The truth about supply chains
18 April 2022
Assessing the realities within the supply chain affecting SC&RA members. Mike Chalmers reports.
According to leading market and consumer data, in 2021 there were 11,642 supply chain disruptions reported worldwide. North America claimed the highest number of disruptions on that list, totalling 47 per cent.
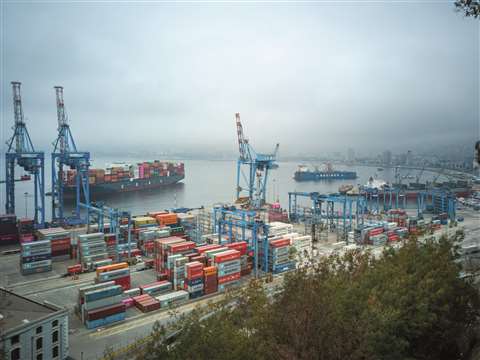
While the supply chain crisis was certainly exacerbated by increased consumer spending during Covid, the problem didn’t start with the pandemic. The skilled worker shortage (the USA alone is short 80,000 drivers) began long before the pandemic. Adding to the challenge, in recent years, big freight rail carriers have also reduced their workforce – while rail freight increased by 40 per cent in weight and 37 per cent in dollar value from 2010 to 2019.
At present, the ingredients making up the modern supply chain shortage recipe appear to comprise a dubious mix of worker scarcity, container and chassis shortages, lack of storage space for just about everything, a need for the industry to modernise and, last, the next-day-delivery model itself.
But given the challenges within this (yet another) new normal, there are still pathways to success – even within the moment.
Push versus pull
“In my research, everyone tends to agree that American spending shot up during the pandemic as a result of economic stimulus,” said Charles Edwards, professor of practice at the University of North Carolina at Chapel Hill in the USA. “And America doesn’t make a lot of stuff domestically; we tend to import, primarily from Asia and elsewhere in Europe. So companies have been stretched because of demand, and at the same time, logistics flows have changed in recent years.”
Edwards explained what was once a “push” model, where the consumer purchased an item and the seller essentially ordered more, has been replaced by a “pull” model.
“A seller used to say, this is what I’m making and this is where you can get it. We now live in a ‘what do we want, when do we want it, and where do we want it delivered’ model. The logistics industry and the freight transportation industry are having their own moment: ‘what do we order, when will we have it, and where do we put it until the real sale occurs.’”
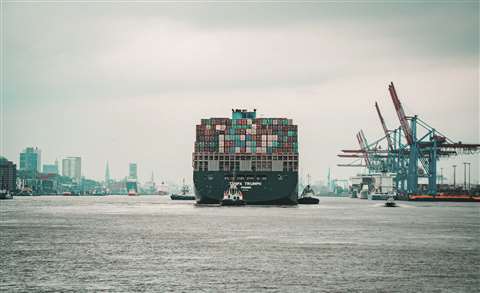
Edwards, who has been in freight transportation and logistics for more than 50 years, added that it’s this “real sale” piece of the equation that is really mucking up the works. “With ecommerce, it’s all about anticipatory orders. When you hover over something online, the algorithm behind it senses that action and sends a message that an order needs to be placed – whether anyone purchases anything or not. So the seller places an order with the supplier and that supplier goes about trying to fulfil the order(s),” he says.
From there, maintained Edwards, it doesn’t take a genius to figure out how quickly the supply chain can clog with distribution centres filling up, storage warehouses backing up and trucks with nowhere to put or store anything.
As for how pervasive the clog is within the USA, Edwards emphasised that the disruption doesn’t discriminate.
“While we hear a lot about the ports out West, it’s the same everywhere – Savannah, New York, Virginia, Seattle. Almost every port in the US is backed up, and it’s because there’s no place to put anything.”
Immediate impact
Scott Bragg, CEO at SC&RA member company Bragg Companies, is trying his best to weather the storm. “We look at the big-ticket items for us and try to stock up on them and at least get them here in Long Beach and southern California, and then we can send stuff to our branches throughout the West,” he said. “But also, your everyday stuff – filters, oil and lube. They’ve all gone up in price and they’re getting harder to find.”
While Bragg admitted the supply chain disruption hasn’t seemed to hit the OS/OW industry quite as severely from what he sees, it’s hardly more than a temporary reprieve. “There are enough businesses just in our trucking world who are all having problems, including the biggest names. So, of course the little guys are too – especially when you factor in the semiconductor shortage.”
