Specialized Carriers & Rigging Association’s Jobs of the Year 2018
01 June 2018
Detailing the projects that won the 2018 SC&RA Job of the year awards announced at the Specialized Carriers & Rigging Association Annual Conference in Florida, USA, as reported by MIKE CHALMERS, TIM HILLEGONDS, HANNAH SUNDERMEYER and D.ANN SHIFFLER
Rigging over US $2 million: Fagioli
Using a custom-built launching system, Fagioli installed 19 mobile gates at the Malamocco Inlet in Venice, Italy.
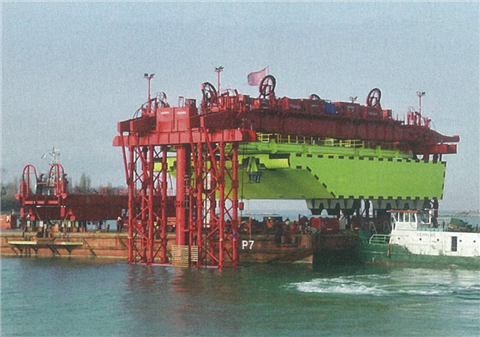
The first phase of the project to install barriers to isolate and protect the Venetian Lagoon from the Adriatic Sea was completed in 2014. Fagioli transported and installed 12,000 tonne concrete caissons as bases for mobile barriers activated prior to exceptional high tides.
Fagioli completed phase two between 2016 and 2017, using an in-house built launching system to install the 19 gates, each weighing 450 tonnes. “‘After undergoing months of detailed analysis, tests, and 3D simulations,” said Edoardo Ascione, president and managing director at Fagioli in the USA, “the Fagioli engineering department designed an innovative launching system to facilitate the installation of all 19 mobile gates.
“The launching system had a lifting capacity of 690 tonnes, a loading capacity of 870 tonnes and contained a movable tower system capable of rotating 180 degrees.”
To assemble the various sections of the launching system, Fagioli used a gantry lifting system, self propelled modular transporter (SPMT) and mobile cranes. After assembling the crosshead beam the towers were assembled.
The crosshead beams were designed with four top-mounted, 300 tonne strand jacks which were used for the lowering and lifting operations of the mobile gates.
Assembly then moved on to the lateral movable towers. The towers were connected at the top and bottom with two beams referred to as top and bottom frames. A middle frame was also used to allow the rotation of the towers.
To install the mobile gates, Fagioli built a dedicated lifting system which it called a “fishing beam.” This was connected to the strand jacking system and hooked on to the gate so it could be lowered into its final position under water.
Fagioli also custom built a transport beam which had four 300 tonne capacity strand jacks and power packs to skid the beams. The structure was designed to lift the gantry off one caisson and reposition it onto another for subsequent gate installations.
In addition, Fagioli used a 36-axle SPMT for moving gantry and beam sections during assembly operations and transporting the gantry launching system, mobile-gates, and transport beams onto the barge.
To complete the operation as efficiently as possible, Fagioli employed a dedicated barge to transport the gates. It had winches for mooring operations and Fagioli was also responsible for the ballasting operations.
When the barge carrying the launching system arrived at Malamocco, the gantry lifting system was positioned over the first 12,000 tonne caisson. The barge was moored and kept steady by tugboats. The gantry launching structure opened the movable tower systems and the bottom towers were then connected to the middle frame. The barge was then unmoored and returned to Pellestrina Island where all the mobile gates were stored.
Using SPMT Fagioli loaded the mobile gate onto the barge, after which it returned to Malamocco. The barge was moored underneath the launching system previously laid onto the caissons. The fishing beam was lowered and connected to the gate before being lifted by four strand jacks mounted on top of the lifting structure so the barge could sail out from under it. The mobile gate was then lowered into the water by the strand jacks connected to the fishing beams. Connecting the gate to the caisson was the final operation.
Rigging US $750,000 to US $2 million: Barnhart
Using creative thinking and clever engineering, Barnhart designed and fabricated a never-before-seen lifter.
