Sustainability in lifting equipment
10 August 2022
With new ideas and technology being developed, tried out and tested, the lifting industry has the opportunity to set the standards of sustainability. Niamh Marriott reports.
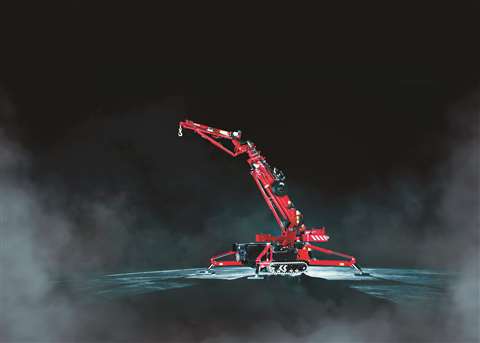
The topic of waste within the lifting sector is often overlooked, so how can the industry use innovative technology to cut down wastage further and maximise its commitment to sustainability?
Inspection compliance company Motion Software makes the argument for automated lifting technology.
“At its core, the lifting industry is about innovation, collaboration and building better foundations for current and future generations,” comments a spokesperson for the company.
Safety and sustainability must be at the heart of this industry. How we work, complete inspections and monitor performance plays a crucial part in our environmental impact and this is why implementing sustainable, innovative technology to assist our everyday industry practices is more critical than ever.
Sustainable lifting technology
With some sustainable innovations, such as solar panels reaching the end of their life cycle, scientists and engineers question how to best dispose of these materials. Automated asset management systems like Motion Software’s Kinetic solution help businesses generate maximum energy by increasing the performance of maintenance and repairs whilst keeping downtime to a minimum.
The company says that green energy doesn’t cost more. With “the increasingly plentiful supply of green energy and growing competition among providers, the cost of green has fallen dramatically” in recent years. It further adds that years of investment in renewable energy had started to filter through.
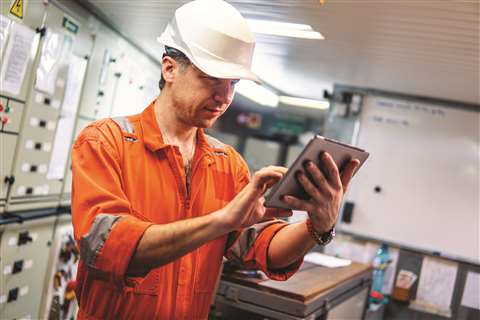
“Lifting technology will be one of the crucial next steps towards incorporating more sustainable practices in the industry, offering paperless processes, increasing control over routine practices and prolonging machine life. Through these essential steps, lifting professionals can achieve their sustainability goals,” the spokesperson comments.
Net-zero steel: an alternative renewable energy
Global industries are looking more and more to alternatives and renewable technologies, and the UK government is funding some of this research. British Steel is conducting a study into the use of green hydrogen to manufacture net-zero steel.
The steelmaker, which is collaborating with EDF UK, UCL (University College London) and the Materials Processing Institute, has pledged to deliver net-zero steel by 2050 and significantly reduce its carbon dioxide intensity by 2030. It secured funding from the UK Government for the feasibility study into switching from natural gas to green hydrogen as a fuel source for re-heating furnaces.
If the study is successful, British Steel will undertake an industrial-scale demonstration, which could see the technology developed and rolled out across all its operations including its main manufacturing base in Scunthorpe, UK. It could also be adopted by other UK steelmakers.
British Steel’s environment and sustainability director, Lee Adcock, said, “As an energy intensive industry with hard to abate emissions, the steel industry offers the potential for large CO2 emission savings through fuel switching from natural gas to hydrogen.
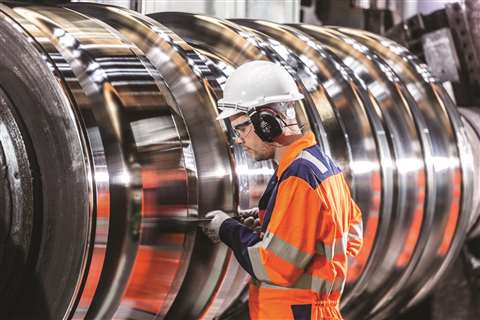
“This study is, therefore, a vital and hugely exciting step on our journey to developing the technology needed to transform the way we, and other steel manufacturers, operate.”
