The A, B, C approach to sling safety
03 December 2018
When lifting loads with synthetic slings rigged in choker or basket hitches there is a real opportunity for sling damage if not ultimate failure. The two largest culprits are cutting from edges and friction from movement.
I published an article a few years ago that finished with the statement, “Slings in one hand, sling protection in the other.” Our company’s Field Services division provides failure analysis and accident investigation services. By a wide margin (87 percent), sling-related accidents that we have evaluated for clients have been synthetic sling related. This category of slings includes synthetic web slings, synthetic roundslings and synthetic rope slings. An excellent report developed by Mackey and Webster for the Department of Energy cited 13 cases of crane and rigging accidents, nine of which were directly attributed to lack of sling protection for synthetic slings.
A recent fatality in the Midwest was the result of inadequate web sling protection. Our company is representing one of the parties and will surely be involved in litigation for years to come.
Are the incidents avoidable? Yes. Can we develop a system or method to lower the risk associated with synthetic sling failures? Yes. Obvious avoidances for synthetic sling usage include objects or environments that are hot or for the
sling, greater than 180 degrees F. Other natural enemies of synthetic slings are caustics and acids, ultraviolet rays and a number of similar elements that can degrade material. For a further listing of reasons to remove synthetic slings from service see OSHA Standard 1910.184 - Slings, or ASME B30.9-2011 Slings.
One of my good friends in the crane and rigging industry finally said, “What are you going to do about it?” He inferred that the “it” was, slowing, if not stopping the volume of synthetic sling incidents due to a lack of protection.
ABC approach
- A is for Abrasion
- B is for Bearing Pressure
- C is for Cutting
Lowering risk
In North America (U.S. and Canada) we are famous for warning, alerting, identifying, notifying and announcing the hazards and potential of a risk situation. The risk can be generated from gases, chemicals, fluids, motion, edges, flying particles, rotating parts, vehicles, moving equipment, falling objects and the like. Does a synthetic sling, of and by itself present a risk? No. Does a load such as an electric motor, concrete form or a piece of steel plate present themselves as a risk? No. Slings can be used without failure and loads can be moved without incident. The obvious issue is the interface between the sling and the load.
As an industry, we can lower the risk of synthetic sling cutting and friction failure by inserting suitable material between the sling and load. Let’s try an A, B, C approach. If I can train my employees to regard the type of risk to the sling, they can select the appropriate sling protection for the load.
A is for Abrasion. The load surface has properties that can cause friction, scrubbing or abrasion damage to the sling. The load may be perfectly circular, like a concrete pipe, but as the sling begins to tension prior to lifting the load, it stretches and can be abraded or burned by the load surface. In this case, the sling protection must be suitable to accept the abrasion on the sling’s behalf without being destroyed.
B is for Bearing Pressure. The web sling, roundsling or synthetic rope sling is planned for use against a radius that is small enough to sever simple rubber belting or similar materials, due to an external force or pressure (the sling). It’s all about the pressure created between the sling and the contact point against the load. If the pressure can sever the protection material, it is unsuitable. As the sling contact width decreases, the pressure (pounds per square inch/centimeter) increases. I have seen 1-inch conveyor belting cut into 12-inch squares that had been fully sheared due to web sling pressure against a load corner (resulting in a fatality). The calculation for determining a sling protector’s resistance to severing and failure varies according to the material, radius and pressure. It would be great to have a universal formula but the variables require a case-by-case evaluation.
C is for Cutting. The load edge is 90 degrees with or without de-burring. Remember our discussion about slings stretching while tensioning? It is easy to envision a sling being cut with even moderate pressure to a load edge (steel plate or machined surface). This category basically requires that the sling is completely blocked from contacting the load edge during any hoisting, slewing or lowering events.
Best practices
Have you ever wanted to be a part of a social movement but couldn’t find the right cause? How about one that saves lives? Employers and their safety departments can review the items typically rigged in their organization and establish the required Class A, B or C sling protection necessary based on the sling-to-load interface. To say the least, the highest risk for a sling incident occurs under the employer’s oversight. They are responsible to train their employees in the proper use of the tools. Sling distributors can help continue to educate the customers about the Class A/B/C differences, and guide them towards the best protection for the applications on their property. Rigging training companies can continue to educate end-users about the ABCs of sling protection during hands-on sessions that involve sling selection and use.
A variety of approaches can lower the risk of synthetic sling damage/failure, which include but are not limited to, rigging to positive connections, such as pad eyes or swivel hoist rings, using spreader bars to minimize the sling angle and opting for other sling types, such as alloy chain or wire rope, when the load prohibits the use of a suitable protection device. (Don’t be fooled. Even chain and wire rope can be cut by a load edge, especially due to the localized pressure at the contact point.) Remember, slings in one hand, sling protection in the other. For more rigging best practices and a full listing of crane and rigging training courses visit www.iti.com.
STAY CONNECTED
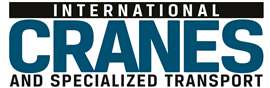
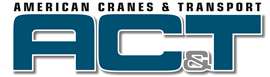
Receive the information you need when you need it through our world-leading magazines, newsletters and daily briefings.