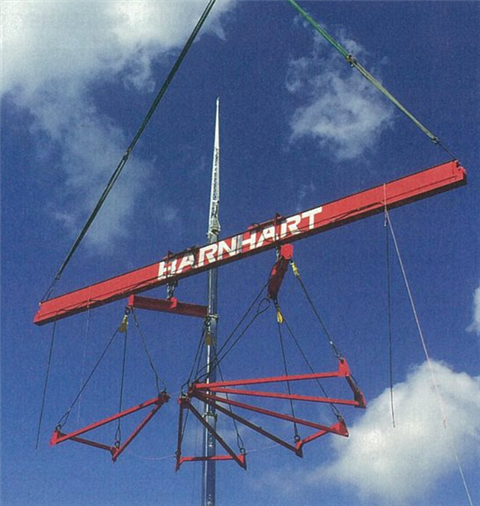
Barnhart’s winning project was completed at a nuclear power plant in Louisiana, USA, where it required innovation and an aggressive execution plan. One of the nuclear facility’s two clarifier units needed repair.
They draw clean water from the Mississippi River for use as cooling water. The clarifier tank is a concrete structure with a wall height of 28 feet (8.5 metres] and an inside diameter of 178 feet (54m). The clarifier core, which is the rotating equipment in the centre of the tank, had 16 lateral supports and tie rods attached to the tank wall. These-supports had buckled and ten of the 16 were structurally compromised.
“The challenge for Barnhart began almost immediately,” said Gene Pugh, Barnhart project sales, “once the clarifier tank had been drained and inspected from the observation platform, plant safety protocol prohibited anyone from entering the tank. There were many things to consider in evaluating repair options, but employee and worker safety was paramount to the plan that would eventually be approved.”
Barnhart’s scope was to provide a lift system capable of lifting from above the 600,000-pound (272 tonne] clarifier structure so as to remove the damaged lateral supports, while also providing crane and rigging support for the subsequent reconstruction of the clarifier unit.
The customer suggested a heavy lift crane to hold the structure while removing the lateral supports. It would have required the crane to hold the load for three weeks which was deemed unfeasible.
Barnhart next considered a girder configuration on the clarifier wall, and then a girder system independent of the wall. The concrete wall, 28 feet (8.5 ml high and two feet (600 mm] thick, would need to be evaluated for its vertical-load capacity, and the rigging design would be complex.
After all options were considered, a four tiered girder arrangement on the concrete wall was accepted. The base tier comprised two eight foot (2.4 ml girders each 180 feet (55 ml long with a 164 foot (50 ml span. This was the largest span ever for Barnhart.
The second tier comprised two temporary bridge girders each 76 feet (23 ml long. The second tier was crucial as it allowed for the load points on the eight foot (2.4 ml girders to be moved closer to the walls instead of being closer to the centre. This reduced the deflection on the eight-foot (2.4 m) girders to acceptable levels and gave the headroom to obtain the necessary sling angles.
The third tier was made up using two five foot (1.5 ml transition girders that were each 84 feet (25.6 ml long with a 74 foot (22.6 ml span. The top tier consisted of two trapezoidal girders supporting the rigging - each 72 feet (21. 9 ml long with a 55 foot (16.8 ml span. The upper assembly also had slide systems on tiers three and four to enable precise placement of the rigging over the structure.
Barnhart’s concept and execution plan adhered to all of the customer’s site-safety procedures. The rigging design and fabrication allowed for the 600,000 pound (272 tonne] load to be lifted safely from 24 rigging locations, which ensured the stability of the structure. The lifting solution was resistant to virtually any severe weather that could have occurred during the course of the project, Barnhart said.
Even the expected deflection was mitigated with design innovations, including strategic placement of the second-tier girders and rockers (also developed by Barnhart], which nullified the effect of deflection on the upper lift system.
Rigging US $150,000 to US $750,000: Fagioli
Lifting, shifting and installing a top ram guide in Romania.