British Steel won funding for the research from the UK Government’s Net Zero Innovation Portfolio (NZIP).
Hybrit: fossil-free hydrogen gas storage
SSAB, LKAB and Vattenfall, which have already been working on fossil-free steel for some time are now inaugurating the Hybrit project’s pilot facility for fossil-free hydrogen gas storage at Svartöberget in Luleå, Sweden. The rock cavern storage facility is the first of its kind in the world. The inauguration ceremony marks the start of the two-year test period, which will run until 2024.
The Hybrit initiative was launched in 2016 and the hydrogen storage facility will be important in the overall value chain for fossil-free iron and steel production, says a spokesperson. Producing fossil-free hydrogen gas when there is a lot of electricity, for example, when it is very windy, and using stored hydrogen gas when the electricity system is under strain, will ensure a steady production of sponge iron, the raw material behind fossil-free steel.
“Sweden will create new jobs by leading the climate change transition, and Hybrit is a good example of doing just that with green technology and innovation. When we build the energy system of the future, we need to both take advantage of opportunities to store energy and ensure that large energy users can be flexible in their consumption. This is exactly what Hybrit does through its unique hydrogen storage,” says Khashayar Farmanbar, Minister for Energy and Digital Development in Sweden.
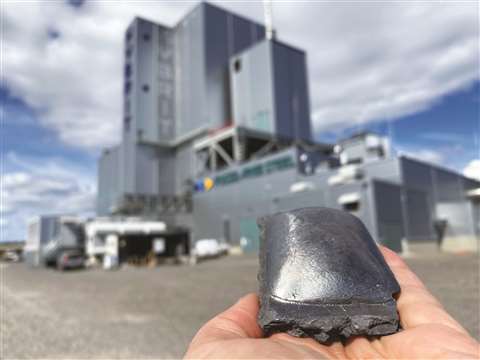
Battery-operated cranes
Hiab, part of Cargotec, has already been looking at fossil-free steel with SSAB, and intends to make its products from this.
Hiab says that while climate change is a very real crisis to tackle, it also presents an enormous business prospect and is also an enormous business opportunity to offer new products and services with less impact on the climate and environment.
Tobias Bunne, Hiab’s environment, health, safety and sustainability director, says, “We are committed to reducing our own CO2 emissions from our operations by 2024 and being carbon neutral in 2030. However, this only represents a small amount of the emissions in our whole value chain. The two biggest contributors are the manufacturing of steel and our customers using diesel to power our equipment.
“All of our equipment can be installed on electric trucks with no, or minor non-costly modifications,” says Bunne. “However, as a stop-gap solution, Hiab offers battery-operated cranes using ePTO (electric power take off) for use with LNG, hydrogen or diesel trucks. Since it provides its own power source, it allows customers to operate their cranes with the engine turned off. It offers the possibility for the cranes to work at night and indoors. Hiab offers battery packs of different sizes.”
The company is also looking at less obvious ways to reduce its product’s environmental footprint.
“Size matters and some of our new big cranes deliver the performance of a larger crane in a smaller package like the Effer 1000,” continues Bunne. “The crane only weighs 9,500 kg but delivers performance of bigger cranes, which reduces emissions and cost of ownership.
“Or the Hiab iQ.1188 HiPro which is the largest Hiab crane to date with a long reach and great lifting capacity, but still lightweight in a compact package.”
Sustainable crane manufacturers
Some companies are not only looking at electric cranes but other areas of sustainability within the company.
For example, almost all Hoeflon machines sold are fully electric, powered by cobalt-free lithium batteries that are built by OX Power. The company aims to consider sustainability in other areas of the business, too. “In our building, we also take sustainability into account,” says a spokesperson.
“The indoor temperature is regulated by means of a heat pump. This system goes 200 metres deep into the ground and retrieves the heat from there. In the summer, it pumps the heat back in to keep the building cool.”
The Supply Chain Sustainability School
Companies are joining together to drive eco solutions to market. UK-based lifting solutions provider GGR Group, has joined the Supply Chain Sustainability School (SCSS) to work alongside key industry players in driving sustainability and collaboration within the construction sector.
The SCSS hosts regular networking events to provide a platform for drivers of sustainability and decision makers to share knowledge. It provides free educational resources to those who are aspiring to enhance their knowledge of best practice in sustainability.
