TopLift 2021: who were this year’s winners?
28 January 2022
The votes have been counted and the winners have been chosen for the 2021 IC TopLift competition. ICST reports.
Despite the chaos and disruption of the pandemic, the 12 months leading up to September 2021 saw many spectacular lifts worldwide, covered by our illustrious magazine. We selected the top ten and put them to you, our readers, to vote on your favourite lift and decide the winner of the TopLift 2021 competition.
Aided by a digital voting form both on our website and social media channels, we had hundreds of responses this year, with every lift receiving multiple votes, and we’d like to thank everyone who got involved.
There was, however, a stand-out winner with a massive majority of the vote, Entry 6 – A Perfect Fit. In a very respectable second place was Entry 10 – Girl Power and, coming in close behind in third, was Entry 9 – Wind Farm Wonder.
If your company has completed a job in the last couple of months, or if you do one before August 2022, that you think merits entry into next year’s TopLift competition, and-or it would make an interesting site report in International Cranes and Specialized Transport magazine, please send details to the editor, Alex Dahm, at [email protected], or by post to: KHL Group, Southfields, Southview Road, Wadhurst, East Sussex TN5 6TP, United Kingdom.
WINNER: PERFECT FIT
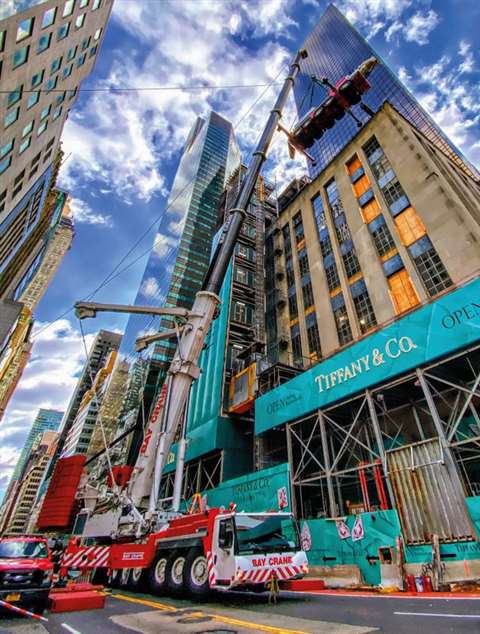
Equipment users: Orange County Ironworks and McLaren Engineering Group
Equipment used: 500 tonne capacity Liebherr LTM 1500
Location: New York City, USA
Working in tight building space constraints, McLaren Engineering’s construction engineering division used a 500 tonne capacity Liebherr LTM 1500 wheeled mobile hydraulic telescopic crane to lift a smaller Liebherr LTM 1130 wheeled mobile crane to a rooftop at the iconic Tiffany & Co. building on Fifth Avenue in New York City, USA, to support the store’s multi-year renovation.
The fully assembled LTM 1500 required eight trucks delivering more than 165 tonnes of counterweight. McLaren’s construction division also provided the crane engineering for a 45 US ton (40.8 tonne) capacity Tadano TR450XL rough terrain crane that assisted in putting the LTM 1500 together.
McLaren put together seven crane plans for this project, designed rigging to lift the crane, designed rooftop dunnage to support the crane on the roof and analysed the building for imposed loads. During the pre-bid process, McLaren worked with the contractor Orange County Ironworks (OCI) vetting a geometry and capacity checks concept for the cranes and then a preliminary look into building reserve capacity. This ended up saving months on the project schedule and millions of dollars too as the work could take place through New York City’s holiday embargo.
“During the pre-bid process, our idea of lifting a crane seven stories over the streets of midtown Manhattan to place it on the roof of the Tiffany & Co. building was initially considered by many as an approach too outside-the-box,” said Matthew Messing, senior vice president of operations Orange County Ironworks. “But we knew that the traditional method of doing crane work from the street would be difficult due to the tight space constraints and would require recurring street closures, ultimately adding two months to the construction schedule. Our solution saved time, alleviated the need to stop work at the site during the NYC Holiday Embargo, and ended up saving costs.”
“Our approach may have seemed unconventional, but we actually spent months finely analysing the best means and methods. We worked with OCI vetting geometry and capacity checks for the cranes and then a preliminary look into building reserve capacity. The building’s location made Tiffany’s vertical expansion an engineering challenge. added Jon Skinner, PE, vice president of construction engineering McLaren Engineering Group.