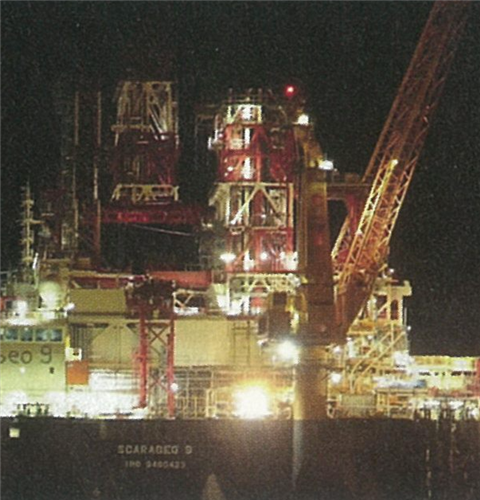
From June to September 2017 Fagioli worked on a challenging operation in Romania to lift, skid and jack down a large top ram guide (TRG). Working for client Saipem it was at Costanza and used an elevator system.
The TRG was transferred from storage to a drilling tower on the Scarabeo 9, an ultra-deepwater semi submersible ship. The TRG was 24 m long, 7 m wide, 18 m high and weighed 16 7 tonnes. The equipment used was as striking as the job itself.
There were four towers with base frames welded to the deck (up to 46 m height); one elevator frame of two longitudinal girders and two transverse bracings; eight L-50 strand jacks for the elevator system; four L-15s for skidding; eight 50 tonne hydraulic jacks for jacking down; and four 200 tonne rollers.
Fagioli started to take the load with the L-50 jacks. Each stroke was about 400 mm, increasing the load in increments of 20%. Lifting continued until the elevator skidding rails aligned with the cantilever skidding rails. At each step the tower was checked for verticality, deck deflection, girder planarity and any deformation.
After installing the L-15 strand jacks and connecting to the top ram guide operators connected and tightened four turnbuckles from the elevator girder to the cantilever beam, and installed two of the bridge elements. Eight stoppers were removed from the skid rails.
Eight 50 tonne hydraulic jacks were positioned under the TRG frame beam and raised to meet the top frame beam of the module. With the full load on the jacks, disconnections were made and the eight jacks were raised. The TRG was lifted and the rollers from the ram guide top frame were removed before it was lowered.
Rigging under US $150,000: Barnhart
Positioning a 21 tonne load with millimetres to spare on a journey of tight spaces, corners and then a vertical shaft.
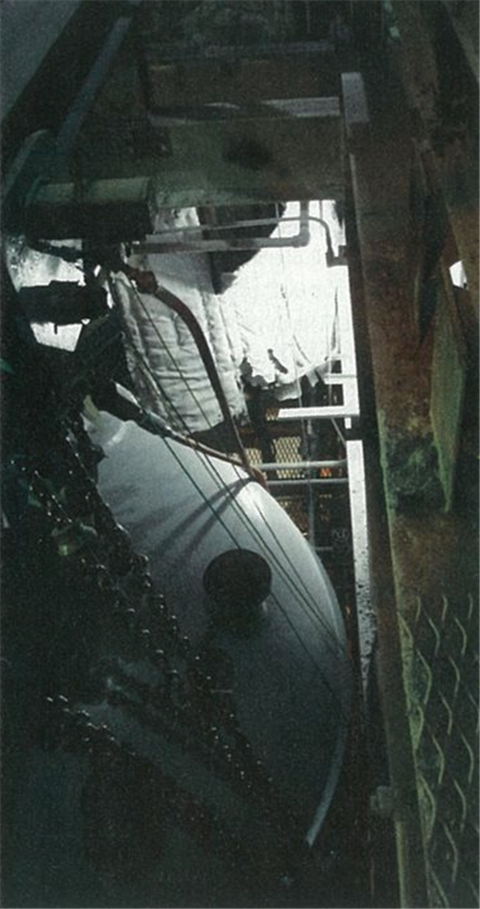
Barnhart’s installation of a silicon reactor for client Evonik was a journey that took them through incredibly tight spaces and ultimately up a vertical shaft for securement on the second floor of a manufacturing facility.
