How to make the right rope choice
06 March 2023
New developments in ropes and winch technology offer real improvements to a crane’s performance. Niamh Marriott reports.
Rope technology is continually being tested and further developed.
Regardless of whether it is a huge lattice boom crawler crane for setting up wind turbines, a crane for handling containers or an indoor crane in a paper factory, they all have one thing in common - the rope, which is a fundamental element of the device allowing the load to be lifted.
Critical component
“The rope has always been a critical crane component, the importance of which has increased due to the development on the crane market, which follows the motto faster, higher, stronger.
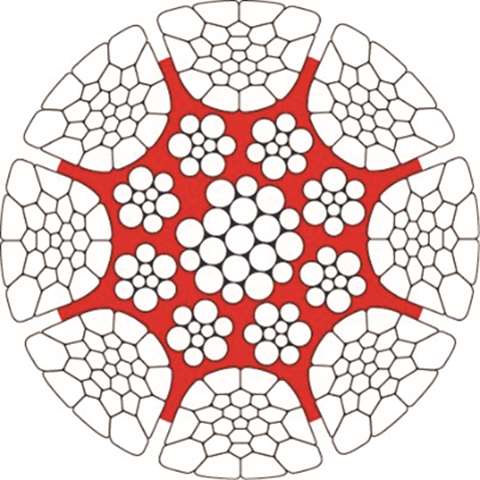
“Safety and reliability have top priority in crane operation. That is why Casar ropes are designed and calculated in such a way that they show their discard status on the rope surface in good time and thus inform their operator when it is time to change the rope,” says a spokesperson for rope maker Casar, a WireCo brand.
Casar has invested in research and development to acquire a technical understanding of the behaviour of wire ropes in various applications.
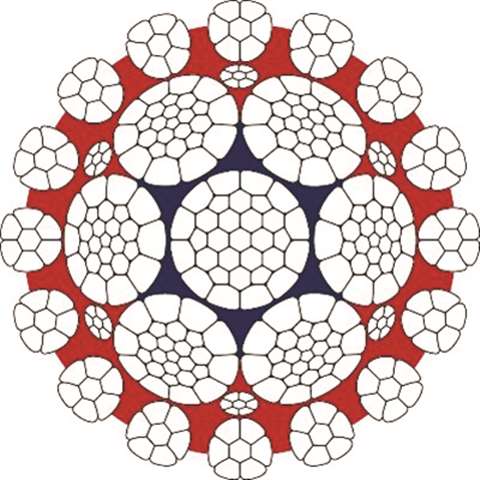
It also invested in the construction and purchase of test machines over the years for its products. For example, important rope properties such as breaking strength, turning behaviour, efficiency, flexibility and diameter reduction under load are determined.
Casar says this knowledge informs future product developments.
Heavy duty
“A heavy-duty application such as the installation of a wind turbine requires a hoist rope to be extremely stable in terms of rotation, the best possible winding behaviour with multi-layer winding and very high breaking forces,” continues the spokesperson.
Its Doublefit product is made from compressed strands and hammered twice. By compressing the strands and hammering both the heart rope and the slammed rope, a round and smooth surface is obtained.
Compared to ropes with a lower minimum breaking force, Doublefit allows the sheaves and drums to be dimensioned smaller and thus considerably increases the crane’s payload.
The Casar Parafit rope is designed to meet challenges with drum crushing. Its special hammered compression is useful for applications with high surface pressures and its smooth surface avoids indentations and damage on the rope’s surface.
Synthetic supply
As the rope debate continues – synthetic fibre or steel wire – there are new options coming to the crane market.
At Bauma 2022, tower crane manufacturer Wolffkran demonstrated a synthetic fibre hoist rope to replace conventional steel wire hoist rope.
It said its new chaRope, developed with rope specialist Trowis, is “the only fibre rope that can replace a steel rope 1:1.” It was shown at the trade exhibition on a Wolff 6021 FX flat top tower crane.