In addition to stockpiling everyday consumables, Bragg’s heavy transport general manager, Eric Peterson, pointed out another adjustment they’ve had to make. “We have two spare trucks on standby now, whereas before, we were utilising our entire fleet. If a truck goes down, it used to be a one- or two-day turnaround to get stuff fixed, parts, etc. Now, we’re looking at a week, maybe two, in some cases, depending on the part.”
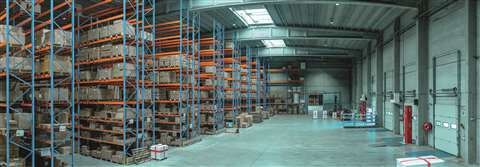
Bragg also spotlighted his company’s digital evolution over the years. “Our system is fairly modern, and we’re continuously updating,” he noted.
“While we realise that not everyone can invest the same in technology, I can’t imagine how difficult the last couple years would have been without it. Two years ago, I hired a chief technology officer, and our IT department is about a dozen people now.”
Moreover, Bragg advised his industry colleagues to consider an additional hire. “A good purchasing agent who can spend time researching and find what you need. We’ve got a couple really good people. You have to monitor it all the time – and find the deals as well as the availability.”
According to Edwards, digitising in this way will undoubtedly help to alleviate the overall disruption. “The US is twenty to thirty years behind on this, but companies – the industry – needs to get over it and modernise,” he stressed.
“Many trucking companies are still using fax machines to move around information. Ultimately, we should be utilising open-access, highly encrypted digital platforms on which all the stakeholders in the supply chain can enter information. It would streamline this process and speed everything up.
“We see how effective digitalisation is for permits alone. The same thinking applies to the greater logistics industry. These systems could be used on many levels in many places and probably have an immediate impact.”
Time to diversify
Along those lines, William Doyle, executive director at SC&RA member Maryland Port Administration–Port of Baltimore, sees an additional layer of opportunity.
“The current US supply chain is broken because it’s outdated,” he assured. “It’s a result of a decades-long model where ocean carriers and beneficial cargo owners have brought forty percent of the nation’s containers through Los Angeles and Long Beach ports and into the Inland Empire.”
Doyle believes the time is now for diversity. “These ultra-large container ships can now come to the East Coast ports like Baltimore that have the necessary infrastructure and channel depth to handle them,” he said. “You also need an efficient supply chain network that includes multiple local distribution, sorting and fulfilment centres as well as great trucking and rail networks, like we have in Baltimore.”
Ultimately, Doyle firmly believes the path to success involves shippers (like retailers and beneficial cargo owners [BCOs]) demanding that the ocean carriers move away from the 30-year-old model of bringing in goods to just a handful of select ports.
Chris Smith, SC&RA vice president of Transportation echoed this sentiment, noting “…when shippers select import and export locations, they must consider that port’s ability to lift and move these large pieces of equipment in and out of the gates. In turn, ports need to consider their crane, rigging and adjacent highway infrastructure through the lens of project cargo mobility as a competitive advantage to offer shippers who face recurring labour, container and congestion issues at other locations.”
Doyle added, “While other ports are dealing with congestion, we’ve been welcoming ships that have diverted from those congested ports and instead come to Baltimore. But like all ports, we could always use more truck drivers – truckers are a lynch pin in every port.”
STAY CONNECTED
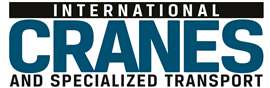
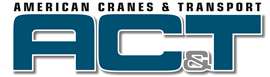
Receive the information you need when you need it through our world-leading magazines, newsletters and daily briefings.