Installation options were limited and a Navisworks model was provided with the reactor’s final location. It revealed a barely possible path through the facility. Two key moves were right-hand turns with 1.8 inches of clearance. After the 46,000 pound (21 tonne) reactor (3.5 x 5.5 m diameter and height) snaked its way through the facility, it had to be tailed to vertical with 75 mm of clearance.
The answer was to modify the shipping frame to lower overall height to be able to use traditional rigging tools, and lift vertically as high as possible using standard chain hoists. It added a means of transport to the shipping saddles to keep the reactor as low as possible while staying within the horizontal constraints of the travel path. At the erection area, the reactor would be tailed to vertical and hoisted to its final set location.
The reactor, however, was not designed to be lifted from the bottom. It was hoisted vertically as high as possible, using a Barnhart low-profile hoist system before the jack up tower took the load.
Roller support frames were added outboard from saddle to saddle, which didn’t add to the overall height or width. Two 16T air hoists with trolleys from Lifting Gear Hire were supported by W8 beams on temporary stub columns. The load was pulled up with only a link and a half of chain to spare.
Moving with specialized equipment: Oxbo Mega Transport Solutions
Oxbo’s team saved time and money on a job to mate the hull and superstructure of a new 3,350 tonne ferry, which was built in two places 60 km apart in the USA.
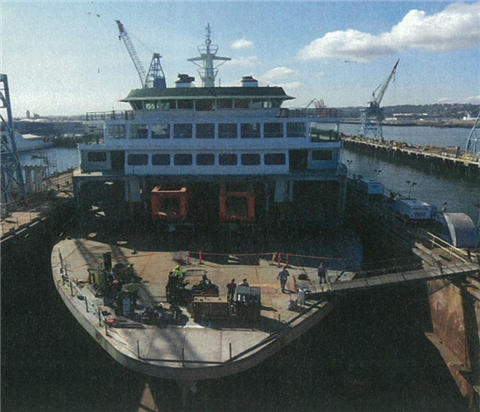
Seattle’s Suquamish ferry was ceremoniously christened in January 2018. Before its first official voyage, however, the 144-car, 1,500-passenger vessel had already experienced a somewhat arduous journey.
Oxbo’s contribution shortened the ferry’s build time. Its hull, built in Seattle, was 98 metres long, 25 m wide and weighed 1,921 tonnes. The upper superstructure, 85 m long, 25 m wide and weighing 1,429 tonnes, was built 50 km away away in Tacoma, Washington. The hull had to be moved onto a floating dry dock in Seattle, while simultaneously loading the superstructure onto a barge in Tacoma.
The barge with the superstructure would then be transported overnight from Tacoma to Seattle where it would enter a second dry dock and be lifted out of the water. The two dry docks would then be tied together and the superstructure would be rolled and installed onto the hull, making it into one vessel. The time allotted was 72 hours to complete all three moves.
Stability was given to the superstructure by placing sections of gantry trusses and a network of cross beams on top of 72 lines Goldhofer PST-SLE modular transporter which was then driven under the centre of the superstructure.
Dock strength was an issue addressed by adding crane mats and beams before manoeuvring the vessel to a position where it was cantilevered 7.5 m out over the edge. The barge loadout was completed in four hours.
In another four hours, crews had lashed the superstructure and achieved the go ahead for the launch. At the same time Meanwhile in Seattle, work continued on the hull. Built inside a building, it had to cross two 2.4 m wide finger piers to get to the dry dock. This was achieved using 48 dollies in two files and hydraulically connected in three zones. Six were self propelled allowing for remote control operation. The hull was loaded out in six hours.