In addition to the usual advantages of fibre rope over steel, Wolff says, substitution of steel with the new rope can be done without any modification of the crane.
The new Trowis rope has a distinctive full cover and is the same diameter overall as the steel rope it replaces.
“The chaRope fibre rope has the same diameter as a steel rope and is thus significantly thinner than comparable products from competitors,” says Thomas Heidrich, Wolffkran CTO and board member.
“The design consists of a multi-layered, twisted core made of high-tensile high-tech fibres and an abrasion-resistant, thin-walled fibre composite cover,” adds Thorsten Heinze, Trowis managing di-rector. “Thanks to this structure, we can offer 12 and 16 mm diameter crane ropes at market entry.”
All Wolff cranes with 12 or 16 mm steel rope can have the new fibre rope instead. No adjustments to sheaves, hoisting gear, or load capacity are needed, Heidrich adds. “In our current portfolio, this applies to all models in the Wolff Clear series, the new Wolff 21 FX cranes and the Wolff 8033.16 Cross.”
Full coverage
A distinctive feature of the new fibre rope is that its cover is an impermeable full sheath unlike the braided cover of competitors.
Moisture can’t penetrate to the inside of the rope and at the same time lubricants can’t leak out, the company said.
“The rope does not run dry, even after many years, and the environment is not polluted with microscopic plastic,” says Peter Streubel, Trowis managing director.
In addition, this cover gives the core of the rope complete protection against the damaging effect of ultraviolet rays in sunlight. Any damage to the cover acts as a wear indicator, showing when the rope needs to be discarded.
Testing of the new rope is ongoing. “The test phase will be completed in June 2023 and the rope will be available on the market in August 2023,” Heidrich says. Field testing will be carried out on Wolffkran’s UK rental fleet.
“In the medium term, we plan to develop further fibre ropes with other typical diameters, together with Trowis, to offer the entire Wolff crane range with the innovative fibre rope,” says Heidrich.
Securing synthetic
Synthetic rope is increasingly being used on a wider range of cranes for its weight savings and longevity.
“Synthetic rope continues to grow in popularity for utility, trailer and towing, construction, military as well as other applications,” says a spokesperson for USA-based manufacturer Paccar Winch.
“Replacing traditional steel cables can drastically reduce the overall weight of any towing or utility vehicle, particularly those with multiple winches.
“Abrasion resistant and easy to inspect, synthetic rope is torque neutral, which means it will not twist and is much easier to handle.”
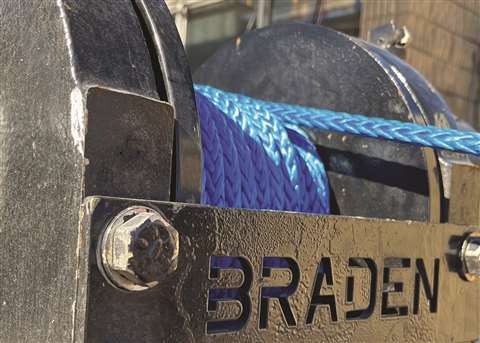
Under its Braden brand, Paccar Winch has launched a new product to address the question of securely installing synthetic rope for winching applications – an anchoring system for all its TR Series recovery winches.
The synthetic rope anchors securely install synthetic rope. The company says it will provide maximum pulling power with up to 40 per cent less weight compared to steel cable.
The anchors were tested during development have a rated line pull of 5,443 kg to 13,608 kg.
To use the anchor, an eye must be spliced into the rope and inserted through the smaller opening of the wedge pocket on the drum.
Install the anchor in the eye, then pull the rope until the anchor is fully seated in the pocket. The anchor will secure the rope in the drum.
Smart spooling
The company recommends using 12 strand single braid pre-stressed rope with a breaking strength of 10,841 kg (TR12 and TR15) or 15,422 kg (TR20 and TR30) or greater.
“Synthetic rope should be installed on a new winch drum with all burrs and sharp edges removed. The rope should be spooled onto the drum while under tension,” adds the spokesperson.