“What really enabled this success, was the teaming of OCI and McLaren,” concluded Messing. “Although Jon and I dreamt up the scheme, it was the foresight to execute it by OCI project manager Adam Van Kleeck, and the rest of the project teams, that enabled it to happen.”
“Our companies have a long history of teaming up to brainstorm innovative approaches to these challenging, complex construction projects with a unique blend of vision and engineering. We have built a reputation of not being afraid to try something new, and having it work,” said Skinner.
To see a video of the lift, click here. (Video courtesy of Tiffany & Co.)
SECOND PLACE – GIRL POWER
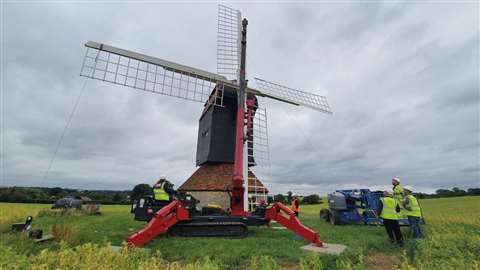
Image caption: Kirsty Parkin and Olivia Rollinson lift plan briefing on site
Equipment user: GGR Group
Equipment used: URW-706 Unic mini spider crane
Location: Bedford, UK
A six tonne capacity URW-706 Unic mini spider crane was used for lifting operations at the 18th Century Stevington windmill in Bedford, UK. The crane was operated by two female operators. Kirsty Parkin, long standing operator, surveyor, and appointed person at GGR Group, and Olivia Rollinson, GGR’s newest female operator, took them helm, with Olivia in the operating seat and Kirsty as the AP. The job required lifting and placing beams weighing 300 kilogrammes and sail frames ready for installation.
Parkin said, “I don’t mind being one of the only few women on site, but it would be great if there were more females in the construction industry out there. If you’re thinking about getting into the industry, go for it!”
Speaking about the job, Rollinson added, “Working on this windmill project with Kirsty has been my most enjoyable project so far and it was great to have some female support on site.”
THIRD PLACE – WIND FARM WONDER
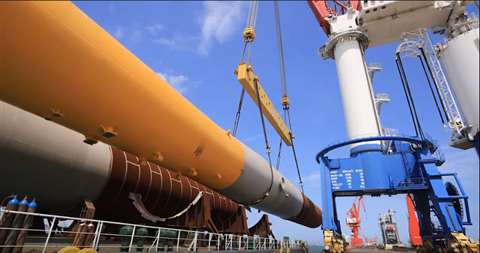
Equipment user: Huisman
Equipment used: 2,600 tonne metre Skyhook Crane
Location: Xiamen, China
Huisman’s Skyhook crane in China lifted its first offshore wind farm components. The luffing jib quayside crane hoisted 100 metre long foundation monopiles, each weighing 1,700 tonnes, from the deck of a cargo vessel. The Skyhook crane occupies its own facility near Xiamen in China. According to Huisman, this lift proves the model is suitable for offshore wind marshalling ports.
According to its manufacturer, the Skyhook is the largest of its type in the world, capable of lifting 2,600 tonnes at a 30 metre radius.
Cees van Veluw, cranes product manager at Huisman, said, “With the high ambitions for offshore wind in various parts of the world, we see that more permanent yet more flexible lifting solutions are key to further efficiency gains in the logistics chain.
“The capacity of the Skyhook matches the foundation sizes we see in the near future. With new marshalling ports being developed worldwide, we see that the Skyhook can contribute to further optimising the logistics of offshore wind turbines and foundations.”
STAY CONNECTED
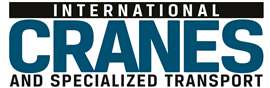
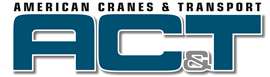
Receive the information you need when you need it through our world-leading magazines, newsletters and daily briefings.