The ballasting operation matched the speeds of the Goldhofers so the transfer of the superstructure over the hull took less than 90 minutes. The superstructure was set within minutes of the plumb bob being set by the owner. The shim packs were pulled from the steel beams and the support system was driven out from under the load and onto the barge in the same 8-hour shift.
Trucking over 500,000 pounds: ALE
On an adventurous route by river and roadway through Venezuela, ALE transported six huge power plant engines each of which weighed more than 300 tonnes.
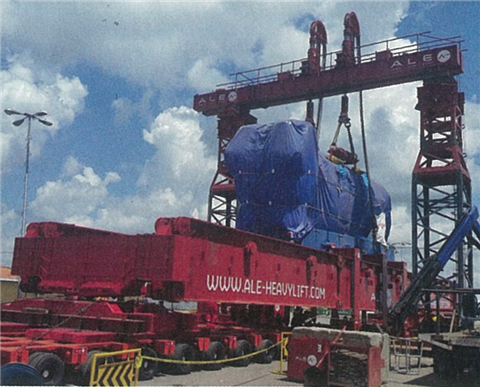
Covering almost 1,000 land and nautical river miles in Venezuela, United Kingdom-based ALE was tasked with transporting six 22 MW power plant engines from Puerto Ordaz to the Santa Ines Refinery in Barinas State, Venezuela. As the distance was so vast, and weighing a combined 1,891 tons, the project was split into three phases.
The route was incredibly varied, involving different terrains and of varying infrastructure - water and land - and transportation through small towns as well as large, populated cities, and through rivers that had never been sailed on before. “We had a very tight water window and had to transport all six engines at the same time,” said Javier Gutierrez, ALE executive director.
ALE began the initial phase in December 2014 following the transatlantic navigation of the six engines from Italy and the trans-shipment to the barge, up to 91 metres long, on the Orinoco River. The engines sailed on the barge from the reception point on the river to temporary storage at the Alianza river wharf in Puerto Ordaz.
ALE monitored the level of the Orinoco to estimate the necessary adjustments for the load-in in February 2015. Once loaded in, the engines were again stored while waiting for the Orinoco and Apure rivers to reach their optimum levels of navigation.
The Orinoco River changes water level by 40 feet (12 m) between the December to May dry season and the May to November wet season. The Apure River is only navigable in the months of July and August. To barge during the high-water levels, ALE had to wait until July.
The second phase started in July 2015 and involved loading the six engines at Cabruta quay on the Orinoco. ALE used 24 axle lines of self propelled modular transporter (SPMT) to load the engines onto one 300 by 100 metre barge. Three pusher boats with low draft were deployed to help with the barging 550 nautical miles along the Orinoco River.
One of the most challenging parts of the route involved passing underneath the Maria Nieves drawbridge serving San Fernando de Apure, on the Venezuelan plains. An operation like this had never been attempted by ALE, or anyone else, and required an impressive logistics effort and close co-ordination between the local, regional and national institutions.
The bridge could only be passed underneath a few days a year because of the negative combination of air draft and water draft limitations. Then, a new central span bridge removal had to be performed, which took one year to design, build and install.
Eight months later, the three barges carrying the engines passed underneath the newly removed span and the first convoy of engines arrived at the Puerto Nutrias Naval Base for temporary storage in Barinas.
The final phase was inland transportation of the engines to the Santa Ines Refinery Development. The engines were loaded from the storage area onto a girder frame trailer, fabricated by ALE, using a gantry system composed of 500 tonne SLS strand jacks. The engines were then transported using 40 axle lines of conventional trailers with three prime movers.
On the 198 kilometre journey the convoy crossed bridges, travelled through small towns and Barinas city streets, before arriving at the refinery. It took six days for each engine to be transported, between October and December 2016. The project completed in January 2017.
The cargo consisted of six dual system generation Wartsila engines 14.3 x 5.3 x 6.0 metres and weighing 318 tonnes each. ALE transported the engines over 500 nautical miles (926 km) and then 200 km on land. ALE used a combination of SPMT, power packs, conventional trailers and trucks, barges and low draft pusher boats, a gantry system with two 200 tonne strand jacks type HLS2000 and a 500 tonne capacity girder frame.