Daniel Ezzatvar, GGR marketing and special products director, says, “GGR has championed the use of low emission and eco-friendly solutions for many years. Over 80 per cent of our equipment can be described as ‘eco-friendly’ because it is either battery powered or mechanical. We see our involvement with the SCSS as a partner member as a way to enhance our overall approach to sustainability, whilst gaining insight into best practise from across the supply chain.”
Can transport trailers be environmentally friendly?
With rising fuel prices, there are some top tips to save fuel for a trailer that can also make an environmental difference. Netherlands-based Broshuis says trailers with an independent suspension can be economical.
In addition to optimised tare weight, the company’s trailers have advantages in terms of loading height and stability. They can drive at any driving height due to its axle geometry, ensuring optimum road holding and reducing diesel consumption.
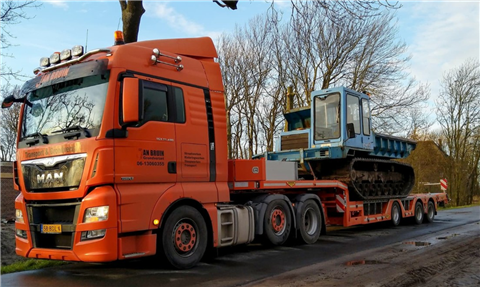
Every time a tyre rubs on the road, this not only leads to high wear, but also to higher fuel consumption. The company also promotes its eco ramp, which is horizontal instead of the vertical, less-aerodynamically efficient type, which can improve fuel consumption by 20 per cent. The ramp can also be used as a loading floor and offers the option of carrying overhanging cargo.
What role can lubricant play in reducing machine emissions?
Tom Hyde, technical manager at Totalenenergies UK says, “Owners and operators of cranes and wider heavy fleets around the globe are not at all immune to the dual pressures of rapidly escalating fuel costs, and rising stakeholder demand for tangible action on issues related to sustainability and climate change. With cranes often carrying hundreds of litres of oil, issues such as carbon emissions and environmental impact are growing in importance as the race toward sustainability and to mitigate fuel price pressures, accelerates.
“The role of lubricants, regrettably, is often forgotten in the context of sustainability. In reality, choosing the right lubricant can and should play a key role in achieving cost savings and minimising environmental impact, including through extending the lifespan of the machine.
“Significant advancements have been made over the past few years in this area, with products now on the market which increase uptime and lower maintenance costs. These efficiency gains are being realised, often through reduced friction and viscosity of lubricants, equating to between 2% and 3% increases in fuel efficiency.
“Given the sheer scale of the global cranes and heavy transport industries, that’s a significant amount of money saved and a lot less carbon dioxide emitted.
“Disposal and recycling of oils and lubricants is understandably critical when it comes to sustainability and minimising environmental impact. Today’s waste recycling providers can take used oil – traditionally disposed through fuel burning in the marine or energy markets – and reprocess it into a base oil product that serves as the foundation for new carbon-efficient lubricating oils. Overall, this emits about 30 % less CO2 than lubricants produced from crude oil.
“The industry still has a fair way to go when it comes to maximising the potential contribution of lubricant efficiency in the race toward true sustainability.”
STAY CONNECTED
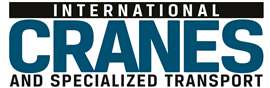
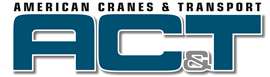
Receive the information you need when you need it through our world-leading magazines, newsletters and daily briefings.