CONNECT WITH THE TEAM
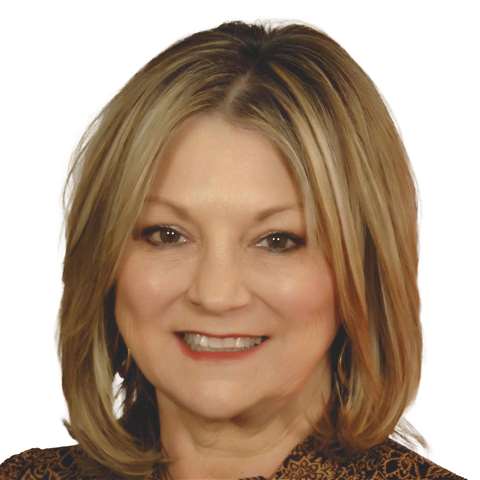
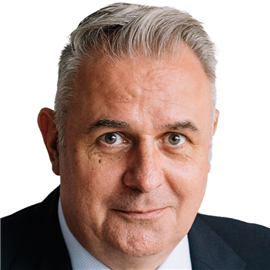
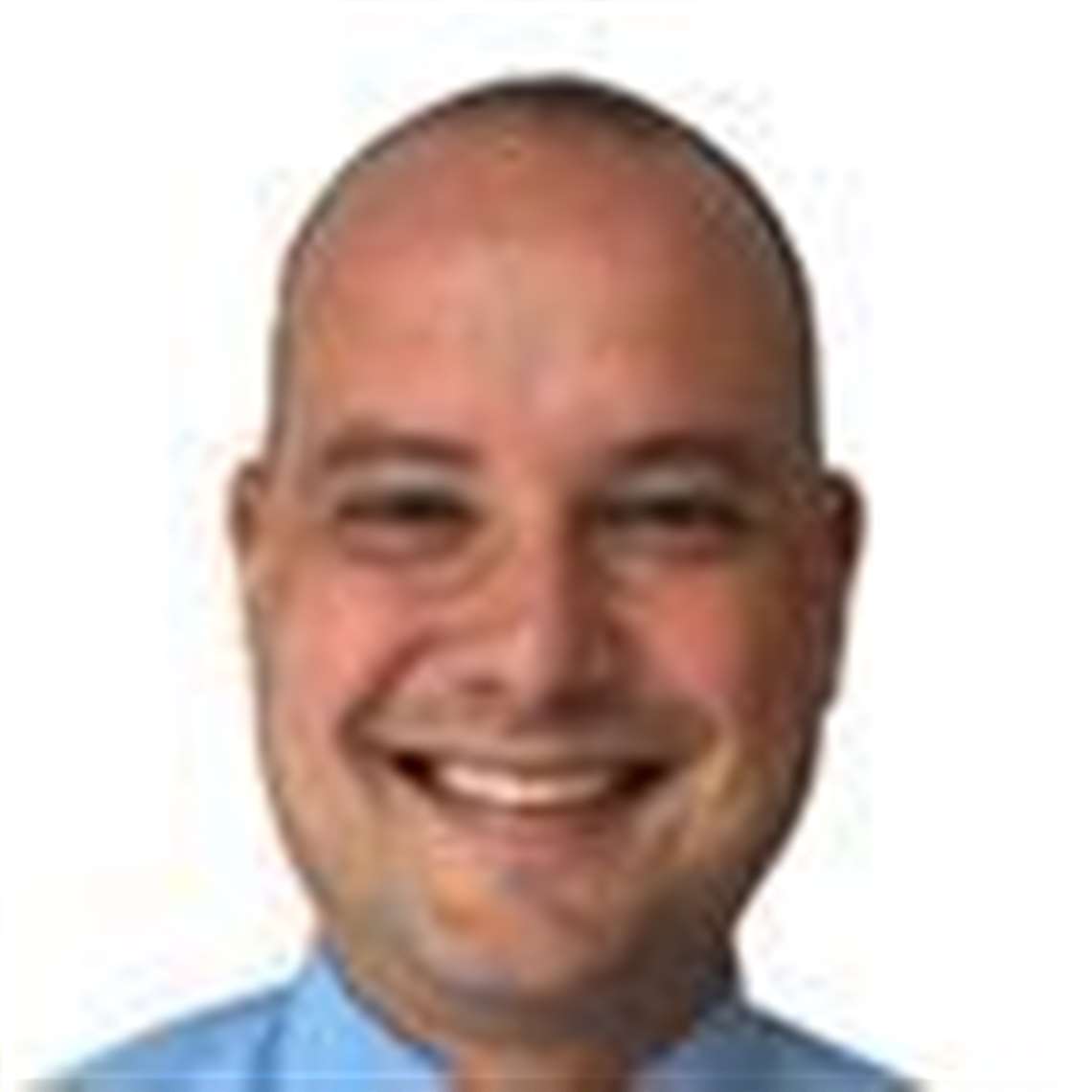
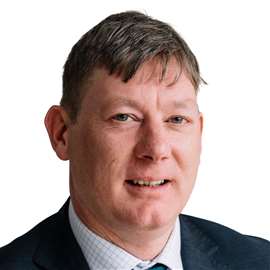