What goes up...
18 March 2008
Amongst the last jobs on the Tacoma Narrows Bridge project near Tacoma, WA was the dismantling of tower cranes perched atop the bridge's two towers. The tedious task was the final major construction effort to take place before traffic started to flow on the new 5,400 foot span, according to Joe McCarthy with Campbell Crane.
To go back in time, construction of the bridge's two 510 foot reinforced concrete towers was the work of a previous pair of tower cranes, each anchored to one of the bridge pier foundations. These cranes required climbs and tie offs at three levels before achieving their ultimate height of more than 600 feet in July of 2004. The final assignment for the original tower cranes was to assemble a second set of tower cranes. These cranes stood atop the bridge's towers. Removal of mast sections from the original tower cranes shrunk their height to a level at which they, in turn, could be disassembled by their newly erected counterparts.
“That left a Liebherr 550 on the west tower and a Potain 560 atop the east tower to service spinning of the suspension bridge's cable and help bring the project to completion,” explains McCarthy. “Each of these tower cranes were configured with 131 foot jibs”.
Three weeks prior to the bridge's July 2007 opening, Campbell Crane brought in a 308-ton capacity Demag TC1200 equipped with 256 feet of main boom and a 157 foot luffing jib to dismantle the tower cranes. Complete tear down and mobilization of the Demag was required between the two dismantle jobs.
The project was far from routine, requiring the services of an outside engineering firm to address problems created by positioning such a heavy piece of equipment on the new bridge's main span. VAK Construction Engineering Services provided the necessary engineering. McCarthy says Campbell Crane was impressed with the work of the Portland-based firm.
“We drove our crane carrier up onto timbers which allowed us to get over the top of a steel grillage system designed to work like a set of snowshoes. This spread the crane's downward forces through the bridge deck in a manner which the bridge's design team found acceptable,” he says. “Each grillage comprised a set of steel beams welded together, placed beneath the crane's outriggers. The length of the beams was calculated to transfer the combined weight of our machine and its load into four bridge deck beams instead of only two.”
McCarthy explained that once the Demag crane was set up beneath the bridge's west tower it went to work dismantling the Liebherr tower crane, a process that would take 15 hours to complete. Northwest Tower Crane Service crews began by removing the tower crane's counterweights. The 7,000 pound concrete blocks were lowered three at a time to the bridge's traffic deck.
“Next, the upper works of the tower crane was rotated 180 degrees allowing the Demag to remove the 55 foot outer jib, then the 76 foot long inner jib,” McCarthy explains. “The relatively short jib configurations used on these tower cranes allowed the contractor optimum capacity.”
The heaviest component to be removed was the tower crane's machinery deck with its gear boxes, motor and hoist system. “This piece is located near the counterweights at the outer end of the 67 foot long counter jib,” McCarthy explains. “The highest point of the tower crane was 400 feet above the bridge deck on which Campbell's mobile crane was positioned. By splitting the tower crane's turntable and removing it in two pieces crews were able to keep loading of the bridge's deck within acceptable bounds.
The Demag was driven up onto timbers which allowed the crane to get over the top of a steel grillage system designed to work like a set of snowshoes to spread the crane's downward forces through the bridge deck in a manner in which the bridge's design team found acceptable. Each grillage comprised a set of steel beams welded together, placed beneath the crane's outriggers
“The base of each tower crane was 292 feet above the bridge's deck,” McCarthy explains. “You go up 292 feet and that's the bottom of the tower crane.”
The challenge for the crane operator was working within “The canyon” of the bridge, as McCarthy described it. “Essentially, we were working up through a narrow canyon formed by the bridge and its suspender cables,” he says. “The gap we worked in was a slot 74 feet wide and 290 feet deep. Taglines were attached to both ends of horizontal members and a close eye was kept on wind conditions. Tower crane components were swung 180 degrees before being lowered between suspenders to the bridge deck below.”
The crane's parts were landed on a protective layer of plywood. WSDOT was adamant: “no steel is to come into contact with the roadway.” Composed of an “exotic mix,” the bridge's hybrid asphalt surface was to be protected at any cost. A pair of Terex 60 ton rough terrain cranes provided by Tacoma Narrows Constructors (TNC) tailed incoming loads before reloading them onto highway trucks for removal. Kiewit and Bechtel comprise the consortium TNC, general contractor on the project.
On completion of the west pier tower crane's dismantling the Demag TC 1200 was disassembled. The crane's carrier along with 14 loads of counterweight and boom moved to the main span's opposite end where the process was repeated, removing the Potain tower crane from atop the Tacoma Narrows Bridge's east pier.
STAY CONNECTED
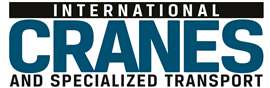
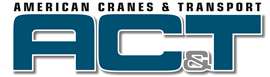
Receive the information you need when you need it through our world-leading magazines, newsletters and daily briefings.