CONNECT WITH THE TEAM
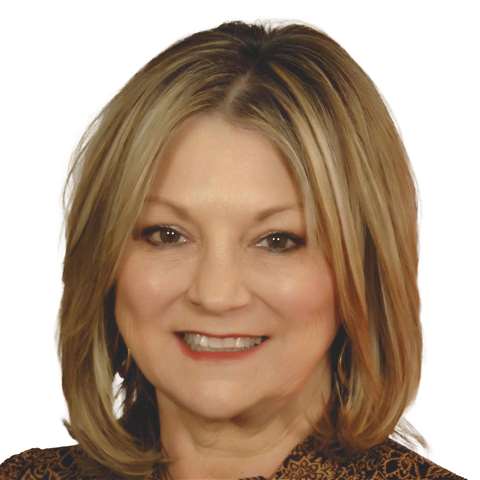
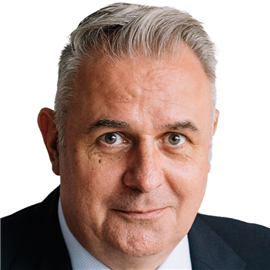
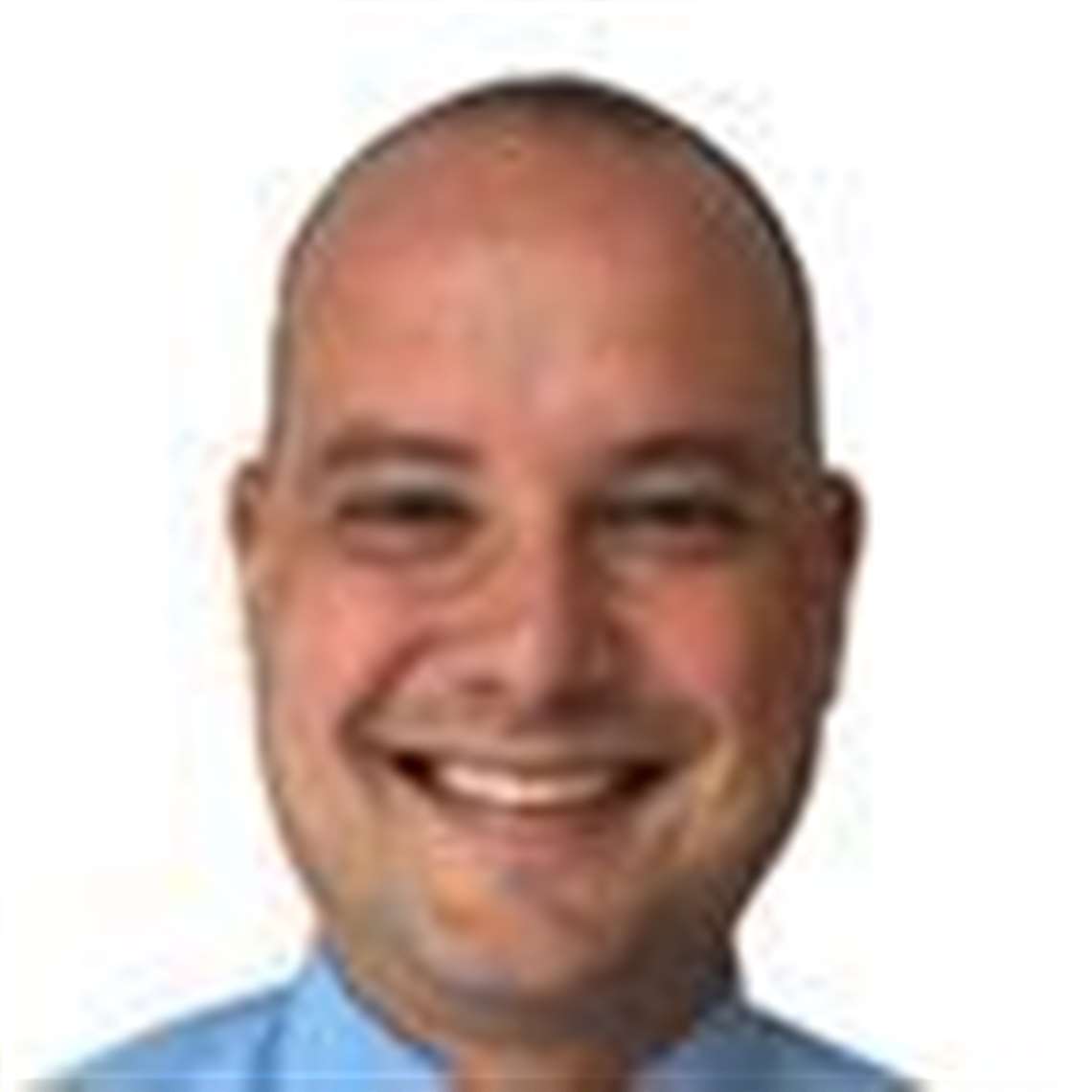
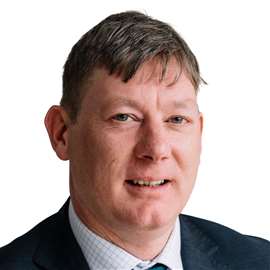