Taking a closer look at self-locking hooks
02 November 2022
Self-locking hooks, also known as safety hooks, have changed the lifting industry, but their use has yet to become universal.
Self-locking hooks, also commonly known as positive locking hooks or safety hooks, are used in all applications, from industrial manufacturing to offshore oil and gas. There are many clear benefits that end-users have found in switching from sling or standard hooks to self-locking hooks – all contributing to enhanced safety in lifting operations.
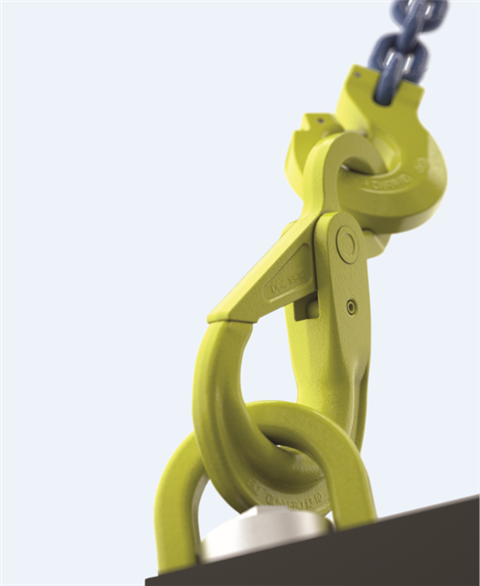
As the name suggests, self-locking hooks close by themselves as soon as a load is placed in the bowl of the hook and lifting begins. Once it closes, it cannot open again until the load is released from the hook. The self-locking hook concept was launched as the BK model by Gunnebo Industries in the 1960s, primarily to improve safety on construction sites where, previously, hooks were rigged without a latch.
Long lasting design
Rigging gear gets put through a lot of wear, which often can result in damage to spring latches, like those on a sling hook. This either leads to the lifting gear being taken out of service, potentially delaying work, or if good lifting practices are not followed, people may use it without the latch, leading to a hazardous lift. A self-locking hook will last longer, preventing delays and unsafe practices, while always remaining closed when under load.
Self-locking hooks are used in a range of applications, including:
- Construction: wire rope slings; chain slings; and as a connection point between a shackle (or hook).
- Industrial manufacturing: chain slings; hoists with self-locking hooks.
- Offshore: forerunners/stingers – the line that comes off the crane on the offshore platform to move loads around or from a supply vessel to the platform.
The offshore galvanized BKLK self-locking hook was recently launched by The Crosby Group. Working closely with end users, we developed this hook to be a game-changer in durability. We’ve continued to innovate on the industry’s first self-locking hook we manufactured, even if the product today looks remarkably like the first one that came off the production line almost 60 years ago.
In the early 1960s, Karl-Axel Wahlström and Stig Lindgren were credited with the first prototype, hand-carved out of wood. They called it the ‘BK’ hook, an abbreviation of ‘Byggnadskrok,’ which in Swedish is a combination of the word ‘byggnads,’ meaning construction, and ‘krok,’ meaning hook. The product was patented and released to the market in 1965.
The BK and Crosby Shur-Loc hooks produced today are similar, and both are now designed to avoid fingers getting pinched when opening the hook. The Crosby Shur-Loc and the Gunnebo Industries BK hook use different approaches to solving this issue. The Shur-Loc was designed with an enlarged thumb access, positioned further down and away from the pinch point, while on the BK hook, a latch rotation stop was introduced to stop the latch from pivoting down on the thumb.
How do these hooks prevent injury?
Even though they are small changes, they are important in increasing worker safety. Pinch point injuries are among the most common on a jobsite. Other design adjustments include flat sections to allow connection with omega couplers or the GrabiQ system, recessed triggers and easy-to-replace trigger sets.
Today, The Crosby Group offers clevis self-locking hooks that connect directly to a chain sling; ball-bearing swivel hooks that can rotate under load; a Griplatch hook with a latch that connects to the body for improved side-stability and reduced weight; galvanized hooks for severe-weather protection; and even a special self-locking version for skip-loaders.
To enhance safety, we have added the option of a handle to minimize the pinch risk when manipulating the hook. The handle was developed for high-risk environments such as helicopter lifts or lifts in offshore operations, where bad weather and swells are common.
Double latch hook details
Another invention that came from the offshore oil and gas industry was the Gunnebo Industries’ branded double latch hook. The secondary, spring-loaded latch acts as a redundant safety feature, making it impossible for the load to slip out, should the main latch come undone (due to being violently hit while the load is idle, for example).
While self-locking hooks are used in all markets, there is an opportunity to expand their use. Sling latch hooks are often chosen for convenience or cost, but in my view, with few exceptions, the benefits of self-locking hooks far outweigh the drawbacks.
Felix Nyberg is global product manager at The Crosby Group.
STAY CONNECTED
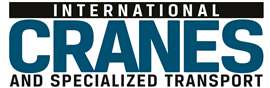
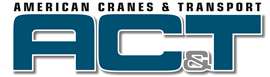
Receive the information you need when you need it through our world-leading magazines, newsletters and daily briefings.
