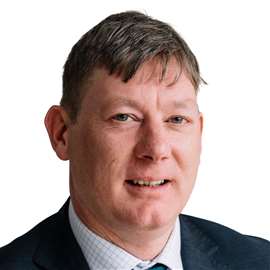