Considering the route, huge preparations were undertaken by ALE’s team. Route studies resulted in dredging and reinforcing port slabs for receiving the engines. Some 15 bridges were reinforced. Most notable was the unprecedented pass under the Maria Nieves Bridge, the only lifting bridge system in Venezuela. ALE estimated that the project required 30,000 man hours.
Trucking 160,000 to 500,000 pounds (net): Edwards
Edwards transported three fully assembled turbines while facing huge storms and rocky terrain.
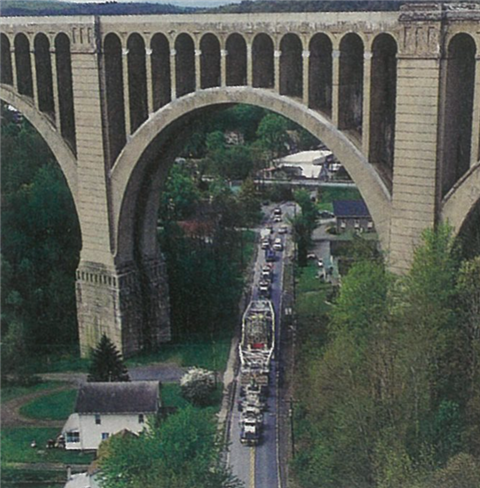
In May 2017 Edwards was contracted to haul three of the largest ever fully assembled turbines from Schenectady in New York State, USA, to a new combined cycle power plant in the hills of Jessup, Pennsylvania.
From the moment Edwards was awarded these moves, the intricate pre-planning started for how to move cargo weighing 375,000 pounds (170 tonnes), 16.25 feet tall and 16.48 feet wide (5 x 5 metres) over a 260 mile (420 km) route.
Challenges included failing bridge structures and tight unyielding turns. Co-operation was needed from approximately 20 local jurisdictions, upper level state DoT personnel in New York and Pennsylvania, power companies, law enforcement officers, private property owners, 12 bucket truck operators and finally three civilian escorts along with Edwards personal escort vehicles.
After six months of planning the first turbine was loaded via in-plant overhead crane onto the Edwards dual lane 32-axle Aspen A500 expandable transporter with three Kenworth Prime movers attached. The final gross weight of the configuration came to 913,227 pounds (414 tonnes) and was 345 feet long, 18 feet tall and its widest expansion was 20 feet 2 inches wide (105 x 5.5 x 6.1 m).
On 2 May the loaded turbine began its 10-day trek. Edwards 30 and 40 foot (9 and 12 ml long bridge jumpers were needed and there were steep mountainous grades and narrow winding roads. Tight turns required meticulous manoeuvring of the trailer, including a turn around a historic antique shop in which an additional crew moved ahead of the load and laid out more than 60 mud mats to cover the dirt lot.
The load continued its planned path to a pre-negotiated transload location where it was lifted using a 700 ton capacity gantry system, then lowered onto an 18 line Goldhofer trailer with the first ADD rive 6-line trailer in the USA.pushing, and a Kenworth prime mover pulling the load. The AD Drive module replaced the back two prime movers, thus reducing total weight of the load and providing maximum manoeuvrability on the job site.
After 2,993 man-hours, the turbine was finally on its last five mile stretch of steep 8-11 percent graded route. The Kenworth was uncoupled from the load and the AD Drive functioned as a self-propelled module to finally position the turbine under the hook on 11 May 2018.
Trucking less than 160,000 pounds: Precision Specialized Division
A complex cross-country module transport by Precision Specialized Division in North America was two years in the making.