CONNECT WITH THE TEAM
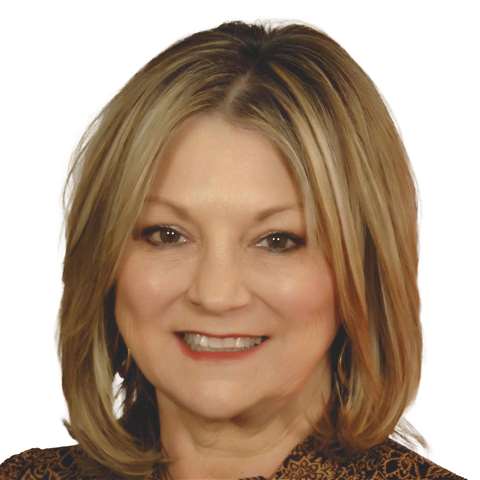
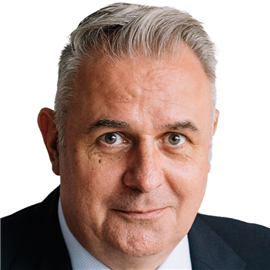
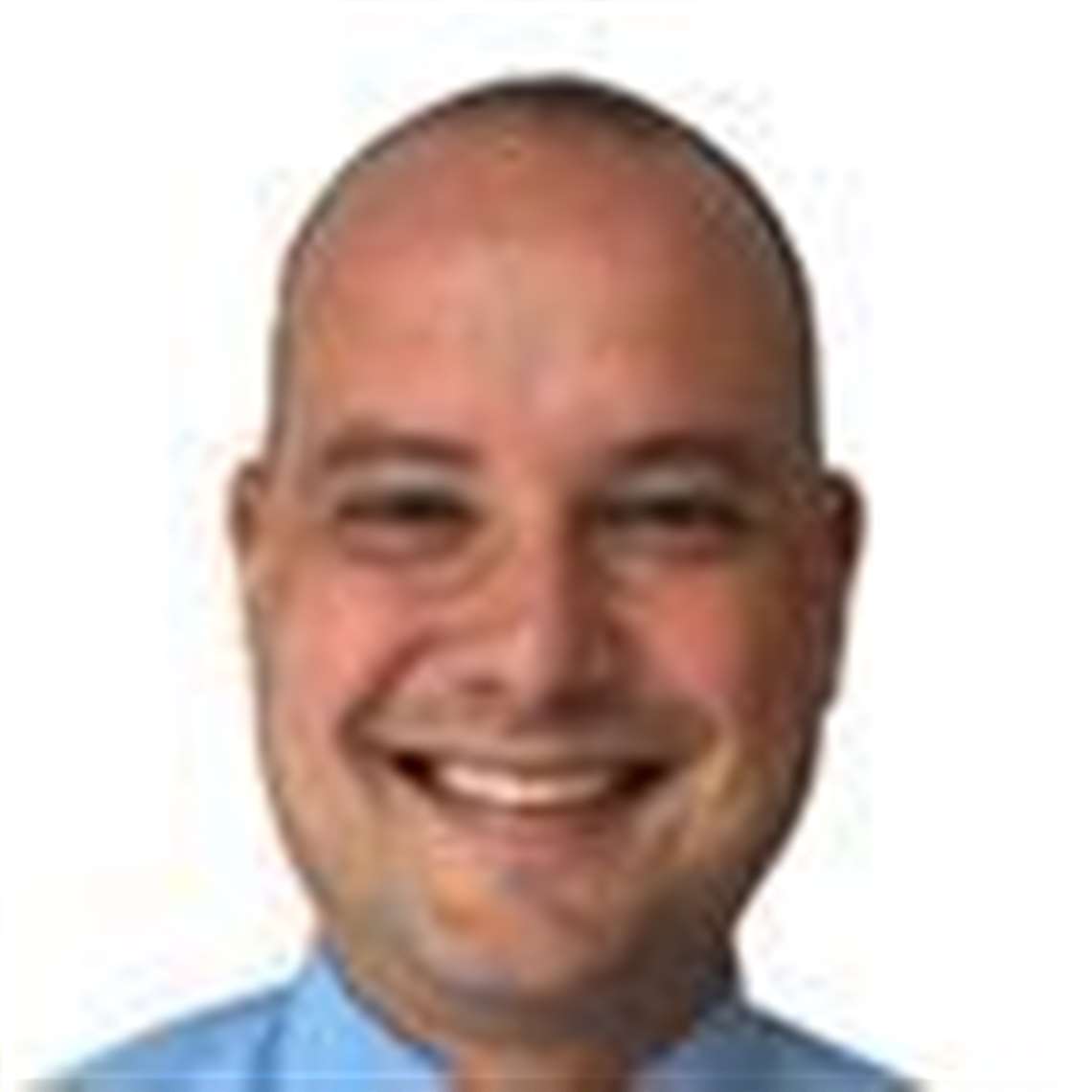
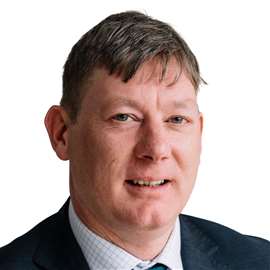