“For best performance, synthetic rope should not be installed on drums that have previously had wire rope installed. A minimum of 8 wraps are required on the drum for pulling at maximum capacity.”
Whether synthetic or wire, rope technology is continuing to advance a crane’s performance by ensuring loads are held strong and high with products that last.
Research vessel sets sail with winch system
MacGregor designed a self contained traction winch system for a geological survey vessel.
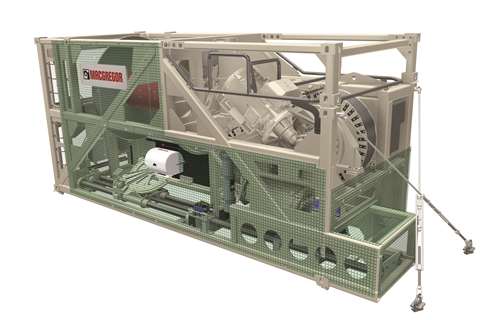
MacGregor, part of Cargotec, has been selected to supply two self-contained traction winch systems for a geological survey drilling vessel owned by Guangzhou Marine Geological Survey (GMGS), a subsidiary of China’s Ministry of Natural Resources, together with HongHai Marine.
HongHai Marine is MacGregor’s partner in China, focusing on MacGregor deck machinery integration and service in the fishery and oceanographic markets.
The vessel is scheduled to be delivered in the third quarter 2024.
MacGregor needed to provide a system with at least 18 tonnes lifting capacity, and a high speed performance of 200 metres per minute.
The containerised system has everything installed on the unit, and only needs the main power from the ship to be ready to operate.