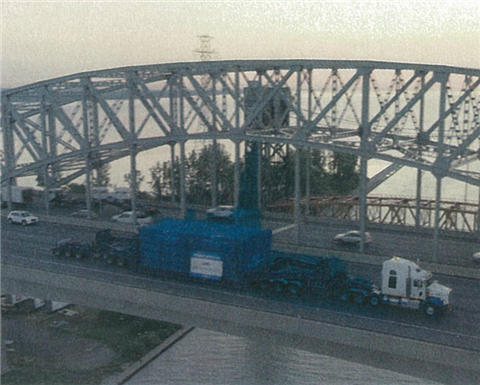
Industrial process technology engineering company Zeton asked Precision Specialized Division a peculiar question: What’s the biggest, largest possible load you could transport by road from our plant in Ontario to Linden, New Jersey?
“The client for this particular job approached us and they had preselected a module size that was different than our norm. In this case, 16 feet wide by 14 feet high was well beyond their usual build size and the end destination was of course was of concern” said Ed Bernard, vice president, Precision Specialized Division in Woodbridge, Ontario, Canada.
This job involved transporting expensive and fragile hi-tech instruments, cased in heavy steel, over a precarious route from North America’s busiest traffic corridor to one of its most populated, 20 miles (32.4 km) southwest of New York City.
Before they could begin designing, Zeton needed Precision to develop a logistical plan for something not yet built. That meant reverse engineering the whole process two years in advance.
Challenges included axle load restrictions in Ontario, at the Welland Canal and at the Peace Bridge to cross the Niagara River into the USA, numerous special permit applications were needed. Then in the USA, constantly changing construction patterns made it difficult to determine a route, especially in Pennsylvania.