CONNECT WITH THE TEAM
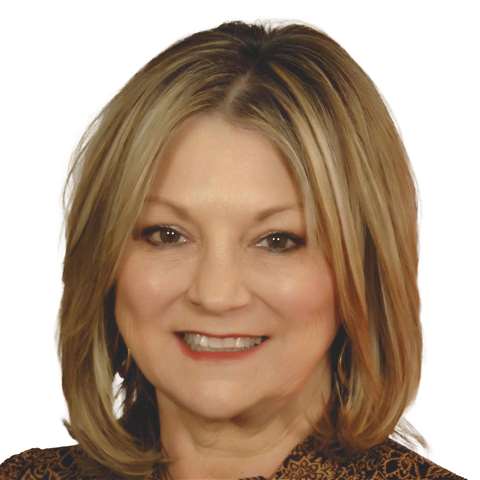
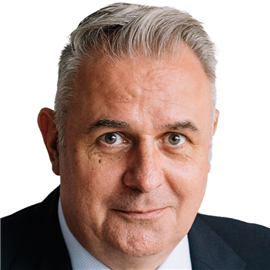
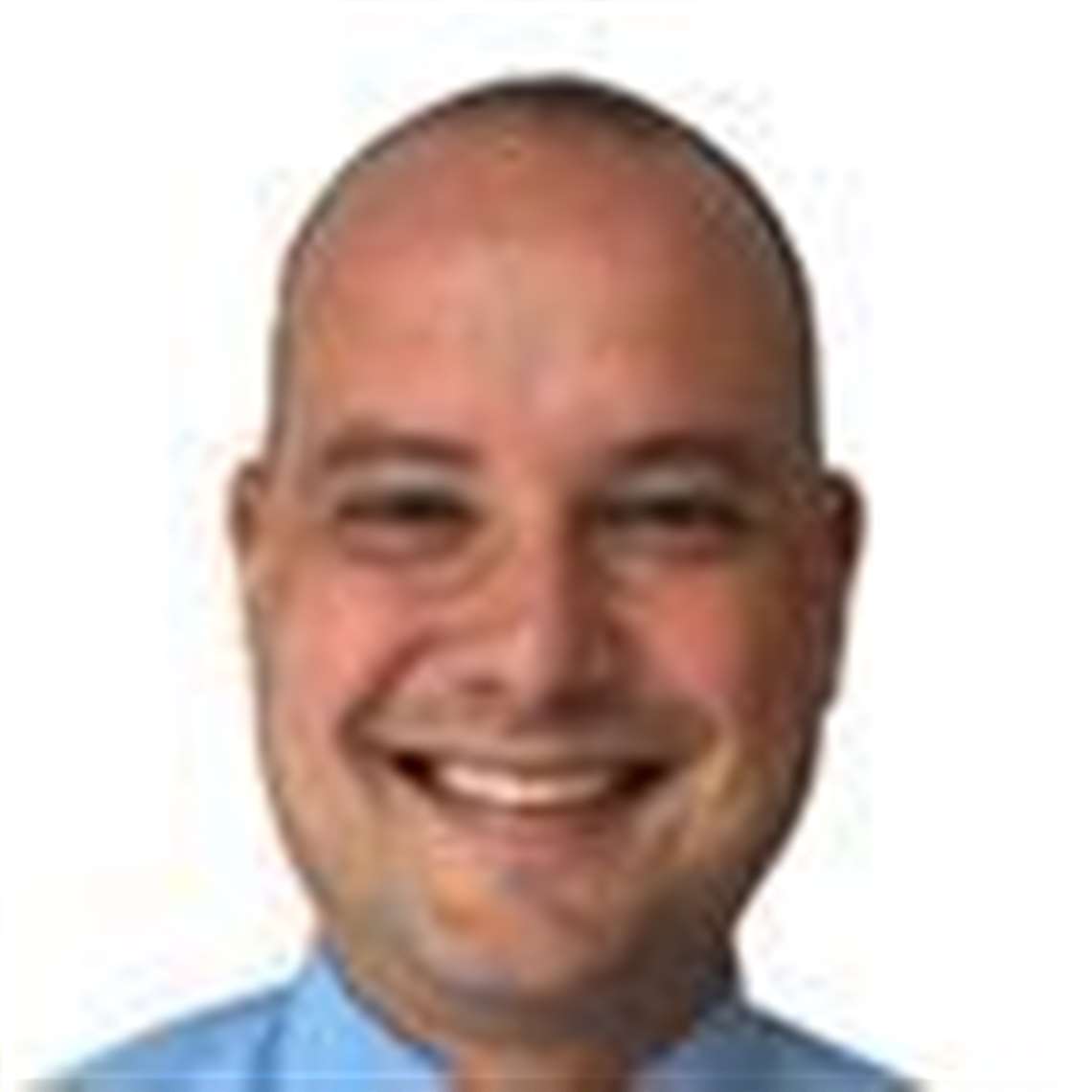
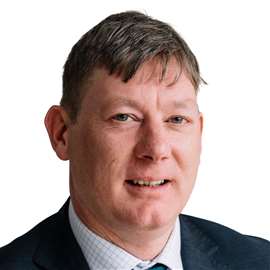