The operator can manage the system either from the local operation panel on the winch, with a wireless radio remote control, or from an additional control panel located where it is needed.
The setup is with a low noise active frontend with an ability to regenerate power to the ship, or operators can use the built in air brake resistors to get rid of generated power during lowering.
The winch system is set up to have 13,800 metres of 17 mm wire or EOM cable. A wire outlet possibility from 0 to 180 degrees sideways, and -10 degrees to 80 degrees in the horizontal plane gives the operator a high flexibility for arrangement and placing of the system onboard.
“We are very pleased to continue the long-standing relationship with HongHai Marine, and proud to deliver equipment for this key project to GMGS. This verifies the quality of our products and skills of our experienced team,” says Jan Erik Pedersen, senior VP of offshore solutions division at MacGregor.
STAY CONNECTED
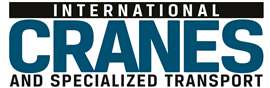
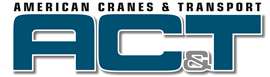
Receive the information you need when you need it through our world-leading magazines, newsletters and daily briefings.
CONNECT WITH THE TEAM
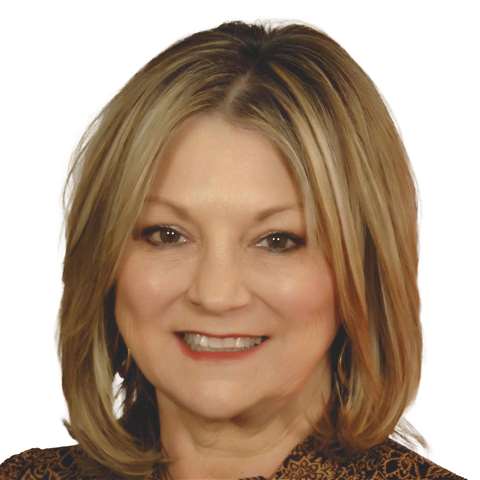
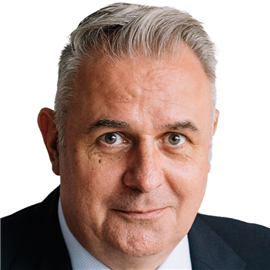
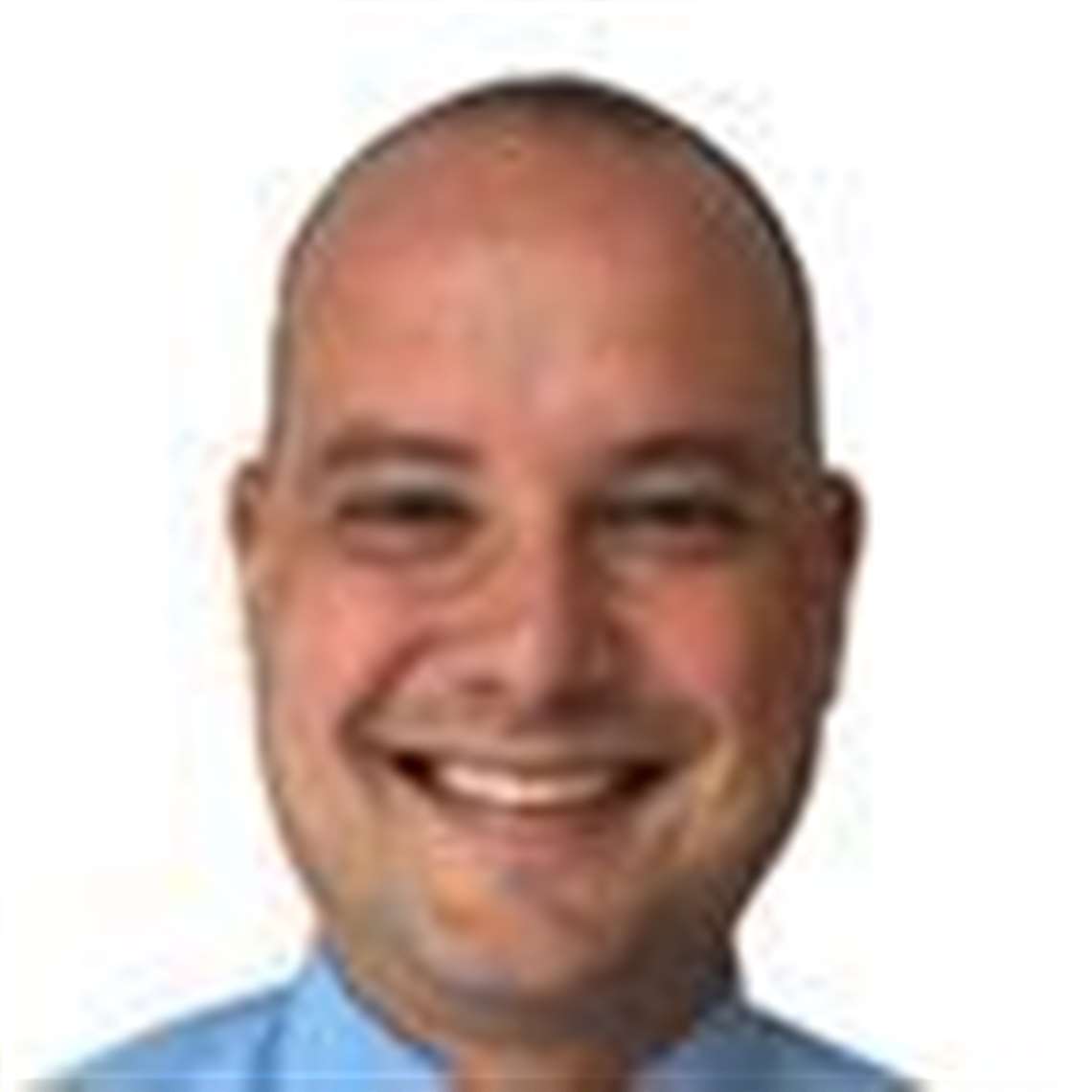
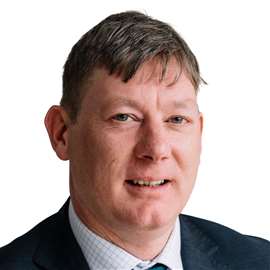