Manoeuvring inside a large petrochemical facility while in operation, and where the infrastructure was designed in 1909, was going to mean tight corners and involve the construction of custom rail beams and modifications to their perimeter trailer.
After two years of hard work, Precision had secured permits, designed solutions that eliminated the highest risks and mitigated the impact of secondary issues. But they still had to get the modules out of Zeton’s facility.
“When Zeton fully completed their project, we were faced with a total of 16 modules ranging from 40 feet by 12 feet by 12 feet on the small end, to their largest at 40 feet by 16 feet and 14 feet,” said Bernard. “We determined the trailer required to transport the larger modules was our Aspen 95-ton, 13 axle rear steer perimeter. The perimeter allowed us to travel lower to the ground by placing the module inside the rails. We used a standard 25-foot deck, but the second had to be a custom-made 13-foot deck, specifically designed to fit the limited access space at the delivery site.”
STAY CONNECTED
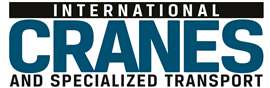
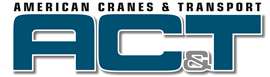
Receive the information you need when you need it through our world-leading magazines, newsletters and daily briefings.
CONNECT WITH THE TEAM
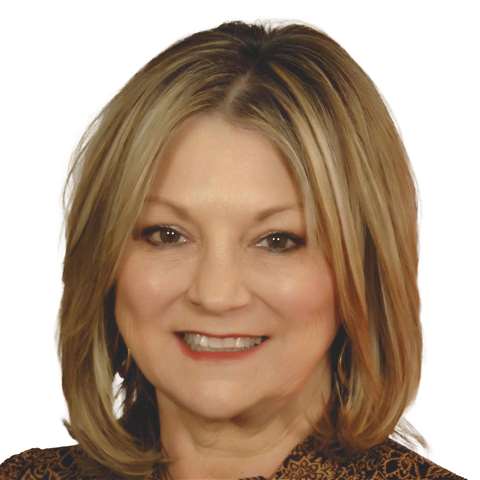
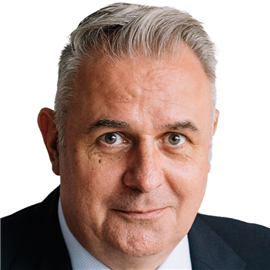
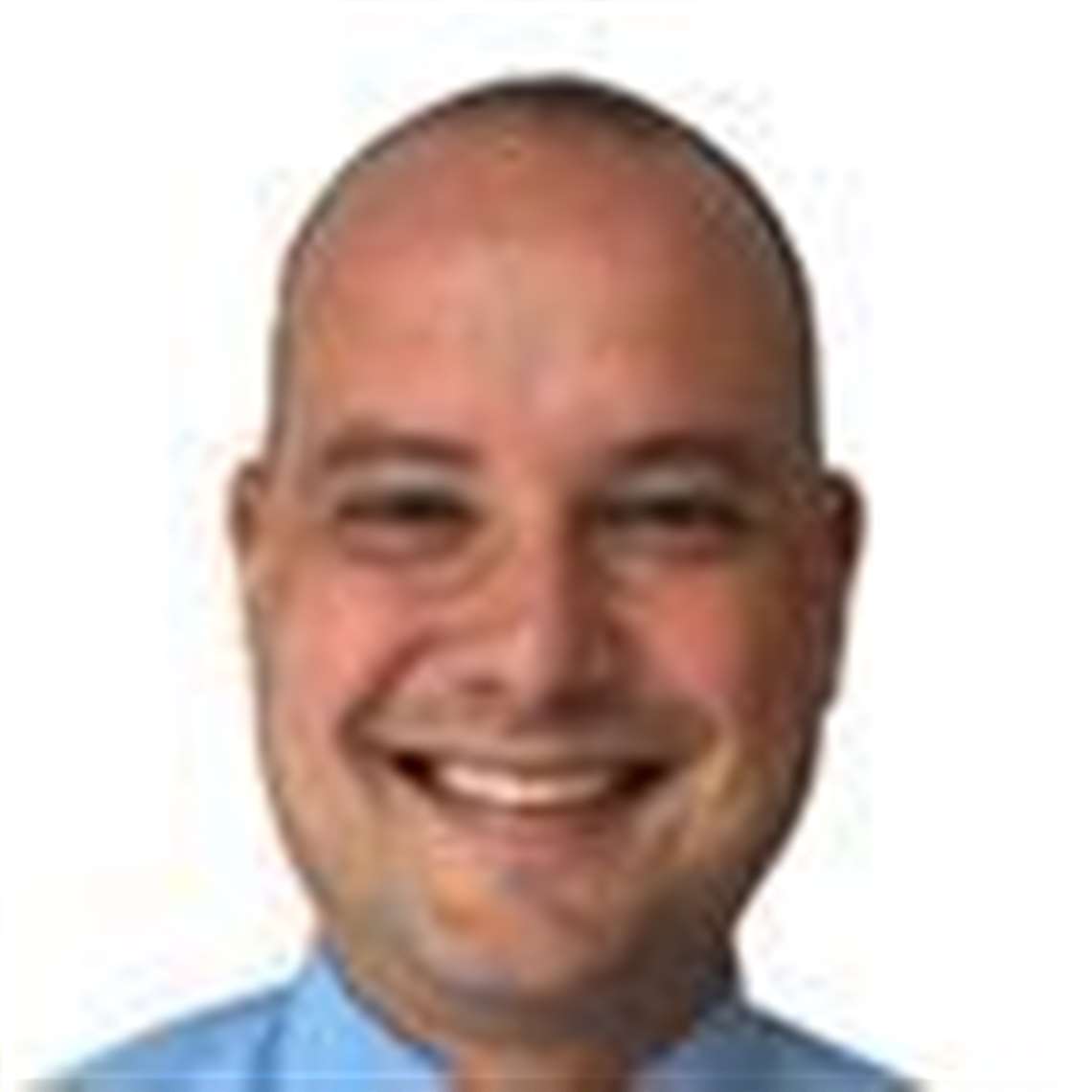
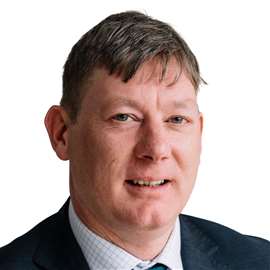