CONNECT WITH THE TEAM
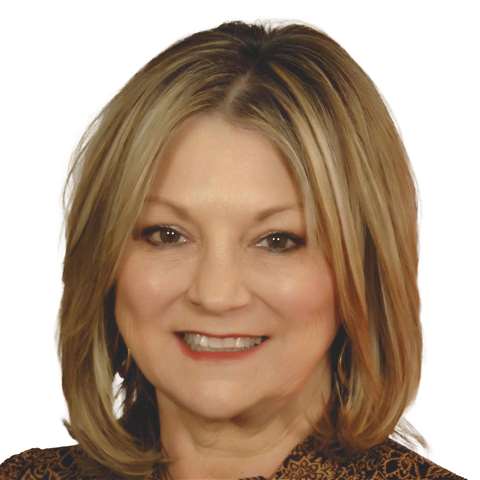
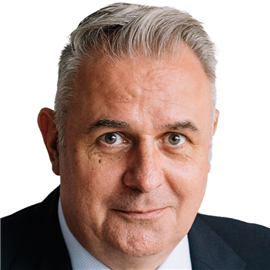
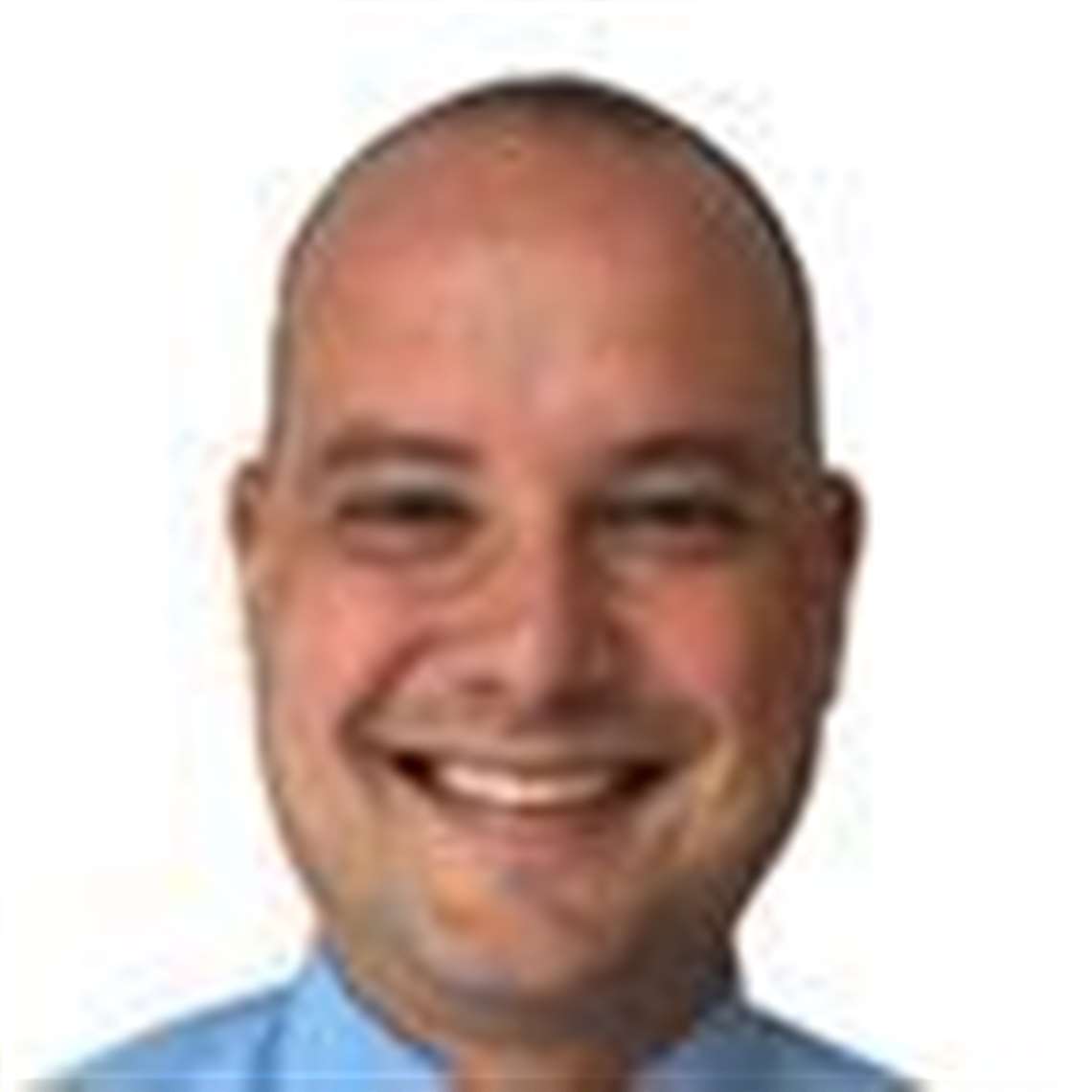
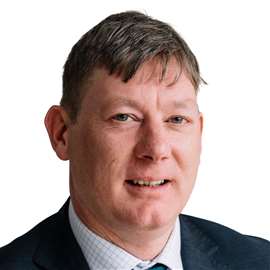