CONNECT WITH THE TEAM
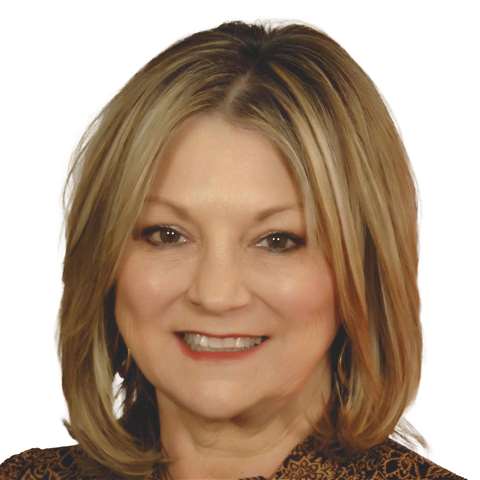
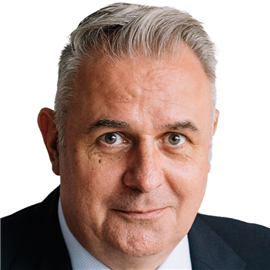
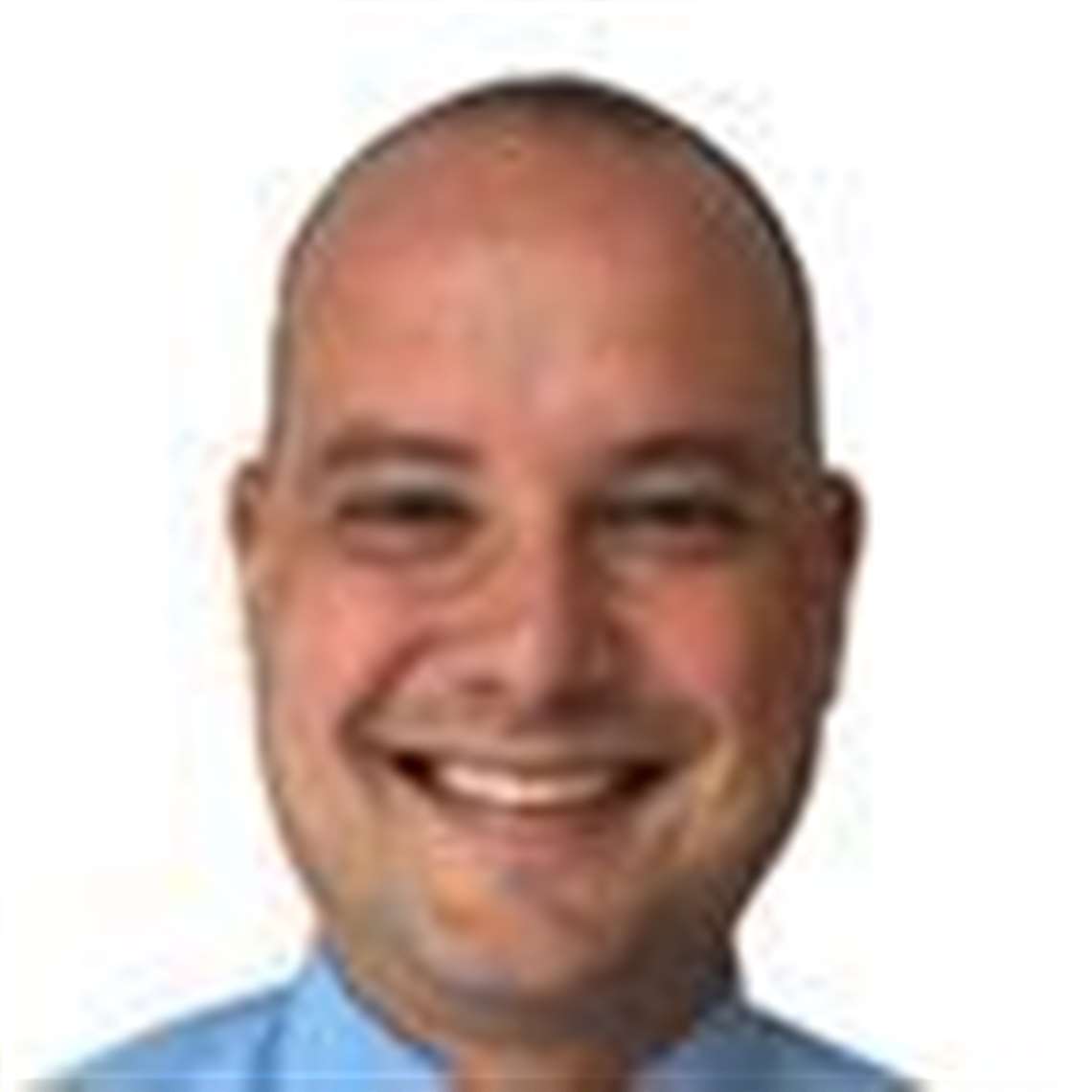
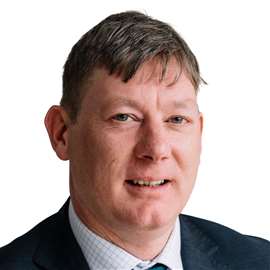